The Environmental Protection Agency (EPA), under the direction of President Biden, is proposing changes to the Clean Air Act, 40 CFR 60. A proposal released in the Federal Register on November 15th, 2021, first mentioned this. After a year of comments, the EPA released an update to this proposal that was printed in the Federal Register on December 6th, 2022. The EPA proposes revising new source performance standards for greenhouse gas and volatile organic compound emissions from the oil & gas industry.
By Tim Chicoine, Director of Sales – WedgeRock Engineered Solutions/Principal – Riverhawk Industrial Sales Inc. and Gobind Khiani M. Eng., P.Eng., Fellow, Mechanical Engineering – Piping/Pipelines
Revision of Standards
The EPA is requiring the U.S to establish emission guidelines that follow the new performance standards to reduce greenhouse gas emissions. Although the oil & gas industry has made great strides in reducing methane emissions, the EPA and the Biden administration is looking at strengthening the restrictions. One area where the EPA is looking to reduce methane and volatile organic compounds is in the operation of natural gas driven controllers at new, reconstructed, and modified facilities.
According to the 2021 Inventory of U.S. Greenhouse Gas Emissions and Sinks (GHGI), pneumatic controllers in petroleum systems were responsible for 700 metric tons of methane emissions, while pneumatic controllers in the natural gas industry were responsible for 1.4 million metric tons of methane emissions.
These amounts represent 45% and 22% of all methane emissions in the petroleum and natural gas industries, respectively. Carbon Limits produced a report for the Clean Air Task Force that identified pneumatic controllers as the second-largest source of methane emissions in the oil & gas industry, only be- hind component leaks.
Natural Gas line pressures have traditionally been used in oil & gas facilities and pipelines as a reliable and low-cost option to control the process; they use actuated valves and controllers, including powering pneumatic pumps. The energy used by this equipment creates a greenhouse gas consisting of methane gas and other volatile organic compounds that is vented to the atmosphere. This compound has potential to affect global warming at a rate between 35x to 120x that of carbon dioxide. It is important to eliminate/reduce methane and GHG venting from these sites to minimize environmental impact of emissions and to maintain sustainability for the oil & gas industry.
Document Specifications
The EPA documents referenced above call out three different types of natural gas-driven pneumatic controllers: high-bleed, low-bleed, and intermittent controllers. High-bleed controllers emit more than six SCFH of methane and VOCs, low bleed emit less than six SCFH of methane and VOCs, and intermittent vent methane and VOCs during operation. For example, if a controller is in operation, i.e., opening or closing a valve, it is considered intermittent.
High-bleed and low-bleed controllers are commonly used on control valves while the intermittent bleed controllers are mostly used on isolation valves. One might think most methane emissions come from high and low bleed controllers, but the GHGI report indicated that 88% of all methane emissions mentioned above come from intermittent controllers. Many field studies on the emission factors of natural gas controllers also indicate that the average emission rates exceed the manufacturer’s published data.
Once these new regulations, titled 0000b New Source Performance Standards and 0000C Emission Guidelines, go into effect, installation of natural gas-driven controllers that emit gas will be restricted to very few applications. Certain States and Canadian provinces have already implemented restrictions on using gas-emitting pneumatic controllers. The Colorado Air Quality Control Commission, for example implemented regulation Number 7 which requires the use of non-emitting gas controllers at new and modified sites beginning May 1st, 2021.
Operators in Colorado were also required to start replacing existing gas-emitting controllers beginning in May 2022. The province of British Columbia updated their regulation 52.05 which re- quires a reduction in the use of natural gas driven pneumatic controllers which began January 1st, 2021. The province of Alberta implemented Directive 60 which requires any pneumatic instruments in- stalled on or after January 2022 to be zero-emission. The states of New York and New Mexico are also considering only allowing zero-emission controllers.
These proposed regulations, along with public pressure and the financial pressure brought about by ESG requirements, are going to affect all segments of the oil & gas industry and are currently being looked at by many organizations.
