The development of thermoplastic control valves can be traced back to the mid-20th century when plastics like polyvinyl chloride (PVC) and chlorinated polyvinyl chloride (CPVC) gained prominence. These materials showed excellent resistance to corrosion and chemical attacks, making them ideal for a wide range of industrial applications. Over the years, advancements in thermoplastic technology and manufacturing processes have led to the creation of sophisticated control valves capable of handling demanding conditions.
By Shane McDaniel, Business Development Manager, Asahi/America, Inc.
To meet the demanding conditions and adhere to industry standards, thermo- plastic valve manufacturers have made various advancements over the last several decades. The International Organization for Standardization (ISO), American National Standards Institute (ANSI), and American Society for Testing and Materials (ASTM) provide guidelines for many different applications and industries. Adherence to these standards is integral to enhancing the safety and quality of thermoplastic valve manufacturing and design improvements. Below are a few examples of how ISO, ANSI, and ASTM are applied to thermoplastic valve manufacturing:
- ISO 9001: ISO 9001 is centered around the concept of a Quality Management System (QMS), which is a set of policies, processes, procedures, and records that define how an organization will achieve and maintain the quality of its products or services. Ensuring construction processes meet ISO 9001 quality standards can result in better project management and workmanship.
- ISO 5752: ISO 5752 is an international standard that specifies the face-to-face dimensions of metal valves for use in flanged pipe systems. The standard is useful for engineers, designers, and manufacturers involved in the design and construction of industrial piping systems.
- ANSI B1.20.1: ANSI B1.20.1 is an American National Standard Institute standard that specifies the requirements for pipe threads, including thread dimensions, tolerances, and thread gages. It covers tapered National Pipe Thread (NPT) pipe threads. ANSI B1.20.1 is important for ensuring the compatibility and interchangeability of threaded pipes, fittings, and valves used in various industries.
- ASTM Standard D-1784: ASTM D-1784 specifically pertains to rigid polyvinyl chloride (PVC) compounds and chlorinated polyvinyl chloride (CPVC) compounds. This standard is used in the manufacturing of plastic pipes, valves, and fittings. It provides a means for selecting and identifying compounds on the basis of numerous physical and chemical criteria.
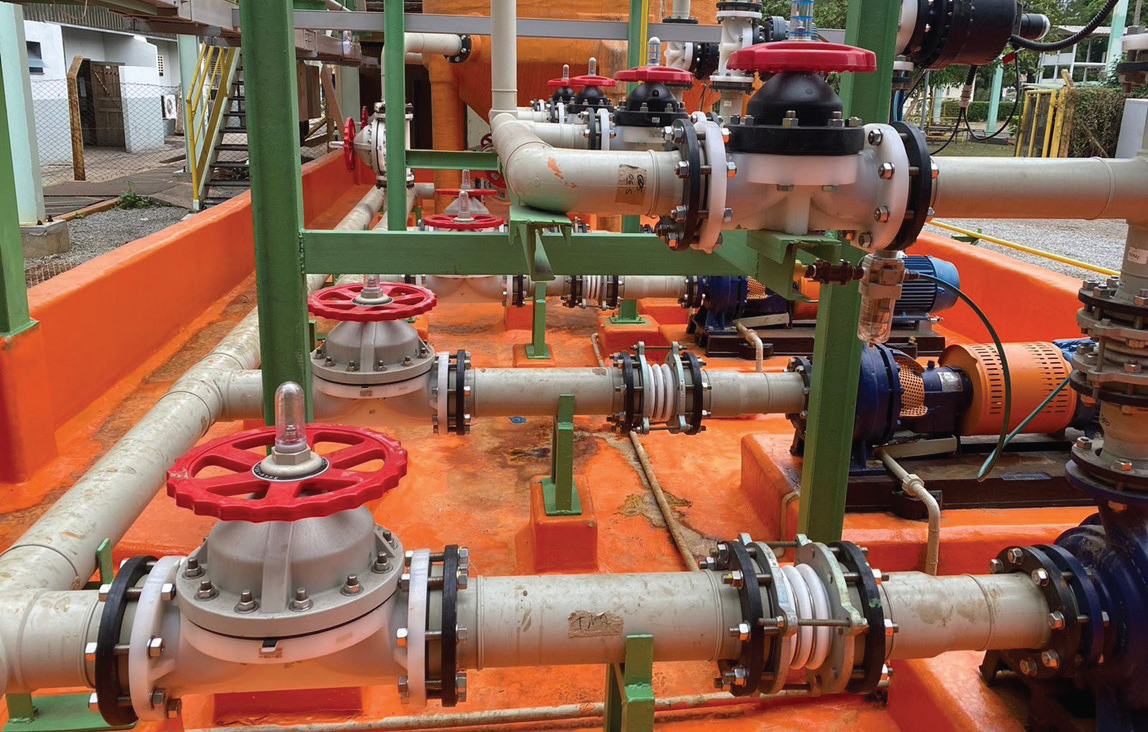
In all these contexts, the ISO, ANSI, and ASTM standards provide a foundation for improving design by focusing on quality, safety, efficiency, and environ- mental sustainability. Designers and engineers should stay up-to-date with the latest standards and apply them as appropriate to ensure their project designs meet the highest standards of excellence and compliance.
