She did it the hard way, working while obtaining a degree in mechanical engineering and starting her full-time career at Fluor’s South African operations. She worked there for nine years before moving to Houston, Texas to join the piping material engineering group alongside Ron Merrick, now Director of Piping Material.
Dwyer has performed in several leadership roles in her long career, including six years as an operations supervisor and a couple of years in procurement, before finding her way back to capital projects and the technical side of piping, which she finds much more challenging but also more gratifying.
“You deal with everything,” she tells Valve World Americas. “There is no such thing as a typical day. You are dealing with different schedules, different client requirements and of course, you are always looking at lowering costs. It is about balancing all of those different elements.”
Valve World Americas was thrilled to have the opportunity to speak to Dwyer about the challenges of working for a global company, the most enjoyable aspects of the job, how Fluor is dealing with increased environmental regulations, and her predictions for the future of the industry.
A project, a team, a taskforce: All different parts of a big machine
As a global company, Fluor has offices on almost every continent and time zone. In each of those offices, employees come from a myriad of different cultural backgrounds, speak dozens of languages and represent every imaginable level of experience and education.
To save on labor costs, Fluor has ad- opted a workshare strategy, wherein some responsibilities and tasks are al- located to other offices. In other words, a project could be in the United States, but the spec development, calculations, and procurement activities could be assigned to the Shanghai office.
This method of operation has been hugely successful in terms of saving on labor costs, as labor rates in some countries are as little as one tenth of what they are in the United States. However, that is not to say that it is the easiest. According to Dwyer, in fact, it has proven to be the most challenging aspect of her job.
“Communication can be difficult,” she says. “Language is always a barrier and communicating in different time zones is a challenge. I am not always able to just call and check in, everything is done through email and weekly conference calls.”
Adopting new habits has helped Dwyer to deal with the some of the more challenging aspects of workshare and mentoring overseas. “It is good practice to follow up on any conversation with an email,” she says. “Then you have it in writing and written language is often much easier to understand than verbal language.”
Despite the challenges, Dwyer is passionate about the job and loves getting results; accomplishing a task, recognizing growth and development in her men- tees and above all, winning the contract to start on a detailed engineering project.
“The reward is being able to start the detail engineering on a newly awarded project after the completion of the FEED (Front End Engineering Design) phase, because that is the most interesting. Now we actually get to do something, and we are all working towards a common goal, all different parts of a big machine,” she says.
Building to the latest standard: Keeping informed to stay ahead of the curve
Fugitive emissions, no longer a distant threat but a present reality, is at the forefront of everyone’s mind these days. We asked our expert in what capacity Fluor has been affected by increasingly strict fugitive emissions standards and learned to what extent the company takes the issue very seriously—from actively participating in API (American Petroleum Institute) standards code meetings, specifying standards and incorporating the requirements to redesigning the plant itself.
“Anytime you have a flange connection or a joint, you have the possibility of fugitive emissions. We do a lot of things to try to eliminate these risks, not only by selecting valves designed for applications with higher leakage probability but in the design of the plant itself. When we eliminate flanges in the design, we are trying to minimize leak paths.”
Ultimately, however, it is the operations team and manufacturers that are most affected by the new regulations, with some manufacturers feeling blind- sided by stricter requirements. More stringent requirements have necessitated changes to valve designs and those manufacturers who have not been involved in API, who “skipped the meetings,” will have a tough time selling their valves to a company like Fluor.
“We used to ask for the latest edition of the standard,” explains Dwyer. “Now we want to know what that edition is. Most of all, it will affect a lot of stock valves, valves on the shelves, because they are not going to be made to the latest standards and whatever we do, whatever we touch, we make sure it is to the latest standards. We always build to the latest codes and standards that are available or unless directed otherwise by our clients.”
