They are ubiquitous in any process plant and their many different designs offer many opportunities to accidents and near misses. This article highlights some safety concerns regarding industrial valves, in the hope that it helps convincing managers and employees of how dangerous this critical equipment may be.
By Davi Sampaio Correia – Technical Consultant
1) Selecting the Right Tool for the Job: Valve Specification
Valve safety starts in the project phase. When people think of valve specification, they often worry about what flows through the piping, and rightly so. However, the environment outside the valve may also be capable of affecting its performance. For example, Stress Corrosion Cracking (SCC) is a type of corrosion that commonly affect certain grades of austenitic stainless steels, such as the ones from series 3XX (AISI 304, 316, etc.). When a susceptible material is combined with tensile stress and a corrosive environment. One of the worse aspects of a SCC failure is that it gives little to no warning; many times, the surface shows no signs of degradation, but fine cracks are progressing into the material.
The IOGP (International Association of Oil & Gas Producers) released a safety alert regarding the use of AISI 304 bolts in offshore environment.1 Several ASTM A193 B8 (Class 2) bolts failed while securing a valve to its respective piping flange. No personnel were harmed, but that was mere luck. In this case, the tensile stress in the bolts combined with chloride from the offshore atmosphere to attack the austenitic material of the bolts. Figure 1 shows a picture of the valve and a macrography of the internal structure with cracks.
Specification includes also selecting the right valve type for a given application. The CSB (Chemical Safety Board) is an independent federal agency of the United States and it routinely investigates industrial accidents. One of these accidents involved an acetylene plant which used a check valve for preventing acetylene from backflowing in case of low water pressure. Figure 2 shows a simplified flow diagram of the plant. On January 25th, 2005, acetylene flowed through the empty water input line at a New Jersey, acetylene manufacturer and accumulated in a shed beside the generator room. When the gas ignited, three works were killed, the shed was destroyed, and the nearby manufacturing building severely damaged. All this could have been prevented with the specification of an actuated shutdown valve in addition to the check valve, which should not have been considered as the sole safeguard against backflow. The spring in the actuator of a shutdown valve would close the valve in case of lower pressure of the water line and would act as a fail-safe mechanism.

2) Lack of Understanding About the Valve
Accidents in operation or maintenance interventions are often linked to ignorance – mechanical ignorance. In other words, people sent to operate or repair valves may not know how they work or how they are constructed. Let’s see some examples.
Valves are designed to do a certain job. Ball valves, for example, are good for isolation and globe valves are good for throttling. Whoever is in charge of operating valves has to understand how they work, or the possibility of an accident will always be present.
When a ball valve is left in a partially open position, zones of higher velocity and lower pressure are created in the vicinity of the ball due to the Venturi effect. As time progresses, the valve will lose the capacity for sealing, due to damage to ball and seats. Depending on the process conditions, the valve may even have the body eroded to the point of eternal leakage, as shown in Figure 3. So, on-off or isolation valves, such as ball, butterfly and gate are made to be left either in the fully open position or the fully closed position. Anything in between is looking for trouble.
Valves are funny: sometimes they leak when you want them to seal and sometimes the seal when you want them to leak. Do you doubt the last part of this statement? Just think of drain valves. It is very common for them to be clogged with debris or dirty. Many an operator opened such a valve, saw no fluid coming out and proceeded to disconnect piping, only to be covered later in toxic or flammable fluids. If a valve is in the bottom of a vessel, it may provide no useful indication of the pressure inside the vessel. There has to be an alternative method to assure there is no residue left before disassembling piping, such as flushing the vessel with a cleaning fluid beforehand. Also, valves in this situation should be operated regularly, in order to avoid plugging.