Thermoplastic Valve Materials & Their Applications
Manufacturers of thermoplastic valves have implemented these standards and design innovations, leading to a rise in the utilization of thermoplastic valves across a diverse set of industries, including: chemical processing, water treatment, pharmaceutical and laboratories, animal life support systems, food and beverage manufacturing, and semiconductor chip manufacturing. Thermoplastic valves are often used in processes involving the control of corrosive or abrasive fluids, where conventional metallic valves may suffer from corrosion issues.
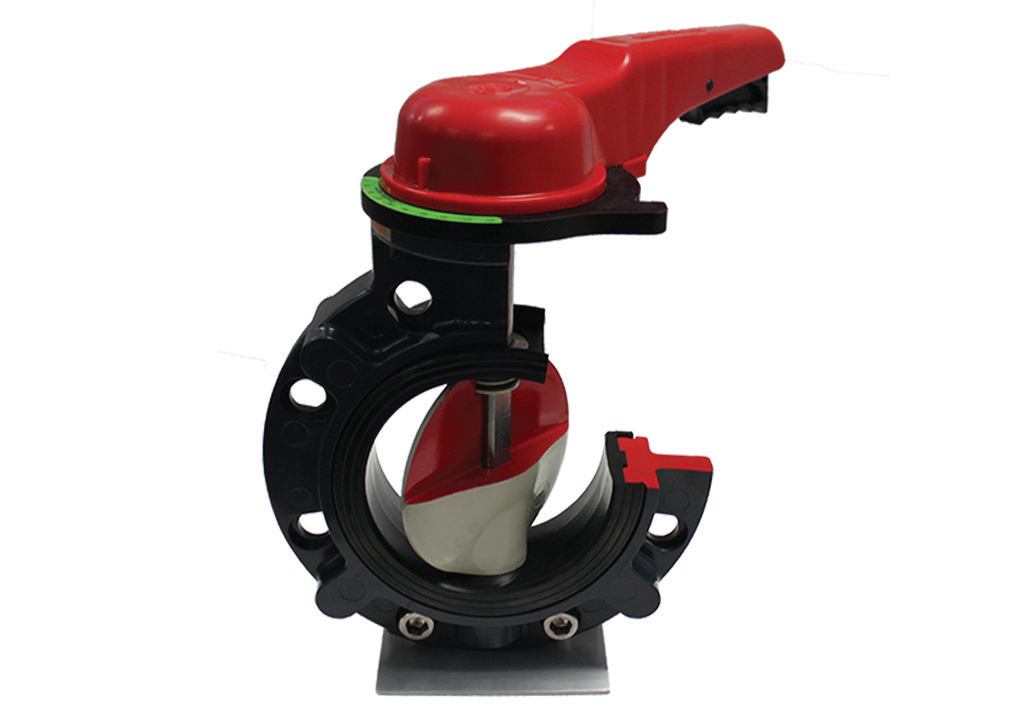
When deciding between metallic and thermoplastic valves, engineers must consider several factors. Thermoplastic valves offer excellent corrosion resistance, lightweight construction, and ease of installation. They are also electrically non-conductive, making them suitable for applications involving flammable materials. On the other hand, metallic valves may have higher pressure and temperature ratings compared to thermoplastic valves and often have better resistance to mechanical wear. The choice between the two depends on the specific requirements of the application.
Another consideration when selecting a valve is the thermoplastic materials of the valve construction. Polyvinyl chloride (PVC), chlorinated polyvinyl chloride (CPVC), polyvinylidene fluoride (PVDF), and polypropylene (PP) are commonly used materials in the construction of valves, pipes, fittings, and other components for various applications. This is particularly true in the chemical processing, water treatment, and industrial sectors. The list below outlines the differences and applications between the aforementioned materials.
Polyvinyl Chloride (PVC):
- Composition: PVC is made from the polymerization of vinyl chloride monomers.
- Properties: PVC is known for its corrosion resistance, lightweight, and relatively low cost. It has good chemical resistance to a wide range of acids, bases, and salts. However, it is not suitable for use with strong oxidizing agents or some organic solvents.
- Applications: PVC is commonly used for water supply lines, drainage systems, and some chemical processing applications.
Chlorinated Polyvinyl Chloride (CPVC):
- Composition: CPVC is a modified form of PVC with added chlorine atoms.
- Properties: CPVC offers better heat and chemical resistance compared to PVC. It is suitable for a broader range of chemical applications and can handle higher temperatures.
- Applications: CPVC is often used for hot and cold-water distribution, industrial applications, and applications where higher temperature resistance is required.
