Recent Federal inspections of refinery & chemical facility BWON programs are finding many sources of unpermitted benzene emissions from facility Waste Management Units (WMUs). The prominent leaking equipment is poorly maintained fixed and internal floating roof tanks and equipment associated with oil-water separation (oil-water separators, APIs, CPIs, etc.). The standards, in § 61.643-§ 61.347, § 61.349, expressly state that WMUs must be engineered to operate with No Detectable Emissions (NDE) as indicated by an instrument reading of less than 500 ppmv VOC above background. It is therefore important to mitigate any risk of NDE with the appropriate assets.
By Tim Goedeker, Bronson Pate, and Mark Ruffin – Teadit
There are two keys ways to improve compliance with the No Detectable Emissions (NDE) control standards for WMUs: use reliable, low emission gaskets or sealants, and use an optical gas imaging camera to identify detectable emissions around all seams, seals, covers, and openings on WMUs. All detectable emissions >500 ppmv must be timely mitigated (repaired). Inspections are finding sources emitting significantly higher than 500 ppmv.
The Benzene Waste Operations NESHAPs (National Emission Standards for Hazardous Air Pollutants) or more commonly known as BWON, was promulgated in 1990 under the Clean Air Act (40 Code of Federal Regulations (CFR) Part 61, Sub- part FF). The BWON standard was put in place to control benzene emissions from facility waste and applies to petroleum refineries, chemical plants, coke by-product recovery facilities, and Treatment, Storage, and Disposal facilities (TSDFs). TSDFs are included only if they handle waste from one of the other facilities mentioned above. BWON is a unique standard as it combines waste and wastewater quality management in an air standard for controlling benzene emissions.
The regulation (40 CFR Part 61, Subpart FF) includes multiple subsections; Applicability, Waste & Waste Stream determination, Compliance options, Point of Waste Generation, and Treatment & Equipment Standards. With many complicated standards, it is essential to understand the key terms used in the standard and throughout this article.
Total Annual Benzene (TAB) Quantity
So, what options does a site have for compliance? Is there only one way to comply? Compliance requirements are determined by the facility’s TAB quantity. To calculate the TAB quantity for a Waste Stream, multiply the annual waste quantity of the waste stream by the flow- weighted, volume basis, and annual average benzene concentration (weight %) of the waste stream. The waste stream quantities will be calculated in Megagrams per year (Mg/yr), one (1) Megagram is equivalent to one (1) metric ton.
BWON allows for two ways to determine the benzene concentration for a waste stream: through process knowledge or direct measurement. Therefore, the benzene quantity (BQ) of each waste stream is determined by estimating the stream’s annual benzene waste quantity.

