Hyperion officials discovered corrosion of its primary outfall pipeline. This was not an unusual condition given the fact that the 50-year-old pipeline and pump header had never undergone any substantial maintenance. Repairing the pipe and pump header became part of a $10 million upgrade to the plant’s 50-year-old infrastructure.
To start repairs in the spring of 2016, maintenance and construction crews diverted effluent (i.e., treated wastewater) that normally empties via the primary outfall pipe into the ocean at a depth of 190 feet to an emergency outfall just one mile from the California shoreline, where the Hyperion plant sits. To complete the work, Hyperion tasked crews to work around the clock for six weeks.
Part of the work involved manufacturing a 10-foot diameter butterfly valve, which plays a critical role in moving wastewater – that meets government clean water standards – from the plant into Santa Monica Bay via the five- mile-long outfall. The plant pumps effluent into the ocean when tide levels are higher than the facility’s digesters; when tides drop below the elevation of the plant’s digesters, operators open the butterfly valve and let gravity move effluent into the ocean bay.

Before the construction project, a set of two cylindrical pumps opened the existing butterfly valve every 12 hours. The valve is critical to public safety and operation of the plant. If the valve were to fail in the open position at high tide, ocean water from the bay and effluent would back up the pipe and flood the whole facility. There is no secondary valve, only a redundant cylinder for closing and opening the valve. In spite of this, the system operated successfully for five decades.
“To head off the corrosion and prevent a ruptured pipe, Hyperion had to totally shut down its five-mile pipeline and line it with a fiberglass cloth, so the pipeline’s cement wouldn’t erode away,” says Tim Fallon, a senior sales engineer for Henry Pratt Company, a global leader in designing and making valves, actuators and control systems.
As part of the repair project, Hyperion’s managers called on Henry Pratt to rehabilitate the existing butterfly valve. According to Fallon, the extremely tight deadline for repairs would mean a tight timeline for refurbishing the plant’s 10- foot diameter butterfly valve.
“After considering the request, we determined the window was so small that it could not be rehabilitated in the time allotted,” adds Fallon. “The old butterfly valve was custom made; it was so uniquely designed that the bolt drilling was non-standard, and the flange connected to the mating part of the pipe was non-standard. Replacing it with a new butterfly valve was our recommendation.”
In the meantime, Hyperion’s crews began rehabilitating the pipe. Project managers for the plant pressed Henry Pratt to provide the existing butterfly valve with a new actuation system, similar to what had been in place before. The prior approach used high-pressure hydraulic oil and operated two cylinders on a lever, providing a double redundancy of sorts. If one cylinder failed or the HPU supplying the cylinder failed, then the plant could rely on the other cylinder.
“To address the actuation challenge, we called Moog Flo-Tork because they design reliable high-torque systems,” recalls Fallon. “The available pressure from the hydraulic power units was about 1,200 psi; we were looking for one million Inch-pounds of torque.”
What Moog supplied Henry Pratt was a system delivering 1.2 million Inch- pounds of torque per rack and pinion actuator, using a tandem design to accommodate the need for redundancy. Due to the compressed timeline for completing the pipeline project, Moog took on additional shifts to supply the two actuators and shave off a couple of months of construction and assembly time. Although the assembly is compact, it creates great power with low oil volume. Henry Pratt put the two Moog actuation systems together as a solution. Even though the two actuators are mechanically sandwiched together, they act as independent primary and emergency backup actuation systems. The solution was met with skepticism because it did not look like the existing system, recalls Fallon.
“After we tested the new actuation system, it worked very well,” says Fallon.
