How changes reflected in the 25th edition of this widely used specification, API 6D will affect manufacturers, engineering contractors, and operators.
By Ed Edgar, Cameron, a Schlumberger company, and Wojciech Zmudzinski, BP Americas
The American Petroleum Institute (API) specification 6D defines the requirements for design, manufacturing, and testing of axial, ball, check, gate, and plug valves. In the United States, it is referenced by the Bureau of Safety and Environmental Enforcement (BSEE) in the Code of Federal Regulations (CFR); the Pipeline and Hazardous Materials Safety Administration (PHMSA); and by state regulators. The specification is also widely referenced by regulators across the globe.
In November 2021, the API published the 25th edition of API 6D in response to the growing needs of the industry. The changes to this specification—the third most referenced of all the API specifications—were thoughtfully made with input from manufacturers and operators, including representatives from International Oil and Gas Producers (IOGP). Some notable changes include:
- Change of the title to Specification for Valves.
- Normative reference to API 6DX for full conformance.
- New requirements for bolting.
- New informative Annex F for Design Validation.
- Definition of permissible purchaser deviations and supplemental requirements in new informative Annex K and Annex L.
- Updated Quality Specification Level (QSL) requirements.
- Improved guidance on non-standard valves and the use of intermediate pressure-temperature ratings.
- Addition of Annex A for repair and remanufacture of valves, replacing API 6DR.
This article covers some of these changes in greater detail to illustrate how they will affect manufacturers, engineering contractors, and operators.
API 6D Evolution
The first version of API 6D was API Standards Number 5-G-1, which was first published in September 1936. It was 20 pages long and sold for 35 cents. The original document covered wedge gate valves, plug valves, and swing check valves for pipeline service. The scope and title remained focused on pipeline valves until the 23rd Edition, published in April 2008. To meet the needs of the industry, the scope of the specification was expanded in the August 2014 publication of the 24th edition to include piping valves and thus the specification title was changed to Specification for Pipeline and Piping Valves. The 25th edition, likewise, sees a change in scope and title, with the new title simply being a Specification for Valves. This change signifies the recognition from API and the task group representing industry that API 6D valves are not only used in the design and construction of pipelines but are in all aspects of the oil and gas industry, and more.



Latest Changes
One change that will likely have an immediate impact are the requirements for actuators and gearboxes. The 25th edition requires actuators to fully conform to API 6DX. In the 24th edition, only the API 6DX rules for sizing an actuator were required. This means that for an actuated valve to conform to the 25th edition of API 6D, the actuator must conform to API 6DX. Also, new in the 25th edition is a 1.5 safety factor for sizing a manual gear-box. This requirement has been included at the request of the operators represented by the IOGP. The 24th edition had no requirements for gearbox safety factor, and it was up to the manufacturer’s internal standard.
Furthermore, in the new edition, there is now a clear distinction between pressure-boundary bolting and, simply other bolting, used for example when mounting a gearbox.
More importantly, the new edition also now requires pressure-boundary bolting be purchased from suppliers that can ensure they conform to API 20E (carbon steel bolting) and API 20F (corrosion resistant bolting) requirements. The bolting manufacturers do not need to be licensed to these standards; however, it should be expected that majority of the supply would come from such suppliers. In fact, the introduction of API 20E and API 20F into API 6A and API 6DSS, and now also API 6D, the increased demand should drive the suppliers to get licensed and hence improve bolting availability.
The new edition introduces a new definition of pressure boundary bolting, which has its own requirements of marking, quality assurance, materials, etc., which are different than the requirements for pressure containing parts and hence are not grouped together. API 6D took a big step forward with the introduction of a new Annex for Design Validation. Many API 6D valve manufacturers also build valves in conformance to API 6A specification, which has long been known for its “PR2-test” for valves. The 25th edition followed the same format and many requirements from API 6A Annex F and developed its own annex for Design Validation. Table 1 shows a list of the activities covered by this annex.
