Hydrogen is the most abundant element in the world. It is produced through different channels, such as coal, alkane dehydrogenation and natural gas. Each year, the world produces roughly 70 million tonnes of hydrogen. Almost 50% is used for ammonia synthesis, 15% for methanol production, and 35% for refining.
The transition to a lower carbon energy system will rapidly lead to a fundamental restructuring and reshaping of the global energy system. There is a significant shift away from traditional hydrocarbons (oil, natural gas, and coal) towards non-fossil fuels, led by renewable energy, such as hydrogen energy. Generally, there are two hydrogen services: hydrogen gas and hydrogen liquid.
By Gobind N. Khiani, Fellow – Piping/Pipelines – Consultant
Technical Challenges in the Hydrogen Economy
The transition to a hydrogen economy towards decarbonization of energy consumption has technical challenges that need to be addressed. Some of the most prevalent challenges include:
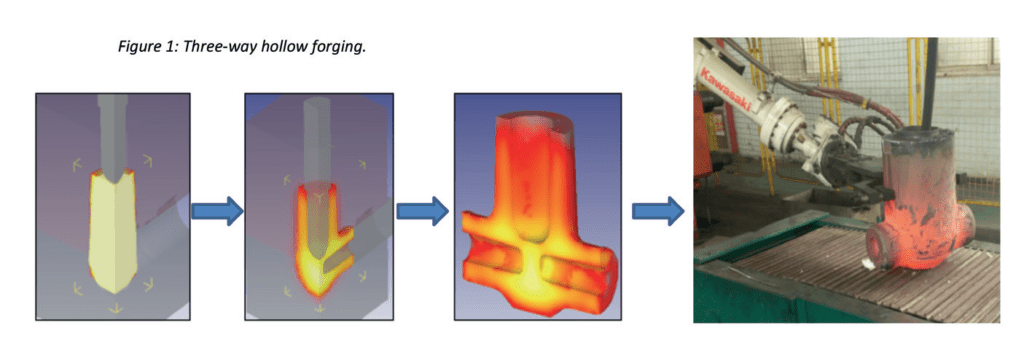
Decarbonized Hydrogen Production
Some clients use natural gas as the feed stock to produce hydrogen. To accomplish this steam methane reforming is used. This process produces a large quantity of CO2 as a by-product. Other processes such as auto-thermal reforming and pyrolysis are being developed to reduce the volume of CO2 that is generated during hydrogen production.
CO2 Transportation and Storage
As steam methane reforming produces CO2 as a by-product, carbon capture, use and storage (CCUS) is necessary to support the transition to hydrogen.
Hydrogen Storage
A hydrogen transportation and distribution network is required to carry out some form of temporary storage. This will ensure an uninterrupted supply to hydrogen. Underground storage may be able to safely store large quantities of hydrogen.

Hydrogen End-Use
Heavy industry consumes 80% of the world’s natural gas, making it viable for a conversion to the use of hydrogen. Converting to hydrogen powered vehicles and converting residential and commercial end users to hydrogen for heat would contribute significantly to decarbonizing the energy system.
Hydrogen Export
Many industries are already supplying decarbonized hydrogen for use in various applications. It is currently exported in various forms including compressed or liquefied hydrogen, or as other products such as methanol or ammonia.
Safe Transportation of Hydrogen
The enormous cost and time required to design and build a hydrogen pipeline is not currently viable. Validating existing systems could, however, be a lowercost solution for current systems. Most industries are looking at hydrogen as a low-carbon energy carrier alternative to emissions-intensive energy sources of conventional oil & gas. This change could have a direct impact on legacy pipelines in terms of the material performance of the steels, as hydrogen can:
- diffuse into the steel and welds used in legacy pipelines,
- cause material embrittlement,
- permeate the material resulting in leaks.
As a result, catastrophic failure may occur when the pipeline is under highpressure conditions. In these cases, it is likely beneficial to perform a retrofit of current pipelines by applying internal coatings in-situ in a cost-effective manner avoiding the need to dig up or remove the existing legacy pipeline. Coatings can become an efficient and cost-effective means of transitioning existing pipelines for the transportation of hydrogen.
Extended testing is also required to fully understand coating resistance to hydrogen under representative operating conditions.
A further detailed evaluation of existing coatings and approaches for assessing coating performance is therefore required.
