To meet the net zero targets and the contribution from hydrogen, valve sales will likely average $4 billion per year, over the next 10 years, and $6.3 billion over the next 30 years.(1) This includes the valves needed for hydrogen use, production, transport, storage as well as for carbon capture and sequestration.
Annual valve purchases over the next 30 years will be substantially greater than over the next 10 years. In the 2030-2050 period, purchases of valves for hydrogen use will average nearly twice that of the first 10 years.
By Robert McIlvaine, President & Founder – The McIlvaine Company
Although carbon capture and sequestration will be relatively small in terms of gas volume, there are many valves used in the processes of CO2 absorption, separation, liquefaction and transport to the final storage site. As hydrogen is the lightest of the gases there are many transportation and storage challenges. The transportation and storage of the gas therefore includes liquefaction, while its production includes steam methane reformation, use of electrolytic technologies, and other methods.
Converting to Hydrogen
Today hydrogen is used as a dominant fuel source for a number of power generating plants, such as the Fusina hydrogen power station in Italy (100% hydrogen), a petrochemical plant in Daesan, South Korea (95% hydrogen), a steel mill in Wuhan, China (60% hydrogen), and several planned facilities converting to 100% hydrogen such as the Magnum plant in Vattenfall, Netherlands, and the Intermountain Power Agency plant in Utah.2
Alterations are needed in the fuel handling systems, valves and piping, and combustor hardware. These alterations are needed to address several issues of concern, including pollutant emissions, operability, and cost. These issues are highly interdependent.
Industrial Uses of Hydrogen
As it stands the biggest user of hydrogen will be power generation. Power plants use hydrogen as a substitution for natural gas in combustion turbines and for the replacement of some portion of the solid fuel in coal fired boilers. Although transporting hydrogen as ammonia cuts transportation and storage costs, it does increase investment needed for valves, when it is used in power plants.
Other industrial uses include chemical and refining applications as well as steel and cement plants which substitute hydrogen for fossil fuels to melt metals and calcine limestone. Some hydrogen is also fed into the natural gas pipelines, and is being used for large truck, ship and rail power in place of oil and gas, see Figure 2. No potential use in passenger vehicles is included in this total.
Presently fossil fuels account for the majority of the electricity generation. Renewable capacity is about 60% of fossil capacity but since production is intermittent the actual yearly generation in TWH is relatively small.
The use of hydrogen will therefore require a relatively small investment compared to the production, transportation/storage and carbon capture and sequestration.
Valves Used to Achieve Net Zero
The Energy Information Administration (IEA) analysis of meeting net zero carbon emissions by 2050 requires 1,800 GW of hydrogen fired capacity.
Assuming therefore that more than 50% of hydrogen is used in retrofitted coal and gas turbine plants, the total capital cost to retrofit these applications would be $1.8 trillion. The average yearly expenditure would be USD $60 billion, and valve costs would be around USD $300 million per year.
Valves are required in fuel cell systems to supply the gaseous hydrogen at the inlet side, and to purge the condensate at the outlet side of the device. According to the initial pressure of the gas, the pressure will be reduced substantially.
Typically, two types of valves are embedded. Frist, the system needs on/off valves to drain condensate, to shut off the tank, and to shut off the entire system. The second valve required is a proportional valve, which is required to dose the flow rate of gaseous fuel to the stack‘s inlet. Depending on the actual power demand, the gaseous fuel flow will be controlled through a highly dynamical proportional behavior.
