With the increased focus on environmental issues, energy producers are giving thoughtful consideration to the growing concerns of fugitive emissions, and all eyes are on a major player: valves. The world’s largest energy companies are now beginning to audit their greenhouse gas emissions, as well as other energy metrics, in order to achieve global sustainability initiatives such as, ‘Net-Zero 2050’.
By Morgan Keith, Marketing Manager – Ladish Valves
A Global Energy Paradigm Shift
While fossil fuels remain the primary source of energy in the United States today, renewables are gaining momentum, and real estate, due to their sustainability, low contributions to the carbon cycle, and reduced greenhouse gases. They can range from renewable diesel, to hydrogen, to wind, solar, and more.
In short, renewable fuels are fuels produced from renewable resources. These contrast with non-renewable fuels such as natural gas, LPG, petroleum and other fossil fuels and nuclear energy. Renewable fuels can include fuels that are synthesized from renewable energy sources, such as wind and solar.
According to the National Biodiesel Board, “biodiesel, renewable diesel, and renewable jet fuel will be recognized as mainstream low-carbon fuel options with superior performance and emission characteristics. In on road, off road, air transportation, electricity generation, and home heating applications, [biofuel] use will exceed six billion gallons by 2030, eliminating over 35 million metric tons of CO2 equivalent greenhouse gas emissions annually. With advancements in feedstock, [biofuel] use will reach 15 billion gallons by 2050.”1
Low Emissions as a Basis, Not an Afterthought
Due to the increasing ESG momentum, refiners have already begun the conversion and expansion of existing facilities to produce renewable fuels as alternatives to petroleum-based products. This shift in production is driving the need for custom valve engineering and design requirements, and unique specifications beyond the bounds of current applicable industry standards. Now more than ever manufacturers are having to make good on the promises made for sustainable valve solutions. This presents a challenge to valve manufacturers competing for market share and provides an edge to companies with engineering know-how, experience with a wide variety of materials, flexible manufacturing capabilities, material availability, machining, testing and NDE capabilities.
It is estimated that over 50% of fugitive emissions come from valves, and as a result, manufacturers hold a major responsibility in achieving global sustainability. There must be thoughtful consideration given to the design and development of products used to construct and convert these facilities to meet current and future government standards. If the United States wants to lead the world in global sustainability, manufacturers must do their part by staying apprised of new technologies and designs used to engineer these products to ensure there are no (or minimal) leaks in these future ready plants. These new generation valves must meet or exceed stringent fugitive emissions standards such as API 641, API 624, ISO 15848, and TA Luft to compete for the business of a high-profile energy company.

Manufacturer Responsibilities
Manufacturers play a vital role in the renewable fuels economy. What gives competitive advantage to one over another some may ask?
1. Consistent Quality Control
& Manufacturing Capabilities
2. Material Availability / On-Time Deliveries
3. Manufacturing Capabilities
(Machining & Testing)
4. Ongoing feedback loop with customers and end-users
It is imperative that valve manufacturers meet and regularly exceed the highest industry standards for valve performance; they must source valves that are specifically designed and manufactured to meet the stringent demands of the most corrosive service environments and high temperature applications. Sticking to regulation allows manufacturers to avoid secondary leakage paths. Additionally, valves must be produced under rigorous metallurgical and manufacturing controls that assure a consistent, high degree of performance and dependability. Return on investment is enhanced by time-tested and proven products with a high rate of performance and reliability.
With domestic source foundries and strictly monitored international vendors, manufacturers can be relentless about the quality of material sourced from their vendor community. From the receipt of raw material to the certified Material Test Report (MTR), a manufacturer should be able to capture complete traceability including heat codes, inspections, assembly steps, testing, calibration, and NDE testing. From receipt of raw material to valve shipment, every aspect of production and quality should be captured. Chemical and mechanical properties should be cross checked and verified to applicable ASTM standards, and inspection routers must capture every stage of the process. Inspections could include PT, RT, PMI or other material specific requirements from the end user.
It is not just testing and machining capabilities that gives favor to one manufacturer over another. Large-scale energy companies often set quick timelines for refinery conversions and/or expansions. Therefore, in addition to its material availability, manufacturing, and testing capabilities, oftentimes the valve manufacturer is awarded project business based on its ability to meet all of those requirements on an accelerated delivery schedule. Manufacturers must prove their credibility by performing all of these tasks and more not just once, but with consistency across all end markets – all the time.
Materials Matter
When it comes to renewable fuels manufacturing, material selection matters. Proper selection of materials in valve construction can overcome many challenges presented in bioethanol, biodiesel, and renewable diesel applications. Depending on how the end user process is being performed, correct materials can often help combat challenges such as stress cracking, corrosion, and acid attack. There must be ample time invested in analyzing end user requirements in order to gain an understanding of objectives. This allows the manufacturer to subsequently design scalable, sustainable solutions.
