Commissioning a major industrial project is no simple task, and Peyman Naderi, a Senior Commissioning and Start-Up Engineer for SNC-Lavalin/Kent, knows this well. In order to adequately complete a project to all required specifications, Naderi must manage many moving parts, from the Front-End Engineering Design (FEED) through to eventual installation. Valve World Americas had the honour of speaking with rotating equipment specialist Peyman Naderi to discuss the commissioning process, common roadblocks, and what he believes is in store for equipment innovation.
By Editorial Team
A Career with Rotating Equipment
Peyman Naderi has had a long, eclectic career as a mechanical engineer, often specializing in the design and maintenance of equipment. He leveraged the knowledge gained in both his undergraduate degree (B.Sc., Mechanical Engineering) and master’s degree (MEng, General Engineering) to earn jobs at several global corporations, including MME GmbH (Mechanical Engineer), MAPNA Group (Senior Mechanical Rotating Equipment Engineer), ThyssenKrupp Industrial Solutions (Senior Mechanical Rotating Equipment Specialist), and now SNC-Lavalin/Kent (Senior Commissioning and Start-Up Engineer). Throughout his career, Naderi has worked in process plants, power plants, and several oil & gas projects. He possesses ample experience with both static and rotating equipment and knows the ins and outs of the oil and gas industry.
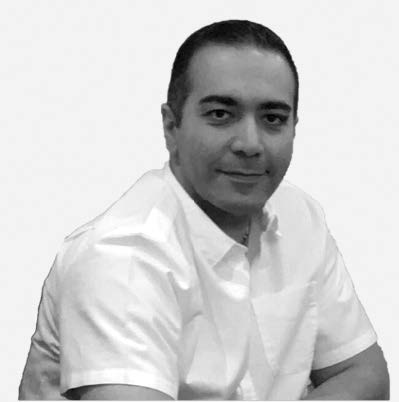
What Does a Commissioning Engineer Do?
“As a rotating equipment expert engineer, and now in my current role, I am doing mostly commissioning and start-up activities, including preparing deliverables with collaborations of other colleagues including process, instrumentation, and electrical engineers. Then I go to the site and lead vendors, engineers and technicians to execute commissioning activities and hand-over to the operation team,” said Naderi.
Naderi said this process often starts in the office by providing systemization, system list, commissioning execution plan, activity list, schedule and work execution flow chart. In next step by reading and understanding a high volume of engineering documents, commissioning procedures will be provided. “For example, if there is a pump, I would prepare a step-by-step procedure including system line up, pump priming, etc. which will say how I am going to commission this system,” he said. The other major step, he said, is to develop a vital understanding of the health and safety requirements for commissioning of each individual system.
It is Naderi’s job to ensure that all client deliverables are achieved; whatever the client has specified that they need from their equipment, Naderi will provide. To do this, he reviews all relevant design and vendor documents such as datasheets, drawings, specifications, factory acceptance test, performance test criteria, control narrative, alarm, and trip setting list to incorporate required data in the CSU procedures. This includes step-by-step guides and mark up drawings on how to best commission equipment.
If there is any requirement to preserve the equipment after commissioning, before going to the start up, required provisions will be addressed in the procedure. Each procedure includes the appendix section to address all of the references and documentation related to this procedure.
All deliverables including procedures will be reviewed by the client and upon their approval, the commissioning team will be mobilized to the site. However, the commissioning procedure is a live document which could be modified at the site based on available resources.
Common Challenges
Every job has its challenges, but Naderi must constantly be thinking outside of the box. For commissioning of rotating and static equipment, the most challenging part is to ensure all prerequisites are fulfilled as per project requirements. Most should be captured in the pre-commissioning activities (e.g., ensuring proper installation and alignment, proper first fills of consumables, proper priming of mechanical seal systems [if applicable], etc.). During commissioning, one should ensure the equipment is working as per design and could reach to the approved performance curve.
By monitoring temperature and vibration during commissioning, one can ensure that there is no excessive heat or vibration in equipment. However, in case of any issue, the application will stop, and troubleshooting will be conducted to rectify the issue.
The COVID-19 pandemic also came with several challenges for Naderi. However, unlike many other companies in the industry, Naderi said his biggest challenge was not in the supply chain due to the commissioning business nature, but rather in finding manpower and support.
“For certain equipment, you need the vendor to be available at the site and run the equipment under vendor supervision. In addition, whole plant operation logic will be implemented by external company/ vendor as per project requirements which has already finalized during design phase. Operation logic will be verified during commissioning activity. If some real logic check is not possible due to commissioning nature, then it will be verified by simulation “method.
The issue came when, during the pandemic, vendors could not be physically on site in the Middle East due to travel restrictions. This, Naderi said, often slowed down the commissioning process.
Paying it Forward
Every passionate professional wants to help preserve the future of their industry. Within engineering specifically, there is often worry about the lessening number of young professionals entering the workforce. That is why mentorship is of the utmost importance to Naderi.
