Adopting strategic maintenance methods in today’s industrial environment is essential for sustaining a valve’s high operational efficiency and reliability. The evolution of traditional reactive maintenance to more proactive strategies plays a transformative role in valve maintenance, from minimizing downtime, extending equipment life expectancy, to ensuring uninterrupted production, and revealing the complex, yet pivotal role maintenance plays in the overall success of these crucial components.
Through a series of questions, Valve World Americas revisits the basics, exploring the layers of structured maintenance programs that are crucial for peak operational excellence.
By Shopia Ketheeswararajah
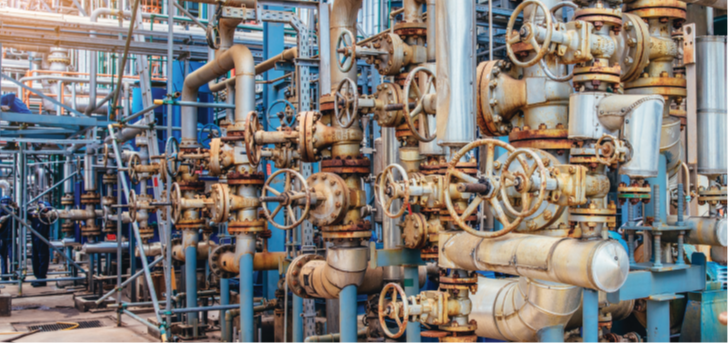
Q: What is the Main Goal of Valve Maintenance?
A: Valve maintenance aims to ensure the equipment operates at a level of efficiency by preventing failures and reliable operation. This plays into the overall life expectancy of the component. Maintenance can involve regular inspection and cleaning, lubrication, or adjustments of valve components to mitigate failures. When operators address material issues such as corrosion, wear, and debris buildup, maintenance aids in preserving optimal flow and minimal leakage. Proactive approaches that maintain these components contribute to the uninterrupted operation of the entire system.
Q: What Are the Primary Types of Maintenance?
A: Regular or scheduled maintenance performed on the field at predetermined intervals assists in preventing equipment failures. Preventative maintenance (PM), can involve tasks such as inspecting, cleaning, and replacing worn parts. Preventative maintenance follows a schedule based on time or usage. Users often utilize standard operating procedures and checklists to ensure consistency. For example, replacing gaskets or inspecting seals in the valve component is one of the most common ways to implement preventive maintenance.
Predictive maintenance, on the other hand, is performed based on the actual diagnosis, or condition of the equipment prior to the failure occurring. This method is dependent on condition-monitoring technologies and data analysis to determine the equipment’s efficiency. For example, techniques such as vibration analysis and ultrasonic testing can be used to detect early signs of imbalances or misalignment of the valve. Vibration sensors monitor the condition of rotating equipment and employing thermal imaging can detect overheating of valve components.
Corrective maintenance is another method that is commonly used. Once a failure occurs, this strategic maintenance method is employed to correct faults and return the valve to proper working condition. To resolve the failure, the root cause of the failure must be identified, followed by the repair or replacement of any faulty components. Valve operators would then require detailed diagnostic tools and procedures to accurately identify the issue. Corrective maintenance can be planned based on predictive insights or unplanned, which can be a result of a reactive response to unexpected breakdowns.
Lastly, reliability-centered maintenance is a process valve operators use to determine the most effective maintenance strategies. This approach involves a structure to identify potential failure modes by evaluating the equipment’s impact on system performance and implementing preventive measures that aid in mitigating risks, resulting in enhanced system reliability.
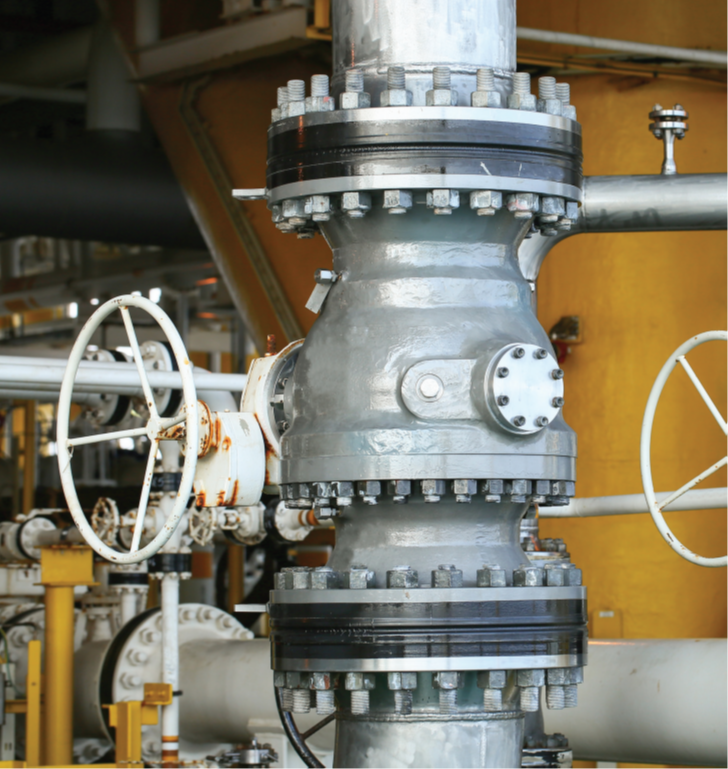
Q: What Are Some Key Elements of a Successful Maintenance Program?
