Valve World Americas had the pleasure of speaking with Mike Dunn, JS Machine and Valve, to discuss his experiences and insights into the field of HF valve service and repair, and his advice for those looking to enter this dynamic and challenging industry.
By Foster Voelker II, Director of Engineering – Williams Valves
Q: What are the biggest challenges for valves and other equipment in HF applications?
A: When dealing with valves in hydrofluoric acid (HF) service, safety is of paramount importance. Hydrofluoric acid is a highly corrosive and toxic substance that can cause severe chemical burns and pose a significant risk to human health.
To ensure safety, it is essential to carefully plan and take necessary precautions before working on equipment that may have been in contact with hydrofluoric acid. This includes using appropriate personal protective equipment (PPE), such as approved gloves, jackets, pants, face shields, goggles, and respirators with HF-approved filters, to prevent exposure to the acid. Additionally, it is important to have proper training and follow established procedures to minimize the risk of injury or contamination.
When it comes to valves that have been in HF service, the risk of contamination and exposure can persist if the valve was not properly decontaminated, even after the acid has been drained and the valve dipped in a neutralization. It is therefore recommended to break down the valves into their smallest components and remove all seal materials, such as packing and gaskets, to ensure that no residual acid is left behind. This can help prevent accidental exposure or contamination during transport or repair
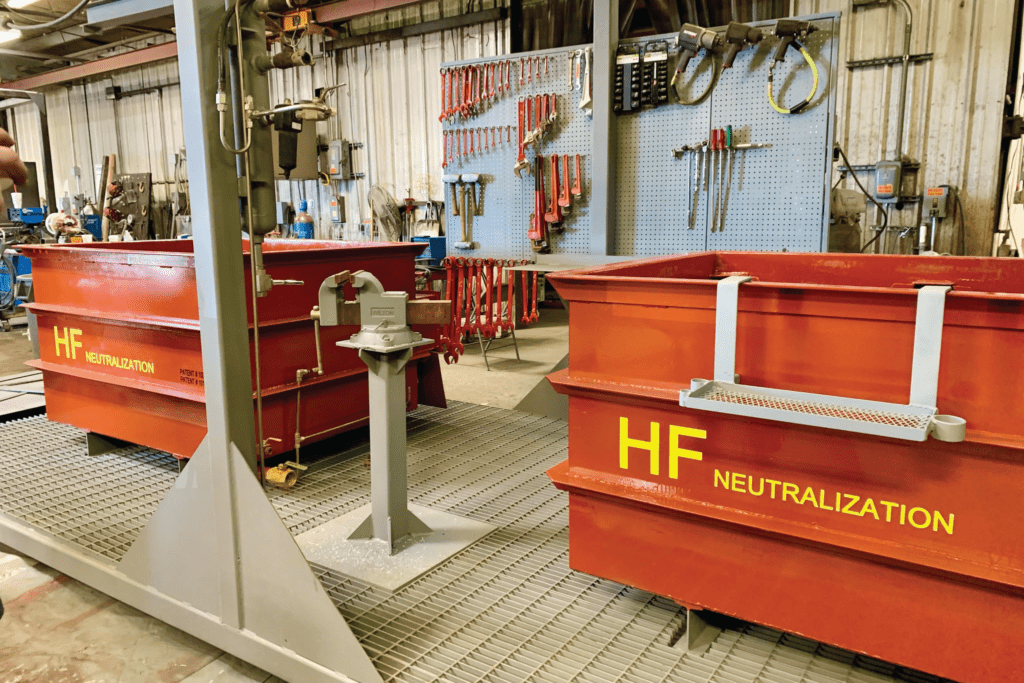
Q: Are there specific process conditions that impact these challenges?
A: The process conditions that valves in hydrofluoric acid (HF) service are exposed to can vary greatly depending on the concentration of the acid in the process stream. For instance, valves that handle 100% concentrated HF will be exposed to much more severe conditions than those that only handle trace amounts of the acid.