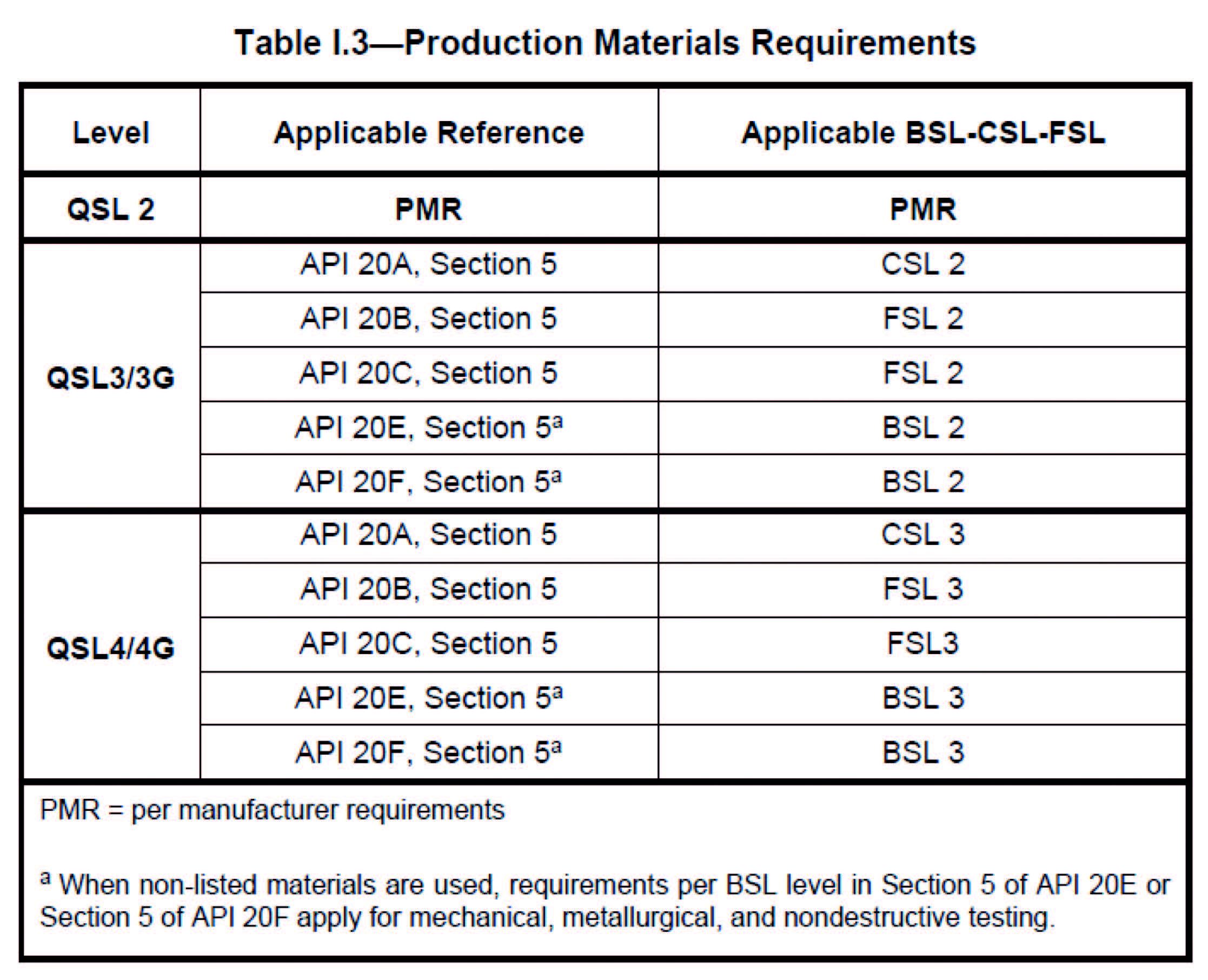
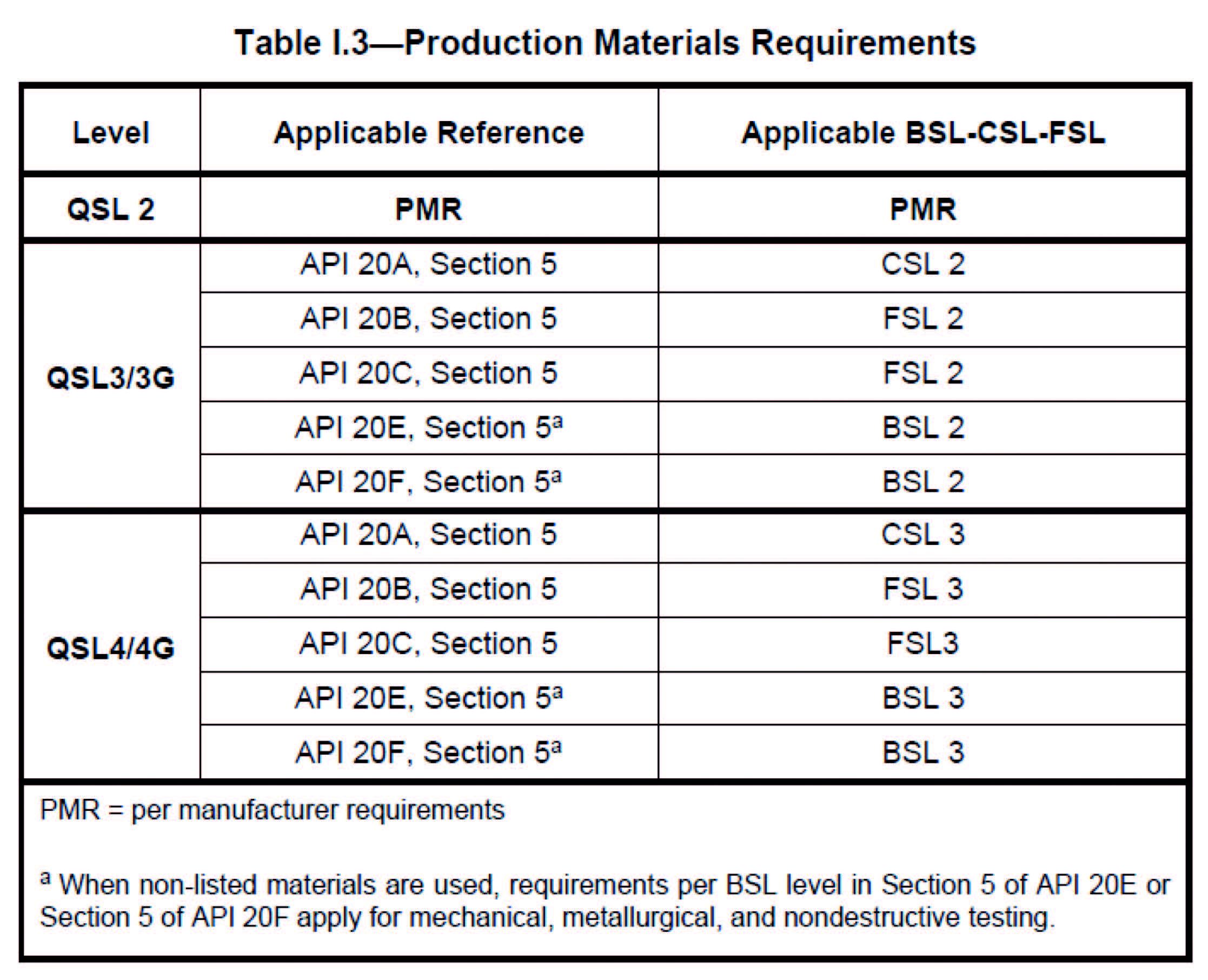
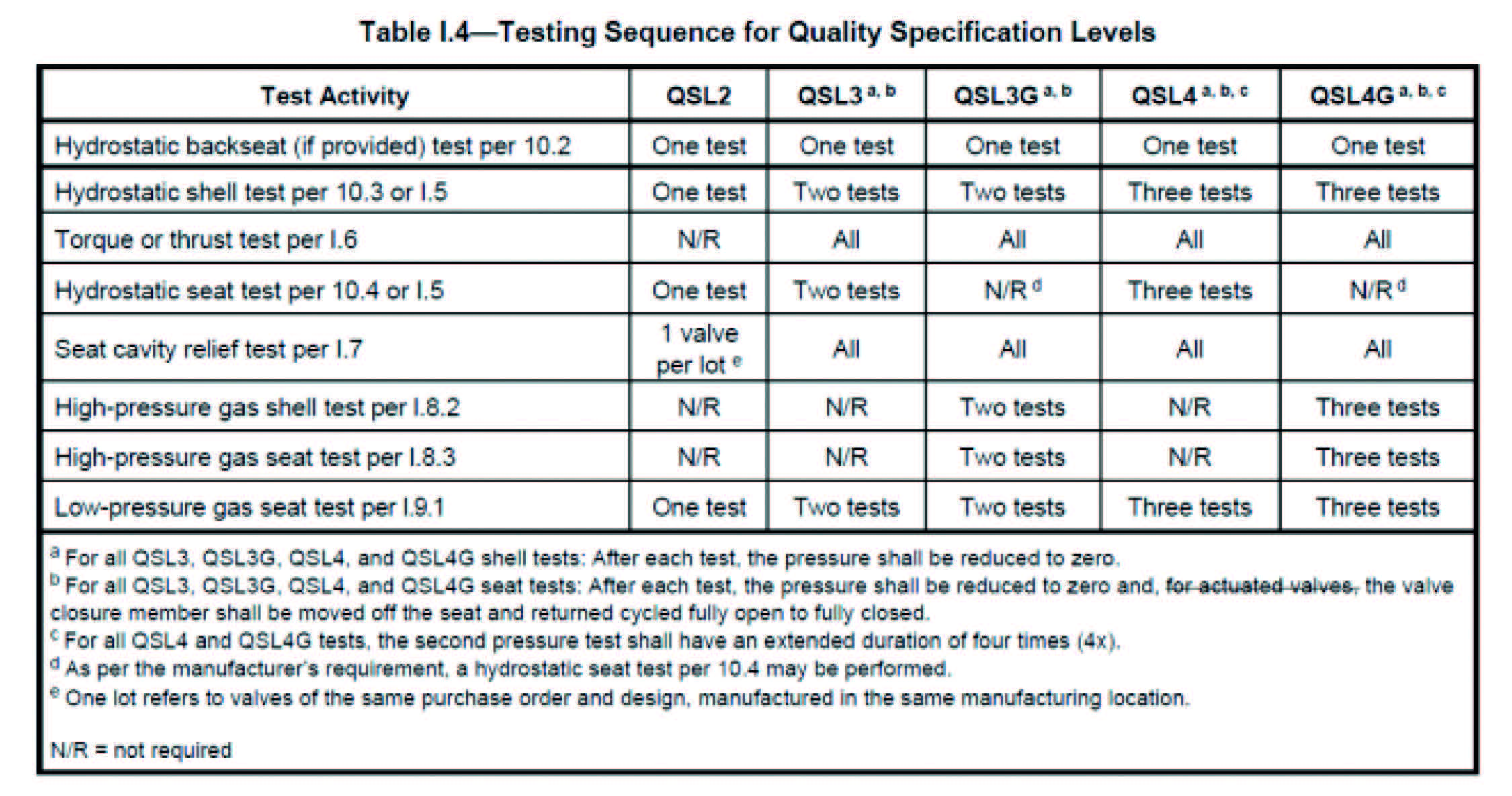
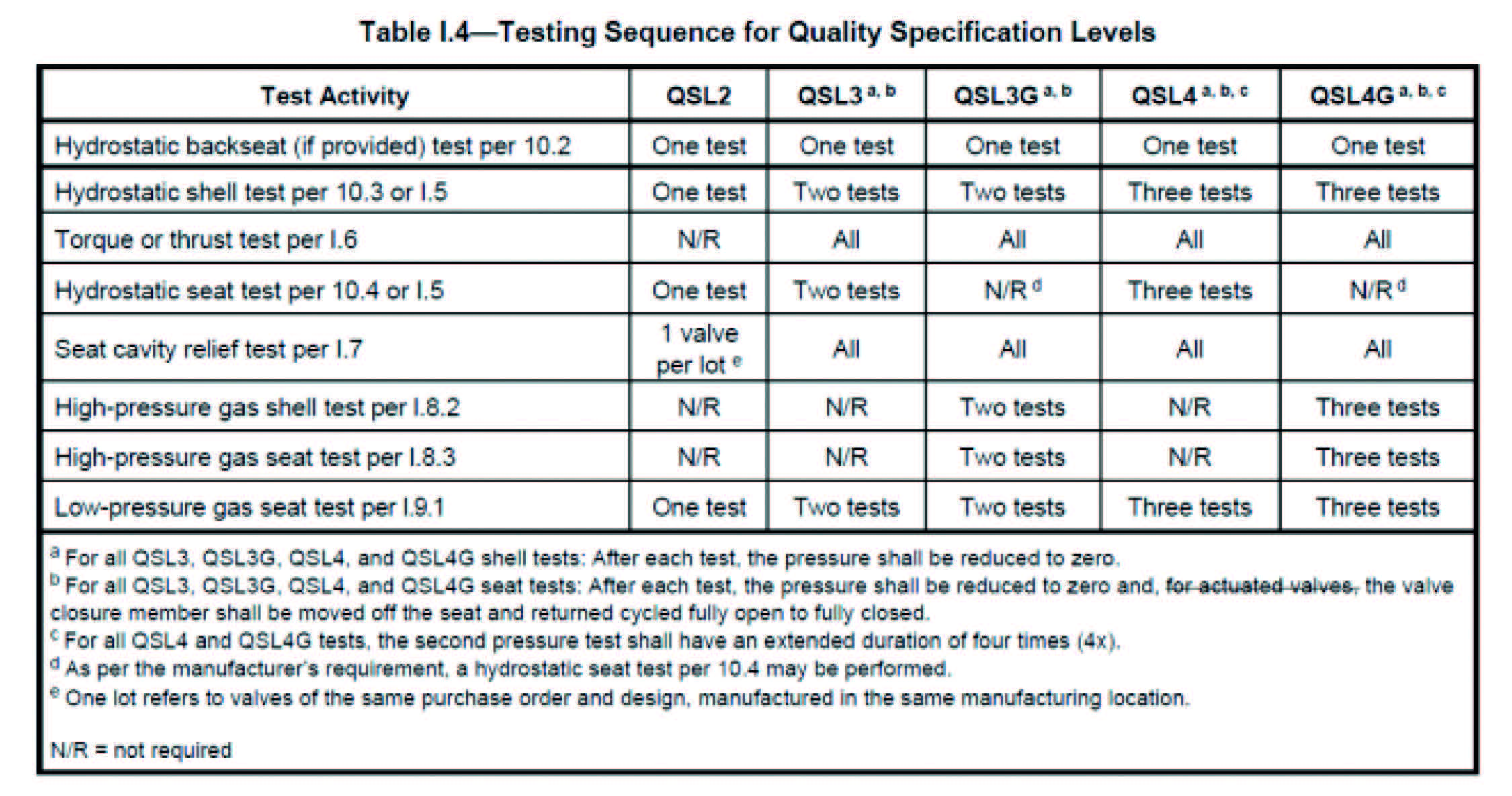
Like API 6A, the annex also provides rules for scaling by valve type, pressure rating and nominal size.
It should be noted that this is an informative annex, and as API 6D states, it represents one method which can be used for design validation. The fact that Annex F has been written, should not be taken to mean that it is the only acceptable validation method. A valve manufacturer is free to develop their own validation criteria, which could include historical service, and remain in conformance with the requirements. API 6D is a document that specifies the performance requirements for products (e.g., valves and gearboxes) and factory acceptance test (FAT) is an acceptable validation of such performance.
The 24th edition of API 6D has 11 instances of the phrase “unless otherwise agreed” and 12 instances of the phrase “by agreement.” These terms permitted flexibility in applying some requirements of the specification, but at the same time, reduced the effectiveness of producing a standardized product. Ultimately, by agreeing to something that is not defined within the specification, the possible permutations of valve design options are endless. API asked the task group to remove or reduce the use of these phrases as much as possible, and as a result, the 25th edition uses the phrase “unless otherwise agreed” two times, and the phrase “by agreement” just three times.
