Does one need all the actuators on the facility to be of compact design or can the optimum range and applications be found wherein returns of using both compact and scotch-yoke designs is maximized? The underlying question is: How and when do I use the compact actuator technology?
The first step toward answering the question is to examine the different technologies available within the compact actuator offerings and become familiar with designs and general selection criteria; then proceed to compare the benefits considering weight and dimensions of the two models (compact technologies and conventional scotch-yoke design), and answer the question stated above based on a specific example.
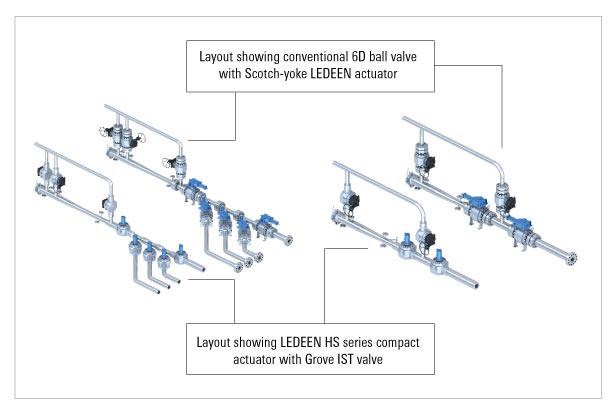
Compact Actuator Technology Offerings
The helical slot mechanism uses a single helical groove on a cylindrical cam and a roller bearing arrangement to give the necessary conversion of linear motion to a rotary motion. (Figure 1)
In the arrangement of a helical spline mechanism, the linear movement is converted to the rotary motion using a helical gear mechanism. (Figure 2)
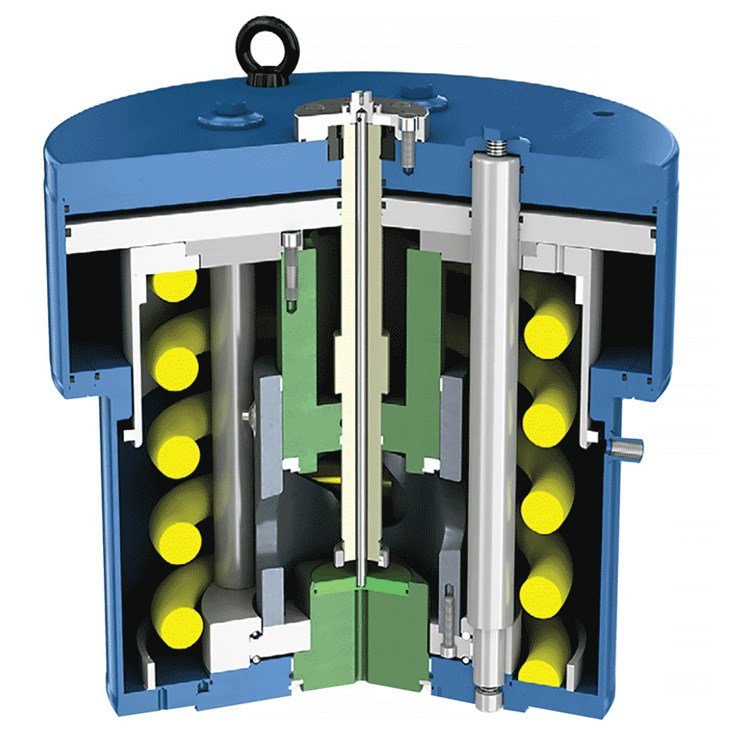
Figure 1: The LEDEEN CP series compact actuators with helical slot mechanism in spring-return configuration. (Courtesy of Schlumberger)
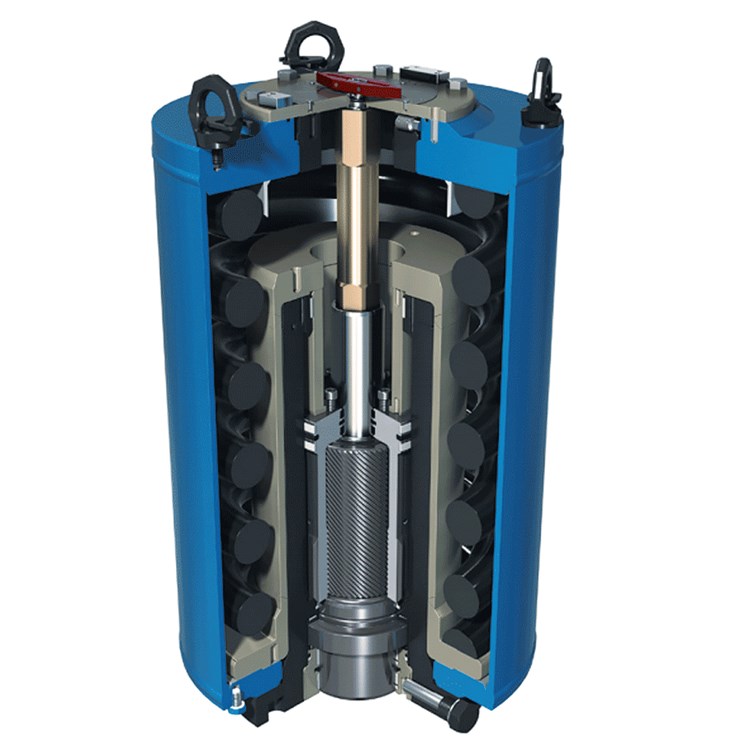
Figure 2: The LEDEEN HS series compact actuators with helical spline mechanism in a spring-return configuration. (Courtesy of Schlumberger)
Efficiency and Reliability Recommendation: Actuators in critical service such as an emergency shutdown (ESD), blowdown, high-integrity pressure protection system (HIPPS), and other similar applications are highly recommended to have adjustable travel stops at both ends (fully open and fully close) of the stroke. Adjustability of the travel-stops at both ends ensures tight shutoff in the close position and optimum flow in the fully open position.