In Summary
The energy landscape is shifting, and valve manufacturers bear the responsibility of producing dependable products for a sustainable future. There is a lot at stake when it comes to manufacturing responsibly, but with the right people designing the right products, much can be achieved. Tomorrow’s energy can and should be manufactured today.
References
1. www.nbb.org/about-nbb/mission-vision
ABOUT THE AUTHOR
Morgan Keith manages marketing and business development for the Ladish Family of Brands. Throughout her career, she has expanded the scope of her expertise from traditional marketing into the vast, fast-paced world of modern digital marketing. Morgan has a passion for delivering effective customer solutions with determination and purpose that increase the brand
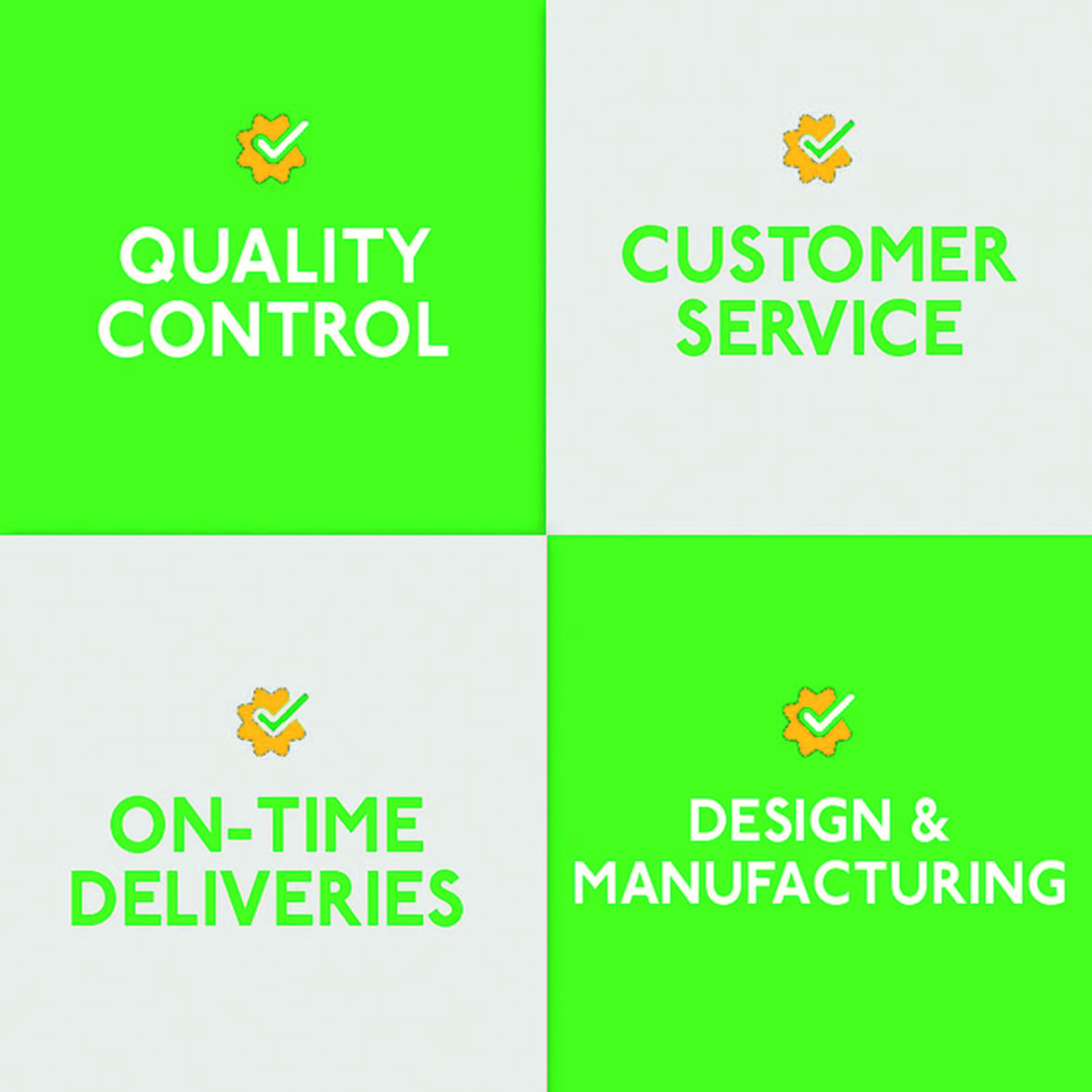