The new specification, however, did not eliminate the flexibility the users have always enjoyed. Most of the topics that were captured by these two phrases, have been moved to Informative (non-mandatory) Annex K. Annex K is titled “Purchaser-specified Customization – Permissible Deviations to Specified Design and Manufacturing Requirements.” As the title states, Annex K allows the purchaser to specify specialty design criteria such as a custom pressure-temperature rating, or a bore diameter that is different than what is required by the main body of the document. These customizations, or variations (i.e., permissible deviations) on the requirements in main body of the document do not affect the API 6D product certification.
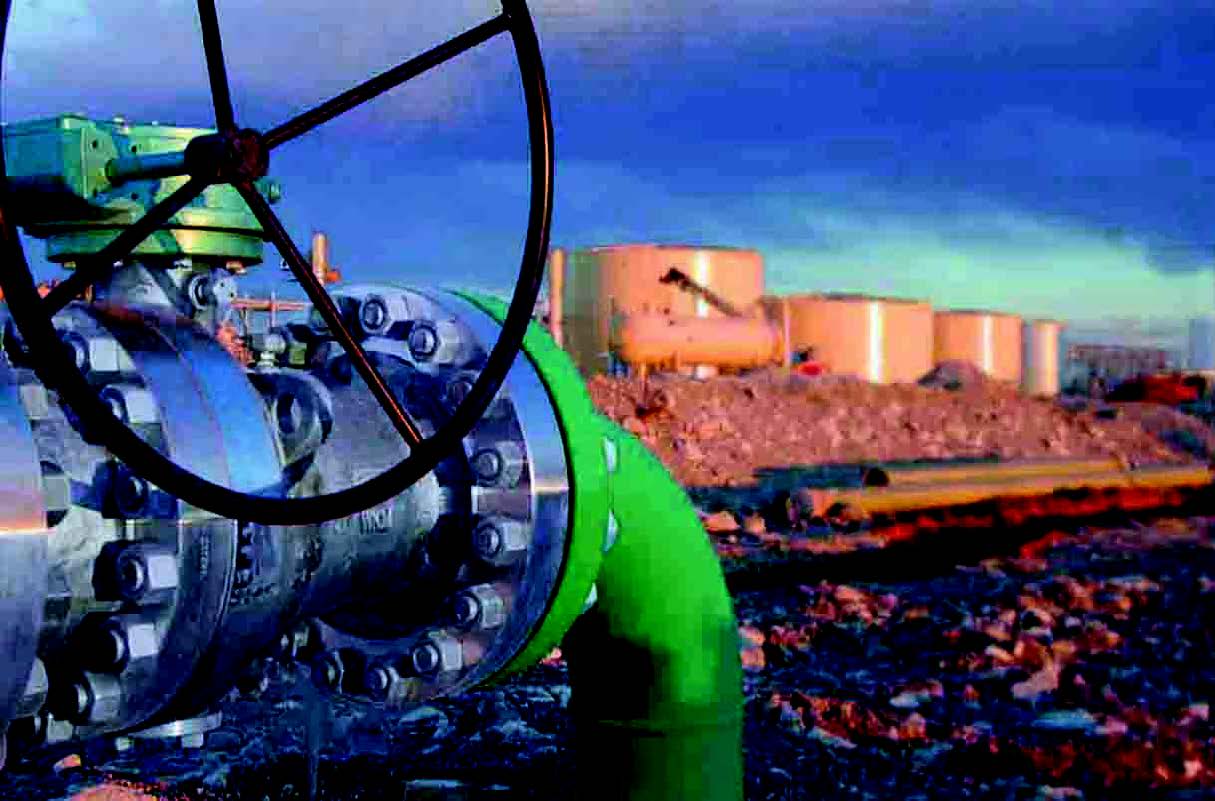
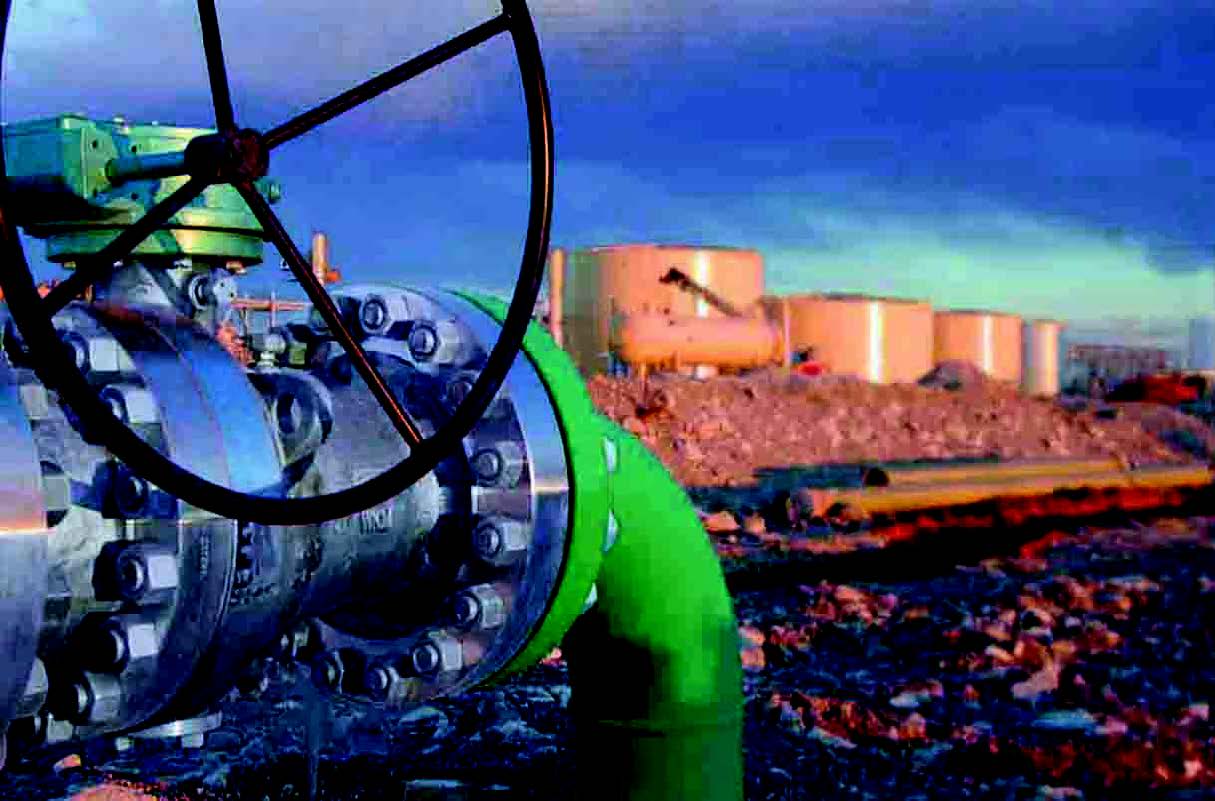
Annex L is titled “Specified Customization – Supplemental Options to Specified Design and Manufacturing Requirements.” As this title states, Annex L provides customization of the valve based on supplemental options. The difference between Annex K and Annex L is that Annex K permits the manufacturer to deviate from a requirement in the main body of the API 6D document. Annex L does not. All the requirements in Annex L are in addition to the requirements of the main body of the API 6D document. It is also worth noting that the items in Annex K must be specified by the purchaser, while the manufacturer (and purchaser) can self-specify the items in Annex L.
Another noteworthy change between the API 24th and 25th editions is the use of Quality Specification Levels, or QSL. In the 24th Edition, the standard, or “lowest” QSL was called QSL-1, and this represented a product that met the base-level API 6D requirements, with no additional quality control. The use of QSL-1 has been dropped in the 25th edition, and a valve with base-level quality has no named reference.
