Hydrogen is expected to play a significant part in the low-carbon future that lays ahead. When interacting with the production and handling of any fluid, valves are not only necessary but critical to successful operations. A valve design in a hydrogen application requires two types of materials; metallic materials when dealing with high pressure and cryogenic temperatures, and non-metallic materials for overall static and dynamic sealing and seating. Hydrogen however, poses a unique challenge for the materials selection for valves. Due to its small size, hydrogen can diffuse into metallic and non-metallic components and, once there, can interact in deleterious, and not-yet-understood, ways with the material’s internal structure. Read on to learn more about hydrogen and its related damage mechanisms in common valve materials.
By Davi Sampaio Correia, Technical Consultant
Why Hydrogen?
Hydrogen is the simplest, lightest, and most abundant element in the universe. As a replacement for fossil fuels, research has been focused on it for its associated use in fuel cells. Fuel cells are battery-like devices that, when fed with hydrogen, produce electricity with only water and heat as by-products. “The energy in 2.2 pounds (1 kilogram) of hydrogen gas is about the same as the energy in 1 gallon (6.2 pounds, 2.8 kilograms) of gasoline.”1 As there appears to be no shortage of hydrogen and its greenhouse emissions as a fuel are nil, it is easy to question what is preventing its widespread adoption. Two issues arise: production and safety.
Production Challenges
While there is hydrogen everywhere, it is not readily available in a useful form. In atomic, or even molecular form (H2, the fuel), it is highly reactive. That means that producing useful hydrogen requires a lot of energy; so much, that the amount used to generate H2 is more than what it will generate in a fuel cell afterwards. Broadly speaking, there are three methods to produce hydrogen natural gas reforming, coal gasification (both thermal processes), and electrolysis. It is common to see colors associated with them, related to the amount of greenhouse gases (GHGs) emissions generated. The major colors are green, gray, brown, and blue.
