In Part 1 of this article, we will learn more about the resistances related to valve movement.
By Davi Sampaio Correia – Technical Consultant
Making the Move
The resistances associated with movement vary from valve type to valve type. For the purpose of this article, let us take a closer look at a ball valve. In order to open and close the valve, torque must be applied to the stem. As the ball rotates, it needs to overcome the resistances related to friction and fluid flow. The amount of torque required is not constant; in fact, there are six major torque values associated with its opening and closing. They are:
a) BTO – Break to Open: The maximum torque required to break (unseat) the ball from its fully closed (seated) position, against the maximum pressure differential. The ball opens against just one seat under pressure.
b) RT – Running Torque: The torque required to move the ball to an intermediary position (approximately 35° to 45°).
c) ETO – End to Open: The maximum torque required to seat the ball in its fully open position.
d) BTC – Break to Close: The maximum torque required to break (unseat) the ball from its fully open (seated) position.
e) ETC – End to Close: The maximum torque required to seat the ball in its fully closed position.
f) BTO with Double Block: The maximum torque required to break (unseat) the ball from its fully closed (seated) position, against the maximum pressure differential. The ball opens against two seats under pressure.

Figure 1 presents the different ball positions associated with the six torques. The friction and flow resistances mentioned before are related to several factors, which basically fall into two categories: Design and Application.
a) Design factors influencing torque: materials selection, surface finish, tolerances, spring constants, and construction methods are some of the design factors that affect the friction between moving parts. For example, if the seats are made with PTFE, the valve should require considerably less torque than if the seats were made of PEEK, due to the higher friction coefficient of the latter.
b) Application factors influencing torque: The single most influential application factor is the pressure differential which the valve is operating under. The higher the pressure pushing the seats against the ball, the higher the friction resistance that the torque must overcome. It is worth noting that the pressure differential affects torque not only by pushing the seats, but also by modifying flow conditions after the ball starts moving; turbulence during opening and closing may create a fluid-dynamic resistance to movement (see Figure 2 for a schematic diagram of this turbulence). Temperature, solid contaminants, and fluid properties are also other factors that may influence the torque. For example, solid contaminants tend to increase the amount of friction between ball and seats, whereas some light oils – which provide extra lubricity – can decrease the amount of torque required.

If the torques required for opening and closing the valve are continuously monitored, the plotted values should resemble something similar to Figure 3. This Figure plots the torques for two conditions: with and without differential pressure. It can be seen that, without pressure, the BTO and ETO are more or less the same. In a similar way, the BTC and the ETC are also in the same magnitude. With differential pressure, the torque values for BTO and ETC are higher, as expected, due mainly to the higher friction force between seat and ball.
Sign Here, Please
The resistances seen in the previous section must be overcome by the torque applied on the stem. For many industrial applications, a hydraulic or pneumatic actuator is the source of the torque. If the actuator pressure, torque at the stem, and ball displacement are recorded for a given situation, they form what is usually called “valve signature”. It is expected that, if the application is the same, the values associated with the signature should be similar, unless the valve or the actuator is facing problems. The signature can be acquired using only the ball displacement and the actuator pressure, but that makes it harder to pinpoint the source of an eventual problem without disassembling valve and actuator. Figure 4 shows a comparison between the pressure of a new actuator (red line) and a degraded one (blue line). The plot has three distinct sections, that will be briefly explained.