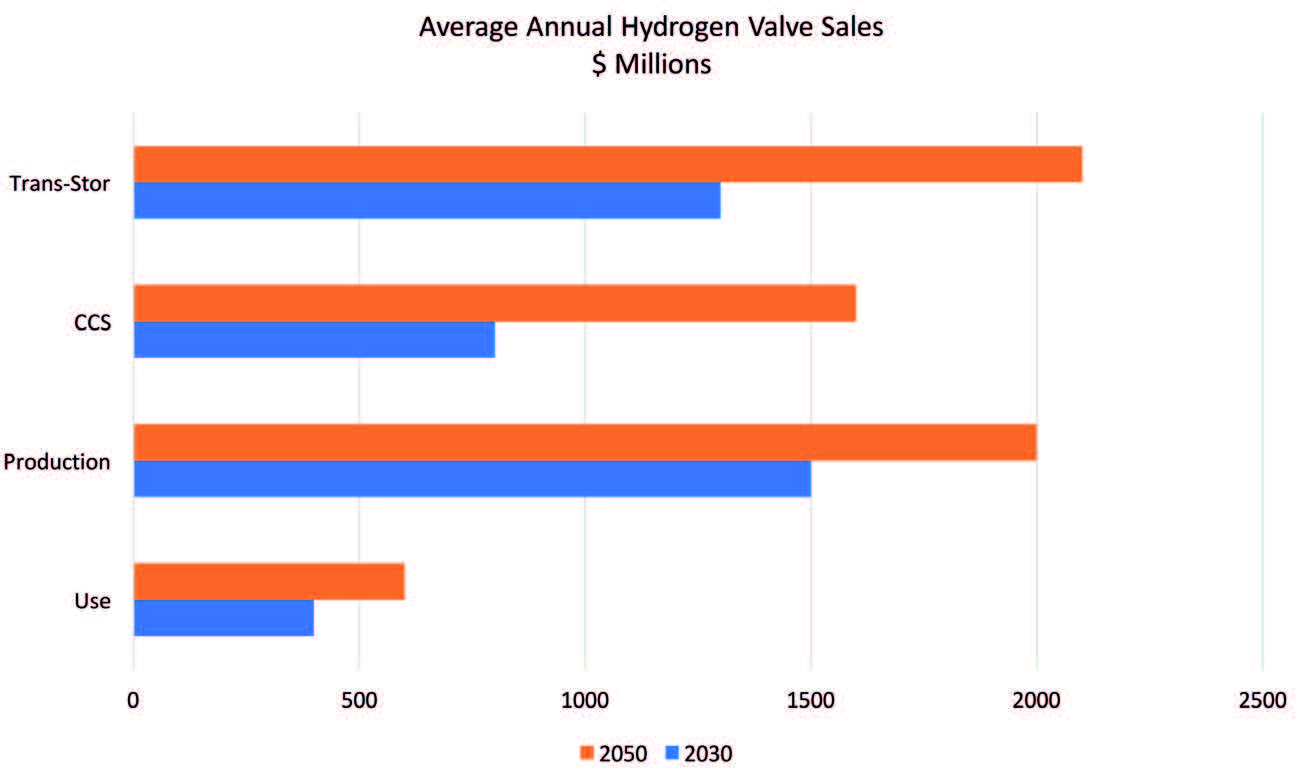
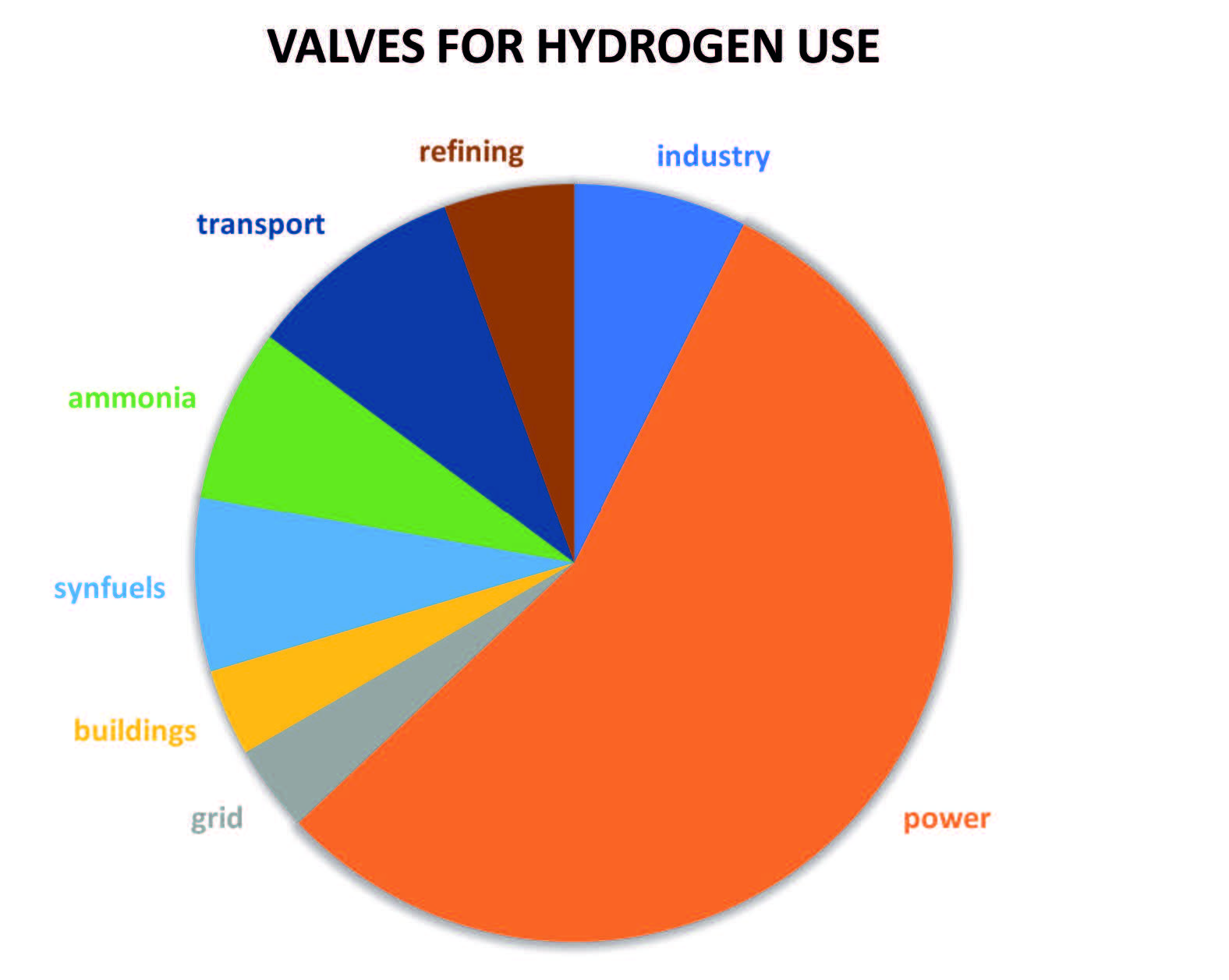
Current Projects
The use of hydrogen may require the addition of a selective catalytic reduction system. Valves will be required for the ammonia reagent injection ahead of the catalyst. In general, the volumes may be higher and the challenges greater for valves in hydrogen fuel and combustion services.
Emerson points out that it’s Fisher Control valves are a solution for a wide range of process industry applications, providing users with high performance and reliability. Including large temperature & pressure coverage, general to severe service needs, low emissions packing and easy maintenance.
There are a number of valves engineered to perform isolation and backflow prevention functions in electrolyzer units, from standard utility services to the more challenging caustic electrolytes. These valves are designed for tight shutoff across a wide pressure and temperature range, with low fugitive emissions to improve system efficiency. The valves are also constructed for long-life performance and rapid servicing to maximize unit uptime.
The Mitsubishi Power near term strategy is to focus on retrofitting existing plants according to Satoshi Tanimura—Chief Engineer and Senior Manager of Mitsubishi Power’ Gas Turbine Technology Administrative Division. In the case of a 20% hydrogen fuel mix, the existing gas turbine can be used,” said Tanimura. “However, making it usable with 30% hydrogen poses quite a challenge.
Mitsubishi Power is developing a 40-MW class gas turbine that can directly combust 100% ammonia with a commercial launch date of 2025. It is continuing work on a pilot project to convert one of three units—a 440-MW M701F gas turbine—at Vattenfall’s 1.3-GW Magnum combined cycle plant in the Netherlands to renewable hydrogen by 2023.
It will supply two hydrogen-capable M501JAC power trains to replace coal-fired units at the 1,800-MW Intermountain Power Project (IPP) in Utah.
To address NOx production, the turbine system will combine selective catalytic reduction (SCR) with “a newly developed combustor that reduces NOx emissions.” That system will then be installed in the company’s H-25 series gas turbines.
