By Sarah Bradley, Catarina Muia & Angelica Pajkovic
“Over our 70 year history, we have lived through many changes in the marketplace. One constant has been customers with applications where technology, design and performance are critical to the process. We have developed many products designed for these critical services; from the U.S. Navy, CERN (the European Organization for Nuclear Research), the ITER project in France – the world’s largest experimental fusion reactor – to many tough processes in oil & gas extraction, refining and petrochemicals, and mining,” said Tom Velan, Chairman of the Board. “We have been, and will continue to be, in cutting-edge technology areas while still serving the MRO replacement market.”
The company’s longevity has been attributed to their commitment to technology and innovation, while also recognizing the varied needs of their customers worldwide. Combined with the streamlined processes necessary to meet or exceed customers’ needs in a timely manner, Velan has positioned itself as a world leader in industrial valves.

Streamlining with Strategic Business Units
As the market began changing with a collapse in oil prices, the advent of Asian competition for commodity valves, and customers’ increased demand for short delivery schedules, Velan made the decision to implement a restructuring plan to significantly improve the way they did business that pivoted on five key strategic levers.
The first lever was a reorganization along five global business segments. Two were already operating as such, namely Velan’s France operations, focused on nuclear valves and highly specialized applications; and Velan ABV in Italy, focused on upstream oil and gas. The three others resulted from reorganizing the North American operations into MRO and Aftermarket, Severe Service, and Project Manufacturing business units.
The MRO and Aftermarket business unit, managed by Rob Velan, focuses on leveraging the installed base through Velan’s channel of global distributors. The Severe Service business unit, overseen by Duke Tran, focuses on highly engineered valves and solutions for severe industrial applications. Project Manufacturing maintains all project-based manufacturing, relying on fast turnaround for quoting, with a supply chain able to deliver under short lead times and respond to customers’ specific designs in RFQs.
Velan continues to embrace the innovative and entrepreneurial spirit that has been the cornerstone of the company’s management from the beginning, while improving and updating the systems in place. “The internal restructuring is helping to better align with customers’ needs. We value building long-term personal relationships with our distributors, customers and end users, but to complement that we are bringing a data approach to better serve customers,” said Shane Velan, Vice President, Transformation and Information Technology.
The second lever in Velan’s strategy is consolidation of the valve manufacturing facilities in Quebec, from three to two plants. The consolidation is scheduled for completion over the next few months. Current production has been gradually integrated into Velan’s other facilities, which are focused on the production of specific valve lines to improve delivery and supply chain efficiency.
To increase agility, the consolidated Montreal plant will focus on quarter-turn valve production including coker and metal-seated ball valves, mainly in support of the severe service business unit. The Granby, Quebec facility will be the company’s multi-turn center of excellence. Williston, Vermont will be the center for nuclear and Navy orders in North America, as well as specialized multi-turn manufacturing to support US customers. The new concentrations will allow the plants to be more efficient and reduce cycle times with increased focus and streamlining of processes.
The third lever is an integral part of the first two and aims to significantly improve manufacturing responsiveness and cycle times. This improvement will stem from relying more on outsourced non-strategic pre-machining of castings and forgings, keeping strategic machining in-house, and forming lean production cells; a move made easier by the decision to specialize the three remaining North American plants.
The fourth strategic lever will be transferring the remaining commodity valve production to their state-of-the-art facility in India, and other Asian manufacturing plants. The Coimbatore, India facility will become the center for forged gate, globe and check valves, including lower complexity project manufacturing. This will reduce Velan’s plant footprint, allowing the company to be more competitive and better serve the Middle East and Southeast Asia market in ways that were not previously feasible.
The fifth strategic lever is the continued modernization of Velan’s systems and processes. To improve on-time delivery performance, the company has for example invested in robust Valve Project Management (VPM) systems, and in configured pricing and costing systems. “Our ability to deliver more than 2,000 metal-seated ball valves, globe valves and other critical service valves, to a project in Asia in 2019, highlights the benefit of instilling VPM systems into our ever evolving practices,” added Duke Tran.

