One of the most challenging tasks for the process and power plant design and maintenance industry has always been valve sizing and selection. While understanding the theories of flow control is vital in this industry, it is also important to consider some often overlooked aspects of the selection criteria and the tools that help avoid common mistakes.
By Alex Koifman, Instrument Management and Business Process Consultant
Historical Progression
It is not uncommon that when the economy is facing challenging times, industry veterans take off their hard hats and decide to enjoy their earned and sometimes delayed retirement. The pandemic disruption of 2020/21 saw a steady stream of ‘right-sizing’ and early retirement packages offered to many long-term manufacturing employees. This opened a pathway for younger engineers to step up.
The challenge with this phenomenon is that a significant amount of experience and know how can be lost with each passing of the hard hat. Today there is a huge proliferation of instrumentation and automation for monitoring and maintaining valves. Cybersecurity, alarm management, field network technologies, advanced process control applications, and remote monitoring solutions, did not exist 30 years ago. This caused great expansion of instrument and valve engineers scope and responsibilities diluting the physical valve focus.
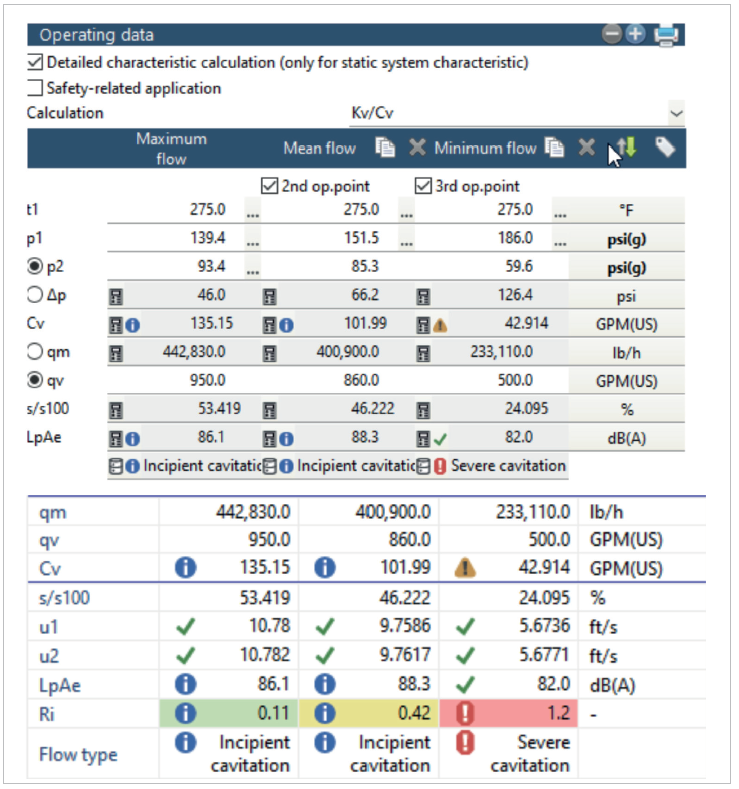
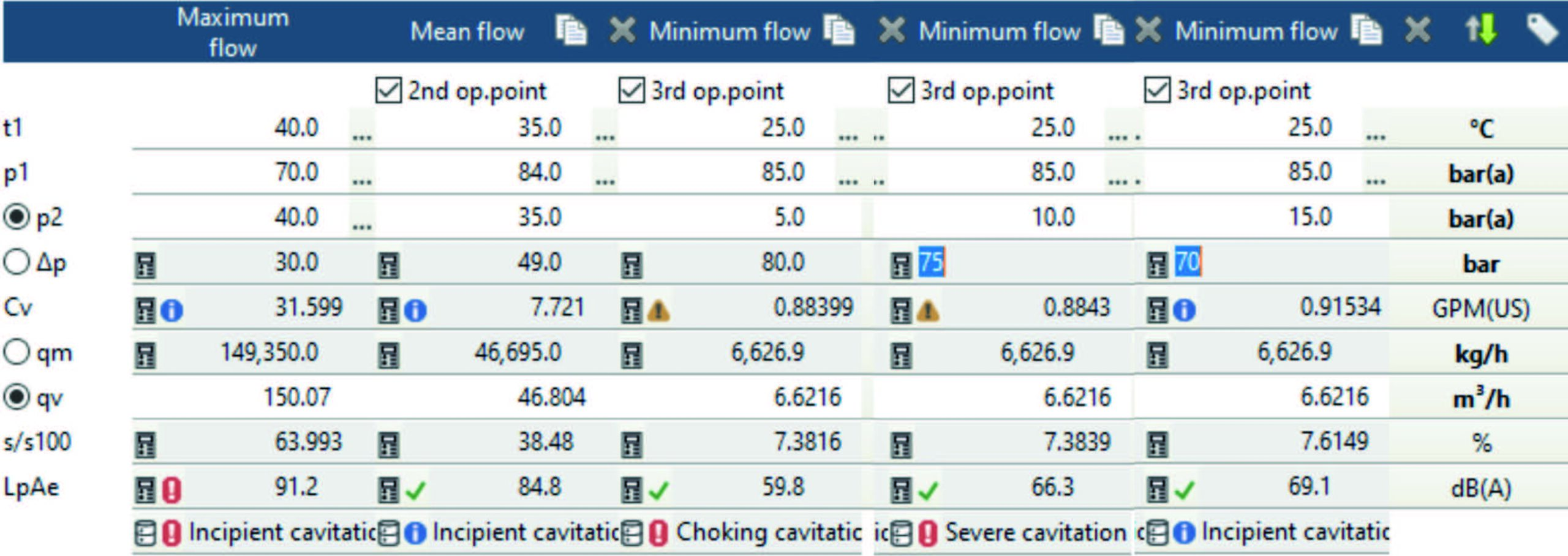
As 30 years ago flowmeter or valve sizing was often done by hand, or early computer applications, knowing the flow measurement and control fundamentals was a must for instrument and valve engineers and specialists. Now, many engineers who enter the industry take on the challenges accompanying building and maintaining plants, sometimes without experience and in many cases without even the base skills. The industry was as much impacted by the globalization and new business practices as it was by the technology advances. Corporate engineering centers that once employed thousands of engineers have given way to turnkey EPC projects, often with fixed cost contract basis. Late 90s and early 2000s saw multi-story buildings filled with engineers working on energy, chemicals, and power projects. This workflow then transitioned to a distributed engineering model where the projects were done and instrumentation and valves were manufactured thousands of miles away from users, sometimes reducing local engineering, sales, and services providers to the role of business, project management and communications experts, which naturally alters their needs for practical skills. That in turn gave the rise to the equipment manufacturers themselves providing more and more added value engineering services to fill in the gaps created by these changes.