Brown – uses black (bituminous) or brown (lignite) coal as primary source of hydrogen. It generates the most GHGs.
Gray – uses natural gas as primary source and it is the most common form of hydrogen generation. It produces less GHGs than brown hydrogen.
Blue – When the carbon generated in thermal processes is captured and stored underground, the hydrogen thus produced is labelled blue.
Green – In green hydrogen no GHGs are generated, as it uses renewable sources as wind or solar to provide the required electricity for the electrolysis process (splitting water into hydrogen and oxygen).
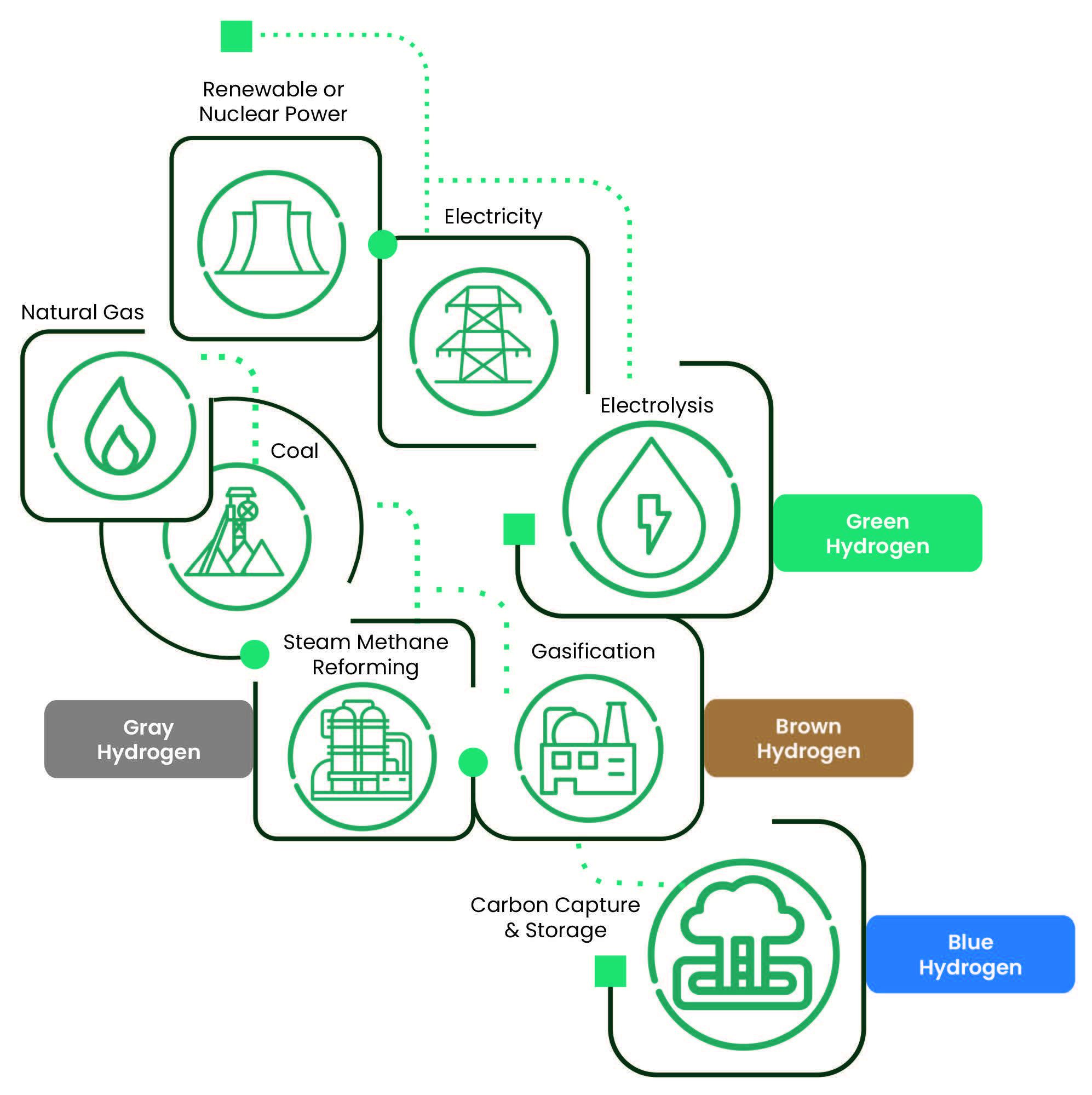
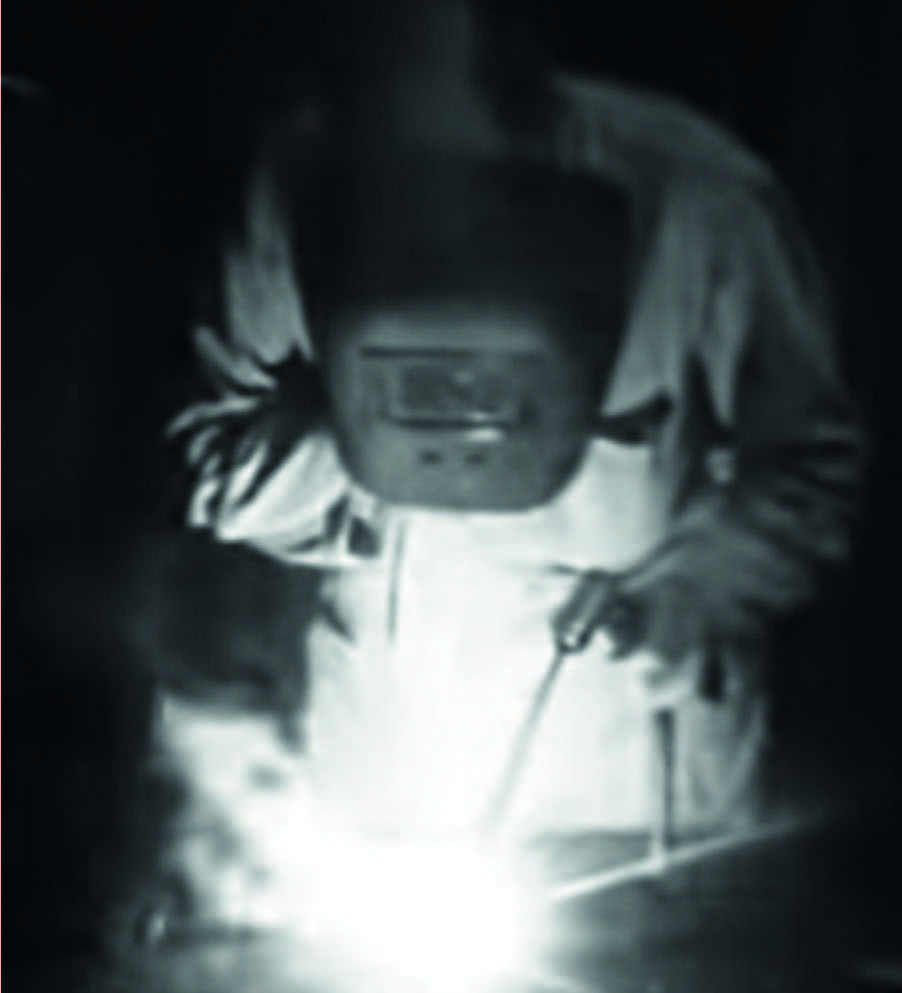
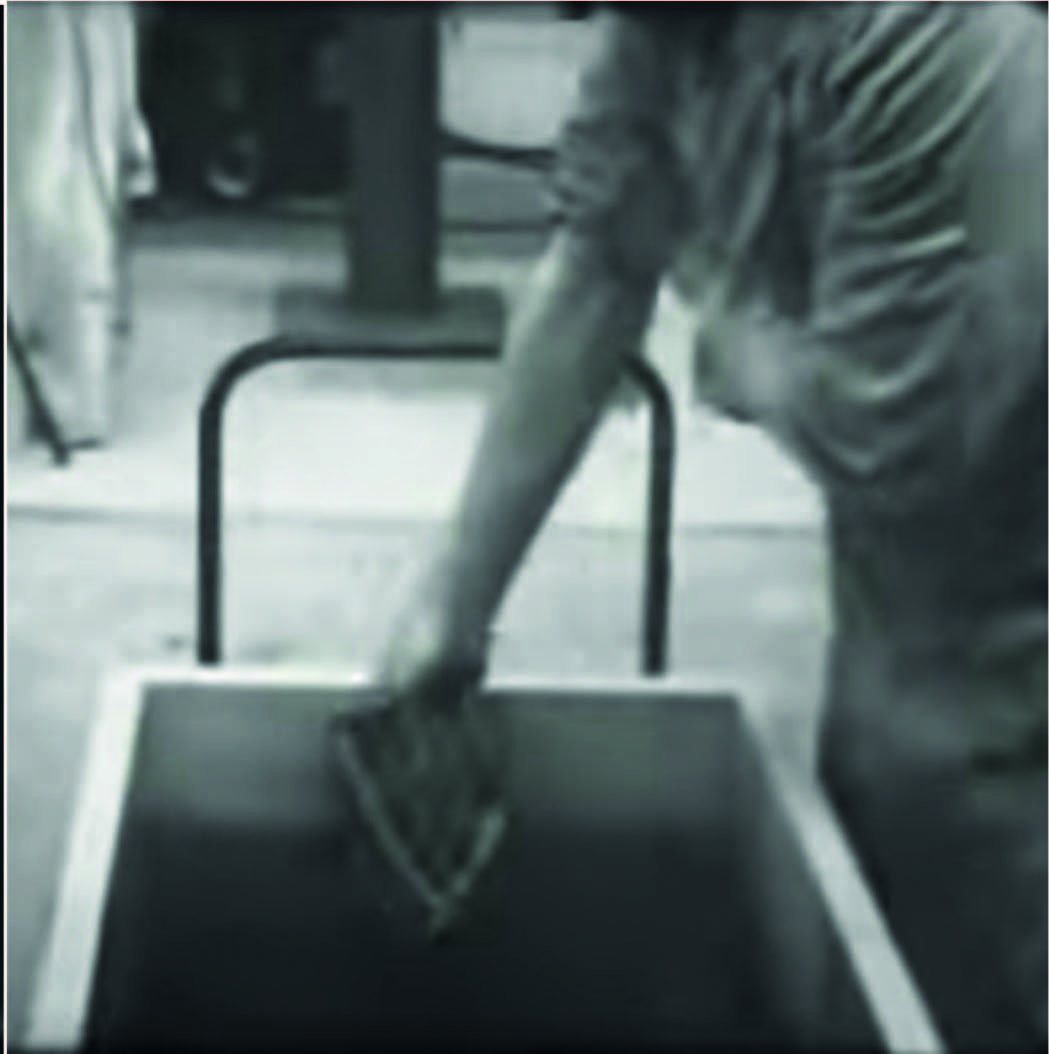

Safety Challenges
For over a century, hydrogen has been used in industrial applications. These have typically been secluded environments, where trained professionals are accustomed to dealing with hazardous
chemicals. Now, the industry is considering hydrogen for consumer use, such as fueling a car at a gas station. New procedures and technologies are needed to make hydrogen handling safe for the layperson.
