Airgas is the leading supplier of gases, welding equipment and safety products in the United States. Headquartered in Radnor, Pennsylvania, the Airgas network is comprised of more than 1,400 locations including retail branches, cylinder fill plants, gas production facilities, specialty gas laboratories and regional distribution centers.
Employing approximately 18,000 people across the nation and serving more than one million customers, Airgas supplies industrial, medical and specialty gases, carbon dioxide, nitrous oxide, welding equipment and supplies, process chemicals and more to industries including: manufacturing and metal fabrication, construction, chemicals, life sciences and healthcare, food and beverage, materials and power, defense and aerospace.
“The industrial gas industry is very diverse,” said Fred. “Your cellphone, the metal parts of your chair, the carbonation in your soda… none of it would exist without industrial gas. We have an entire medical group that does nothing but medical gas. We have a food segment and they focus on ways that you use industrial gas in food. I focus on the ways you use industrial gas in welding.”
Fred has worked in the welding and maintenance industry for over 30 years, primarily in the fabrication, heating plant and pipe industry. Entering into the military straight out of high school, Fred worked with armored vehicles and diesel repair before attending college to obtain an AAS in welding and certificate in machining technology, ultimately graduating from the University of Utah with a BS in Welding Engineering Technology. Fred has worked for Airgas, an Air Liquide company, for 18 years as a welding specialist and Subject Matter Expert (SME) for piping code, fabrication, inspection and materials.

“I was hired into Air Liquide in 2000 as a welding specialist and have worked my way up to National Project Manager for our Manufacturing and Metal Fabrication group,” explained Fred. “In addition to working with our customers, I serve as SME for our Capital Improvements special project team. I am fortunate that I have had essentially the same core job responsibilities for my entire tenure, as that sort of experience is invaluable.”
Prior to joining Air Liquide, Fred was employed as a pipe welder, heating plant engineer and weld shop manager. It was in his role as heating plant engineer that he first became acquainted with working with valves.
“I have been on the welding side of things for a very long time, but when I was a Heating Plant Engineer, I was heavily involved with valves in a wide variety of fluid service. In my current role as SME, I help select valves and piping for dozens of fluid services, suggest materials of construction and determine how to best connect the process pipes to these valves,” said Fred. “In my industry we use a lot of valves – manual, automatic, control valves – so it has given me a background in many different types of valves.”
In his current role, Fred’s primary responsibilities fall under four categories; national project management, national sales, subject matter expert and training. The project management role primarily involves coordinating the activities of Airgas’ Welding Process Specialists as they serve national account customers and providing a variety of value added processes. This closely ties into the national sales effort, as the programs and projects assist the company in gaining and retaining its clients. As an SME, Fred works with project teams, providing specialized guidance on welding, code compliance and material selection. Finally, he performs training all over the country for Airgas associates, primarily for nationally launched products and process specialist knowledge transfer.
“I like the wide variety in my work and that I am constantly working on so many different things. There is not much chance of getting bored with only doing one thing,” Fred revealed. “I can be working on a project with 6,000 PSI nitrogen one day and -452oF liquid helium the next. Add that to the sales and travel portion of my job and it keeps you busy.”
In his spare time, Fred is an AWS Certified Welding Inspector and manages to find the time to act is the Chairman of the AWS A5S (shielding gas) committee. He is also a voting member of ISO US TAG 44.

Very Cold Valve Applications
With the wide array of products and applications used throughout Airgas’ facilities, the sheer volume of valves used significant.
“We use an awful lot of valves and there are a few that are at least a bit unusual, if not unique. We have a couple of applications that use non-stop high cycle valves and we have to carefully select products that will maintain leak tightness in both flow directions, for at least 1,000,000 cycles and cycle up to every 30 seconds,” Fred explained. “Of course, there are hundreds of other, more standard valves used in installations I work on and many of these need to be cleaned for oxygen service or be suitable for cryogenic applications.”
With high-pressure and cryogenic applications at temperatures as low as -452°F, materials selection is paramount. Metals that can withstand these temperatures without failing must be considered. The opposite circumstances are also true, as high temperatures can bring their own challenges.
In liquid nitrogen service, Airgas uses special valves of which there are three or four styles that can be used depending on the specific application. In cryogenic situations where the piping system may be covered in ice, an extended-stem, cryogenically-rigged valve – a manual valve with the handle approximately 10-12 inches away from the pipes – would be used to control the -300oF piping system.
The dramatic temperature differential with the valve getting very cold and warming back up again over time can also result in leaks especially through the stem. “It is kind of the nature of the low temperature world. That is why we try to do some things with the extended stem to get the sealing element away from the cold so that it does not have to respond to those wild temperature fluctuations.”
“They are a little more specialty. You cannot just go to a local hardware store, you have to go to a real valve vendor. Most valve manufacturers have a cryogenic part identifier once you order the valves. It tells them to do a few things that are specific to cryogenic valves or they have a line of valves designed specifically for cryogenic service,” said Fred.