The testing required by Annex I, Table I.4, for QSL-2 through QSL-4/4G is in inclusive of the FAT performed for a standard valve. For example, for QSL-3, hydrostatic test will consist of a total of 2 test cycles, i.e. one performed as part of the standard FAT plus one test performed to qualify to QSL-3.
Also new in the 25th edition is reference to “Production Material Requirements,” which is discussed in Annex I. There are no Production Material Requirements for standard valves, and for QSL-2, the requirement is Per Manufacturers Requirements (PMR). From a supply chain perspective, standard product and QSL-2 may use materials per manufacturer’s standard. This changes with QSL-3/3G and QSL-4/4G, with normative reference to API 20A (castings), 20B (open die forgings), 20C (closed die forgings), 20E (alloy and carbon steel bolting) and 20F (corrosion resistant bolting) bolting, castings and forgings will need to be procured with additional quality requirements, most of which will occur during raw material production (ref. API 6D Table I.3).
The significance of these changes cannot be understated – valves currently on a shelf at either the manufacturers or distributors will need to be carefully reviewed before they are deemed in full compliance with the new edition of API 6D.
Another area in the new edition is an improved guidance provided on non-standard valves and the use of intermediate pressure-temperature ratings, with other than ASME end flanges. These can be designed to any intermediate pressure-temperature rating (such as PN155 for metric or 2250-psi for US customary), determined using an industry-accepted design standard, and with an agreed valve bore size (e.g. DN200R), and marked on a body and nameplate as outlined in Tables 11 and 13 of the specification.
Another new annex for API 6D is Annex A, titled “Repair or Remanufacture of Valves.” The content in this annex originated from API document RP6DR which was titled Recommended Practice for the Repair and Remanufacture of Pipeline Valves. API RP6RD was concurrently withdrawn with the publication of API 6D, 25th edition. With the addition of Annex A to the document, it aligns many of the repair and remanufacture requirements to those of new production valves, especially in testing and inspection stages. Annex A includes special marking requirements and differentiates between repair (disassembly, replacing parts, reassembly, and testing) and remanufacture (same as repair but can also include machining, welding, heat-treating or other manufacturing operations).
Product Quality Enhancement and Standardization
There are nearly 700 API 6D licensees around the world that must conform to the 25th edition by November 2022. From the end-user’s perspective, many of the changes should improve durability and longevity, and overall product quality of standard and engineered valves. From the manufacturers and distributors’ perspective, conformance to the 25th edition will drive change over time toward more standardized and rationalized products.
The task group responsible for the revision of API 6D includes subject matter experts from operators, manufacturers, consultants and regulators from the United States, Canada, Italy, Norway, France, United Kingdom, Saudi Arabia, Brazil and Colombia and others. Revising the document was nearly a three-year process and involved nearly 100 volunteers.
Tables reproduced courtesy of the American Petroleum Institute. API 6D, Specification for Pipeline Valves. 25th Edition. 11/1/2021.
ABOUT THE AUTHORS


Ed Edgar is Technical Sales Manager – Offshore, Cameron a Schlumberger company. Ed is a Professional Engineer, and an engineering graduate of The University of Houston. He has been a design engineer and engineering manager in the Oil and Gas industry for 29 years. In his current role as Technical Sales Manager, he is responsible for technical support for all Cameron Valve products globally. Ed has participated in API and ISO standards development for 16 years and is Chairman of task groups for API 6DX and API 6DSSX, and is a task group member for API 6D, 6DSS and 6FA.


Wojciech Zmudzinski is a Professional Engineer, Mechanical Engineer graduate of University of Toronto, Canada, with extensive experience in valve design and manufacture, new technology qualification and testing, service failure analysis and repair. In his current role at bp America Inc. as Engineering Advisor for Valves, Wojciech provides guidance and deep discipline expertise in valve and actuation engineering, covering detail design and analysis, manufacturing processes, valve qualifications, and testing, supports operations with failure investigations and root-cause analysis, risk assessments, and equipment criticality evaluation. Wojciech represents bp in several API task groups, including API 6D, 6DSS, 6DX, and 6DSSX.