Valves used in a number of processes are designed to meet environmental regulations. Valves find wide spread use in food manufacturing where there are special cleanliness requirements. One process includes purifying air prior to exhausting it from stacks. This can involve either fabric filters or scrubbers or both depending on whether the contaminant is particulate, gases or a combination. Electrostatic precipitators are an alternate means of particulate removal but have limited use in the food industry. An exception would be a food plant with coal fired boilers. Thermal oxidizers which combust odorous or harmful gases are also in limited use. Cyclones are used to separate large particles from the air stream. All of these processes require valves. The fabric filters use pulse jet valves to clean the fabric filter bags. A single collector in the food industry could require a 1000 valves.
Fabric filters also have a role in product recovery. For example a coffee slurry is injected into a hot gas stream in a spray drier. The powdered coffee is then captured in a downstream fabric filter. Valves are required to control the slurry injected into the spray drier as well as for cleaning the bags. The dust is pneumatically conveyed from the collector in a system with multiple valves.
A number of technologies are used to purify liquids in the food industry. Filters are used to purify water used in food processing and also used to purify juices and other liquids. Crossflow membranes are used to remove small particles from food liquids and water where the solids content is modest. High pressure valves are needed for cross flow applications. Final filters are preceded by a macrofiltration device if there are large amounts of solids to be removed. As a result a number of valves are used at each stage in the purification process. Clarifiers and centrifuges are also used to purify liquids with large amounts of solids. Valves used in these processes must handle large percentages of solids as well as meet FDA requirements for cleanliness.
Valves are also used in heating and cooling processes commonly needed in food processing. Wastewater treatment processes require a number of valves. Some food companies are converting food waste to biogas. Many food companies generate steam and use natural gas or solid fuel boilers. Steam generation requires high pressure and high temperature valves.
Three hundred international food companies will account for 50 percent of the valve purchases by the industry. They will also influence the purchasing decisions made by the smaller companies. Since their purchases are predictable it is possible to build the primary sales program around accurate forecasts of their “new, replace, and repair” expenditures.
Six of these companies will account for just under 10 percent of the total valve purchases over the next five years. The food industry will be spending $1.8 billion for valves per year while the top six purchasers will spend over $174 million.
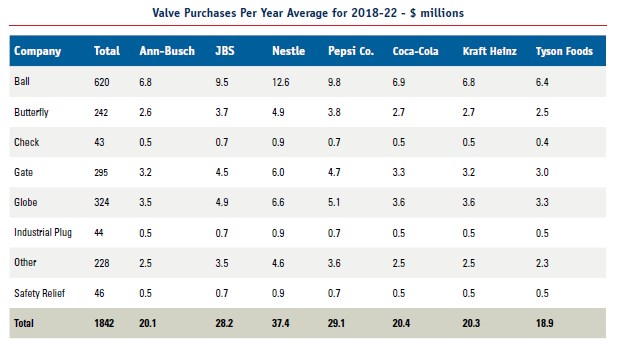
Anheuser-Busch InBev is based in Belgium and is the world’s largest brewer and sixth largest purchaser of valves for food and beverages. Many of the operations are U.S. based.
Nestlé is the world’s largest food and beverage company and largest purchaser of valves for food and beverage applications. It has more than 2000 brands and is present in 189 countries around the world. (2)
Nestle will spend $37 million for valves next year. Coca-Cola and PepsiCo purify large quantities of water for their beverages and food products.
JBS S.A. is a Brazilian company which is the largest (by sales) meat processing company in the world, producing factory processed beef, chicken and pork, and also selling by-products from the processing of these meats. The processes require both air and liquid filtration. For example liquid filtration is used to purify blood products which are then spray dried and captured in fabric filters. Wastewater treatment of facilities used to grow animals requires substantial valve expenditures.
The Kraft Heinz Company is the third-largest food and beverage company in North America and the fifth-largest food and beverage company in the world. Cheese manufacturing requires significant investments in centrifuges and cross flow filtration with accompanying valves.
Tyson Foods has expanded from chicken to a number of food products. Valves are needed throughout the cycle from poultry feed to poultry raising to food processing.
Many food companies are embracing the Industrial Internet of Things (IIOT). Remote monitoring of the valve performance in all their plants allows them to centralize purchasing and make decisions based on lowest total cost of ownership. (3) As a result a few people at each one of the 300 largest food companies will make 50 percent of the valve purchasing decisions. This creates a unique opportunity for direct sales by filtration suppliers. The first step is the determination of the future purchases by each large prospect.
(1) Industrial Valves: World Markets published by the McIlvaine Company
(2) Industrial Plants and Projects published by the McIlvaine Company
(3) IIoT and Remote O&M published by the McIlvaine Company