Further, the testing should be carried out to evaluate:
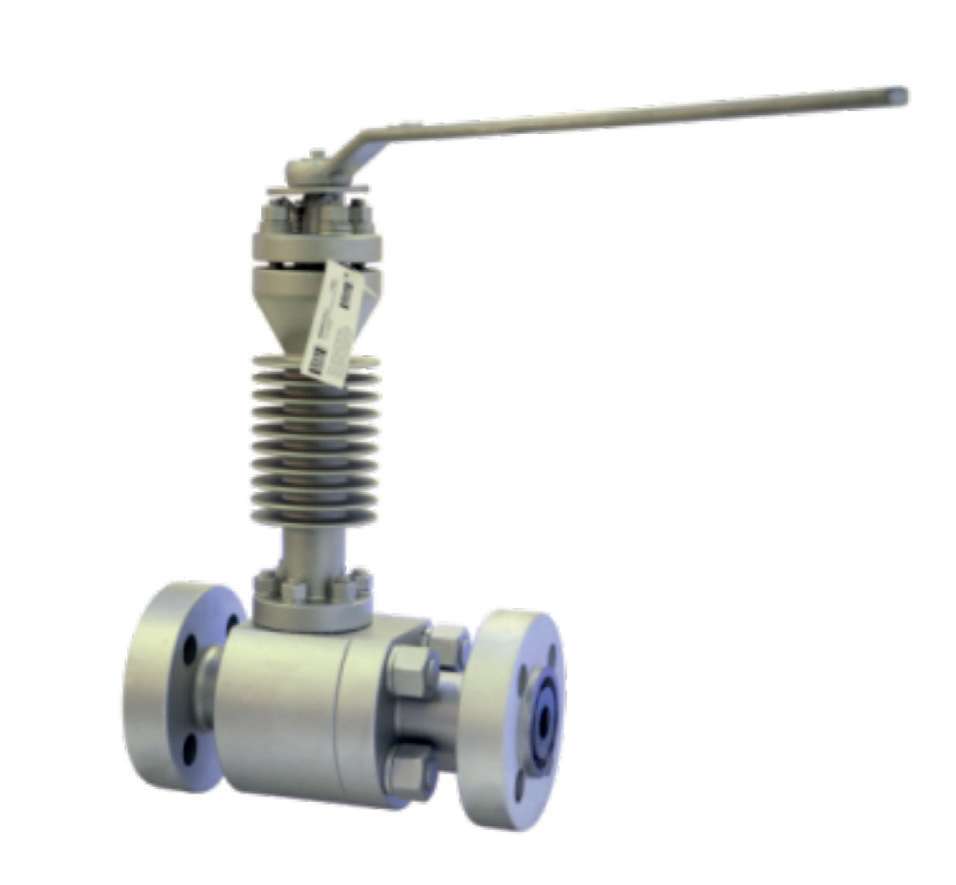

- The hydrogen permeation results of several small-scale plates with different coating types and thicknesses. It should also be evaluated at different gas pressures in a 100% hydrogen environment.
- Hydrogen permeation data for all coatings.
- A comparison of small-scale plate permeation testing to full-scale pipe hydrogen permeation under different test pressures. Review of test results of different thicknesses.
- An assessment of the effect of coating type and thickness on pipe performance because of hydrogen diffusion.
- Recommendations for additional work.
Hydrogen Gas Service Characteristics
-
- Gas phase or mixed phases, small atom,
- High temp. and pressure,
- H2/H2S environment (hydrogen embrittlement & corrosion),
- Flammable and explosive,
- Hydrogen bubbling and cracking.
