Tailings tank level control valves in mining applications play a critical role in mineral processing, especially in the process of increasing water recovery, which is paramount for improving the environmental sustainability of mining projects. One example of this application in mineral processing is the tailings control valve at the bottom of an Eriez Coarse Particle Flotation circuit using HydroFloat® technology.
The throttling response, reliability, flow dynamics, wear resistance, and sizing practices of the control valve in this critical service require a dedicated engineering approach to ensure the valve is properly designed to handle this abrasive service, which is crucial to the operation of the flotation cells.
By Amir Emami, P.Eng. & Maria Aguirre, P,Eng. – SAF
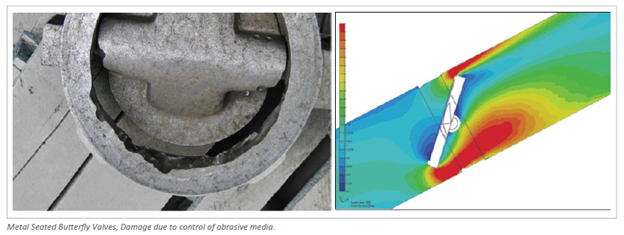
In this article, the SAF engineering team sheds light on valve sizing practices to account for changes in slurry fluid behavior during the mine start-up phase versus normal operation. The changes in slurry fluid properties impact valve sizing and throttling response, and if not accounted for with proper engineering practices, it can lead to valve and piping failures, resulting in unplanned downtime and repairs. This article illustrates the critical nature of these considerations by analyzing an application at NewCrest Cadia in Australia, demonstrating the Coarse Particle Flotation technology.
A severe service control valve designed to handle the challenging flow conditions of tailings applications needs to have proper engineering checks and balances to ensure reliable service.
Over years of dealing with extremely abrasive processes, SAF, the creators of Slurryflo valves, have developed a design philosophy that proves to be the best approach for selecting control valves for severely abrasive processes, ensuring optimal control and the longest lifespan:
- Dedicated effort in sizing each valve for the full spectrum of process conditions.
- Streamlining and optimizing flow components to reduce unwanted turbulence for the majority of the throttling positions of the valve.
- Using the toughest materials available for flow components to slow the damaging effects of erosion.
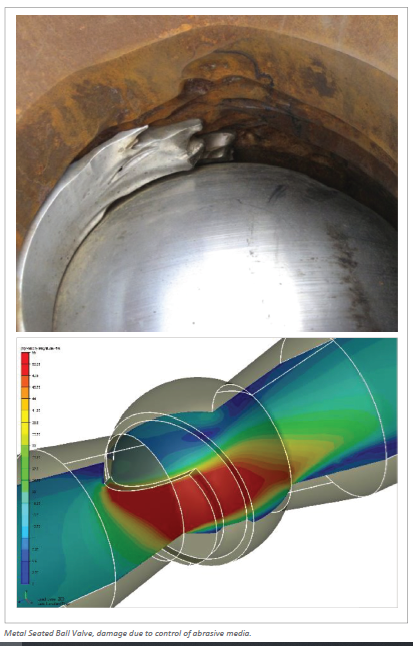
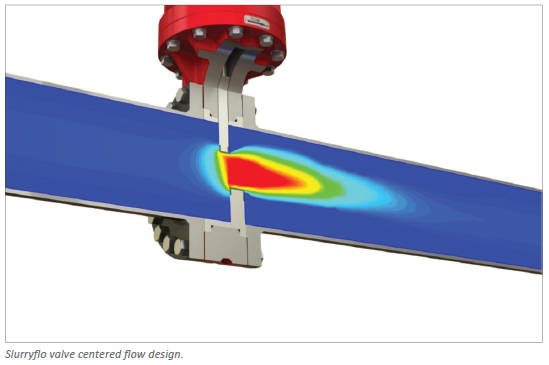
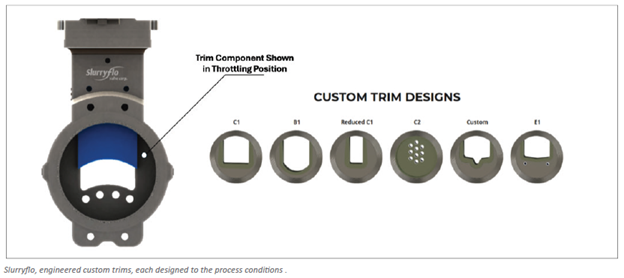
With the Coarse Particle Flotation technology demonstration project at NewCrest mine, this design philosophy was used to successfully mitigate challenges in this tailings control application. For step one, in addition to evaluating typical process conditions covering minimum, normal, and maximum flow conditions, the design engineer sought to understand the mine start-up flow conditions, which had vastly different flow environments and fluid properties that significantly impact the throttle characteristics of the valve. In this project, the mine start-up phase produced very high viscosity tailings, which are considered a non-Newtonian fluid, requiring a Cv (flow coefficient) correction method using high viscosity numbers. The science of valve sizing for non-Newtonian fluids is not exact, and there is no straightforward calculation; however, iterative approaches coupled with experimental data can assist a valve design engineer in ensuring the rated flow capacity of the valve can handle higher flow demands required with very high viscosity tailings fluids. This detailed flow and sizing analysis is a critical starting point in custom engineering a control valve for this type of service.
The next step was the design and development of the valve trim components, which are the parts that control the fluid through the valve. An iterative approach using Computational Fluid Dynamics (CFD) simulations was employed to study the velocity gradients through the valve at different flow conditions and analyze flow parameters such as turbulence, eddies, and areas of flow recirculation that can create excessive erosion damage to valve components. This iterative design approach allows the engineering team to minimize unwanted turbulence and evaluate valve performance in all throttling conditions while carefully monitoring the discharge jet and many other variables to predict valve performance in the field.
Another crucial design step in custom engineering a valve for abrasive flow environments is the dedicated approach to streamline flow components. The final step of the design philosophy is selecting materials appropriate for the given application in terms of corrosion, temperature, pressure limitations, and especially abrasion. In some cases, a proprietary composition of carbide is used to balance toughness and strength with abrasion resistance, as these valves must function in some of the harshest flow environments with large solids and high-velocity tailings fluids.

Following the design and custom engineering philosophy developed by SAF for the Slurryflo valves, the reliable and predictable operation of severe service control valves designed to handle tailings discharge has been practically demonstrated. In many mining applications, end users are reluctant to use control valves for throttling high percentage solids tailings fluids, as they have proven to be difficult for most control valve types. However, it has been demonstrated that for severely abrasive control applications in the mining industry, the right approach is an engineered valve designed specifically for the process conditions to ensure proper control while minimizing turbulence and centering the flow.