Although high-quality valves are available from a range of original equipment manufacturers (OEMs), valve performance issues will invariably occur. Over time, pressure swing adsorption (PSA) process pressures ranging from 300 to 700 psi contribute to equipment wear and result in leakage. This can impact process efficiency along with the volume and purity of the hydrogen end product. Leakage at the valve seat or stem also raises the risks of fugitive emissions and non-compliance with environmental regulations.
By Cris Sidwell, Global Product Leader, Control Valves – Flowserve
Pressure swing adsorption (PSA) applications are essential to operations in chemical plants, oil refineries, and other facilities that separate and purify a wide range of industrial gases, including hydrogen. Dozens of control valves, along with isolation and on-off valves, are installed with piping and instrumentation on large skids paired with adsorbent beds in the PSA process.
Less-than-optimal valve performance or equipment failure that disrupts production can create significant unplanned expenses for unit operators. However, companies can avoid unexpected downtime and delays — which in some cases, add up to millions of dollars — by taking the following three steps:
- Select the right valves for PSA application requirements with an emphasis on maximizing reliability.
- Ensure the valve supplier can provide expert, timely support, and services when urgently needed.
- Complete projects on agreed-upon schedules and within budget by partnering with an OEM experienced in PSA applications.
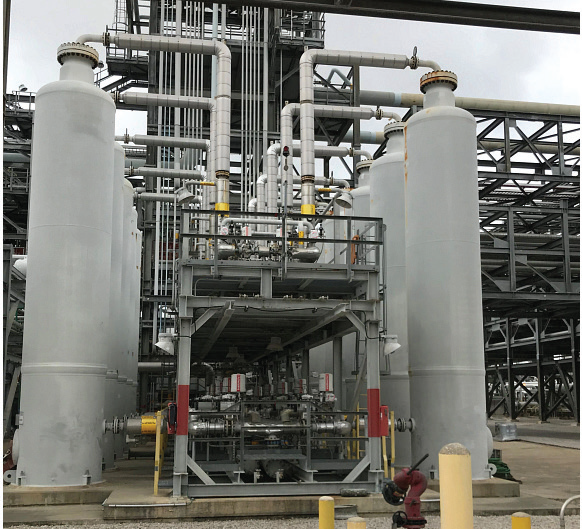
Major Challenges: High Cycle Rates and Pressures
PSA skids designed for hydrogen production incorporate dozens of control valves opening and closing in the right sequence at the right times. Most valves — along with the associated pneumatic actuators and positioners — cycle 120,000 to 150,000 times a year.
The high process pressures are necessary to separate carbon from methane in the feedstock to produce hydrogen. Cycling the pressure in the beds as many times a day as possible maximizes the amount of hydrogen produced. But the extreme conditions take their toll on valves; it causes wear of valve seats, as well as the guides in globe valves, and the bearings in butterfly valves, which degrades shut-off capability and process control.
Another common failure mode is when valve stem leakage is caused by packing wear or failure, which can result in the loss of valuable gas feedstock and purified hydrogen. Stem leaks also release fugitive emissions, raising safety concerns and causing compliance issues.
The high number of cycles takes its toll on actuation as well. Piston or diaphragm seals can wear, causing pneumatic actuators to become less responsive. This leads to the loss of precise valve control. Actuator springs and connection points can also be affected. In such cases, actuators can lose throttling capability or the ability to move to a fail-safe position in the event of power loss, while valve-to-actuator and positioner-to-actuator connections can loosen over time and result in decreased throttling accuracy.
How to Address Common PSA Skid Valve Issues
When selecting butterfly or globe valves for PSA applications, it is important to consider how the valves are engineered to resist wear to deliver control accuracy and rangeability.
Here are three steps one can take, along with questions to ask OEMs, to enable them to confidently choose flow control equipment for PSA applications in operations:
1. Select the right valves for PSA application requirements, with an emphasis on maximizing reliability.
Control valves on PSA skids must maintain tight shut-off. Unit operators should thoroughly evaluate valve design with respect to the most common wear points previously noted.
Underperforming valves can adversely affect process efficiency and lead to unnecessary maintenance and repair. However, wear-resistant globe and butterfly control valves are ideal for PSA processes if they are designed to meet stringent leakage requirements and can tolerate rapid cycling.
This is why some manufacturers subject their valves, actuators, and positioners to rigorous one million-cycle endurance tests. The test results are accepted as proof that the equipment can withstand the high cycling rates and temperatures typical of operating conditions in PSA applications.
Reliable high-cycle performance starts with thoughtful design. Seat design is a key differentiator among high-performance butterfly valves. The first recommended step is therefore that an individual specify a butterfly valve that has a seat design that adjusts to maintain contact with the disc, even after wear. This is less of an issue with globe valves, which have a tapered plug that can be driven farther into the seat to maintain proper contact.
- Material choices impact durability and wear as well. Specify a seat design that includes ultra-high molecular weight polyethylene (UHMWPE) components. This material possesses excellent wear resistance and can prolong seat performance.
- The operator should make sure to specify high-cycle, fluid power units when it comes to actuators. They should include wear-resistant seals, long-lifecycle springs, and very tight connection points with the valve and positioner. Splined shafts are best. It is best to avoid designs with a mechanical adapter between the shafts because of the high incidence of wear at the connection point.
- One should also avoid NAMUR connections between the actuator and the positioner. While adequate in many applications, they are not tight enough for the high cycling of PSA applications. They tend to wear quickly and lose throttling accuracy. A better alternative is a connection that utilizes a spring that biases the positioner shaft to maintain positive contact with the actuator linkage.