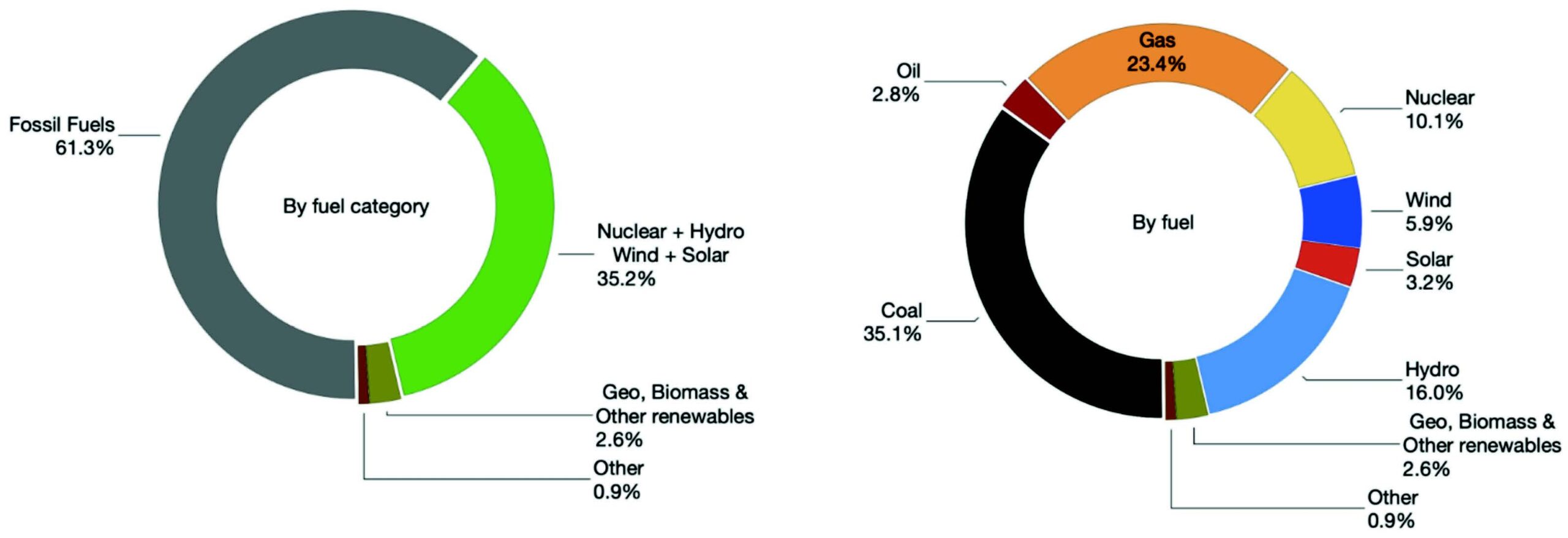
Final Thoughts
Over the next few years hydrogen will be used to replace up to 20% of the natural gas in turbines without significant capital investment. Other short term uses will be to supplement solid fuels in coal fi red boilers. In the long term, the production of hydrogen from biomass with CO2 use or sequestration will create negative carbon emissions.
Changes to the European Union’s emissions trading system are one of the factors contributing to the shift to cleaner steel production. The German steel producer Salzgitter has announced it will convert its first coal-based blast furnaces to hydrogen and renewable energy-based direct iron reduction and electric arc production by 2026 and complete the full conversion of its steelworks by 2033. Salzgitter, which has formed a partnership with Orsted for offshore wind power and the use of renewable hydrogen, is aiming to supply low-carbon steel to all BMW’s European car manufacturing plants. This comes as ArcelorMittal announced a €1.7 billion ( $1.9 billion) plan to build an electric arc furnace at Fos-sur-Mer and a 2.5 million ton direct reduction iron unit at Dunkirk. The company plans for both plants to be commissioned by 2027 and replace three of its five French blast furnaces by 2030.
Valve suppliers will be challenged by the leakage, safety, embrittlement, and other issues with utilization of hydrogen. However, to some extent this will be the tail waging the dog. Forty years ago a power plant supplier could not even be considered unless he had the ability to remove the SO2. Small sulfate slurry isolation knife gate suppliers took on an important role in shaping purchasing decisions for the entire plant.
The same importance that is put on valve integrity, is likely to be implemented for the use of hydrogen. The turbine supplier will not be successful unless he has the lowest total cost of ownership for hydrogen combustion. Part of this will be the critical valves. In turn the valve supplier will only be as successful as his hydrogen offering even though it may be a small part of the total. The end users, system suppliers and valve manufacturers all have to understand the technology developments and fi nd the best solutions for hydrogen valves.
