“Iran is one of the biggest countries in the oil and gas industry. When I was a student, my brother was working as a mechanical engineer and he introduced me many different types of engineering work in the industry. I found piping engineering to fit well with my interests and also my studies, because having a background in Material Engineering is very important in selecting materials for piping and valves,” explained Mahsa.
“Within industry, piping is a system of pipes used to convey fluids such as liquids and gases from one location to another. The engineering discipline of piping design studies the efficient transport of fluid. Generally, industrial piping engineering involves three major subfields: Piping Materials, Piping Design and Stress Analysis. The knowledge of corrosion and protection is needed for determining how to protect pipeline/piping in corrosive environments.”
Mahsa has spent over a decade working for five different companies on eight different big projects. Arriving in the United States in 2014 as a permanent resident, Mahsa began working as Piping Lead Engineer for Orascom E&C based in Houston,Texas.
Orascom Construction Limited is a leading global engineering and construction contractor primarily focused on infrastructure, industrial and high- end commercial projects in the Middle East, North Africa, the United States, and the Pacific Rim for public and private clients. Orascom E&C USA Inc., is Orascom Construction’s wholly owned engineering and construction subsidiary based in the United States. With its Head Office located in Mclean, VA, Orascom E&C is specialized in the construction of large industrial facilities including two new projects: a Debottle-necking facility in Beaumont, TX that will increase annual methanol production capacity by approximately 182,500 metric tons and annual ammonia production capacity by approximately 40,000 metric tons; and a $1.5 billion natural gas-based fertilizer production facility in Wever, IA that will produce 1.7 to 2.2 million tons per year of ammonia, urea, urea ammonium nitrate, and diesel exhaust fluid. This fertilizer plant is the first world scale facility of its kind built in the US in 25 years.
Mahsa is currently involved in the NatGas Methanol plant in Beaumont. The methanol production plant is be- ing constructed on a 514 acre plot of land located adjacent to the existing integrated ammonia and methanol production complex.The projects form the first phase of the larger gas-to-gasoline (GtG) plant proposed by NatGasoline. The second phase of the GtG plant involves the construction of a 22,000 barrel per day (bpd) motor-grade methanol to gasoline ( MtG) production unit us- ing the refined methanol either from the proposed new methanol production unit or other sources as feedstock. Air Liquid was contracted to supply oxygen to the plant and will also construct a new air separation unit (ASU) at the site to produce oxygen, nitrogen and argon.
“EPC projects have three parts; engineering, procurement and construction. This project includes all three parts. Engineering part which is detail design of our plant is assigned to our subcontractor Air Liquide in Poland. Procurement and Construction is handled by the Orascom team. In my role, I am interfacing between the different vendors and subcenters in piping discipline. I check and review all of the piping documents and would solve any issues that come up related to piping,” said Mahsa. “For example, AL engineering team will issue the valve data sheet for us and during the purchasing process, needs to review vendor deviations. I would review the documents and see if I can alter some requirements or review the technical offer from the vendor to make sure the deviation is acceptable or not. Then I would negotiate with the vendors, procurement and the design company to decide which is the best available option.”
In her current role Mahsa is supervising all piping deliverables by the engineer- ing contractor (Air Liquide) including 3D model, specifications, line list, ISOs, MTOs, piping plot plan layout and more. Resolving any issues related to piping materials, specifications, fabrication and field construction, she enjoys the diversity and challenges her role brings.
“Within industry, piping is a system of pipes used to convey fluids (liquids and gases) from one location to another. The engineering discipline of piping design studies the efficient transport of fluid.
Piping Engineering is wide and it can be challenging to know about all the components like pipes, valves, fittings, flanges, gaskets – how are the components used and what are the important factors to take into consideration? What materials should be used in which applications? What are the important industry standards used for piping components? There are many different components so you should know all information for each of them,” Mahsa revealed. “I like to learn new things and there are lots of matters related to piping that I can learn everyday which can be about corrosion, welding, inspection and more. It is so broad that if you want to change your area of focus, there are plenty of opportunities. It is good for me because I do not get bored at all in the piping field. It makes me feel alive. Everyday I can face to new challenges to solve.”
Though Mahsa thrives on the challenges, that does not mean that her role does not include some difficulties. Of- ten time and cost of projects can bring new challenges of their own.