Polyvinylidene Fluoride (PVDF):
- Composition: PVDF is a high-performance fluoropolymer made from the polymerization of vinylidene fluoride monomers.
- Properties: PVDF is known for its excellent chemical resistance, high-temperature resistance, and good mechanical properties. It has outstanding resistance to various chemicals, including strong acids and bases.
- Applications: PVDF is commonly used in the chemical industry for handling highly corrosive substances. It is also used in valve, pipe, and fitting applications in the semiconductor, pharmaceutical, and food processing industries, where the highest purity water processes are required.
Polypropylene (PP):
- Composition: PP is a thermoplastic polymer made from propylene monomers.
- Properties: PP is lightweight, durable, and has excellent chemical resistance. It is known for its resistance to a wide range of acids, bases, and solvents. However, it may not be suitable for use with strong oxidizers.
- Applications: PP is commonly used for water and wastewater systems, as well as in chemical and industrial applications where corrosion resistance and low-cost materials

Control Valve Types & Considerations
The successful application of thermoplastic control valves relies on careful consideration of several factors. Engineers should assess the chemical compatibility of the thermoplastic material with the process fluid, operating temperature and pressure conditions, and potential exposure to UV radiation or other environmental factors. Proper valve sizing, material selection, and sealing mechanisms are critical to ensure long-term reliability and safety.
Elastomers, such as ethylene propylene diene monomer (EPDM) or fluoroelastomer (FKM), are often used as sealing elements in thermoplastic control valves. Selecting the right elastomer is crucial to ensure compatibility with the process fluid and operating conditions. Engineers should consider factors like temperature range, chemical resistance, and sealing performance when choosing elastomers to ensure leak-free operation and prevent valve failure.
There are several types of thermoplastic control valves available, each with its own advantages. The choice depends on the specific needs of the process. Some factors an operator might consider are media type, environment (inside/outside, hot/ cold), sizing, temperature, and pressure.
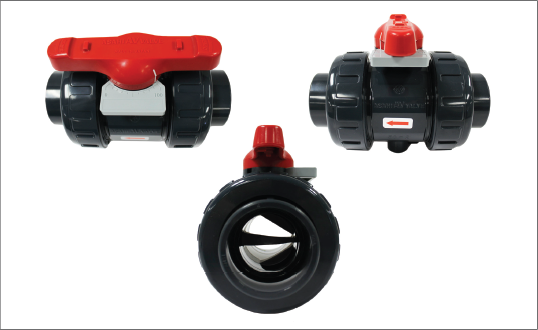

- Butterfly Valves: These quarter-turn valves offer excellent flow control and are compact, making them suitable for tight spaces. They are often used where precise throttling is not required and are most commonly used in on/off applications. Butterfly valves are known for their quick operation and relatively low-pressure drop when fully open. Some manufacturers offer a spherical disc design for increased Cv or flow.
- Ball Valves: Ball valves are quarter-turn valves known for their simple and reliable operation with tight shut-off capabilities. They are commonly used in applications requiring on/off control. Ball valves features include the ability to create a tight seal when closed to minimize the risk of leaks. The use of the correct thermoplastic and elastomeric materials gives the ball valve a wide spectrum of applications and uses, including use with harsh chemicals, like sodium hypochlorite. Recently, some manufacturers have designed a ball valve for precision flow control by custom manufacturing the ball inside of the valve, giving end users additional functionality in the field.
- Diaphragm Valves: Diaphragm valves are multi-turn valves ideal for applications where contamination or leakage must be minimized. They are commonly used in the pharmaceutical and biotechnology industries. The diaphragm is the central component of the valve and is typically made of an elastomer, such as PTFE or Teflon™. The body of the diaphragm valve is the housing that controls the fluid flow and can be designed in a variety of configurations including straight-through, weir type, or multi-port design. Some valve manufacturers offer a three-layer diaphragm consisting of EPDM/PVDF/PTFE to provide a gas barrier protecting the bonnet internals from aggressive off-gassing chemicals, such as sodium hypochlorite.
- Globe Valves: Globe valves are linear motion valves that provide precise flow control and are suitable for applications requiring high accuracy. The globe valve is named after the spherical shape of its body, which is designed to accommodate the disk or plug that controls the flow of media through the valve. The globe valve’s primary facilitator of flow control is the disc or plug inside the valve body, which can be raised or lowered to control the flow of fluid. Globe valves are effective at both on/off and modulating flow applications.
Final Thoughts
The use of thermoplastic control valves has become increasingly popular in various industrial applications due to their exceptional resistance to corrosion and chemical attack. However, successful implementation requires careful consideration of material compatibility, operating conditions, and valve type. Engineers and specifiers should work closely with the manufacturer and other experts in the field to ensure that the selected thermoplastic control valve meets the specific requirements of their application while adhering to industry standards and regulations. By doing so, they can harness the benefits of thermoplastic valve technology for efficient and reliable process control.