In recognition of this fact, organizations such as UOP have established different classifications for valves based on the level of HF exposure. These classifications help to ensure that valves are appropriately designed and specified for the specific process conditions they will be exposed to. Material selection, for example, is critical when it comes to ensuring that valves can withstand the corrosive effects of HF. Valves that will be exposed to higher concentrations of HF may require more specialized materials, such as Monel, while those that handle lower concentrations of HF may be able to use more standard materials such as carbon steel.
Q: What are the industry specifications or resources available that provide guidance on HF?
A: Currently, during the repair of HF valves, our organization adheres to a stringent set of industry standards including UOP Specifications, API RP 751, and API RP 621. Among these, API RP 751 serves as a valuable resource as it provides comprehensive guidance on the procurement of materials for use in Alky units, as well as general safety protocols and minimum equipment owner requirements for neutralization prior to valve off-site transportation. Additionally, API RP 751 offers direction on critical aspects of valve repair such as welding, hardness, and PWHT (if deemed necessary) for materials such as Low RE Carbon Steel, M35-1, and Alloy C276. Due to the corrosive nature of HF, specific regulations have been instituted for Carbon Steels, and the standards outlined in API RP 751 specify allowable residual elements and their corresponding concentration levels. It is also essential to conduct non-destructive examinations, such as PMI, on valves intended for HF service to ensure optimal performance and safety.

Q: What are the most common modes of failure?
A: The answer to this question depends on the type of valve. In plug valves leakage that occurs on the top cap, particularly on the bonnet around the stem area, is most common. If plug valves are not moved or broken off the seat periodically there is a tendency for the sleeve to turn into the flow path.
On gate and globe valves the most common areas of failure come from packing leaks, as well as corrosion and the build-up of fluorides on the mating surfaces like wedge guides. For check valves, one of the major problems that has been seen is the external hinge pin. Most manufacturers now make checks incorporating internal hinge pins, but if an external hinge pin is used it is recommended to seal weld the plugs before installation. Another major problem in HF is that people use the wrong material in the wrong process. For example, stain less steel is prohibited in HF processes. Having something with stainless in high concentrations of HF is a disaster.

Q: What does the future of HF look like?
It has been proposed that UOP will adopt ISO ALKY Process Technology as part of its ongoing efforts to optimize systems.
Future of HF:
According to Honeywell UOP, “The ISO- ALKY process solution offers refiners the ability to produce alkylate using a specialized ionic liquid catalyst that simplifies handling procedures and provides comparable process and economic performance to conventional liquid or solid acid catalysts. The technology is backed by 80 years of innovation in alkylation by Honeywell UOP and an alliance with one of the world’s leading integrated energy companies, as well as a successful startup and operation at design rate and octane for the first commercial size ISOALKY unit.1” The Chevron Corporation and Honeywell commissioned the world’s first commercial-scale ISOALKY process unit that uses ionic liquids to produce alkylate in 2021. The new catalytic process uses a non-aqueous liquid salt or ionic liquid to produce a valuable high-octane blending component that helps lower the environmental impact of gasoline. This technology can be used in new refineries or existing facilities under- going expansion or retrofit applications. It has wider and improved feed flexibility compared to conventional alkylation technologies and eliminates the need for offsite regeneration and polymer by-product handling.2 Chevron has already started shutting down most of their HF units to move to this new technology.
The future of HF service seems to center around the advancement and implementation of new technologies and procedures to enhance safety and efficiency in handling hydrofluoric acid, such as the ISOALKY process. However, given the extent of current systems in place, it is probable that HF service will entail a blend of new technologies and ongoing compliance with established safety protocols to guarantee the secure and efficient handling of hydrofluoric acid.
References
- https://uop.honeywell.com/en/industry-solutions/ refi ning/gasoline/alkylation
- https://www.chevron.com/newsroom/2021/q2/ chevron-and-honeywell-announce-start-up-of-isoalky-ionic-liquids-alkylation-unit
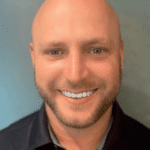
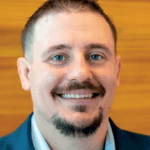