Ongoing Evaluation
Due to this pressure, current members of the oil & gas industry are evaluating the following options:
- Instrument air conversion: Use of compressed air system to operate pneumatics (if site is grid connected this is an economical option),
- Self-contained solar powered instrument air compressors for use with instrument air driven controllers,
- Nitrogen: conversion, like instrument air, by retrofitting existing pneumatics to use nitrogen,
- Electric actuation: This involves replacing a gas-powered pneumatic controller with an electric motor-driven controller (grid powered or solar-powered),
- Hydraulic and electrohydraulic actuators,
- Spring-Return electric operators (grid powered or solar powered),
- High-efficiency gear operators.

The best approach depends on the specific needs and resources of each site. Implementing zero venting strategy can help minimize the environmental impact on these GHG and methane emissions and assist in moving the oil & gas industry towards a new level of sustainability.
The proposed regulations focus on what the EPA refers to as ‘best system of emission reduction’. With relatively few exceptions, the stated best system of emission reduction is to require the use of zero-bleed controllers. The two exceptions listed are for areas in Alaska where grid power is not available and the lack of sunlight make solar power not feasible as well and when ‘functional needs’ outweigh the methane emissions, such as the case with ESD valves.
Actuators
As with most actuator applications, there are multiple options depending on location, number of controllers at a location, type of controllers already installed, operating media, customer philosophy, and history with various products, and economics. The economic consideration can be broken down into several categories, such as initial material cost, total installed cost, total cost of ownership, etc.
Three of the most common actuators, gas over oil, direct gas, and natural gas-driven low-pressure, must be modified if they are to be installed in new applications. Two solutions utilizing natural gas-driven controllers that are permitted under the new rule are self-contained natural gas driven controllers, and natural gas-driven controllers equipped with a vent recovery system. A self-contained natural gas driven controller consists of a gas/hydraulic or direct gas actuator with a recompression system that captures the exhaust and pumps it back into the sales line.
There are also organizations that manufacture recompression retrofit kits for existing gas over oil and direct gas operators. Vent recovery applications require the use of vent recovery systems that capture the gas emissions of natural gas-driven controllers and reroutes that gas to a process that would normally use gas from the sales line, such as a gas fired heater.
It is important to note that if the owner chooses to use this type of equipment, they will be required by the new regulations to perform quarterly inspections using optical imaging equipment and maintain records of these inspections and any repairs deemed necessary. The initial cost of the retrofit might be lower than replacing the entire assembly, but there are drawbacks. The quarterly inspections, record keeping, and maintenance required makes the total cost of ownership of these options higher than total cost of ownership of other solutions.
Alternative Options
Alternative options, outside of gas/hydraulic and natural gas-driven low-pressure actuators, are instrument air driven pneumatic actuators, electric, hydraulic, electro-hydraulic, self-contained hydraulics, spring-return gears, spring-return electric, and high-efficiency gears. Since natural gas as a motive will not be allowed, these options require an alternative motive source for operation such as manual operation, electric operation (either grid powered or solar powered), or pneumatic operation (instrument air or nitrogen).
Instrument air-driven low-pressure pneumatic actuators have long been used in the oil & gas industry. These come in many different styles such as rack & pinion, scotch-yoke, double scotch-yoke, diaphragm, and more. These actuators can be used with multiple operating medias. A common application of these instruments in the oil & gas industry is to use natural gas from the pipeline. A series of regulators and relief valves are used to ‘knock down’ the pipeline gas to a usable pressure, typically 60 to 120 PSI. Natural gas-driven low pressure pneumatics exhaust gas during operation and therefore will not meet the zero-emission requirement of the EPA. These actuators are, however, relatively easy to modify to meet the new requirements. Low-pressure pneumatic operators can be easily converted to utilize instrument air or nitrogen as an operating media. A low-cost option would be to install a nitrogen tank at the operator, but this solution will require maintenance and monitoring of the nitrogen level. A nitrogen compressor can be used to retrofit gas powered actuators, it requires the use of an internal or external air compressor, making the system more complex and costly.
