In this article, we will explore what makes a plant ‘aged’ and what problems tend to keep aging plants’ managers awake at night.
By Davi Sampaio Correia – Technical Consultant
Definition of Aging Plants
A government agency in the United Kingdom (U.K.), the Health and Safety Executive (HSE), has defined what makes a plant ‘aged’. It states, “Aging is not about how old your equipment is; it is about its condition, and how that condition is changing over time. Aging is the effect whereby a component suffers some form of material deterioration and damage (usually, but not necessarily, associated with time in service) with an increasing likelihood of failure over the lifetime”(1). Another way to express this concept is to relate aging with fitness for purpose. That is, a plant where deterioration or obsolescence has compromised its capacity to operate in a safe and reliable way.
Deterioration may be caused by several mechanisms that may either act in an isolated or combined manner. In fact, plants may have a combination of these mechanisms in a specific location but not in others. According to the HSE, the three most dangerous aging mechanisms are erosion, corrosion and fatigue:
“Recent research shows that 50% of European major hazard ‘loss of containment’ events arising from technical plant failures were primarily due to aging plant mechanisms such as erosion, corrosion and fatigue. These ‘aging’ events equate to an overall loss of 11 lives, 183 injuries and over EU €170 million of economic loss. This demonstrates the significant extent and impact of aging plant-related failures on safety and business performance”(1).
The International Atomic Energy Agency (IAEA) has other important definition related to aging; one originally linked to nuclear plants but also useful for other companies. According to the IAEA, aging management is defined as the coordination of existing programs in order to understand, monitor, and control the aging effects on structures, systems and components of a plant(2). The IAEA’s ‘programs’, refer to: maintenance, in-service inspection and surveillance, as well as operations, technical support programs (including analysis of any aging mechanisms) and external programs such as research and development.
The top 10 issues we will explore in this article are not aging effects, such as corrosion or fatigue, as they are specific of each plant. Instead, we will investigate aging management issues, as they are pertinent to any industry.
1. Workforce – Senior Employees, Newcomers, and Training
When senior employees retire, they take with them part of the plant’s history, which may contain subtleties not formally recorded or, if recorded, difficult to retrieve. Many problems tend to repeat themselves and if proper care is not taken to train a new generation before the senior employees retire, there is the risk of ‘reinventing the wheel’ many times over.
In theory, this could be mitigated by an adequate ‘overlap’ with a young employee. In practice, there are two problems. First, recruiting bright young men and women to work in the industrial field has its own challenges. Even more if they perceive the plant as less-than modern (to use a euphemism) and lacking the allure of some technology companies. Second, management must come up with a very well-structured training program in order for the expected knowledge to be passed along. If simply left to wander together through the plant, it is less likely for the knowledge to flow from the more experienced to the newcomer, as in an osmosis process. The most probable outcome is that both will carry on their regular duties and exchange no more than pleasantries.
In short, a successful training program requires time and effort to provide adequate mentoring, goals and feedback. What is the content that should be learned? What is the time available for learning? What are the tools required? How will this knowledge intake be measured? These are some of the questions that need to be answered for a training program to succeed.
2. Operational Procedures
As a plant ages, practices allowed in earlier life may now stress components beyond safety. Repeated training is required for all operators to adapt to the new procedures. This is particularly hard for senior operators as some respond to the new procedure with a mental attitude of, “But I have been working the other way my whole career!”.
Combining new and old equipment may also be another cause of change in operational procedures. For example, “in a system with a new and an old electric generator connected in parallel, the higher failure rate of the old generator may lead to repeated overloads and a faster degradation of the new one”(3). Therefore, a proper operational procedure needs to be written to combine the various pieces of equipment.
Procedures related to the recognition of aging mechanisms and their warning signs should be regularly revised. Vibration in a new piece of equipment may require immediate attention. In older equipment, it may be normal and under the acceptable value. A new piece of equipment’s given corrosion rate may be high but acceptable, short-term. An older piece of equipment with the same rate may be unacceptable due to the accumulated reduction in wall thickness since operation began. Equipment training for operators must address these issues, or risk failure due to insufficient skill to discern between the ‘old abnormal’ and the ‘new abnormal’.
3. Changes in Standards and Regulations
Concerns about occupational health, safety, and environmental issues have led to more stringent standards and regulations worldwide. They may not be at the same point in the road, but they are all heading the same way. Do you remember coal-fired plants? The light rain of black dust that covers everything; the smell; the smoke – a bleak scene straight from a Dickens novel. While coal is still being used, it is clear that its importance is only diminishing. In New York State, for example, the last coal-fired power plant closed its doors in March 2019(4).
Workplace safety is another critical concern. According to the United nations (UN), “toxic exposures kill workers once every 30 seconds, while a worker dies from workplace hazards more generally every 15 seconds”(5). Toxic exposure is particularly harmful due to possible cumulative effects – although it may not be immediately lethal, it will eventually lead to negative health impacts.