To Naderi, mentorship is all about enthusiasm and connection. “You should be interested in what you are going to do for work,” he said. “If you are interested, the mentor will be very excited to tell you what is going on and what is happening in the industry. The knowledge will be transferred to you because if you are interested, you are going to read, you are going to learn, you are going to know what you are required to do, and then, you may have some good questions.”
The most important part of mentorship is safety. “The first of any technique taught in mentorship is understanding that safety is the highest priority,” Naderi said. “So to be a mentor, you have to understand people. It is not only about safety for the asset, but about safety for your life because working with equipment needs some certain level of caution.” He continued: “Rotating and fixed equipment are the main component of every plant, and if the equipment does not work, it will affect the plant productivity. So having reliable equipment is the most important concern for plant operation.”
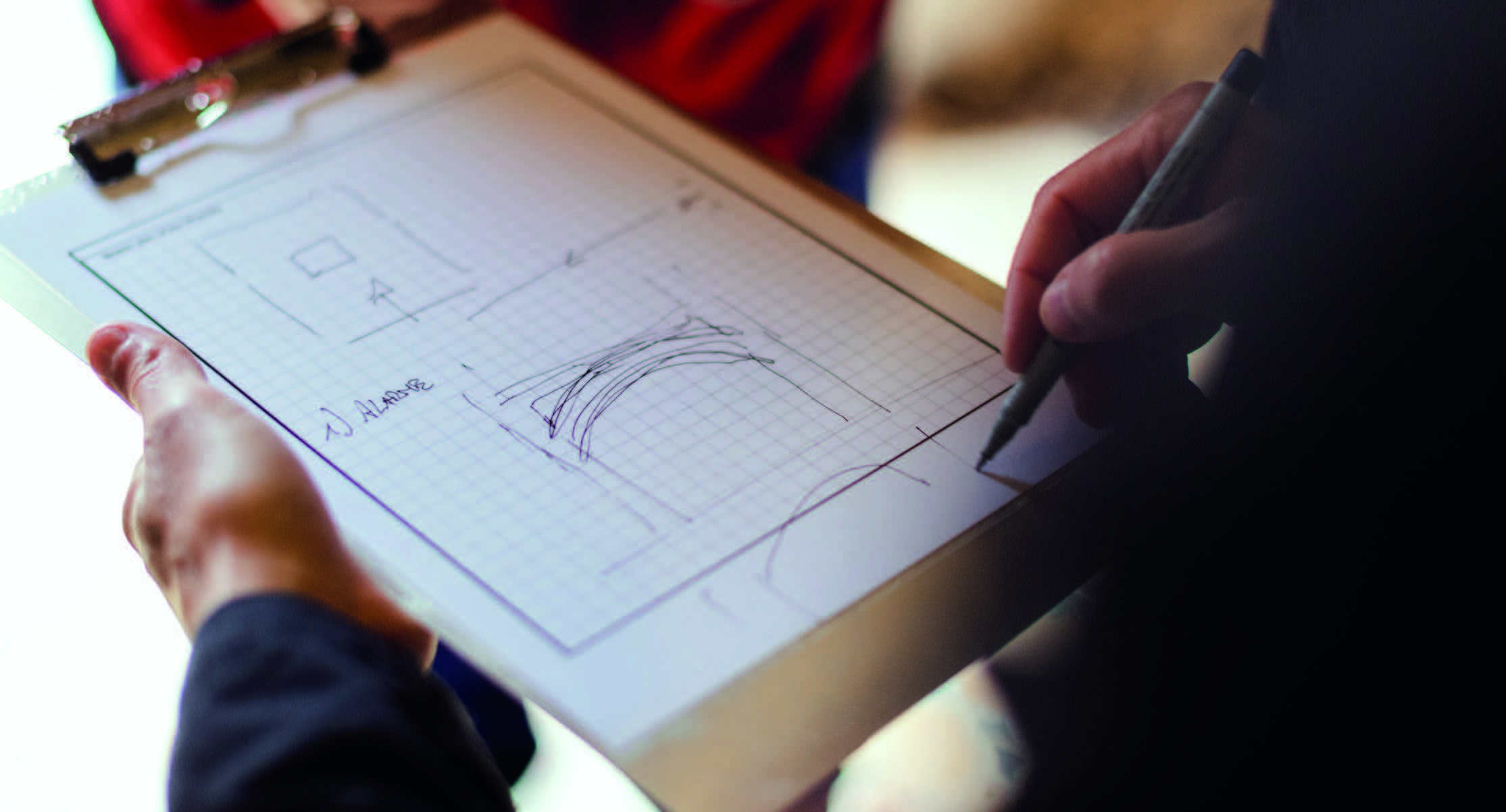
Predicting the Future
Naderi believes that there is still ample space for innovation when it comes to fixed and rotating equipment, namely in improved efficiency. “Improving efficiency will have direct effect on energy saving, and that is one of the main areas of concentration around the world,” he said. “When you increase the efficiency, it means you are using less power.”
Demand for static and rotating equipment is expected to rise due to global expansion and requirements. Naderi remains optimistic about the future. To him, there is always room for growth, and he, like many other skilled professionals, is eager to see what the future will hold, months, years, and decades down the line.