A: Comprehensive planning, skilled personnel, and proper tools are some of the most important elements of a cohesive maintenance program. Planning and scheduling maintenance involves using software tools that not only aid in scheduling interval maintenance, but it also helps with keeping track of work orders and allocating resources efficiently.
Continuous monitoring and evaluation involve using key performance indicators (KPIs) to assess the effectiveness of the maintenance program. KPIs usually refer to the average (mean) time between failures (MTBF), mean time to repair (MTTR), equipment downtime, and maintenance costs. For example, advanced tools such as IoT sensors and machine learning algorithms can provide real-time understanding of the component’s condition. Performance reviews can also help in pinpointing areas of improvement, ensuring the maintainability of the equipment aligns with the user’s goal.
Training personnel must be familiar with the latest techniques and technologies. This can include hands-on training with equipment, safety protocols, and certification programs. Ongoing learning and regular workshops are vital in ensuring staff stay up to date on maintenance methods, tools, and best practices. Other vital elements of a successful maintenance program include documentation, recordkeeping, providing operators with the correct tools and equipment, as well as inventory management.
Q: What Are the Benefits of Implementing a Computerized Maintenance Management System?
A: Computerized maintenance managements systems (CMMS) establish a calendar with detailed tasks and timelines of performed maintenance activities during planned downtime to minimize disruption. In certain cases, operators implement critical analysis to identify and prioritize tasks that impact the overall maintenance schedule. This tool can be used to enhance regulatory compliance, improve decision-making after analyzing maintenance data, and aids in managing work orders and inventory.
Q: What is the Role of Failure Modes and Effects Analysis (FMEA) in Maintenance?
A: FMEA is a method used to identify failure modes, its causes, and the effects on the system’s overall performance. This analysis method prioritizes maintenance activities based on the severity and likelihood of the failure that had occurred. This makes certain the critical components of the valve, such as the gasket or sealing receive the most attention.
Q: What Are Common Challenges in Implementing Effective Maintenance Strategies?
A: Some challenges in implementing maintenance strategies can include data management, resource allocation, integration, training, and resistance to change. Collecting and analyzing maintenance data is vital for the predictive maintenance approach. This process involves setting up sensors and data collection tools on critical equipment to continuously monitor its condition. The challenge pertains to handling the immense amounts of data generated, which must be accurately processed. Advanced data analytics tools and software can aid in differentiating the data to schedule maintenance when it is needed, which also benefits maintenance costs.
Allocating resources to key maintenance strategies includes securing a sufficient budget for these operations, but also ensuring the right mix of skilled personnel can be obtained. This requires a precise understanding of manpower and financial output for routine tasks or emergency repairs. Optimizing the use of these resources allows users to avoid overstaffing during low demand periods and vice versa.
Integrating maintenance activities with production schedules to reduce downtime involves developing a schedule that aligns with production demands and does not interrupt production cycles. This is where CMMS can be facilitated through tools that are provided to aid in scheduling, tracking, and documentation tasks in real-time. On the other hand, ensuring staff are trained on the latest technologies and techniques is also crucial for the effectiveness of the maintenance strategies.
Lastly, overcoming resistance to change within an organization involves a proactive mindset. Management is required to lead by example, therefore promoting the benefits of a proactive maintenance strategy through extensive training can establish a culture that values maintenance as a tool that can be supported by demonstrating the cost benefits and improved operational metrics associated with these practices.
Final Words
Successful valve maintenance management stems from several key elements, from strategic resource allocation and robust data management systems to proactive production schedules and ongoing learning. Organizations must address the challenges of implementing effective maintenance strategies; not only does it prevent equipment failures, but it also aligns with broader operational goals that lead to improving performance and ensuring reliability in the valve equipment.