A solution that is gaining popularity in conjunction with instrument air driven actuators, is the use of packaged compressors. There are multiple vendors that are currently supplying packaged compressors that can be powered from the grid, a solar system, or even powered using natural gas. Packaged compressors can be sized for as little as one operator or for multiple operators, such as you would see in a compressor station. This solution can be cost effective for small retrofit jobs where low-pressure actuators are already installed or in new applications where many operators are needed, especially if grid power is available. Solar powered or natural gas-powered instrument air compressors are a viable solution for remote locations that do not have access to grid power. To keep the compressed air clean and dry, compressors and their components such as filters, aftercoolers, lubricators, separators, and dryers require more maintenance than electric actuator solutions. While the initial cost of installing these compressors might be lower than other options, the total cost of ownership must be considered a factor in deciding the cost effectiveness of this solution once the preventative maintenance and upkeep is factored into the equation.
Electric operators are mentioned extensively by the EPA as a viable option to natural gas-driven controllers. Much of this comes from a report done by Carbon Limits in 2016 and updated in 2021. Today’s electric operators can be operated using single-phase (120 VAC-230 VAC), three-phase (208 VAC-480 VAC) and low voltages (12 VDC -24 VDC). This flexibility allows for options based on what source of power is available, solar, grid, or on-site generator. If grid power is available, electrics are a cost-effective solution. If grid power is not available, a solar system or a natural gas generator can be installed. One comment mentioned in the EPA’s report is that electric operators require qualified technicians for initial set-up in the field, but once installed, electric operators require very little maintenance making the total cost of ownership low compared to other options.
A Look at New Types of Systems
This discussion would not be complete without an update on solar powered systems. While solar powered air is a relatively new but promising technology, photovoltaic solar systems have been installed in various application in the oil & gas industry. Updates from the 2016 Carbon Limits reports published in 2021 indicate that the costs for solar panels and batteries have been coming down as they gain popularity. Suppliers and users of this equipment have also learned lessons on the application and installation of this equipment.
Hydraulic actuators and electrohydraulic actuators can be grouped into the same discussion. Hydraulic actuators require the use of a hydraulic power unit (HPU). An HPU is typically used to operate several hydraulic actuators at a site but can be used for a single actuator. Electrohydraulic actuators have the hydraulic power unit built into the actuator. These usually consist of an electric motor, pump, controls, and a hydraulic reservoir. Electrohydraulic actuators eliminate the need for hydraulic tubing from the HPU to the actuators making them a cleaner solution. Both of these solutions require power to operate; either grid or solar power. The benefit of these two solutions is that the actuators can be supplied with a spring to create a fail-safe solution. The use of hydraulics also can provide precise positioning in control applications. Hydraulic and electrohydraulic actuators are susceptible to temperature fluctuations in certain areas of the country as well as leaks and increased maintenance.
Spring-return electric actuators are gaining popularity and are becoming common industry alternatives. There are multiple vendors out there that offer spring-return electric actuators. The original units were designed for the process industry and consisted of a quarter-turn electric actuator with a clock spring and clutch mechanism to release the spring on loss of power. These smaller units typically had low output torques and a relatively high cost per in-lb. of torque. Recently, manufacturers have developed options that expand the torque output of spring return electric actuators. They can be used for both rotary valve and linear valve applications. There are organizations that manufacture a complete unit and organizations that manufacture components such as the electric controller and spring-return gear assembly. The spring-return gear allows for increased scalability with installed products over 225,000 in-lbs. and designs that produce more than 1 million in-lbs.
An important item to consider is how the spring is held in its ‘ready’ position.
Some units use an electromechanical brake while others use a true mechanical device, such as a wrap spring assembly. This difference can have a huge impact in power consumed while being held in its steady state, especially when using a solar system to operate the actuator as it may require a larger battery bank. One of the many benefits of using a spring-return gear in this application is the flexibility to use any manufacturer’s electric actuator. This allows the end-user the opportunity to use a piece of equipment they are familiar with, eliminating the need for additional training while also eliminating the need for additional spare parts.

Power-less Solutions
There are solutions that do not require power that can be used in certain applications. Self-contained hydraulics can be used as a manual-reset ESD valve. These typical consist of a manual hydraulic pump, hydraulic reservoir, and controls mounted to a spring-return hydraulic actuator. These actuators can be set up, so if low voltage power is available, they go to a failure position on loss of power, a low-or high-pressure signal, or a signal from the control room. These devices can operate without power but are reduced emission at that point and not emission free.