This is a business trend that is increasingly seen in the modern instrumentation and valve business. One could ask – why such a history detour in the article about valves? It is here for the simple reason that without understanding the causes of today’s challenges one cannot affectively address these challenges and find both business and technical solutions. Industry has to face new workforce skills, short and long term disruption to the traditional supply chains including engineering and, as a core solution, technical competency and knowledge retention. Valve sizing and selection is one of the areas where this knowledge acquisition and retention is equally critical for operators, vendors, and engineering.
Valve Sizing and Selection
Anyone who has worked with valves can typically recite the key criteria for reliable valve selection; valve type, size, noise level, presence of cavitation, and corrosion protection. Unfortunately, other, less common criteria are often overlooked amidst the time, cost, and resource pressures of the project.
There is no question today, in the age of global high-speed internet coverage, that the availability of automation tools is essential for every profession and task. One of the biggest challenges associated with automation tools is ensuring that the correct data is used. The first criteria
that should not be overlooked for valve selection, is therefore the application process and piping data as well as the type, geometry, and configuration of the valve. Without accurate information, the output of the sizing tool is unreliable and sometimes misleading, defying the whole purpose
of the sizing and selection process.
The second criteria to be sure to consider is the cavitation index. If a vendor does not publish cavitation index, finding the valve that will match the application can be very difficult. Other parameters, though often hard to obtain and evaluate, are just as important. Take a pressure loss, for example. The effect of the 1.5 Mw power loss on a 20” valve may be negligible,
but the same pressure loss dissipating kinetic energy of the fluid on a 3” valve may have a very destructive effect. Not only will it elevate noise, which is one of the key and easy to observe indicators, but also increasing vibration downstream, potentially leading to a failure.