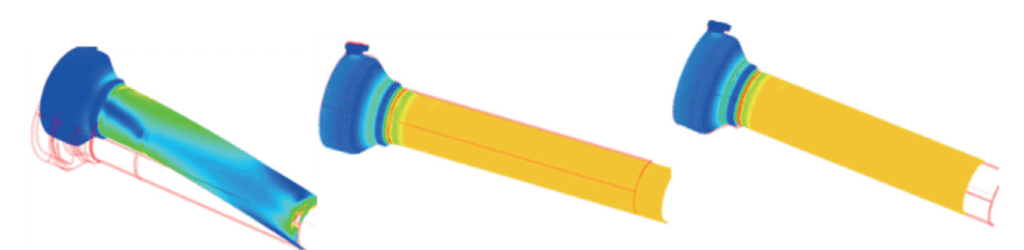
Valve Solutions for Hydrogen Services
There are several solutions currently offered by manufacturers for valves in hydrogen services. These include:
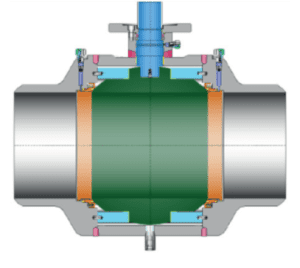
- Fugitive emission design,
- Pressure seal bonnet for high-pressure class,
- Live load nut of packing seal,
- All internal passage sharp edges rounded,
- Avoid threaded structure for internal parts,
- Special control of material composition and forming technology.
For general gas service, such as shrinkage holes, use casting material to avoid cracks and other defects of pressure-bearing parts. For high-temperature or high-pressure gas service, use raw material with AOD/VOD. The preferred forging type is the type with grain size 5 (CS, AS) or 7 (SS) size ASTM E112.
A ball valve used in the refining industry is typically a forged bolted metal seated ball valve. They are ideal for hydrocracking units which contain H2 gas along with HT&HP. These valves require good sealing performance and reliable operation.
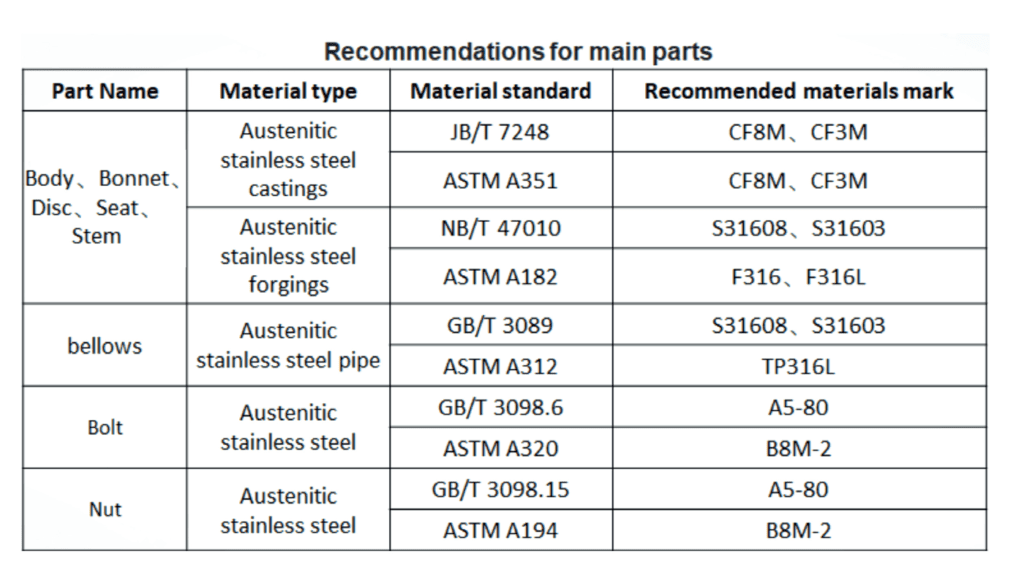
For long-distance pipeline transportation of mixed H2 gas service, fully welded ball valves are also common and should be designed with adequate strength and toughness. In addition to service fluids pressure, valves need to withstand the ground load. In frigid and frozen zones, the low-temperature impact toughness of material should be considered to avoid brittle fractures; these are typically caused by axial tension and pressure led by temperature fluctuations, external loads caused by landslides, ground subsidence, and flooding. For fully welded ball valves, welding line and heat-affected zone (HAZ), and crack tip opening displacement (CTOD) should be taken into consideration.
It is important to note that the failure location is not in the ball valve but the pipeline. The best way to validate the location is by using software simulation analysis.
External Load Safety Assessments (Anti-Bending, Tensile, Compression)
When the valves are closed, two seats can block the fluids from both sides. Fluid pressure relief can be accessible through a relief valve whose relief hole functions for in-line seal service. Meanwhile, a blow-out valve is equipped at the bottom of the body for regularly exhausting debris and contaminant. Precautions should be taken to avoid the adverse influence of debris on the sealing. If leakage occurs, emergency sealing solutions should be offered.