A small solar system that can provide 24 VDC allows for an emission free failure mode as well as communication back to the control room that an upset condition has occurred. Once driven to the failure mode, an operator must go out to the site to identify and fix any upset condition and then pump the actuator back to the ready position. These applications require low voltage power for operation from the control room or from a remote operated controller and pressure switch/ transmitter. The operator usually will have a position transmitter installed on the actuator as well, so they are aware of the valve position. In certain areas of the country, these operators can be susceptible to temperature changes and can ‘creep’ to the failure position causing an error reading from the position transmitter when the switch loses contact.
Spring-return gears can be used as a manual-reset ESDs as well. Instead of hydraulic, they use a planetary gear mounted to a spring-return rack and pinion system. Once the spring-return gear receives a signal (either electric or pneumatic), the spring is released and the valve is driven to its failure position. Again, much like the self-contained hydraulic, the operator must go out to the field, identify, and fix the problem, and use the gear to drive the actuator back to the ready position. As an all-mechanical solution, spring-return gears are not affected by temperature changes which eliminate the problem with creep as well as hydraulic leakage. In many cases, spring return gears require much less work to reset using the handwheel than stroking the hydraulic pump.
In cases where valves are not operated frequently, high-efficiency gears can be used in lieu of natural gas driven operators. Convenience actuators are used on larger valves that are rarely operated so pipeline operators do not have to manually turn a valve. Many organizations have size limitations on when gears can be used. Historically, commercially available worm gear operators took an inordinate amount of turns to open or close a valve. With the advent of high-efficiency worm and high-efficiency planetary gear operators, opening and closing of valves takes much less work.
Due to the proposed regulations banning gas-emitting controllers, oil and gas organizations may need to rethink these limitations and allow for high-efficiency gear operators to be used on larger valve sizes. Table 1 shows the difference in the amount of turns on a commercial worm gear, a high-efficiency worm gear, and a high-efficiency planetary gear. High-efficiency gears can be designed with lower rim-pulls as well, making these good alternatives to convenience actuators to reduce GHG emissions.
Final Thoughts
To recap, it appears oil & gas companies are going to have to change the way they operate their isolation and control valve assemblies, so they no longer emit gas during normal operations. There are multiple options that can be considered based on several different parameters. Organizations will have to make this decision based on what is most important to them. Options include overall cost of material, total cost of installation, return on investment, total cost of ownership, amount of maintenance, or other parameters decided on by the end-user.
References:
- Standards of Performance for New, Reconstructed, and Modified Sources and Emissions Guidelines for Existing Sources: Oil and Natural Gas Sector Climate Review. (2021, November 15). Retrieved from https://www.govinfo. gov/content/pkg/FR-2021-11-15/pdf/2021-24789.pdf
- Saunier, S., Darani, H., & Pederstad, A. (2016, August 1). Zero Emission Technologies for Pneumatic Controllers in the USA. Retrieved from www. carbonlimits.no/wp-content/uploads/2017/01/ Report_FINAL.pdf
- Standards of Performance for New, Reconstructed, and Modified Sources and Emissions Guidelines for Existing Sources: Oil and Natural Gas Sector Climate Review. (2021, November 15). Retrieved from www.federalregister.gov/ documents/2021/11/15/2021-24202/standards-of-performance-for-new-reconstructed-and-modified-sources-and-emissions-guidelines-for
- Saunier, S., Darani, H., & Pederstad, A. (2016, August 1). Zero Emission Technologies for Pneumatic Controllers in the USA. Retrieved from www.carbonlimits.no/wp-content/uploads/2017/01/Report_FINAL.pdf
- Venugopal, M., Saunier, S., (2021, November. Zero Emission Technologies for Pneumatic Controllers in the USA. Retrieved from cdn.catf.us/wp-content/ uploads/2022/01/31114844/Zero-Emissions- Technologoes-for-Pneumatic-Controllers-2022.pdf

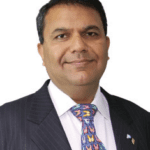