For many aged plants with the inability to cope with the regulatory wind, shutdown and decommissioning are the common fate, but this result is avoidable. Many companies are not only complying with the regulations but sometimes go above and beyond them. Siemens, for example, is pledging to have carbon neutral operations by 2030, with measures such as increased use of renewable energy and efficiency optimization at its plants(6). For Siemens, linking greener practices with long-term growth is not only prudent but profitable.
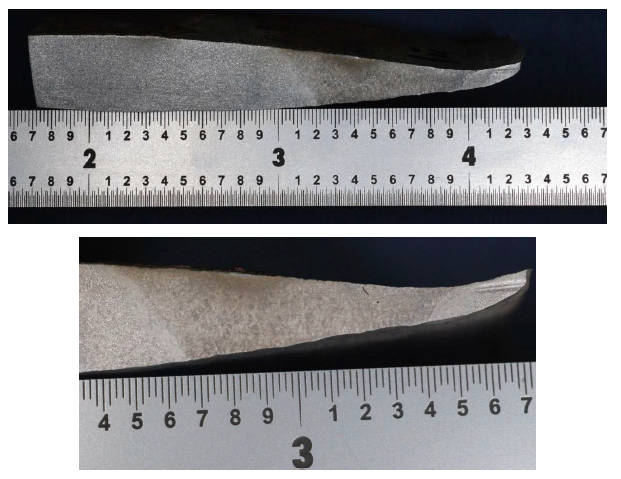
4. Adequate Information
Information is the very foundation upon which a successful aging management program is built. Essentially, there are four streams of information required throughout a plant’s life. One or more information systems are generally used to keep track of them:
Plant Condition (Including Structures)
This is often understood as the maintenance records and the results of the frequent inspections of the various components used in the plant. However, it should also include records related to the instrumentation history such as pressure, flow, temperature and changes in raw materials.
Deteriorating Mechanisms
The information in the previous paragraph fuel the analysis of which deteriorating mechanisms are the cause of aging, what measures can be taken to mitigate or lessen their effect, and what rate is expected for them to progress.
Management of Change (MOC)
Repairs, overhauls and retrofitting are routine tasks that may not leave a plant in the original condition. All the modifications that cannot be classified as ‘replacement in kind’ must be recorded as MOC and the related documentation must be updated.
Codes and Related Documents
Design codes are reviewed frequently, as the knowledge on certain subjects is refined and updated by science. Some old assumptions may no longer be permitted under the revised code, which requires an analysis determining whether the original design is outdated but still valid or if a previously unknown mechanism now requires review. Changes in design codes may also trigger a review of the original hazard and operability study (HAZOP). Are the original assumptions still valid? Has any process modification invalidated them? What aging mechanisms were overlooked? The history of breakdowns, MOC, turnaround and accidents (both local and from similar plants) must feed this review.
In 2009, there was an explosion followed by a fi re at the Silver Eagle Refinery in Woods Cross, Utah, where several homes were damaged. The cause was a rupture in a pipe, severely damaged by corrosion (sulfidation). In a report commissioned by the U.S. Chemical Safety Board (CSB)(7), the pipe’s wall thickness ranged from 0.570 to 0.032 inches, as the measurements progressed near the fracture surface. The metal loss was estimated to have occurred undetected in the course of 14 years. This is just one example of how the lack of adequate information can lead to a negative outcome. See Figure 1 for an example of metal loss in the piping.
5. Understand the Aging Mechanisms – Multidisciplinary Approach
Industrial plants are complex environments, not only because of the sheer number of components, but also because of the various ways these components can interact and influence each other.
A change in raw material composition may trigger a new aging mechanism. A valve replaced with a heavier version of the same model may be responsible for fatigue cracks. Changes that may appear innocuous to the operating team may prove disastrous in the long run. That is why the process of understanding the aging mechanisms must involve professionals from different fields – one sees what others may not even notice. Some common disciplines involved for this task are engineering (process, mechanical and electrical/instrumentation), operations, and health, safety and environmental. Without proper understating of aging, the following steps of monitoring and mitigation are severely compromised.
6. Adapting Current Maintenance Programs
Even before a plant has its first start-up, a maintenance program is already running. As part of the Asset Integrity Management (AIM) plan, the maintenance program is expected to be reviewed and modified in accordance with the aging mechanisms at play. For example, inspection frequency may be updated, and some new techniques may be required to monitor the progress of damage. At the same time, there is a list of routine activities – like painting, lubricating, etc. – that do not change much since the plant’s start-up. The latter can be known as ‘maintenance management’.
Some companies prefer to keep maintenance management and aging maintenance under one roof. Other companies prefer to create two separate structures. These two types of maintenance share some of the same goals – both are used to keep the plant reliable and safe. “However, there are significant differences. On one hand, the main objective of maintenance management is to keep the plant in good operating condition and to optimize equipment availability.