“One of the major issues affecting the acceptance of hydrogen for public use is the safety of hydrogen installations (production and storage units) as well as its applications (i.e., as vehicle fuel or home use).”2 The hazards associated with the use of hydrogen can be characterized as physiological (frostbite and asphyxiation), chemical (burning or explosion), and physical (embrittlement and component failures). It is on this latter hazard that this article will focus on. Remember the statement that 1 kilogram of hydrogen gas has the equivalent energy of 1 gallon (2.8 kilograms) of gasoline? While this is true, there is a catch. The 2.8 kilograms of gasoline exist inside the car fuel tank at atmospheric pressure. Compacting enough hydrogen gas to reach 1 kilogram however, requires significantly higher pressure. Today, fuel tanks that are used to store hydrogen operate with 350 bar for buses (and other heavy duty applications), and 700 bar for light vehicles. Designing safe procedures and equipment to deal with hydrogen stored at such high pressures is therefore no easy task.
As the molecules is so small, hydrogen can migrate through materials and interact with them in ways that lead to unannounced, catastrophic failure. Figure 2 provides an indication of how much hydrogen can be accommodated in steels. If hydrogen can diffuse that easily into solid metals, they can also do so in polymers and elastomers. If left unchecked, the degradation mechanisms of both materials can cause failure
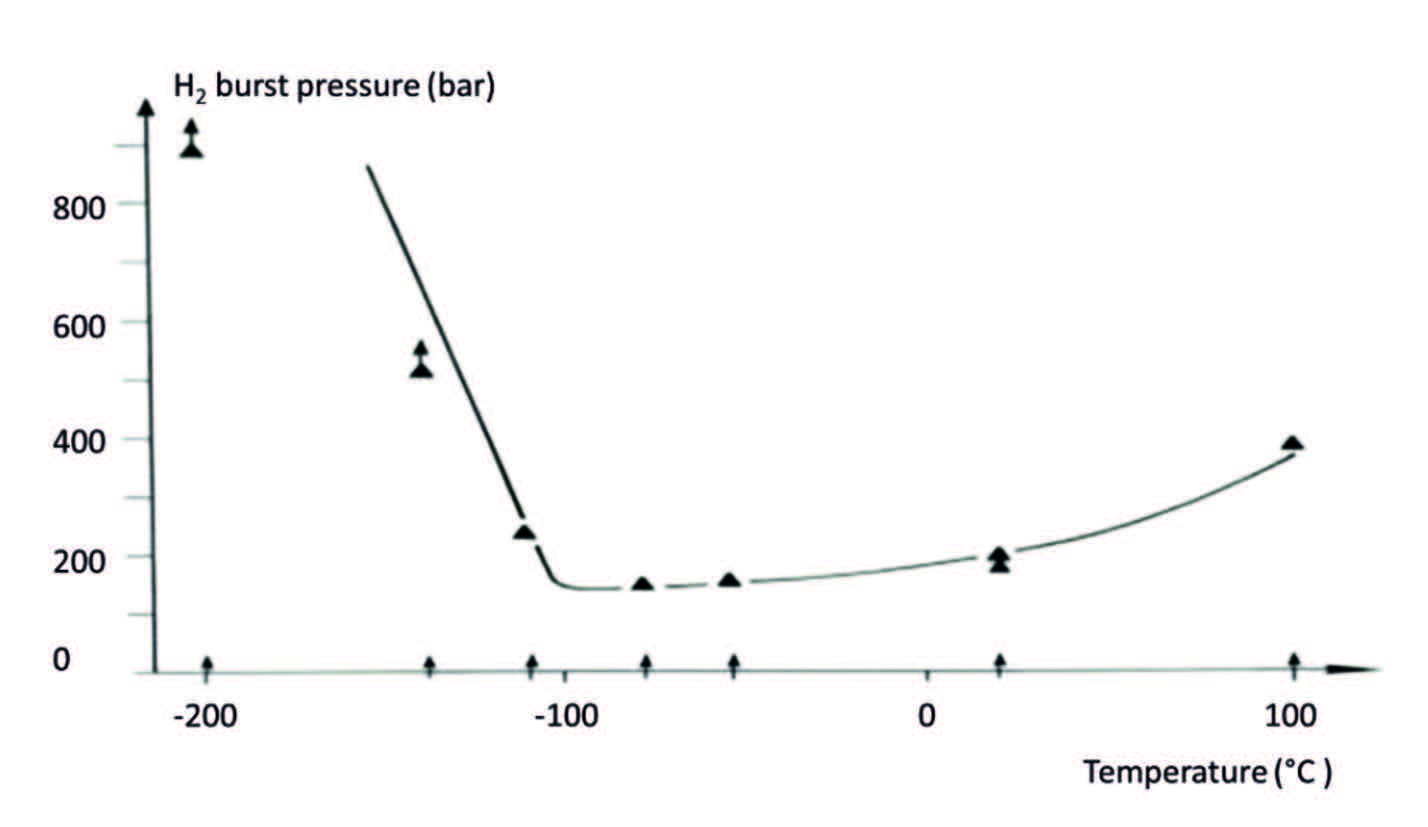
Hydrogen and Metallic Materials
When considering alloys for hydrogen service, a designer has to keep in mind that the “mechanical, environmental, and materials variables that generally contribute to hydrogen-assisted fracture are: loading mode (e.g. static vs cyclic stress), hydrogen gas pressure, temperature and material strength level.”4 The designer must also be particularly careful with extrapolations, as “mechanical properties measured for a low-strength steel in a low-pressure hydrogen gas should not be applied for exposure to high-pressure hydrogen gas or to same steel in a high strength condition.”4
Typically, whenever one thinks of potential issues that can arise with hydrogen and metals, hydrogen embrittlement comes to mind. The ASM handbook3 cautions us, however, that hydrogen embrittlement is just one type of hydrogen damage mechanism from a broader category of potential issues. When material failure is associated with reduced load carrying
capability or fracture below the yield strength, it is hydrogen embrittlement. Other failure modes associated with hydrogen damage include: cracking, blistering, hydride formation, and loss in tensile ductility.3
Ductility is a mechanical property related to a material’s amenability to deformation; that is, how much it can be plastically deformed without fracture. As temperature drops, metal alloys that are ductile, such as many carbon steels as well as ferritic and martensitic stainless steels, may become brittle. Materials such as copper, aluminum, nickel, and austenitic stainless steels however remain ductile even at cryogenic temperatures. The behavior for a specific alloy will depend on several factors including: crystalline structure, grain size, the propensity to absorb contaminants, and heat treatments.