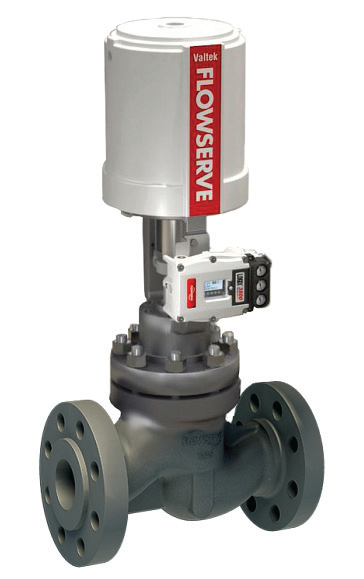
Key questions for plant operators to answer:
- Has the valve/actuator/positioner completed a one million-cycle endurance test per the rigorous procedures accepted by PSA process licensors?
- Is the valve/actuator/positioner li- censor approved for use in PSA applications?
2. Ensure that the valve supplier can provide expert, timely support, and services when urgently needed.
PSA is a demanding application for valves and related automation equipment. Even the best valves on the market can fail. When they do, an offline PSA bed can shut down as much as 20% of a refinery’s capacity, potentially costing millions of dollars each day.
Avoid this risk by working alongside an expert partner who provides superior technical support and services that minimize planned and unplanned downtime.
Confirm that the valve OEM has PSA unit experience and offers remote and on-site technicians to quickly trouble-shoot issues and make repairs. Some OEMs provide aftermarket support by referring you to a third-party workshop. A better option is to partner with a valve provider that has a global network of quick response centers located in the same country or region as your production facilities. This will provide the user with immediate access to the engineers who designed the valves, actuators, and positioners, and experienced technicians trained to work on the equipment.
Long-term Service Agreements to Improve PSA Valve Reliability.
Many OEMS offer long-term service agreements to ensure their fl ow control equipment meets performance expectations. Agreements can be designed around key performance indicators (KPIs) to ensure that the PSA unit supports the business objectives.
Look for a partner who can:
- Create a program based on a budget and KPIs,
- Support only those assets deemed necessary,
- Incorporate parts, on-site or off-site support, repair/upgrades, and training programs.
Smart Monitoring to Predict Maintenance Needs.
Further insights and support are avail- able by utilizing smart positioners and advanced predictive maintenance solutions that monitor and analyze valve conditions and performance. In addition, some OEMs operate remote monitoring centers where trained specialists track equipment performance and identify issues inside valves and positioners before they disrupt production.
These advanced solutions can enable unit operators to schedule needed maintenance before equipment issues occur. They can extend the time between maintenance, minimize unplanned downtime, and help reduce costs.
Key questions for plant operators to answer:
- Does the OEM operate a global network of response centers staffed by engineers and expert specialists available to support the PSA applications locally?
- Does the OEM also offer a predictive maintenance solution based on digital condition monitoring and analytics?
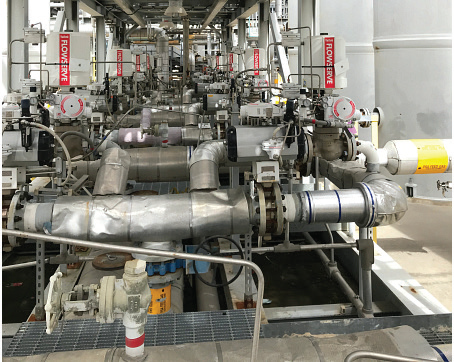
3. Complete projects on agreed-upon schedules and within budget by partnering with an OEM experienced in PSA applications.
When OEMS do not deliver valves and other flow control equipment on time, significant project delays and missed production targets result. The unplanned costs escalate quickly for plant operators, their engineering, procurement and construction consultants, and the PSA skid licensors.
Ideal solutions can be found by working with a valve OEM who employs a project management team with a history of successfully supplying PSA solutions. These specialists will not be surprised by the quality and testing requirements specified by PSA skid licensors, contractors, and end users.
Be sure to partner with a flow control OEM that has a reputation for delivering, installing, and commissioning valves and other equipment on time for PSA applications.
This becomes especially important when global supply chains remain constrained and difficult-to-source materials or parts are necessary to complete the PSA project. It is important to look for a partner that has established business relationships worldwide along with global service capabilities. The OEM’s project tmanagement specialists will be able to call upon their supply chain contacts to meet the project’s timeline.
Key questions for plant operators to answer:
- Does the OEM have a proven record of delivering valves and other equipment for PSA units according to agreed-upon lead times?
- How many times has the OEM completed PSA unit projects with licensors?
- How prepared is the OEM to leverage multiple suppliers when necessary to expedite the materials and components needed for the PSA project?
Picking the Ideal PSA Valve Partner
Select reliable control valves, actuators, and positioners that can withstand the high pressures of PSA skid applications to increase process efficiency and/or the quality of the hydrogen produced. These choices can enable unit operators to avoid un- planned downtime, maintenance, product loss, and penalties and/or fines incurred for regulatory non-compliance that can cost plant operators millions of dollars.
The three steps recommended herein can help. Completing each with the support and services of an expert PSA valve partner can prevent costly risks. Instead, the company will be able to meet hydro- gen production targets for quality and profitability while also ensuring uninterrupted plant operations.
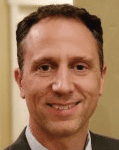