On the other hand, aging management is focused on assessing and handling the aging and degradation of the plant, and on developing a plan to extend its lifetime in a safe way. Therefore, it seems logical to consider the management of aging as an additional factor that should be included in the general maintenance management of the facility. A key issue for a successful integration requires finding out how the new requirements will affect and modify the existing maintenance management”(3).
7. Mergers and Acquisitions
Mergers and acquisitions involving old plants may require the harmonization of different business cultures and AIM practices. Additionally, other various aspects can differ including the information systems, as well as the maintenance software that records and schedules tasks. This is a huge problem, and one with no simple recipe to solve. The only guidance for this type of situation is to have resources (time, people, tools) set aside to delve into the differences, and create a detailed plan stating how the two strategies will be merged or the reasons why it would be best to separate them. It is crucial to remember that some equipment may have insufficient documentations or records about maintenance, aging mechanisms, MOC, etc., which will require an initial screening with several inspections techniques, and will need to be reviewed before discussing the possibility of a merger.
8. Finding Replacements
Some companies had theirs plants built with such efficient designs and high-quality materials that the service life can easily reach 30 years without major modifications to the original equipment. This is often the case in nuclear power plants. As time passes, however, many of the original suppliers may no longer be available, or most likely, have modified their designs. Additionally, some of the more specialized equipment can only be provided by a few suppliers, and these suppliers have an international clientele, which may cause severe backlogs. The risk in these cases is to succumb to the operational pressure and accept ill-fitted adaptations – ones that were not adequately vetted by a multidisciplinary committee in a thorough MOC process.
9. Cybersecurity
Since the Stuxnet discovery in 2010, more and more companies became aware of the possibility of cyberattacks. The Stuxnet is “a malicious computer worm, first uncovered in 2010, thought to have been in development since at least 2005. Stuxnet targets supervisory control and data acquisition (SCADA) systems and is believed to be responsible for causing substantial damage to the nuclear program of Iran”(8). In a plot apt for a science fiction movie, Stuxnet reportedly compromised the plant’s programmable logic controllers (PLCs) and caused fast-spinning centrifuges to tear themselves apart. Yes, a computer virus interfered with process parameters and caused the destruction of important equipment. In a less sophisticated attack, a substation in Ukraine was targeted in 2016 and Kiev experienced an hour-long blackout(9).
Companies should take such possibilities seriously and search for reliable partners that can help “design, test, certify, and secure their internet-connected devices, networks, and control systems”(9).
10. Disruptive Technologies
In the recent past, technologies took a long time to be adopted and reach consumers (see Figure 2). Telephone landlines (do you remember them?) took 50 years to reach 50 million users. Mobile phones reached the same level in 12 years. What was once a staple of any home, is barely recognized by many children, today. This kind of disruption occurs in the industrial world as well. Kodak, for example, once a powerhouse in the film industry, fi led for bankruptcy in 2012.
Keeping your business relevant has never been more challenging. Surviving in the 21st century requires constant education and diligence to be aware of what is being researched and likely to impact your particular industry. Attendance to trade shows and conferences, reading your industry’s magazines, and curating the right network of knowledgeable people, is the least one can do.

https://www.visualcapitalist.com/how-long-does-it-take-to-hit-50-million-users/
REFERENCES
1) HSE (Health and Safety Executive), RR823, Managing Ageing Plant – A Summary Guide, P Horrocks, D Mansfi eld, K
Parker, J Thomson, T Atkinson & J Worsley, available at https://www.hse.gov.uk/research/rrpdf/rr823-summary-guide.pdf
2) IAEA (International Atomic Energy Agency), Ageing Management for Nuclear Power Plants, Safety Guide No. NSG-
2.12, available at https://www-pub.iaea.org/MTCD/publications/PDF/Pub1373_web.pdf
3) Pedro A. Peréz Ramırez and Ingrid Bouwer Utne, Challenges Due To Aging Plants, Published online 11 April 2011 in
Wiley Online Library (wileyonlinelibrary.com). DOI 10.1002/prs.10453.
4) https://www.nytimes.com/2020/03/20/nyregion/coal-energy-ny.html
5) https://qz.com/1564995/toxic-exposure-at-work-kills-one-worker-every-15-seconds/
6) https://new.siemens.com/global/en/company/sustainability/decarbonization/carbonneutral.html
7) https://www.csb.gov/-csb-releases-analysis-showing-cause-of-rupture-and-hydrogen-blast-in-2009-silver-eaglerefi
nery-accident-in-woods-cross-utah-pipe-walls-thinned-due-to-corrosion-that-went-uninspected-for-years-/
8) https://en.wikipedia.org/wiki/Stuxnet
9) https://www.ge.com/power/transform/article.transform.articles.2017.nov.6-problems-keeping-power-plant#
10) https://www.visualcapitalist.com/how-long-does-it-take-to-hit-50-million-users/