When adding hydrogen to this low temperature environment, evidence suggests that hydrogen-assisted damage can be neglected below -150°C, at least for some of the commonly used austenitic steels for hydrogen storage (See figure 3). That leaves the designer with one less challenge; only the normal considerations of dealing with mechanical characteristics, expansion and contractions phenomena and the thermal conduction of the various materials.5
As the hydrogen supply-chain requires materials that can safely hold the element for production, transport, storage, and end use, hydrogen must be stored as either a compressed or a refrigerated liquefied gas. To store compressed gas, the storage tank must have a pressure capacity in the range of 5,000–10,000 psi (350-700 bar). For refrigerated liquefied gas, tanks need to be able to withstand temperatures below -252.8°C (-423,04°F or 20,35 K, the boiling point of hydrogen at one atmosphere pressure). Hydrogen affects these two conditions in different ways.
High-pressure gas storage at regular ambient temperatures is an entirely different situation. Here hydrogen-assisted failure is a very real possibility. Due to a lack of complete understanding of the mechanisms that lead to failure, hydrogen embrittlement remains the worst offender. Two of the most commonly held beliefs of what leads to embrittlement are: that hydrogen atoms diffuse through the metal and recombine into molecules with higher volume, increasing pressure from within the crystalline structure of the metal; or that hydrogen reacts with some constituent of the metal and forms brittle components more prone to initiate cracks (See Figure 4). In both cases, loss of ductility and crack initiation may lead to catastrophic failure.
There are general rules that can be followed regarding metallic alloys compatibility with hydrogen service. These rules include: prioritizing austenitic stainless steels, aluminum alloys, and copper alloys as well as avoiding nickel and titanium alloys. The most comprehensive, up-to-date guide on materials selection when dealing with hydrogen is the ‘Technical Reference
for Hydrogen Compatibility of Materials’, which provides a wealth of information on the advantages and disadvantages of the following alloys:7
• Plain Carbon Ferritic Steels
• Low-Alloy Ferritic Steels
• Quenched & Tempered Steels
• High-Alloy Ferritic Steels
• High-Strength Steels
• Ferritic Stainless Steels
• Duplex Stainless Steels
• Semi-Austenitic Stainless Steels
• Martensitic Stainless Steels
• Austenitic Steels
• Nitrogen-Strengthened Stainless Alloys
• Precipitation-Strengthened Stainless Alloys
• Specialty Alloys
• Aluminum Alloys
• Copper Alloys

Hydrogen and Non-Metallic Materials
Trying to reach zero-leakage rates in valves using only metallic materials is already hard enough; when dealing with an element as small as hydrogen, it is nearly impossible. Thus, polymers and elastomers are critical for valve design in sealing and seating applications. When selecting non-metallic materials for hydrogen service, the technician faces two additional challenges.