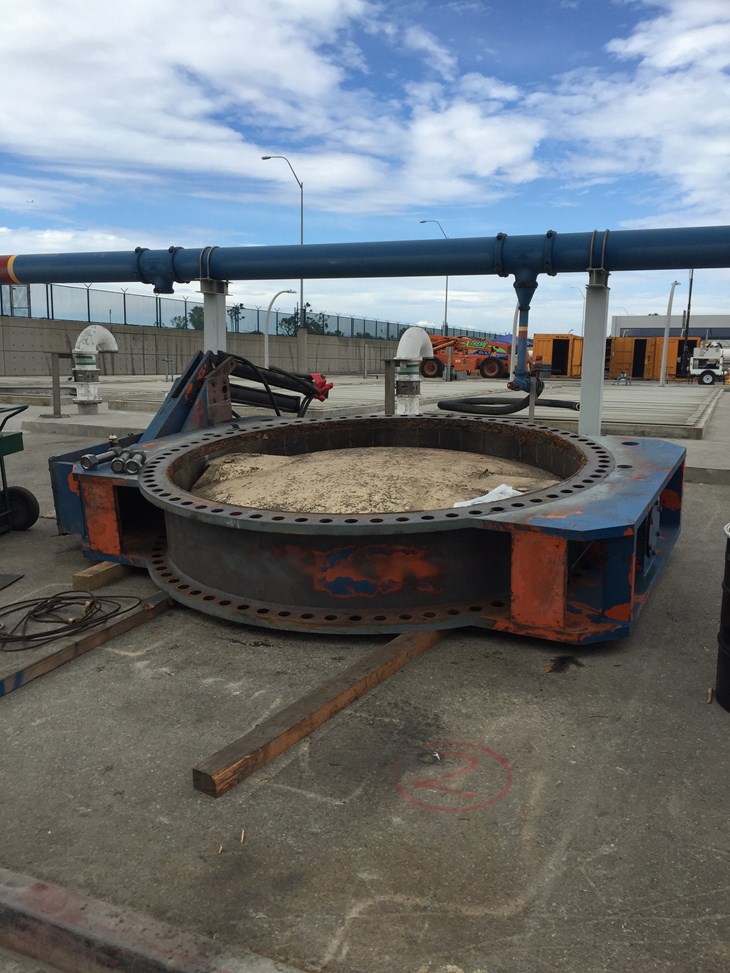
As Fallon and Moog examined the existing butterfly valve, Hyperion mentioned that there had been a valve position indicator installed. But the companies found no evidence of a feedback system. If there was one, the engineers surmised, the plant personnel had removed it years ago.
So Henry Pratt convinced Hyperion to allow the company to manufacture a new butterfly valve, which would work in unison with the Moog Flo-Tork actuation system. Hyperion’s managers agreed. After taking delivery of the two actuators, they were mounted to the new butterfly valve. The assembly was then shipped to Hyperion, and crews at the plant installed it.
According to Fallon, the success of its portion of the project rested on the fact that the company was able to deliver the most cost-effective and reliable approach to operating the butterfly valve. The application demanded the highest mechanical advantage with the lowest volume of oil. The assembly was able to reduce the volume per stroke through greater mechanical advantage in the actuators.
“Hyperion had initially indicated that they wanted an electric actuation system, and I think that is partly because consumers regard the oil-hydraulic approach as messy,” says Fallon. “Moog supplies both electric and hydraulic actuation solutions, and, in this case, the footprint of the HPU is smaller and uses a lesser amount of oil – that’s a benefit in itself.”
The solution enabled Hyperion to bring its facility back online without incurring any additional days beyond the scope of the initially proposed repair and maintenance project. This allowed the plant managers to avoid the legal burden and expense of additional permitting required to run the emergency outfall beyond the specified window granted by the City of Los Angeles. Since the installation, the valve and actuation system have operated around the clock flawlessly, giving plant managers and the public an upgraded level of safety and environmental protection.
About the author
Allen Ruef is the product line sales manager at Moog Inc. He has been with the company for 15 years in numerous roles including engineering, R&D and sales. Allen holds a bachelor’s degree in mechanical engineering from the University of Akron and has been involved with actuation for more than 20 years.