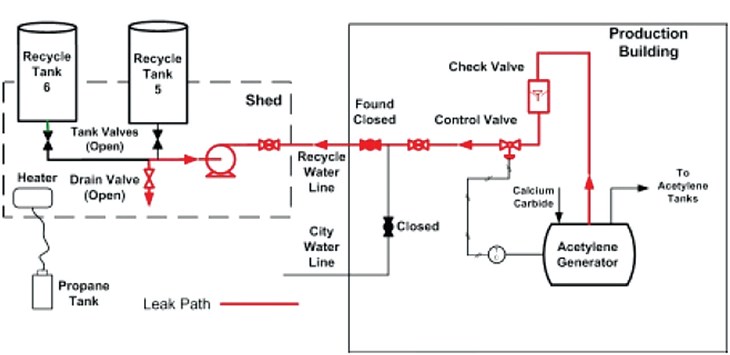
One last issue regarding operation is what I call valve feeling. A field technician is supposed to know how much torque is needed to operate a manual valve. In other words, how the valve feels when it is being opened or closed. That is the only way he or she may detect problems such as a broken connection between handle and obturator. Many accidents happened because a valve believed closed was in fact open – corrosion or prior excessive force may have severed the mechanical continuity between obturator and handle (or gearbox). An experienced technician must be capable of differentiating opening a valve in this condition from a normal valve. All the more reason to exercise caution when introducing a new valve model in a plant: everyone involved has to be trained in its operation.
Ball valves come in many shapes and sizes. One of them is the compact floating ball valve with butt weld end connections. In 2009, a maintenance worker was killed when he tried to disassemble one of these valves. As you can see in Figure 4a and 4b, the valve was a 3-piece side entry valve. The worker mistook one of the valve side covers for the piping flange. As a result, the ball was projected outward of the valve by line pressure and hit the worker (Figure 4c).
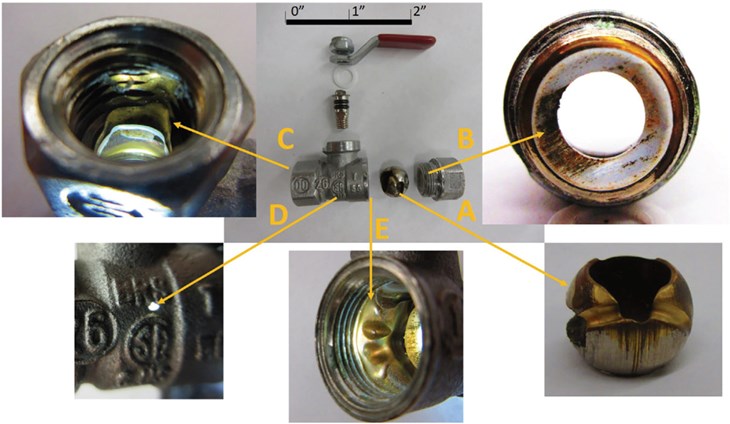
3) Leadership Indifference
If employees sense a company’s leadership is not serious about safety, they will quickly disregard what little safety procedures may exist. This is human nature, prone to see anything that slows the pace of things getting done as hindrance – including safety. It is management’s duty to tell people that procedures exist for a reason and that sometimes we need to take a step back to have a better understating of the situation. Let us review two areas where management enforcement is critical for safety: management of change and tagging.
Management of change is a critical part of any process safety program. It is a procedure to ensure prior evaluation of every change capable of modifying the level of risk in a plant. The whole idea is to avoid unintended consequences of ill-considered changes. For example, when confronted with a defective ball valve in a high-pressure gas line, many maintenance planners would not blink in replacing the valve with one in the warehouse if the only difference between them is the o’ring specification.
Say the original is a fluoroelastomer with RGD capabilities and the other one is a similar grade but with no RGD resistance. RGD stands for Rapid Gas Decompression and it means the o’ring was formulated and processed to be more tolerant of pressure drops in gas applications. Given a severe enough pressure drop, entrapped gas molecules may expand inside the elastomer and cause surface blisters, splits or catastrophic failure. So, going back to our example, if no management of change procedure is followed and the valve is replaced, the plant may be only one decompression event away from an external gas leak.