Choosing the Right Mechanism for Best Performance Output and Maximizing Benefit: In general, both helical slot and spline designs are interchangeable with the two primary power fluids used on a typical platform or vessel (low-pressure pneumatic and high-pressure hydraulic); however, each mechanism (slot or spline) has performance advantages over the other as summarized in Table 1. The table also can be used as a basic technology selection criteria.

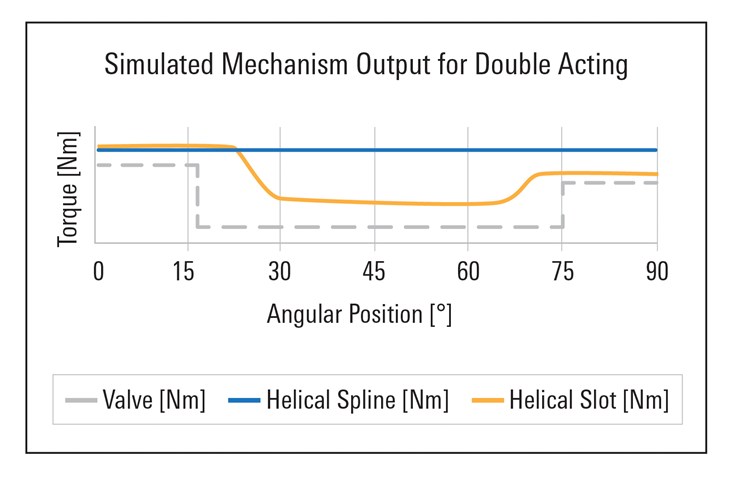
Simulated torque profile of helical spline and helical slot mechanisms in a double acting configuration. (Courtesy of Schlumberger)
The two mechanisms differ in the way torque output is delivered. As shown in the chart above, the helical slot actuator minimizes the energy in the mid position of the valve and helps reduce issues like jerking, tangential velocity, and energy releases. Meanwhile, helical spline delivers a constant torque for the entire duration of the stroke.
Evaluating Real Benefits and Answering the Question of When to use the Compact Actuator:
To select the best fit actuators and to maximize the returns, it is recommended to perform a complete analysis of each actuator once the valve is selected. The following criteria is suggested.
- Weight only
- Space only
- Weight and space only
- Weight, space, and cost
The criteria will help determine the true benefits when comparing the attribute individually or collectively. The comparison is made between the compact technologies and conventional scotch-yoke designs. Each parameter namely length, width, height, envelope space, weight and cost of the actuator is evaluated. To elaborate, two cases are highlighted in this article with different power source, namely low-pressure pneumatic and high-pressure hydraulic. In each case, two configurations are considered to reflect the different usage of actuators in a FPSO; t two configurations are double acting and spring return. In all cases, the actuators are selected and sized for an 8-in 2500# standard API6D ball valve, t keeping the requirements for torque delivery consistent for both compact and scotch yoke.
Case 1: Low-pressure pneumatic
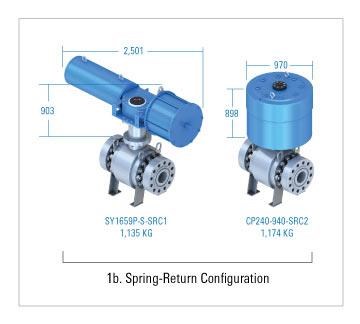
LEDEEN SY Scotch-yoke and LEDEEN CP compact actuator using pneumatic power in double acting configuration. (Courtesy of Schlumberger)
Observation 1a: In the double-acting (DA) configuration, the compact actuator is 58% shorter in length while 13% and 19% more in height and width, respectively. The overall space savings when considering envelope dimensions is only 12% in favor of compact design. The argument in favor of the compact actuator weakens further when weight is the only consideration. In this case, the compact actuator is 128% heavier than the scotch-yoke actuator.