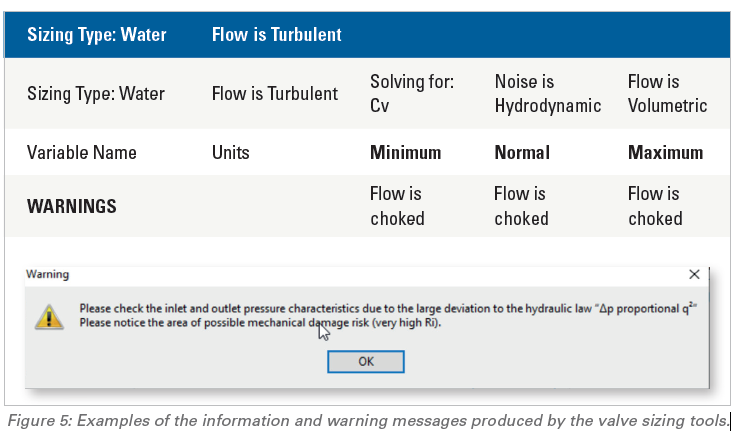
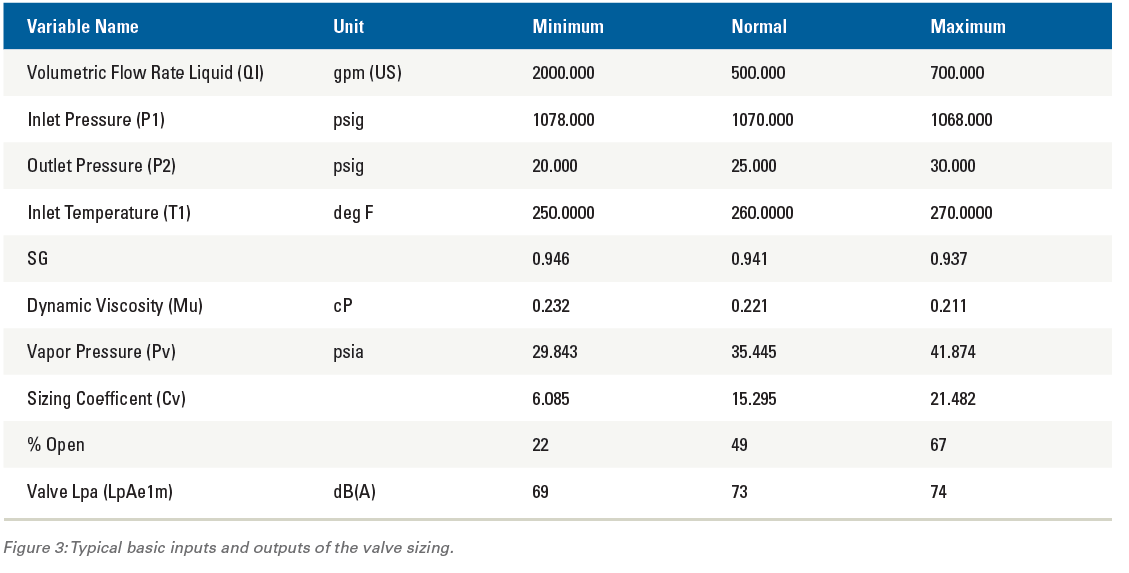
Determining the Correct Valve
So how does an end user select the right valve? The answer is simple: evaluate all the parameters that are affecting the valve, the behavior and controllability of the flow, and the reliability of its operation in the context of where the application will be used.
Knowledge and expertise are not the only ingredients for success in valve sizing. Knowledge of where and how the application will be used is essential. For example, it is often assumed that if a valve fails, it can be replaced with the same valve. As factors like a flow and upstream pressure can change during the lifespan of the failed valve, it is best not to assume that the specifications for the original valve will be accurate for the replacement valve. It is essential that the process and piping data given to the valve supplier is up-to-date and reviewed by the process or unit engineer. Figure 1 highlights an example of a small progressive decrease in the pressure drop of the minimum flow from 80 bar to 75, and finally to 70. It also shows how the change in the flow behavior from choking, to severe, to incipient cavitation, drastically affects the valve.
Another example can be seen in Figure 2, where severe cavitation in the 6” water service valve caused a significant industrial incident. High outlet flow velocity effected the bend in the outlet pipe which unlimitedly caused a hole in the pipe, which in turn damaged nearby process equipment causing a fire.
Automation Tools
The industry today has multiple vendor specific and few vendor independent tools, such as CONVAL and InstruCalc. A common practice is to use vendor a specific tool to find approximate values of the Cv and size or perform preliminary calculations. This practice, however, does not fit well when looking for severe service applications or challenging process conditions where precision and reliability are critical.
Most tools will provide basic calculations and criteria as well as graphic clarity on these. Basic tool will provide calculated values for defined applications operating points – inputs, intermediate calculated vales and primary calculated values are clear and easy to understand, similar to the data shown in Figure 3.
A high-performing software will show where these operating points are on the Cv curve to provide a good assessment of how fit a valve is for the application’s primary purpose of flow control. It will also show when the valve is not a good fit, as seen in Figure 4. Here the minimal flow conditions occur at the start of the valve opening when flow turbulence prevents good flow control. The highest quality tools and software will provide an additional assessment of how well the chosen or evaluated valve fits the application, as shown on Figure 5.