Liquid hydrogen is formed by cooling hydrogen to – 253℃ for liquefaction, the density of which can reach 780 times that of ordinary hydrogen, and the storage capacity of the same volume is 8-10 times that of gaseous hydrogen (under different pressures). The main pressure range of cryogenic liquid hydrogen valve is low pressure, generally less than 4MPa. Hydrogen storage has therefore become a challenge to be solved.
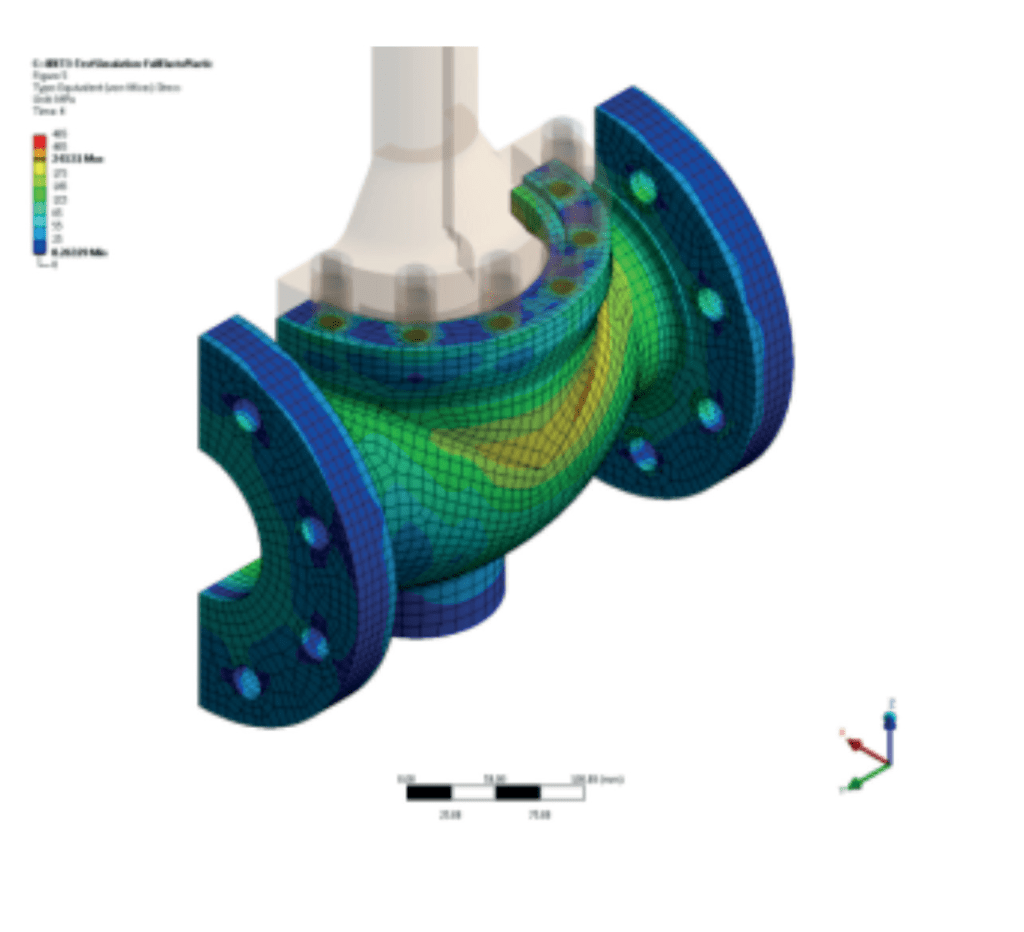
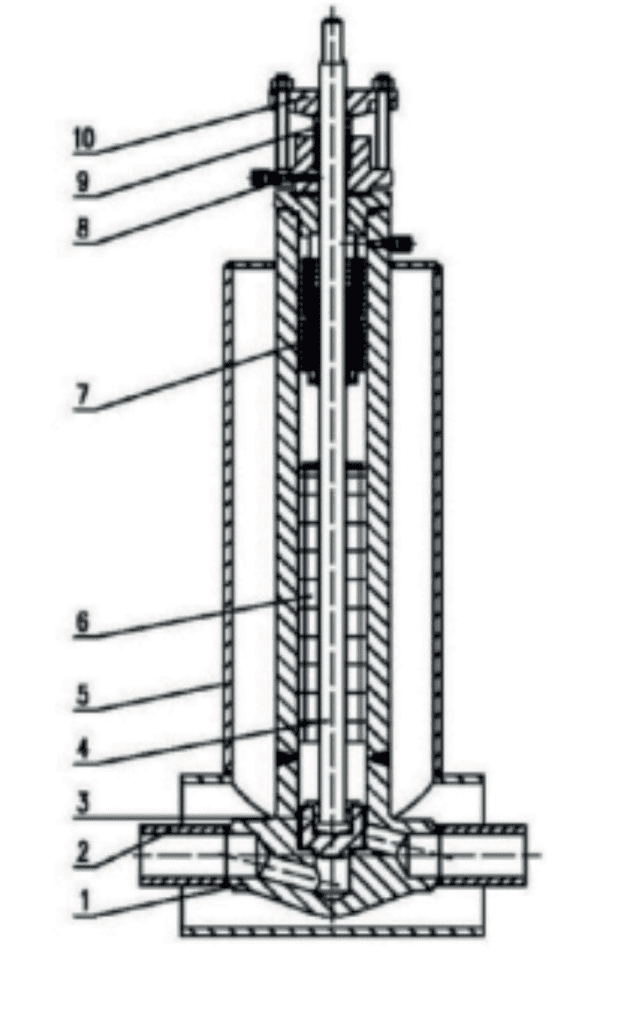
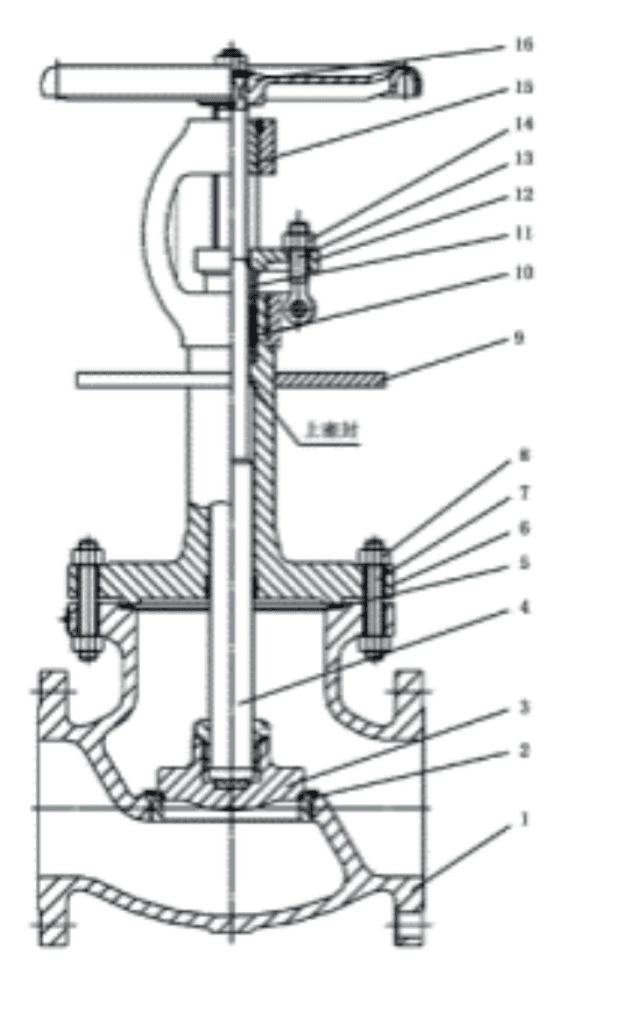
Liquid Hydrogen Pipeline Materials Shall Meet the Following Requirements:
- For metal materials in contact with hydrogen, special attention shall be paid to hydrogen embrittlement and hydrogen accelerated fatigue;
- The non-metallic materials in contact with hydrogen shall have good compatibility, and the applicability of the materials under hydrogen conditions shall be verified;
- Influence of temperature change, material performance change under ultralow temperature conditions;
- Permeation rate of hydrogen atom shall be known;
- The mechanical stability, strength, and service life of non-metallic materials shall be maintained within the full working conditions and life cycle due to the impact of hydrogen degradation.