Expanding Severe Service Capabilities
Velan continues to grow its capabilities for severe service industrial applications that are highly abrasive, corrosive, and/or with high temperatures and high pressures. These products can require highly-tailored designs where quality is of the utmost importance.
‘Logic’ Control Panels
Velan continues to be the world’s largest supplier of critical valves to the delayed coker industry, including switching and isolation valves. It is crucial that each valve is operated correctly and in the proper sequence. “This is where the idea of the ‘Logic’ Control Panel came from,” said Duke Tran, General Manager, Severe Service Business Unit. “We created an entirely electronic control panel that links every critical valve within the delayed coker unit.”
Inside the Control Panel is Velan’s proprietary software controlling all critical valve operating sequences. Velan Control Panel hardware and software, working in unison, feature various safety mechanisms to prevent the operator from operating the wrong critical valve during a process switching sequence. “Typically, any major accidents that occur in delayed coker units are caused by human error and the control panel cuts down that possibility.”
Ebullated Bed Valves
“With 70 years of experience from various critical applications, we have taken proven valve design features and incorporated them into the ebullated bed valve line,” stated Tran. In 2019, Velan was awarded licenses to manufacture severe service ball valves for two world-leading ebullated bed processes. The resulting product has several features not presently seen in any other valve around the world. “For the first time we are designing a complete matrix of the product so that we can offer a size range from 1 inch all the way to 24 inches, with a pressure rating up to ANSI 4500. Although a stainless steel or graphite gasket is typically used in valve design, the ebullated bed process conditions require a gold-plated pressure-energized gasket. Due to both the corrosive nature and the high temperature of the process, gold is the ideal metal for sealing,” continued Tran.
The valves also meet all relevant licensor specifications and testing standards, including two API standards and one ISO standard for fi re-testing. Velan also developed new stem packing technology to meet the latest fugitive emission standards.
Additionally, Velan has developed unique technologies that will be integrated into the valve; patented cable drive actuators and a patent-pending 3D-printed thermal sleeve. “Unlike any other company, we have incorporated a cable drive pneumatic actuator to our valve while simultaneously accounting for the fact that the extreme process temperatures can cause a thermal shock that would split the valve’s body. Velan’s technology therefore provides a thermal barrier to defend against the risk,” explained Tran.
IIOT Solutions
In general, IIoT systems are used in critical service to monitor and control applications. Recently, interest in monitoring not only the application itself but the area and conditions surrounding the application has grown in the industrial sector. For Velan, this interest lies primarily in monitoring the condition of their valves. “We monitor the valve performance, the actuators and the processes that are going through both,” explained Tran. “This way we are able to tell the end user how everything is working, if there are any process changes, or if there is a hiccup within their system that they need to fix before it becomes a serious and costly issue. For Velan, IIoT is not just hype. We have been providing valve automation and monitoring since 1983. IIoT is an additional technology to enhance Velan’s unique Complete Valve Solution Ecosystem (CVSE). In the past we could only monitor either the valve and/or the process conditions locally and on-site. With IIoT, Velan can help our customers monitor their critical valves 24/7 live and from any location around the world. Based on our many decades of field experience, many of the very costly unscheduled shut-downs due to critical valve failure could have been prevented if live monitoring by valve experts were available. Today, IIoT provides our valve experts and the customers the ability to proactively monitor and intervene to prevent upset process conditions that often cause the valves to fail. Multi-million dollar losses due to unscheduled shutdowns are common in the industry. Velan’s IIoT solution, as part of our CVSE, will minimize the risk of unscheduled shutdowns, and opens up new possibilities in predictive and preventive maintenances to further increase operating profit margin to our end-users,” stated Tran.

VEL-8
As a result of 10 years of collaborative R&D, Velan has launched VEL-8, a patented coating technology applied between the ball and seats of a valve, specifically designed for improved service life in severe High Pressure Acid Leaching (HPAL) conditions. “Designing a valve is only half the story. For metal-seated ball valves, it is the coating that makes the valve work well,” Tran admits. “It is important to remember that each service requires a different coating to be used. We are a valve manufacturing company, but we do everything we can to make our product the best for our customers; this separates us from other companies.” In the mining industry for example, Velan has worked with the National Research Council of Canada and the University the Montreal to develop VEL-8, a coating specifically designed to increase service life in highly corrosive processes. For this reason, Velan continues to heavily invest in development of coating technology.
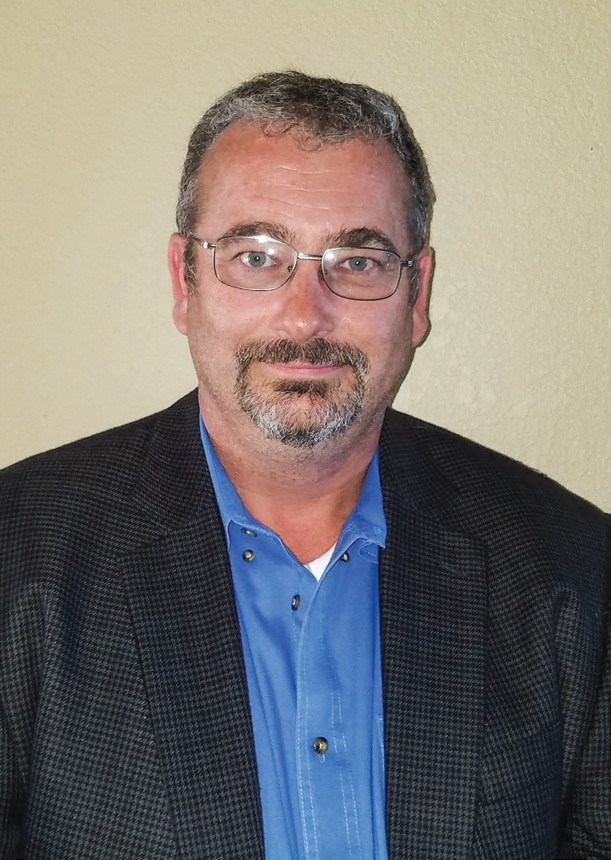
Transforming the Future
“The common denominator across all of the strategies we employ and the product we create is the focus of the end-user, while leveraging the strengths of Velan that we have always had. Namely the brand power, product quality and engineering depth,” said Yves Leduc, the CEO of the Company.
Today, Velan is more modernized in its ways of managing the business than it was just a few years ago. This has been an ongoing transformation to alter their plant footprint, restructure the businesses and plant organizations through consolidation and concentration of products, transfer of commodity products to more cost effective manufacturing, reducing lead times by reducing non-strategic machining and the continued modernization of all systems.
“As we enter an incredibly volatile and uncertain economy caused by COVID-19, we are thankful for the progress made in the last year, as the company is in many ways already transformed. The combination of all these actions has made the company lighter and more agile, much more resilient to great shocks, but above all, customers are already getting the benefits of a vastly improved business model designed for meeting their needs faster and better,” said Yves.
“The 70th anniversary coincides with the year we will have significantly redefined our business, readying it for the next decade. Velan is an enduring company because of our capacity to change and adapt, and all of our employees should be proud of that,” summarized Yves. “We have a strong global presence of manufacturing facilities and an excellent product reputation in terms of performance, quality and depth of engineering capabilities. We have a great brand that is the result of 70 years of hard work by many really dedicated and experienced people around the world,” concluded Tom.