Variation on Mechanical and Chemical Properties
Bodies such as ASTM and ASME define composition, heat treatment, and properties for metal alloys with very stringent rules. Polymers and elastomers, on the other hand, do not have yet the same degree of standardization. For the same polymer grade, properties on finished
pieces may differ due to additives or due to the manner that the chips or pellets of the original polymer were processed into the manufactured part.
Understanding of Degradation Mechanisms
The detrimental effect of hydrogen in steels was first reported in 1875.8 From then on, a steady stream of research has been done on the subject which has led to a robust body of knowledge on what works and what does not when dealing with hydrogen. Sadly, non-metallic materials
are not in the same position. There continues to be a significant amount of research required on the degradation mechanisms, physical stability, permeation properties, friction and wear, fracture, fatigue, and rapid cycling effects on non-metallic materials.
While the SANDIA report7 contributes to closing the knowledge gap for nonmetallic materials, it does so by limiting itself to data on gas permeation. In other words, it simply provides a summary of hydrogen transport data in common polymer materials. The reason for the limited scope is as follows: “We are unaware of hydrogen compatibility studies for common polymer materials that might be expected in gaseous hydrogen service, thus we have eliminated the sections on mechanical properties and microstructural considerations.”7
This lack of knowledge drives many conservative maintenance procedures, such as replacing valves and hoses on a fixed schedule for lack of inspection tools or ability to predict future performance. For valves and other equipment, it is also important to mention that non-metallic materials also include lubricants and other fluids that might be involved in operation
or maintenance. They too require assessment regarding compatibility with hydrogen service.
Conclusion
Countries around the world have pledged to reach net-zero emissions by 2050. Hydrogen is a critical part of this goal, due to its abundance and clean-burning characteristics. However, integrating hydrogen safely in the energy matrix will require further research into materials, as there are still doubts about potential incompatibility, especially for polymers in high pressure applications.
REFERENCES
1. https://afdc.energy.gov/fuels/hydrogen_basics.html
2. Ram B. Gupta, Hydrogen Fuel: Production, Transport, and Storage, 1st Edition, CRC Press, 624 pages.
3. Stephen D. Cramer and Bernard S. Covino, Jr. (Editors), ASM Handbook Volume 13A: Corrosion: Fundamentals,
Testing, and Protection, 1135 pages, 2003, ASM International, ISBN: 978-0-87170-705-5
4. SANDIA, Technical Reference for Hydrogen Compatibility of Materials, SANDIA report SAND2012-7321, available
at https://www.sandia.gov/matlsTechRef/chapters/SAND2012_7321.pdf
5. Barthélémy, H., Hydrogen Storage – Recent Improvements and Industrial Prospectives, annals of the ICHS 2013
SEPTEMBER 9-11, 2013 – Brussels – Belgium, INTERNATIONAL CONFERENCE ON HYDROGEN SAFETY, available at
http://www.ichs2013.com/images/papers/132.pdf
6. Wei Zhang, Evaluation of Susceptibility to Hydrogen Embrittlement—A Rising Step Load Testing Method, January
2016, Materials Sciences and Applications 07(08):389-395, DOI:10.4236/msa.2016.78035
7. SANDIA, Technical Reference for Hydrogen Compatibility of Materials, SANDIA report SAND2012-7321, available
at https://www.sandia.gov/matlsTechRef/chapters/SAND2012_7321.pdf
8. Amit Khare et al, A Review on Failures of Industrial Components due to Hydrogen Embrittlement & Techniques for
Damage Prevention, International Journal of Applied Engineering Research ISSN 0973-4562 Volume 12, Number 8
(2017) pp. 1784-1792
About the Author
Davi Correia is a Senior Mechanical Engineer who has worked at a major Brazil-based oil company for the last 15 years. Correia is part of multi-disciplinary team that provides technical support for topside piping and equipment of production platforms. During this period, he began to work with materials and corrosion, and later moved to piping and accessories technology,
where he has become one of the lead technical advisors on valve issues. Correia was part of the task force that revised the IOGP S-562 standard, and wrote the S-611 standard. Correia has a master’s and a doctor’s degree in welding by the Universidade Federal de Uberlandia.