A good tool will also allow the user to extend the assessment of the application beyond the one, two or even three operation points. It will provide a simulation of the operation and valve parameters at the full span rather than on discrete operating points, see Figure 6. Ideally, the tool will consider and factor in additional parameters like pressure drop, valve authority, the temperature at vena contracta, outlet flow velocity, and others to make recommendations as shown in Figure 7.
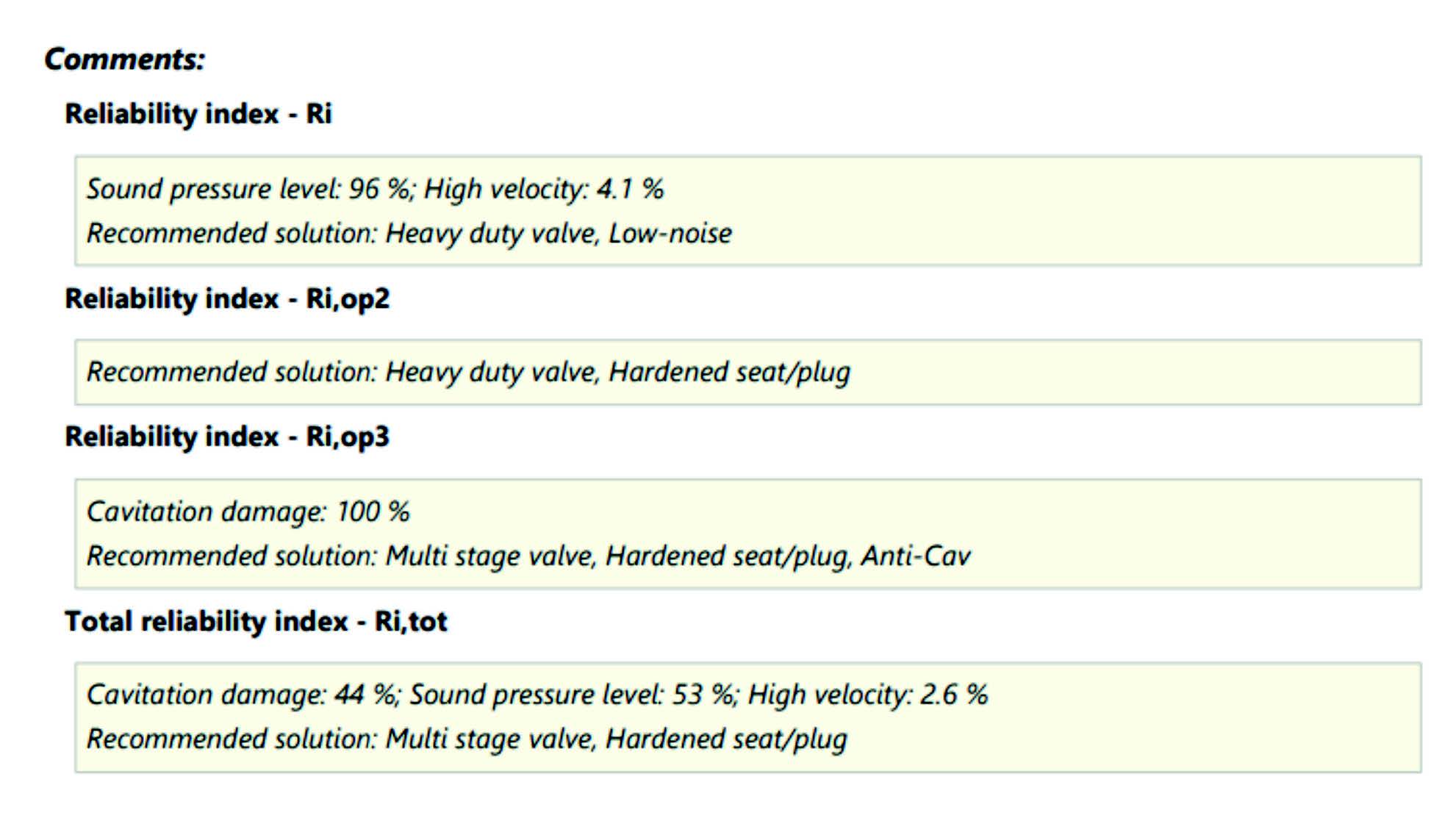
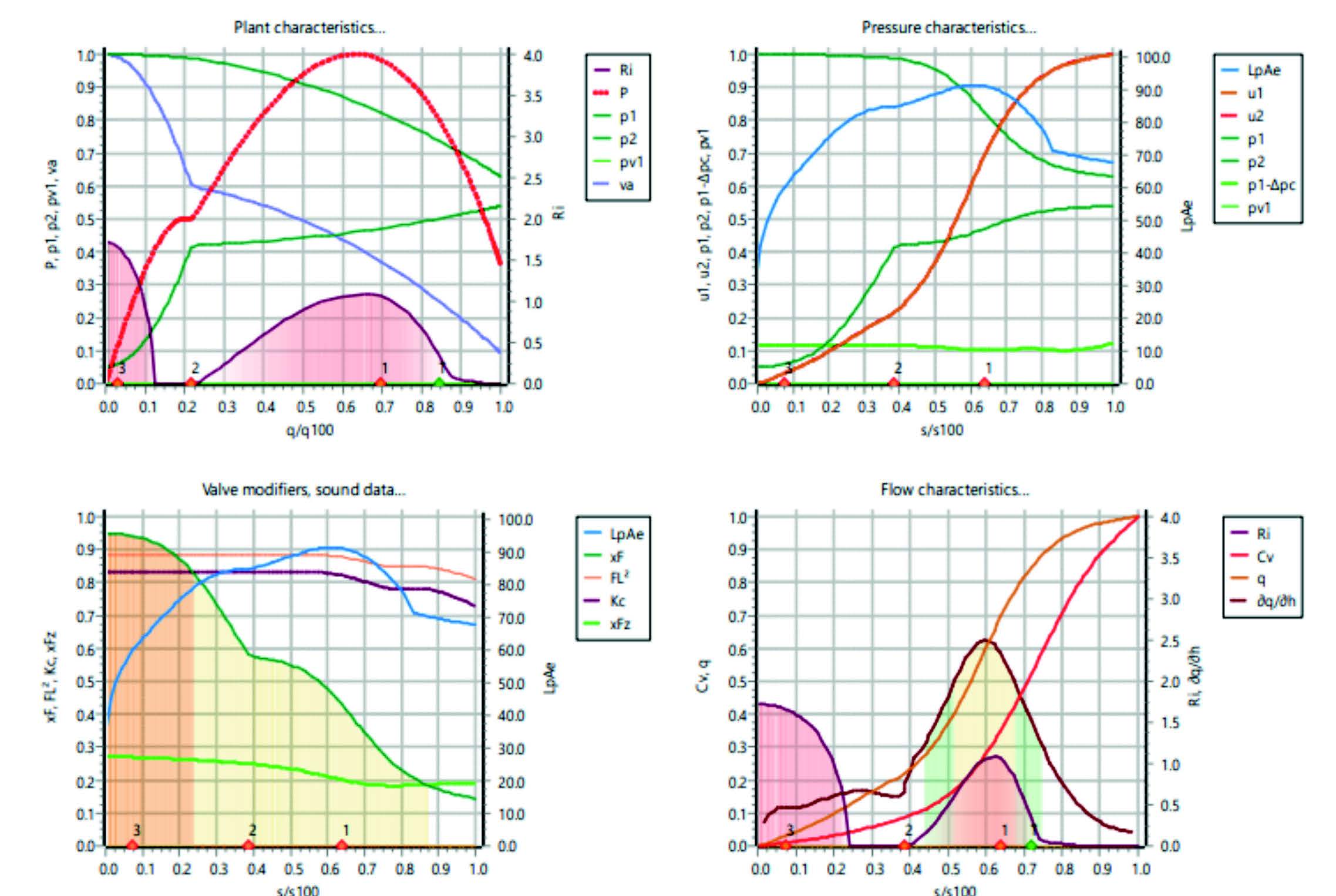
Final Thoughts
In summary the demographic and business realities of the modern time dictate that expert knowhow and experience ought to be coupled with sophisticated advanced tools to provide consistent and optimal results. The use of tools and ensuring that criteria are not overlooked will maximize productivity and the reliability of process industry. Automation tools cannot replace the essence of engineering – knowledge, critical thinking, team work, nor can they be a substitute for often intimate manufacturer knowledge of how their valves perform, but it can supplement and help these tasks to reduce variability and increase consistency of the positive results.
About The Author
Alex Koifman, instrument information management and business process consultant, has been involved in instrument plant design and valve sizing software systems since 1995 in a variety positions for engineering and software companies, including Intergraph (Hexagon) and F.I.R.S.T. GmbH. His current focus is introduction and support of the CONVAL® – world’s leading valve and instrument sizing application – in North America. He has been involved with Valve World since 2017 and has been moderating Valve World Americas workshops since 2019. He also contributed to the work on the WIB Recommended Practice S 2812-X-19 leading to the development of the ISO 5115. At the Valve World Mexico 2022 he will participate at the Valve selection panel and present advanced valve sizing and selection application at the Control Valves track.