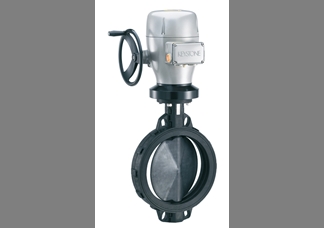
Tyco Valves and Controls’ CompoSeal valve provides comparable pressure and temperature performance to traditional valves with the benefit of improved environmental credentials and a reduced carbon footprint. A range of butterfly valves made from a combination of two thermoplastics which offer increase design flexibility, CompoSeal remains firmly within existing regulatory framework and ISO, API, PED, EN and EnEv industrial design standards. In comparison with traditional metal methods, the valves require less energy in production through the use of injection molding technology and uses reduced amounts of raw materials.
Given the increasing importance of sustainability, the composite materials may be reused as the valves are fully recyclable. These benefits can reduce CO2 emissions up to 70% based on 10,000 valves. As the products are substantially lighter weight, transportation is more efficient and they require minimal assembly labour. The CompoSeal valve reduces heat loss through low thermal conductivity and performs well in harsh environments without the need for a protective paint layer. This also takes away the need for solvents in the coating process.
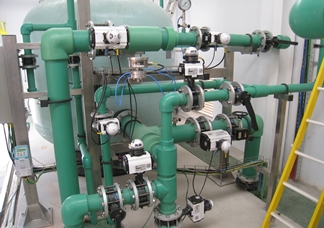