“I have had some difficult valves, particularly in steam service. Often, certain steam valves only get actuated once or twice a year, and depending on the type of valve, the seating areas can get filled up with all sorts of water treatment residue. If you close the valve on this residue, you can damage the seat. Now the valve is damaged and may not seal properly. It can be very difficult to replace, as it generally means the whole steam line needs to be shut down. In cases like this, proper valve selection can eliminate this problem,” explained Fred.
Fred went on to explain that material selection is very important for ball valves in cryogenic applications. The valve material must be what is referred to as resilient, meaning it can maintain its strength even at very low temperatures. Carbon steel is not one of those materials, however. Typically, stainless steel, brass, bronze or similar heavy duty alloys can withstand the low temperatures of cryogenic applications.
In terms of seats and seals inside the valve, the material chosen for these components is also crucial. Materials such as Teflon and a variety of other polymers are commonly used in seating the valve. Sealing components such as gaskets and washers must be intelligently selected for resilience at low temperature as the materials may shrink too much at low temperatures, which can cause the valve to leak. The ball itself has to be cross-drilled in a specific way to relieve the annular space, which during the operation of the valve becomes flooded with liquid nitrogen as you perform the act or opening and closing the valve.
“When you close the valve, you have to make sure that there is a way out for that nitrogen, which is going to very quickly vaporize and build up pressure. You have to make sure that the gas has a place to go,” he said.
Globe valves also bear some interesting features, such as the ability to seal tighter than a ball valve. Globe valves allow for flow control functionality rather than just on and off and that it is easier to throttle than a ball valve, he noted. The globe valve does, however, have more pressure lost especially its small openings, in comparison to a ball valve. It is useful in applications that can afford to lose some pressure.
Fred explained that applications at Airgas sites typically run valves in medium pressure applications, anywhere from 20 or 30PSI up to 6,000 and do not typically go up to the higher pressures of 15,000-30,000PSI, except in some instances in working with gaseous nitrogen.
The features necessary in working with cryogenic liquids are not required in gas applications, where affordable carbon steel materials can make valves thick and strong enough to handle 15,000 or 20,000 PSI.
Though the physical issues that Fred has encountered when working with valves can be challenging, the most urgent problem he faces is balancing the competing needs of material of construction, valve type and longevity against cost. All factors must come together in a delicate balance to be successful. Technology plays a big part in helping to extend the lifetime of many components.
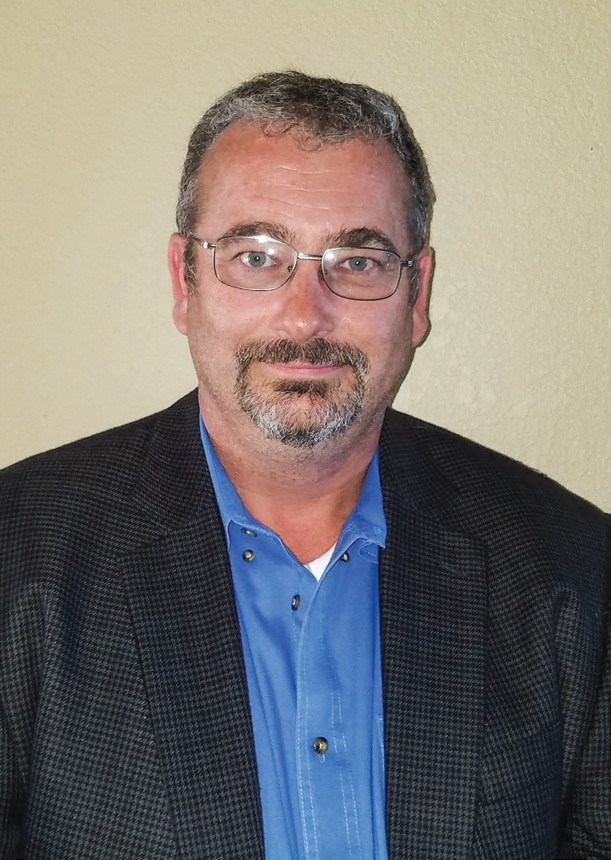
“Longevity and fitness for service are key for valves. When substandard valves are used, you have more potential for failure or you do not extract the true value of the valve over its lifetime. We keep spares and rebuild kits for larger, more specialized valves, but for smaller, more standard products, it is often cheaper to replace and recycle the old valve,” he said. “We continue to see more advancements in materials for the body and trim of the valve. Our projects are sometimes in harsh environments and meeting fluid service requirements can be problematic. When we can select materials which can last several years longer, that is a valuable feature for us.”
When asked about any particularly challenging maintenance jobs, Fred recounted that generally valves placed in difficult locations have been ongoing issues. “I have had a couple of occasions where the valve was placed in a very challenging location that was subject to significant pipe stress. The pipe was moving all around, mostly due to the thermal expansion, and the valve would actually get so much leverage applied to it that it would leak,” he explained. “For a flanged valve, distortion on the piping inevitably forces the flanges apart in a way that can cause leakage. After that much movement it becomes impossible to seal at the base of the flange and you end up having to cut the valve completely out of that location and move it to a place where it would not be exposed to that kind of stress.”
For Part Two of this article, check out the November issue of Valve World Americas.