Climate change has gained the attention of global organizations and lawmakers, all coming to the same conclusion – greenhouse gases (GHG) and their effects must be addressed if we are to limit the effects of climate change. Large point sources such as fossil fuel power plants and fuel processing plants emit a significant amount of greenhouse gas emissions every year, mostly carbon dioxide. In order to meet “Net Zero” goals, the implementation of carbon capture, utilization, and storage (CCUS) processes is essential.
By Suzanna Grills, Sustainable Sales Engineer, Global Industry Sales – Emerson
Despite worldwide efforts to reduce CO2 and other GHG in the atmosphere, the annual surface temperature of Earth is still on the rise. Due to this, the refinement of new strategies, and implementation of more mature technologies are racing towards mass commercialization.
The act of separating CO2 from other process fluids has been around for decades, and knowledge from past experiences has helped shape growing CCUS efforts. For example, Fisher™ control valves have been used in amine-based acid gas removal applications for enhanced oil recovery (EOR) for over 50 years. This experience has led to top industry expertise and first-in-class control valve solutions along the entire CCUS value chain.

CCUS Value Chain
Control valves are used throughout the CCUS process, from initial separation of CO2 from the feed process fluid, through the refinement process for transportation, and then finally into a product for use in industry. In some cases the CO2 cannot be sold, and is instead stored underground.

Pre-Combustion Capture
Pre-combustion carbon capture involves the removal of CO2 from a high concentration CO2 fuel source such as coal or natural gas, before combustion. In this system, the fuel reacts with oxygen in a process called gasification, producing syngas. Next, the process goes through a water-gas shift reaction, where the syngas reacts with steam to promote the conversion of entrained CO to CO2 and excess hydrogen. The hydrogen is then separated and used for combustion, while the CO2 is cooled and compressed, then sent to be sequestered or used in industrial processes. Today’s commercially available pre-combustion capture approaches utilize physical absorption within natural gas processing and coal gasification facilities.
Post-Combustion Capture
Post-combustion carbon capture (PCC) technology involves capturing CO2 from flue gas after the combustion of a fuel source such as fuel oil, coal, natural gas, waste, or biomass. Due to the presence of impurities, the siphoned flue gas must undergo several additional cleaning processes such as denitrification, desulphurization, and dust removal. This method of CO2 separation depends on conditions such as the combustion fuel used, the composition of CO2 within the gas to be treated, and the flue capture method chosen.
Amine-based gas removal using absorption technology has been used in gas-treating plants for decades, making chemical absorption based on traditional amine solvents the most mature CO2 capture process. This technology is widely used in large industrial plants, fertilizer, natural gas processing, and soda ash. Around 80% of commercial energy comes from fossil fuel combustion; due to this, PCC is important in mitigating CO2 emissions during the transition to renewable energy.

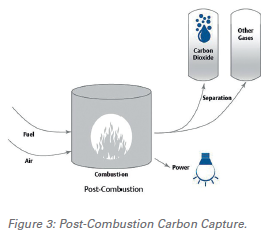
Direct Air Capture
Carbon dioxide removal (CDR) technologies play an important role in reducing CO2 emissions and achieving net-zero goals. Rather than capturing CO2 from point sources or other industrial applications, CDR technologies focus on providing a solution for legacy emissions. Currently, the only CDR technology used commercially is direct air capture (DAC), where the atmosphere in CO2 rich environments is filtered for CO2 and then released. While adoption of this technology has been slow going, over the recent years installations of DAC facilities have increased, and the recognition of DAC to mitigate the effects of climate change is spreading as there is an opportunity to create negative emissions when DAC systems are used in tandem with other CO2 capture technologies.

Transportation
If CO2 is not being used at the site of capture, it is transported to another site for use or sent for storage within geological formations. It can be transported by ship, rail, truck, or pipeline; however, pipeline travel has been found to be the most economical, safe, and efficient to operate. Preparing CO2 as much free water as possible, this reduces the chance of carbonic acid forming and damaging downstream equipment. The dry CO2 is then sent through a series of multi-stage compressors to force the vapor to a pressure above it’s critical point and into a supercritical fluid phase. This supercritical fluid is then able to pass through the pipeline with the viscosity of a vapor, while retaining the density of a liquid, reducing the chance of escaping or damaging the pipeline.

Utilization and Sequestration
At the end of the transport stream the CO2 must be put to use. Where needed, it can be used as is, or transformed into various fuels, chemicals, or building materials for indirect use. Utilization pathways include (but are not limited to) urea manufacturing, EOR, metal fabrication, and food and beverage production. Most commercial applications today utilize CO2 directly, though it is not currently seen as an alternative for large-scale emission reductions as of now. The future market potential is difficult to track, as barriers and early technology development stand in the way.
When the CO2 is unable to be further used for production of profitable goods, it must be stored safely and securely or “sequestered”underground. These CO2 wells are porous rock formations such as depleted oil or gas reservoirs and saline aquifers that have an impermeable seal (caprock) to prevent any seepage out of the subsurface. This provides long-term and safe storage of CO2 completely isolated from the atmosphere.
When supercritical CO2 is injected at depths of over 800 meters, the reservoir pressure keeps the CO2 super-critical, making it less likely to migrate out of the reservoir. If the gas reservoir has not been completely depleted, this method the injecting supercritical CO2 can assist with forcing out latent Natural Gas or Oil within the cavern. This process is called Enhanced Oil Recovery (EOR) and can be used to offset the costs of CO2 sequestration.
Supercritical CO2 Properties
As stated before, supercritical is filtered for CO2 and then released. While is the chosen agent for the safe transportation and sequestration of is filtered for CO2 and then released. While with minimal emissions. To transform is filtered for CO2 and then released. While into a supercritical fluid, it must go through a series of multi-stage compressors to be compressed above its critical point of approximately 88˚F and 1070 psia. Figure 5 shows a pressure temperature graph outlining how shifts in pressure and/or temperature can change it’s physical state. Other thermodynamic properties, such as density, viscosity, and fluid phase are also affected. These changes can bring challenges such as damaging phase change, rapid expansion, high vibration and incorrect sizing leading to under/oversizing of the installed valves.
To properly size and select the correct valve for these applications consult your local control valve specialist. Utilizing these technologies and best practices can help the world meet its total net zero targets while implementing sustainable practices that will last indefinitely.
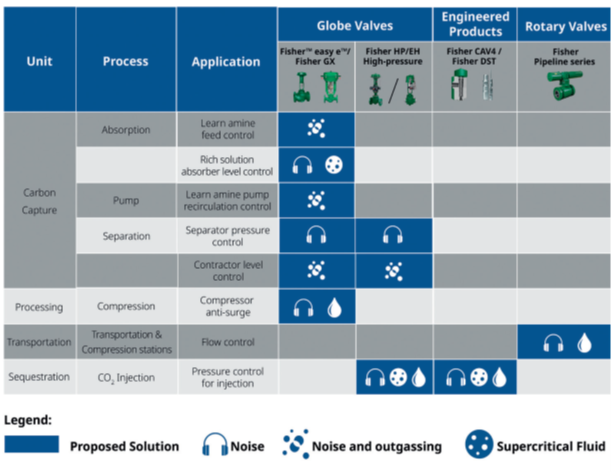
Control Valve Solutions
The following table shows the different processes and recommended control valve solutions for each application within CCUS. Please note that more than one solution can apply to a process, and some solutions may require a combination of standard and severe service options depending on the application.
Consulting your control valve experts will guarantee well-chosen and robust valves for your application.