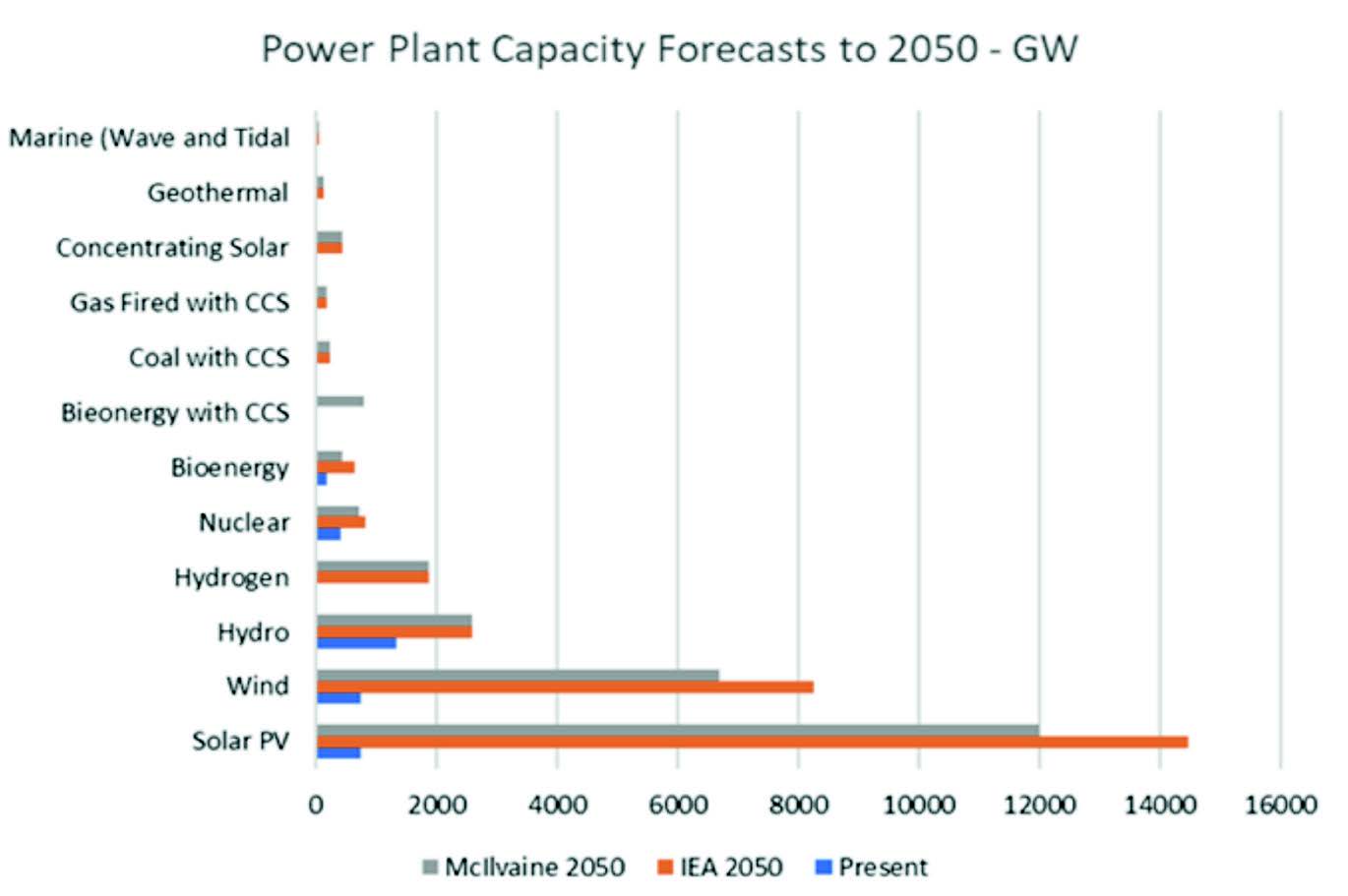
REFERENCES
1. Valves: World Markets published by the McIlvaine Company
2. Utility Tracking System published by the McIlvaine Company
ABOUT THE AUTHOR
Bob McIlvaine founded the McIlvaine Company in 1974 and oversees the work of 30 analysts and researchers. He has a BA degree from Princeton University.