When specifying gaskets for applications, one of the primary concerns is typically, ‘will this particular material stand up to the process media to which it will be exposed’? There is not often much consideration for the inverse effect of how the gasket material itself could impact the process. For most industrial applications, this is justified by the fact that there is little risk of any particulate from the gasket material adversely affecting the final product in a substantial or significant way. Exceptions apply of course, such as discoloration concerns for particular products and highly sensitive applications; for example, plastics used in semiconductor and microchip production.
However, gasket materials utilized in applications where products are being produced or processed for human consumption are more closely scrutinized, and for good reason.
By Chris Morris, Sales Engineer – Teadit
Zero Tolerance for Contaminants
Service organizations like the National Sanitation Foundation (NSF) and 3-A Sanitary Standards, and government agencies like the Food and Drug Administration (FDA) seek to develop standards and safety guidelines to protect individuals, as consumers, from products that are unsafe or hazardous to one’s health and well-being. These standards, such as the NSF-61 which establishes guidelines to prevent contamination of drinking water from any of the materials used within processing and distribution systems, require the manufacturers of those materials to meet strict contaminant thresholds and to undergo regular sampling and inspection.
Contamination of a product with unsafe chemicals or other ‘leachables’ is not the only area of concern, however. Even if a gasket material is safe and will not contaminate a consumable product, there are other concerns for food, beverage, and pharmaceutical producers. When considering a new gasket material for their processes, major breweries perform taste testing on their beers that have been exposed to the material to ensure that it does not impact the flavor their customers have come to expect and enjoy. Similarly, one can imagine opening a bottle of pills and seeing small black specks in the otherwise white pills. Safe or not, the individual probably will not risk taking the medication because it looks abnormal from what is expected.
These are some of the many concerns for producers. Not only must products be safe, but they must look, taste, and feel appealing to consumers. Therefore, the components, including gaskets, used in the manufacturing processes of these goods must not adversely affect the quality of the final product.

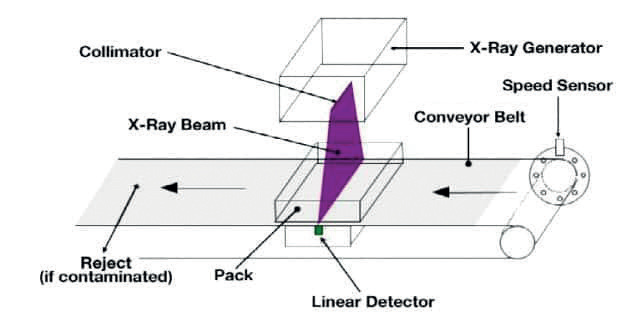
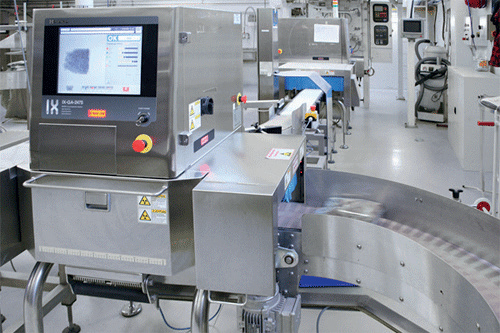
Dated Sealing Materials
For many years, the primary approach to FDA and similar applications was to develop and utilize materials that were safe and free from harmful contaminants, tough (i.e. not prone to shredding, tearing, or flaking), and white or relatively color free. Often these materials were specialized elastomeric compounds or virgin forms of polytetrafluorethylene (PTFE for short, or Teflon as it is commonly known by its trade name). While these products meet the primary health and safety requirements, and check many of the secondary boxes listed above, neither are ideal choices from a sealing perspective.
Both elastomeric compounds and PTFE are prone to extreme creep, or cold-flow, a phenomena associated with some gasket materials; the materials exhibit a tendency to expand or “flow” radially when compressed. Creep is a primary contributor to bolted joint relaxation, where the joint loses the applied compressive force over time, which can lead to leaks, blowout, and other sealing issues. Moreover, these types of materials do not commonly perform well in steam service, and which is one of the primary methods for cleaning and sanitizing lines and equipment in food, beverage, and pharmaceutical applications.
The use of these materials can therefore further compound pre-existing sealing issues leading to increased downtime or loss of product. If issues do arise, determining the contamination of these materials is difficult, if not impossible, to detect through traditional means due to their low conductivity properties.