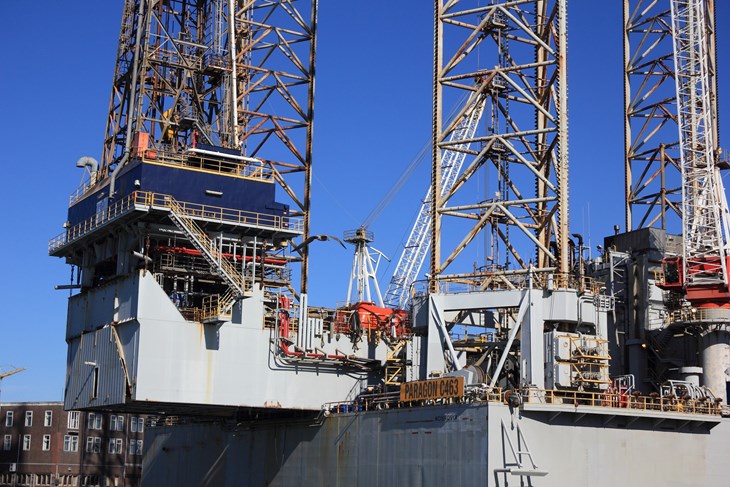
Many EPC companies work with an Approved Manufacturers List (AML) to simplify the procurement process, but Fluor does not. “It is a liability for Fluor,” says Dwyer. “If we worked with an AML, we would have to audit each of the manufacturer’s facilities, which we do not do.”
Instead, they have what they call an Evaluated Supplier List and a Manufacturers List, which is an internal list of all the suppliers and manufacturers that Fluor has used over the years without experiencing any issues with the quality of the product. In other words, a list of manufacturers that Fluor holds in good standing, which the procurement team can consult when making purchasing decisions.
What if the client has their own ideas about what they want to do and who they want to use? “We use a client’s AML or create a project list with recommendations on what to use, but of course the client will get a buy-in from us if they have a really strong preference. However, because of the amount of work that we do, and “We use a client’s AML or create a project list with recommendations on what to use, but of course the client will get a buy-in from us if they have a really strong preference. However, because of the amount of work that we do, and overtaken demand, creating a fiercely competitive market and driving prices down. Marathon Oil, and companies like it, are able to get high-quality materials at a much lower cost and they are wise to take advantage while they still can – because it might not last much longer.
“We are already seeing the price of gas starting to edge up,” says Dwyer. “More capital projects are going ahead, and we are already seeing some of the big oil companies, companies like Exxon and Chevron, starting to make money again and now they have the money to keep building. That’s a good sign.”
With all the political changes going on in the United States, we asked Dwyer what she thought would happen with fugitive emissions standards; if they will they become more or less stringent in the current climate.
While she suggests regulations may become less stringent in the short-term, ultimately, Dwyer believes that manufacturers, EPC companies and end users will stay the course and continue to hold themselves, and their suppliers, to the same high standard.
“Now that we have gone down this path, we have committed to it. The EPA might let up a little, but that could change quickly and then we would end up scrambling again. Additionally, end users want better products – it makes it easier for them to control and manage the plant. After all the years we have spent getting to the point we are at, I doubt we would turn back now.”
As always, we also asked Dwyer what advice she would give to young people entering the industry. With mentorship opportunities few and far between, and the very landscape of the industry and how it operates changing every day, how can the next generation set themselves up for success?
“The more you get involved, the better,” she says. “Some young people think they can just find the information they need online, or read about it on Wikipedia. To me, that is not an education. The way you learn is to go and see it with your own eyes, and talk to people who know about it.”
“Having a network is critical, and it will save you so much time. When I am asked a question, I usually have a response within ten minutes, because I know people and I know who to ask if I do not have the answer. You need to build those relationships, and you can’t do that online or by just sending an email. You need to put in the time.”
About Claire Dwyer
She is an esteemed member of the Fugitive Emissions Summit Americas 2018 Steering Committee. The Fugitive Emissions Summit Americas is a Conference & Exhibition dedicated to fugitive emissions control throughout various industry, including oil & gas, chemical, petrochemical, power generation and more.