When it comes to industrial valves, there are many different types to choose from and they vary greatly in size, design, function, and operation. Finding the right valve design enhances system performance and lengthens service life. Although coaxial valve technology has been in use for decades, many of their attributes and potential benefits remain unknown. It is therefore important for valve end users to be aware of the ways that this technology could improve their processes.
By Ralf Hinz, VP of Sales – Co-Ax Valves Inc.
A Glance Back
The coaxial valve was invented by Gottfried Müller, a German engineer, in 1960 out of necessity. Many valves from that era were often thought of as too slow, too unreliable, and too prone to failure.
At the core of most of these problems was the extreme pressure differentials created inside valves by high operating pressures. Excessive actuation forces were required to overcome these pressure differentials. High-pressure differentials also increased valve cycle speed and made operation erratic and unpredictable. Structural strains caused by pressure imbalances caused accelerated valve wear and early failure.
Today, the descendants of these original coaxial valves are being used in a broad range of applications worldwide – successfully handling system pressures up to 500 bar (7,500 psi) while delivering millions of precise, repeatable cycles at actuation speeds as rapid as 30 milliseconds.
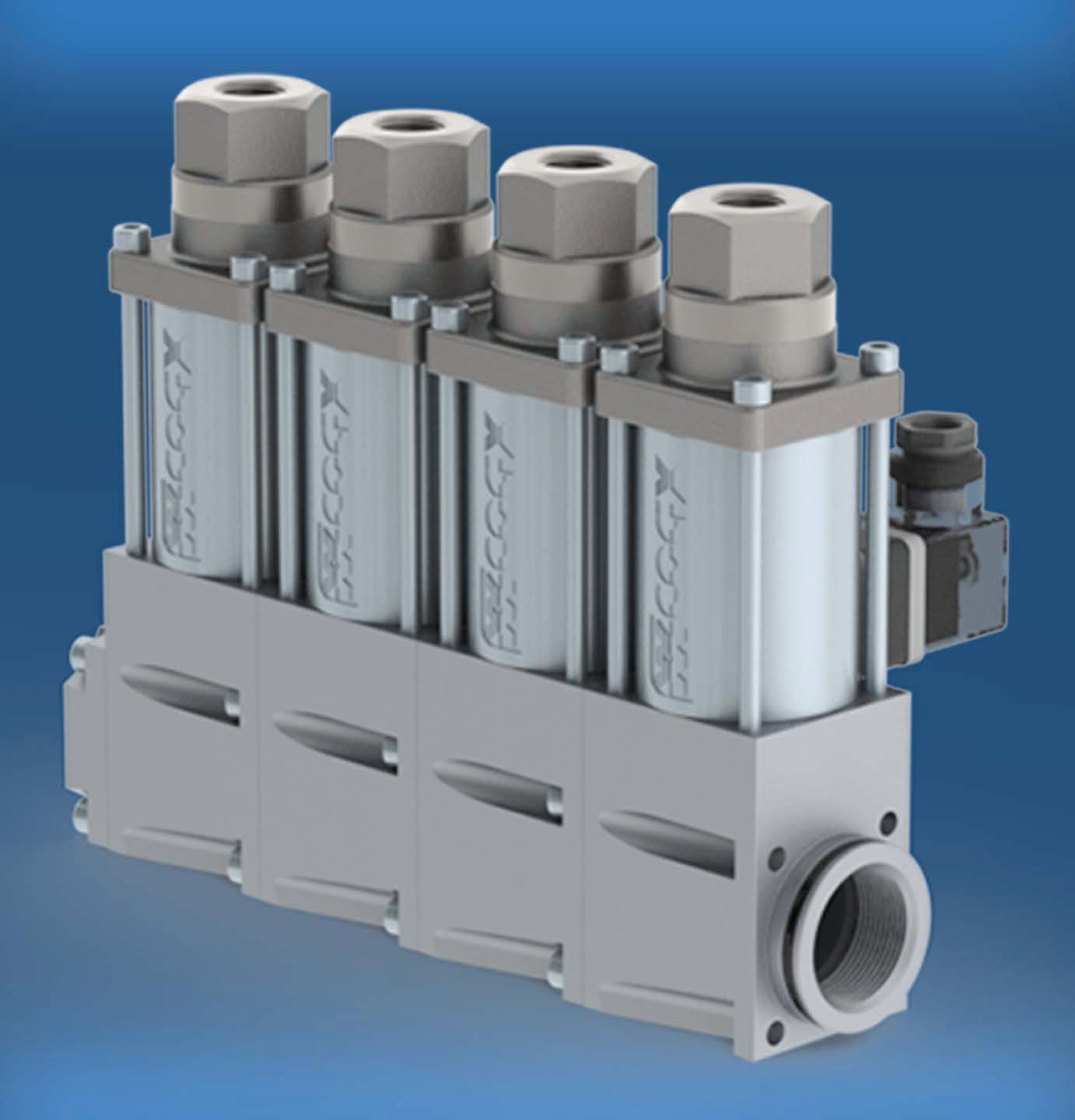
Unique Design
A coaxial valve works by utilizing an internal, axially movable hollow tube, which can either control or divert the flow of media passing through the valve. The internal tube is typically made of stainless steel, which offers greater corrosion, wear, and chemical resistance, making the valve suitable for a wide range of aggressive or corrosive liquids or gaseous media.