The main point is to ensure the waste quantity is representative; the oil and water fraction of the waste must be determined. There are vital thresholds that must be used when determining which streams are applicable and which are not. For example, waste streams that are <10% water are organic waste and, therefore, should not be included in the calculation of the TAB. However, if the organic waste is mixed with aqueous waste (>10% water content), then the mixed waste is treated as an aqueous waste and would be included in the TAB.
Benzene Control Options
After the TAB is determined the facility will fall within one of the three control options:
- Facilities with a TAB greater than 10 Mg/yr: are required to install environ- mental controls on their waste streams and WMU and submit quarterly and annual reports [§61.355(a)(3)].
- Facilities with a TAB less than 10 Mg/ yr but greater than 1 Mg/yr: are not required to install controls but must submit an annual TAB report and an updated report if the TAB goes above 10 Mg/yr [§61.355(a)(4)].
- Facilities with a TAB of less than 1 Mg/ yr: Are required to submit an initial TAB report and update the report if the TAB goes above 1 Mg/yr [§61.355(a)(5)].
An important point to consider is that most facilities will have a TAB greater than 10 Mg/yr and will require environmental controls on the equipment transporting process wastewater including the WMUs. This equipment is subject to no detectable emissions threshold and no detectable emissions monitoring standards as noted in §61.343 thru §61.347 and §61.349.
Benzene Compliance Options
The rule also provides three options for managing uncontrolled Benzene Quantity (BQ). Most facilities, however, use either the 2MG or 6BQ option. A facility under these compliance options will include the TAB and the uncontrolled BQ.
- 2 MG Compliance Option: The facility may choose certain wastes to exclude from control up to a cumulative uncontrolled BQ of no more than 2 Mg/ yr. The uncontrolled wastes must be counted at the POG. The benefit of the 2 MG option is that a facility may exclude from control or the cumulative 2 Mg/yr calculation any stream with less than ten ppm benzene and any Process Wastewater Stream with a flowrate less than 0.0005 GPM or wastewater quantity <10 Mg/yr [§61.342(c)(2)].
- 6BQ Compliance Option: The facility may choose certain wastes to exclude from control up to a cumulative uncontrolled BQ of no more than 6 Mg/yr. However, all streams with greater than 10% water are included in the cumulative 6 Mg/ yr calculation, including those less than ten (10) ppm benzene. All organic streams must be controlled. The uncontrolled waste must be counted when it enters the first uncontrolled WMU. Waste streams never managed in uncontrolled WMUs are counted at the facility discharge [§61.342(e)].
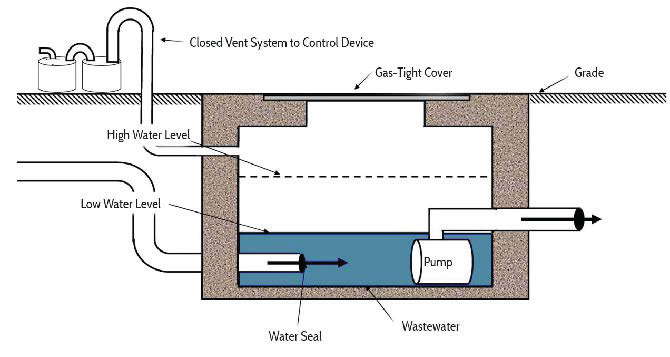
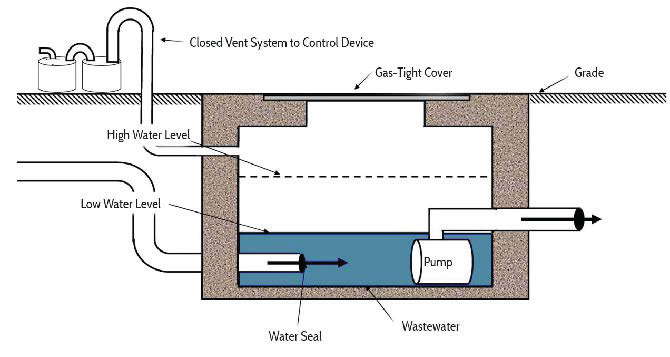


Control or Treatment of a Waste Stream
Control or treatment of Waste Streams must meet one of the following requirements:
- Remove benzene from the waste stream to less than 10 ppm on a flow-weighted average basis.
- Remove benzene from the waste stream by 99% or more on a mass basis.
- Destroy benzene in the waste stream by incinerating the waste in a combustion unit that achieves a destruction efficiency of 99% or greater for benzene.
Waste Management Units (WMUs)
Wastewater Treatment Systems include equipment with specific control requirements, except for Enhanced Biodegradation Units. The control, periodic monitoring and leak repair requirements for WMUs are listed in Table 1.
As mentioned above, most facilities will have a TAB greater than 10 Mg/yr and will require environmental controls on the equipment transporting process wastewater to the WMUs. This equipment is subject to no detectable emissions threshold and no detectable emissions monitoring standards as noted in §61.343 thru §61.347.
The standard in each paragraph states: “The cover and all openings (e.g., access hatches, sampling ports, and gauge wells) shall be designed to operate with no detectable emissions as indicated by an instrument reading of less than 500 ppmv above background, as determined initially and thereafter at least once per year.”
The standard for closed-vent systems and control devices, §61.349, varies slightly, “The close-vent system shall be designed to operate with no detectable emissions as indicated by an instrument reading of less than 500 ppmv above background, as determined initially and thereafter at least once per year.”
There are two key factors to improving compliance with the NDE control standards for WMUs. First, the facility should be proactive using reliable, low emission gasket or sealant material on all seams, seals, covers, and openings (any interface that could have detectable emissions to the atmosphere) for each WMU. Second, the facility should proactively use an optical gas imaging camera to ‘look’ for detectable emissions from all BWON equipment with an interface that could leak process vapors to the atmosphere at each WMU.


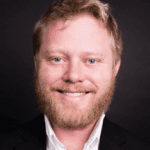
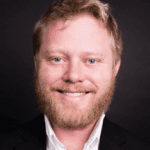
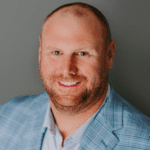
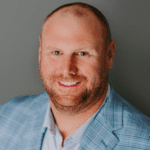