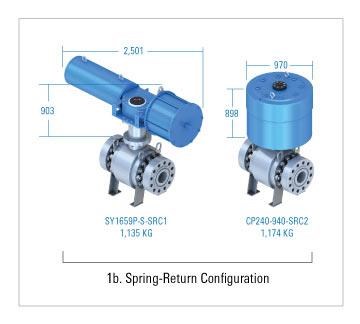
LEDEEN SY Scotch-yoke and LEDEEN CP compact actuator using pneumatic power in spring-return configuration. (Courtesy of Schlumberger)
Observation 1b: In the spring-return (SR) configuration, the compact design fairs better compared to the conventional alternative. The compact actuator utilizes half the space (envelope volume of the compact actuator is 101% less than a scotch-yoke actuator). However, if only weight was the consideration and there were no constraints of space along the pipeline, one could save by selecting scotch yoke.
Case 2: High-pressure hydraulics
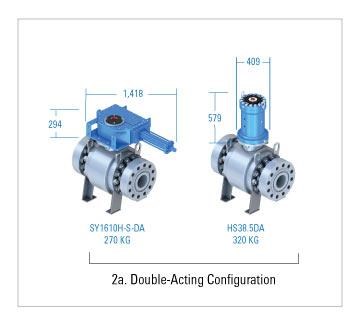
LEDEEN SY Scotch-yoke and LEDEEN HS compact actuator using pneumatic power in double-acting configuration. (Courtesy of Schlumberger)
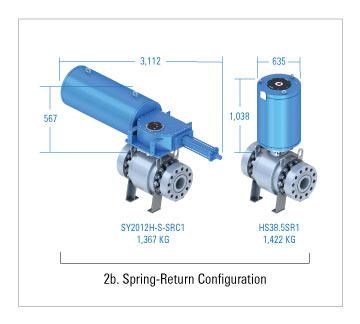
LEDEEN SY Scotch-yoke and LEDEEN HS compact actuator using pneumatic power in spring return-configuration. (Courtesy of Schlumberger)
Observation 2a: In the case of hydraulic actuators in double-acting configuration and using a helical spline mechanism, the envelope area of the compact design is about 197% less compared to the scotch-yoke actuator. The smaller length of the compact mostly drives this space optimization. However, the height of the compact actuator is more than the scotch yoke and this could be an important parameter to consider in managing the overall piping layout. In addition, the compact actuator adds 16% more weight, and if weight is the prime consideration with available space along the pipeline, scotch yoke could be a more favorable option.
Observation 2b: In the single-acting configuration, the most significant benefit from the compact design is the optimization in the length of the actuator assembly. In the example, the compact actuator is 390% or 5 times as short in length compared to a scotch-yoke SR actuator. Considering the envelope volume overall, the SR compact actuator is 241% smaller in size. However, compact actuator in this case adds more weight on the platform, though slightly. The compact actuator is only 4% heavier than the scotch-yoke design, which may be acceptable considering the benefits in optimizing length and overall space.
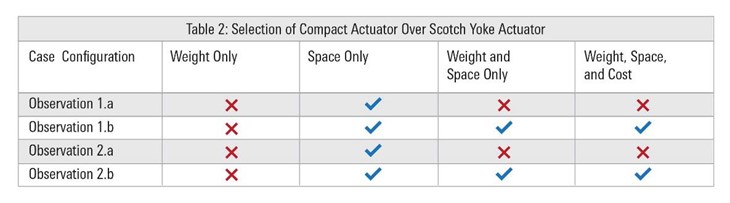
Table 2: The decisions are based on a typical outcome and could vary on a case-by-case basis. (Courtesy of Schlumberger)
Benefiting from Compact Actuator Technology
Finally, the compact actuator technology when appropriately selected can provide a valuable benefit to the project. Space savings more so than the weight could be a key driver going for compact actuators. Detailed evaluation and appropriate selection of actuation mechanisms on every valve of the offshore processing facility will help in true optimization of the project costs. Blanket overall standardization either with compact technology or with scotch yoke could potentially limit the use of the best techno-commercial design solution on the facility. It is also important to note that with each valve manufacturer the torque requirements will change, and hence, the dynamics of the best-fit actuator mechanism may vary.
The industry does recognize the challenges in such detailed evaluation, especially due to multiple manufacturers being involved, and ultimately, the best techno-commercial solution could be a combination of different technologies using a conventional scotch yoke, compact helical slot, and compact helical spline mechanisms on a single facility. Using a single manufacturer for all the mechanisms could help in optimizing evaluation and costs associated with engineering, project management, and aftermarket lifecycle costs.
About the Author
Sarang Tipre is the global technical and commercial sales manager, Valves & Measurement, Cameron, a Schlumberger company, where he has worked for the past five years. In this role, Tipre leads the company’s worldwide valve actuation initiatives that encompass sales, commercial and supports the innovation and development of new products and services. Tipre has held positions such as field engineer, regional manager, product manager, and business development manager and has worked in South Asia, the Middle East, Canada, and the United States. He holds a degree in mechanical engineering from the University of Pune and an MBA from Vanderbilt University.