As manufacturers continued to strive for improvements to better serve the needs of this industrial segment, they looked for ways to take advantage of the safeguards already in place.
Innovative Advancements
Food, beverage, and pharmaceutical companies have long utilized x-ray and metal detection technologies to safeguard their products from contamination by foreign materials. What if one could develop gaskets and gasket materials that would be easily detectable by these existing systems? This idea led several manufacturers to develop specialty products that utilized unique combinations of magnetic metallic fillers to produce specialty gaskets, o-rings, etc. that would easily detect a contamination issue.
As an overwhelming majority of these improvements and innovations have been focused on specialty products for sanitary fittings, because they are so broadly used, there are numerous other gasketing applications that continue to lack an improved or better solution.
Of the available materials for general gasket applications, PTFE materials still offer the greatest upside due to the many benefits inherent to the material, such as its high level of inertness and overall cleanliness. To address the well-known pain points of this material, PTFE based gasket manufacturers derived a special manufacturing process for PTFE sheets known as the HS-10 process. Developed in the late 1960s by DuPont, the solution to material creeping includes utilizing fillers to give the material additional strength.
The key to the strength of the HS-10 process is not just the addition of fillers, it is in the distribution of those fillers within the material. Rather than skiving the sheet from a large billet, the way traditional PTFE sheet is produced, the material undergoes a series of steps that ensure a thorough and even disbursement of the fillers throughout the entire sheet area. Additionally, the process creates a high level of fibrillation within the cross-section of the material; the microscopic fibers provide the high tensile strength needed to resist creep.
The development of a metal-detectable sheet gasketing material, coupled with the existing developments for sanitary fittings, will provide food, beverage, and pharmaceutical manufacturers with access to detectable gasket solutions for any flanged connection. As the metal detectable/magnetic HS-10 restructured PTFE technology can provide benefits and opportunities to other industries as well, this emerging technology has significant potential moving forward.
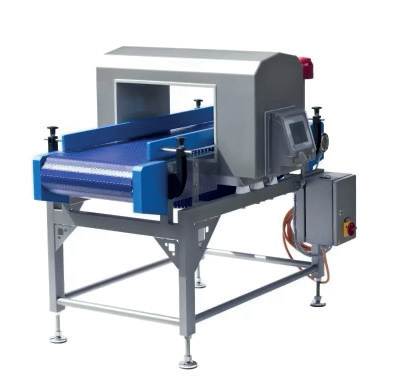
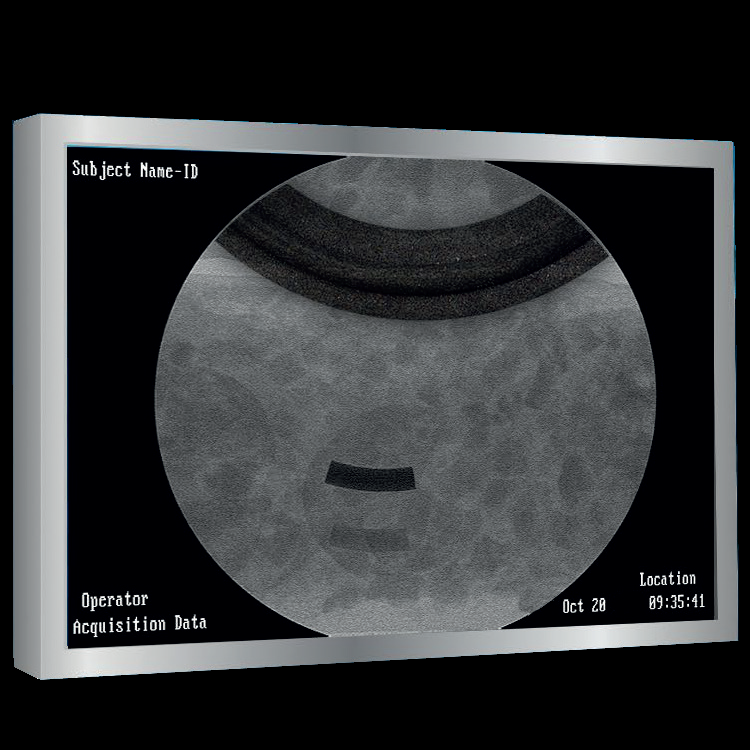
The key to the strength of the HS-10 process is not just the addition of fillers, it is in the distribution of those fillers within the material.
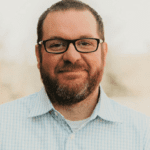