When a plant starts operation, everything is new, well-identified and people tend to be cautious, as they are not familiar with the layout. As time passes, colors fade, metal rust, tags fall, and what was once easy to locate now may take some back and forth between piping and diagrams, what is likely to induce human error. Sometimes, process upsets require immediate action, and such occasions may cause even experienced workers to make mistakes. For example, the CSB also has a report4 about an explosion and fire at the Formosa Plastics Corporation. In this tragic event, five workers were killed and three severely injured. All due to the wrong valve being open during an upset. In order to reduce the likelihood of human error, management has to ensure – among other things – proper pipe marking and valve tagging.
Plants may have layouts that are misleading, with pipes appearing and disappearing through numerous interfaces. And even with a good layout, lack of proper tagging and color codes may confound technicians. So, it is management’s duty to ensure piping, valves and other equipment are properly identified throughout the plant. The standard ANSI/ASME A13.1 (Scheme for The Identification of Piping Systems, 2017) plus local legislation is a common combination used for guidance. Figure 5 has some examples derived from the ASME A31.1. Also, companies have their own internal procedures regarding the unique identification used for vessels, valves, and piping. For lines, for example, the format may resemble something like this:
• XX”–YY–ZZ—WW, Where:
• XX” – nominal pipe size
• YY – Fluid service code
• ZZ – Unique identification for the line
• WW – Material and pressure class (carbon steel, #300, for example)
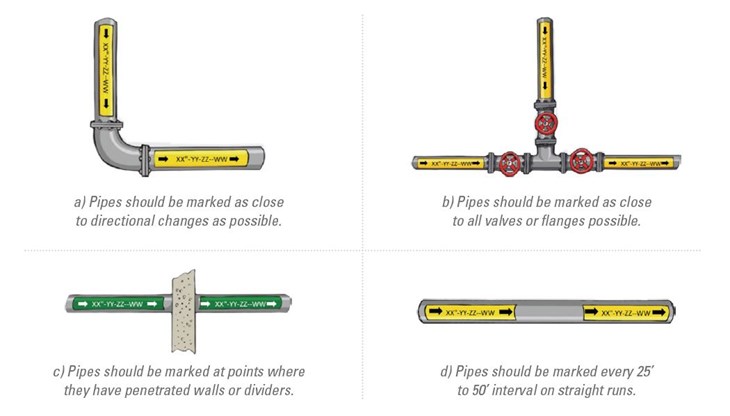
Conclusion
A long time ago, I heard someone say in a presentation that safety should not be a priority for any business. As the audience stared to the lecturer in disbelief, he calmly explained that safety should be a value, not a priority. Priorities change – due to market, budget, or legislation – but values do not. So, if safety is a value for you – and I hope it is – remember to always ask yourself: ‘Do I really know this valve’?
REFERENCES
1. https://mailchi.mp/iogp/iogp-safety-alert-297?e=0e7f9474ba
2. https://www.csb.gov/acetylene-service-company-gas-explosion/
3. Moses, D. et al, An investigation of the failure of a 1/4” ball valve, Engineering Failure Analysis 100 (2019) 393–405, https://doi.org/10.1016/j.engfailanal.2019.02.047
4. https://www.csb.gov/assets/1/20/formosa_il_report.pdf?13838
ABOUT THE AUTHOR
Davi Correia is a Senior Mechanical Engineer who has worked at a major Brazil-based oil company for the last 15 years. Correia is part of multi-disciplinary team that provides technical support for topside piping and equipment of production platforms. During this period, he began to work with materials and corrosion, and later moved to piping and accessories technology, where he has become one of the lead technical advisors on valve issues. Correia was part of the task force that revised the IOGP S-562 standard, and wrote the S-611 standard. Correia has a master’s and a doctor’s degree in welding by the Universidade Federal de Uberlandia.