“Sometimes you might have to search out ways to work more affordably and in reasonable time. It can make some decisions difficult. It can also make it challenging to find the best product for the application while meeting these parameters, but you never compromise quality and safety,” said Mahsa.
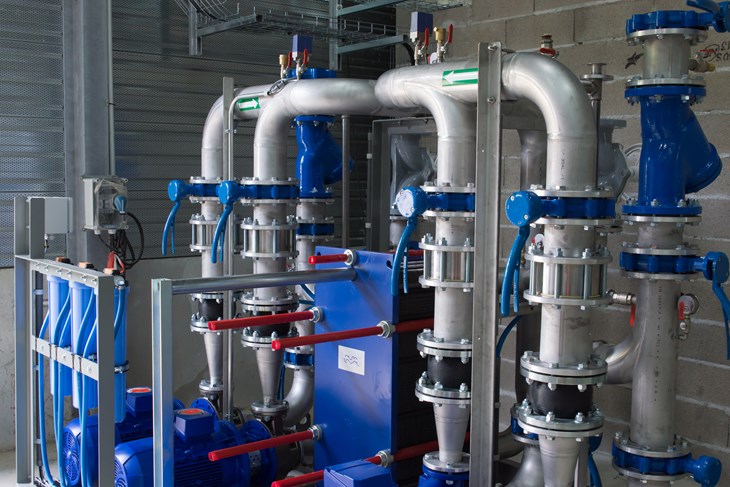
Volume of Valves
In the NatGas project, Mahsa estimates that the project will use approximately 5400 different valves including gate, check (swing, dual plate, non-slam), ball, butterfly and globe valves. The projects will use some specialty valves that have special requirements, such as valves for oxygen service that need to be free of grease or graphite and pressure relief valves which are used for tank protection.
“We are using some breather valves, also known as direct acting pressure/vacuum relief valves, which are special types of relief valves specifically designed for tank protection.The range includes pressure only, vacuum only and combined pressure/vacuum valves, all available with flanged outlets or vented to atmosphere. We also have some special swing check valves and wedge gate valves for oxygen service,” said Mahsa.
In the piping discipline, Mahsa’s team will prepare MTOs and then using an approved vendor list the procurement team will select 3-4 vendors to give their technical offers.
Piping team will check the vendor offers technically, verify their product catalogs, certification test report and prepare technical bid evaluations for piping components based on the vendor offers. Finally, the procurement team will make a final decision based on price.
While most of the valves being specified are commonly used in similar projects and are fairly easy to obtain through many vendors on the company’s approved vendors list, Mahsa explained that some specialty products and components that are more customized might not be as readily available as commodity products.
“Sometimes for special components we may have to purchase some materials from a new vendor. In this situation, the procurement team will usually search and find new vendors that are able to provide the components we need and will send their catalogues for us and the client to approve. We will verify that they can provide the exact product we need, review their certifications and the procurement team will help narrow down the choices based on price and time scheduling. After a vendor has been approved, it can be added to the vendor list going forward,” Mahsa explained.
While most valves she has encountered have worked as designed and in fairly straight-forward applications, Mahsa described how some valves can fail during the test phase, during a pipe test and she will be tasked with the repair. Once the valve passes all inspections it can be evaluated as acceptable for the job.
“We do our own testing, so I spend a lot of time performing these tests and following repair instructions from the vendor should they fail during the test. I check all the valves based on specifications and standards and once they pass all the tests, we can use it,” she said. “We find that some valves leak or they were not polished very well after welding, which can lead to corrosion after installation. This is something that should have been rejected during inspection, but once it has been installed they will come to me to see if it can be repaired or if it should be rejected and replaced. Some other issues we encounter are weld spatters on welds found under inspection, material deviations or the valve fails during a High Pressure Closure Test.”
Feelings on the Future
Mahsa believes that the industry has changed significantly in recent times and that ongoing technological advancements and the development of new software will continue to change the game. Innovation in 3D modeling, stress analysis software and material management programs are all ways that her role specifically has been positively impacted by technological advancements. Mahsa is also excited about the new possibilities these changes will bring to the oil, gas and petrochemical industry and the piping engineering field.
“My current project is the most interesting one for me. It is a big chance for me to work on this huge project and I learned a lot while working closely with European companies like our design firm, and many U.S. Companies and subcontractors,” concluded Mahsa. “Now I have a big picture of piping and I am involved with all parts of Engineering, Procurement and Construction from the beginning of the project until it will be completed.”