The coaxial tube is supported by guiding bands and dynamic seals, which only allows for axial tube movement and prevents the media from contacting any other valve components inside the actuation chamber. The tube ends seal against a seat disc to prevent the flow of the media when the valve is in the closed position. The valve can be actuated by either an electromagnetic solenoid or a pneumatic actuator.
The key aspect here is that the valve, by design, is pressure balanced in any position. The only forces that the valve must overcome are those arising from the seal friction and viscosity drag. There is no pressure differential to overcome and therefore, the switching behavior is unaffected by the system pressure, even if the pressure is fluctuating. There is no internal pilot orifice through which the media is forced to flow through, this makes the valve less susceptible to contamination. Regardless of the type of actuation, the actuator is always integral, which eliminates the possibility of stem seal leakage to the atmosphere.
Another unique feature of the co-axial design is that the process valve and actuator are combined in a single unit. Since actuation requirements are minimal, no bulky external actuator is required. Therefore the valves take up less installation space, further increasing their versatility and making them easier to integrate into new and existing machines and systems.
Key benefits of a coaxial valve include:
- High cycle life,
- Fast acting,
- Compact design,
- Comparatively high flow rates,
- Less susceptible to contamination,
- Back pressure tight,
- Bi-directional flow,
- Self-compensating for seat wear, and
- Valve can be mounted in any orientation.
The control tube is the sole moving part. When energized, the actuator shifts the control tube either away or against the valve seat to allow or stop flow. A spring inside the actuator, makes the valve either fails closed or fail open and at the same time provides for seat wear compensation.
A Closer Look
Pressure Balanced
Regardless of system pressure and pressure differences, the coaxial design balances forces within the valve. Whether it is regulating vacuum or high pressure, the results are always exact and consistent. Coaxial valves, unlike some conventional valves, do not require a minimum pressure differential to work.
High Cycle Life and Fast Actuation
The control element inside a coaxial only needs to move about 25% of the actual orifice size. They are also extremely fast-acting when compared to other actuated valves, even with a highly viscous media and regardless of the pressure differential, as fast as 30 milliseconds.
Compact Size
All of the valve components are engineered around the axis of the flow channel, eliminating the need for an external actuator and keeping a compact profile.
Comparatively High Flow Rates
Coaxial valves are suitable for highly viscous fluids. The flow path is designed with minimal obstructions, which permits comparatively high flow rates with a minimal pressure loss. Despite the valve’s compact size, the media is capable of flowing straight through the valve without any significant deviation.

Less Susceptible to Contamination
Even in the presence of contamination in the media, the coaxial valve design reduces valve seat wear. Coaxial valves have up to ten times the lifetime of ordinary valves, even under harshest conditions. The straight-through flow also prevents buildup on the seat, by flushing any dirt or contaminates out of the valve.
Back Pressure Tight
In the closed state, the force of the spring inside the valve, forces the control tube to be positioned against the valve seat. This enables the valve to handle a reversed pressure differential.
Bi-Directional Flow
The valve’s design allows the medium to flow in both directions, in some cases eliminating the need for check valves elsewhere.
Self-Compensating for Seat and Seal Wear
While the valve is de-energized, the spring is pushing the control tube into the seat. At the same time the spring compensates for seat wear. The actuator on a coaxial valve is always integral, which eliminates stem seals. Any leakage caused by a worn out or damaged dynamic seal will be contained internally.
When to Use a Coaxial Valve
For many varying reasons, coaxial valves are highly advantageous in applications in the gas turbine market, specifically with their ability to rapidly open and close and low leak rates. The seals used in the composition of valves are particularly long lasting and offer incredibly low rates of leakage. The same goes for processing applications that depend on the pressure-balanced nature of the valve design, as well as the aerospace and the machine tool industry.
For a valve to perform well in Hydrogen service, it has to have excellent shut off capabilities, as well as low internal and external leakage, in order to ensure high level of process stability and repeatability of the system.
Final Thoughts
For over 60 years, coaxial valves have been used to control some of the most challenging flows, from non-lubricating liquids, vacuums, and gaseous medias to gelatinous, abrasive, contaminated and aggressive media. They have established a strong record for speed, repeatability, durability, and reliability under extremely difficult conditions, and have emerged as the valve of first choice in several industrial segments. Yet many who specify valves are still unaware of coaxial technology, and the potential benefits.