a) First, the pressure in the actuator is stable at 205 bar and the valve has not started to move.
b) Then, the command to close the valve is given. For this case, the actuator spring is supposed to provide the energy for the closing and the pressure recorded is related to the fluid leaving the actuator. In the red line (as-new condition), the spring starts moving the ball when the actuator pressure is at 100 bar. That is, even with 100 bar of pressure left in the actuator chamber, the spring is powerful enough to provide the BTC torque. On the blue line, the pressure has to fall around 40-50 bars lower before the spring is able to move the ball. This is indication of a problem, either in the valve or in the actuator.(3)
c) The pressure on both lines slowly declines. A difference is shown after about the six seconds mark where the red line suddenly has a drastic pressure decrease; this is because the actuator spring has reached the endpoint and the valve is now fully closed. On the blue line, the pressure keeps declining rather slowly, meaning that it takes a longer time to reach the end position. The difference in closing time between the red and blue valve is about two seconds, which might be the difference between accident and safe operation.(3)
When there is torque data available, it is easier to locate the source of problems. Figure 5 shows the results of a test carried out on a special type of ESD-valve with adjustable sealing seat – that is, the contact force between seat and ball can be increased independently from the pipe pressure. The test was done to see how differences in valve friction can be visualized. It was carried out by running the test with no seat active, one seat active and two seats active. All tests were done with no system flow, using actuator pressure sensor and strain gauges.(3)
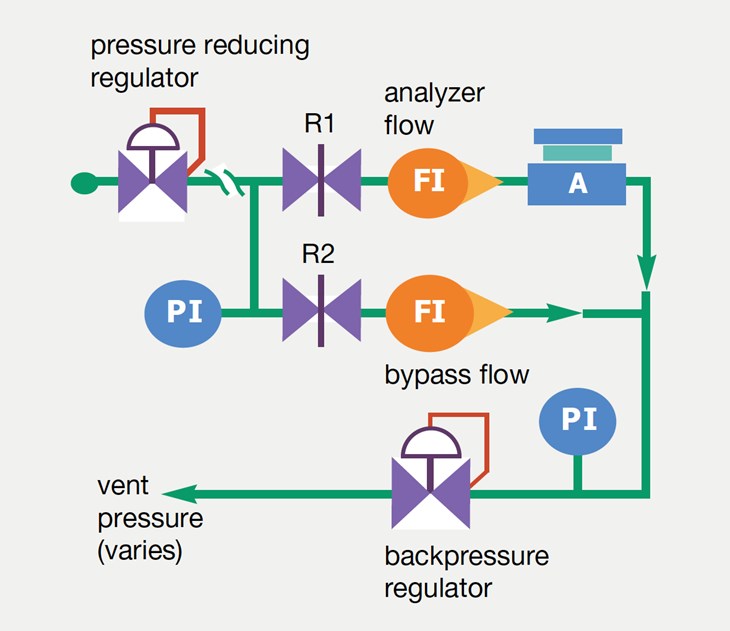
It can be seen in Figure 5 that, for the condition with low friction, the torque values resemble the ones shown in Figure 3 (Valve closing – no Pressure). As the friction is increased, the curve starts resembling more like the “Valve closing – Full pressure” case in Figure 3.
There are not many standards covering the setup, instrumentation, and procedures for acquiring a valve signature. Perhaps, the most common ones are related to subsea valves – API-17D (Specification for Subsea Wellhead and Christmas Tree Equipment) and API-6A (Specification for Wellhead and Christmas Tree Equipment). These API standards establish requirements for Performance Verification Tests (PVT), which are designed to validate a valve’s design and provide acceptance criteria for functional tests that are performed during Factory Acceptance Tests (FAT).
The API standards require cycling a set of valve and actuator under several conditions. The variables related to valve signature are recorded and the valve is dissembled and inspected for wear after the cycling. As the number of cycles for the test is related to number of cycles estimated for the operational life, the API procedure attempts to establish a correlation between valve design and wear from cycling for subsea valves, which are considered critical components for subsea system reliability.

Read Part 2 of this article on January 11th, 2021.
REFERENCES:
1) G. Gokilakrishnan et al, Operating Torque in Ball Valves – A Review, International Journal for Technological Research in Engineering, Volume 2, Issue 4, December-2014 ISSN (Online): 2347 – 4718.
2) Ming-Jyh Chern et al, Performance test and flow visualization of ball valve, Experimental Thermal and Fluid Science 31 (2007) 505–512.
3) Jeeves et al, Predicting Valve Failures in the Digital Age of Valve Management, presented at the Abu Dhabi International Petroleum Exhibition & Conference held in Abu Dhabi, UAE, 11-14 November 2019, SPE-197451-MS.
4) https://www.mrcglobal.com/Global-Region/Products/ValveWatch/Sensors.
ABOUT THE AUTHOR
Davi Correia is a Senior Mechanical Engineer who has worked at a major Brazil-based oil company for the last 15 years. Correia is part of multi-disciplinary team that provides technical support for topside piping and equipment of production platforms. During this period, he began to work with materials and corrosion, and later moved to piping and accessories technology, where he has become one of the lead technical advisors on valve issues. Correia was part of the task force that revised the IOGP S-562 standard, and wrote the S-611 standard. Correia has a master’s and a doctor’s degree in welding by the Universidade Federal de Uberlandia.