- Valve metallic materials with special control of Cr、S、P and other elements, also higher mechanical properties than standard such as ASTM A182 & A351 for liquid hydrogen service;
- Ferrite content: no more than 3% for forgings, pipes and bars, and no more than 8% for castings;
- Cryogenic treatment: no less than 2 times for parts in liquid hydrogen medium;
- Welding process qualification and special selection of welding materials.
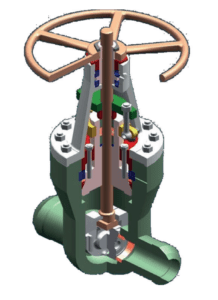
Additional Technical Requirements for Liquid Hydrogen Valves
- Globe valve or ball valve should be used for hydrogen pipelines;
- Liquid hydrogen should be prevented from remaining in the valve core when the ball valve is closed;
- Globe valve shall be installed in the liquid hydrogen return line as close to the container as possible, and there shall be no other accessories between them;
- All additional valves shall be degreased and dried before assembly;
- The valve shall be designed with an anti-static structure (4 Ω max), and fire-safe design if needed;
- Shell test of the valve shall be able to reach 4 times the maximum allowable working pressure without leakage for 1 minute.
- The minimum fatigue life of bellow shall not be less than 10,000 times, and the corrugated pipe material shall be 316 L;
- For valves with vacuum jacket structure, the valve shall be body extended. For gas insulation, the valve shall be bonnet extended;
- The valves installed on mobile equipment such as tank cars shall undergo vibration and impact resistance tests;
- Prototype testing at the available qualified institute shall be done to make sure the valve meets the operation performance at super low temperature;
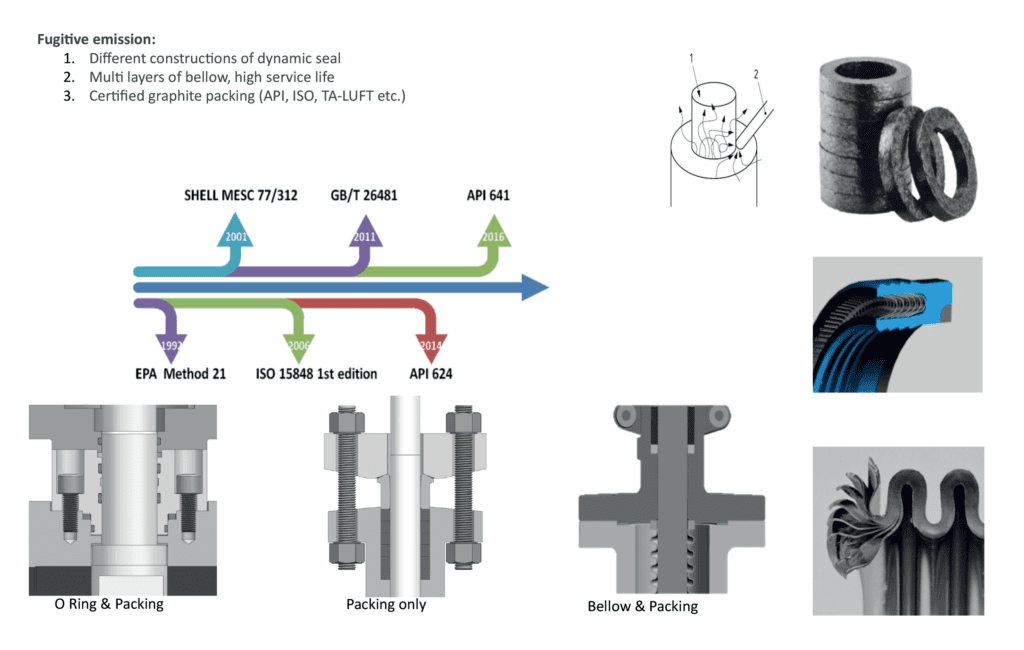
Final Thoughts
To date, both gaseous and liquid hydrogen valves are widely applied in the hydrogen energy industry and traditional oil & gas industry. The focus on these specialty valves is continually developing along with the global incentive to use clean energy for the environment. Safety comes first and all industries should take every precaution in hydrogen service possible. Currently, API is developing code named API6Z for Hydrogen Valves.
REFERENCE 1. Courtesy/Contribution: CFER Technologies Inc and Neway Valves Ltd
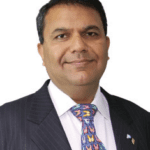