Ideal Features & Benefits of a Check Valve in LNG Applications
In almost every piping system, there is a need for back flow prevention. Most piping systems utilize pumps or compressors to generate needed pressure for movement of line fluids or gases. When rotating equipment stops, flow reversal or back flow occurs, and one of the most significant elements of the LNG production system design is integrating the means to prevent back flow, thereby protecting equipment, and preventing damage to plant infrastructure, as well as excessive emission leakage, and potential medical emergencies. Whether in the gas field, liquefaction plant, LNG storage tank, LNG tanker or gasification terminal, a valve that is paramount across the LNG value chain is the check valve. These valves offer solutions to the destructive effects of flow reversal and prove reliable in the severe conditions presented during the LNG process.
Intended primarily to protect pumps, compressors, piping systems or other critical components in the value chain from dangerous system deceleration and water hammer, the check valve is different from shut-off and control valves. While those valves have the ability to stop flow completely, check valves allow the flow of fluid in a single direction, thus their capability for preventing back flow surges. Additionally, unlike on/off valves, check valves are flow sensitive and rely on the line fluid to open and close, making them one of the few self-automated valves, a benefit in its own right. As a result of their constant exposure to fluid mediums, check valves are highly susceptible to wear, sticking, jamming and wedging, and traditional check valve solutions can suffer from heavy slamming caused by turbulence, which in turn can compromise their ability to prevent flow reversal. Another pain point posed by traditional check valves such as swing and tilted disc check valves is their long closing distances which can actually exacerbate the effects of water hammer and the significant pressure loss that results from the utter of in-stream components. These valve types are more susceptible to low flow conditions that can cause wear and premature failure.
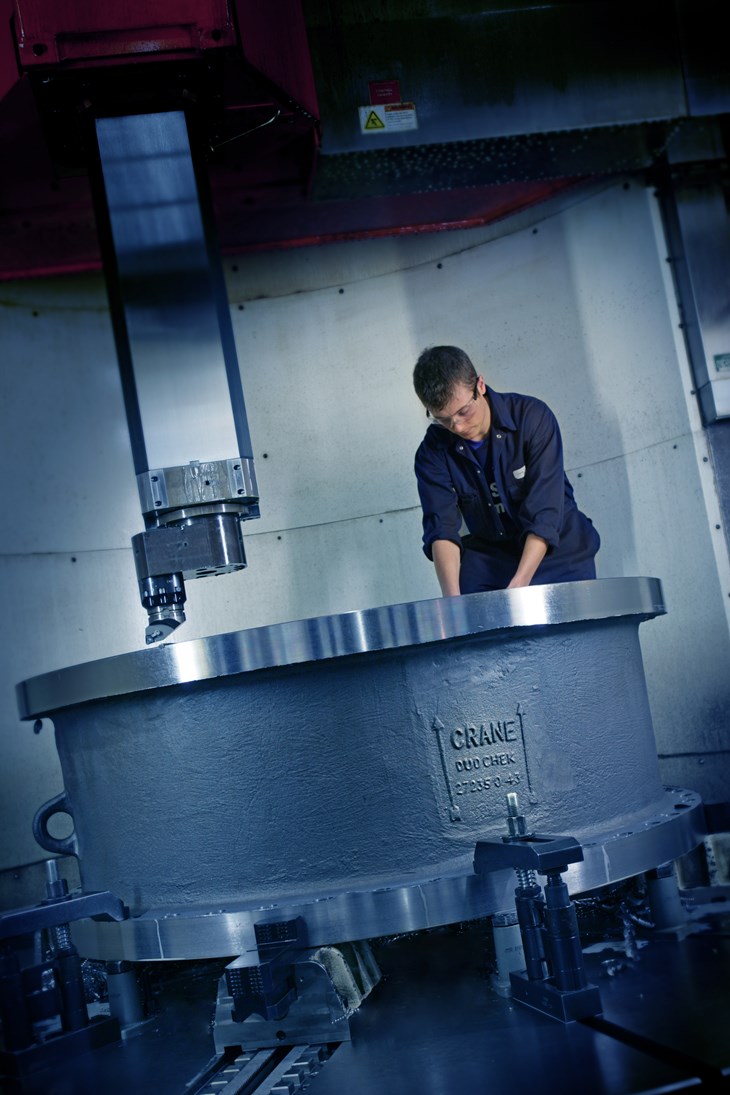
To address these challenges LNG manufacturers may instead seek out alternative check valve solutions that incorporate features and benefits that can directly address and counter these problems. For example, a dual-plate wafer valve design is a stronger, lighter, smaller and more efficient check valve than the swing check. Utilizing springs to increase the valve reaction and response time, a highly engineered dual-plate check valve can better protect equipment in place along the liquefaction and regasification terminals present within an LNG processing plant. An increased response time can reduce the water hammer effect for an improved non-slam performance. Directly ad- dressing the extreme cryogenic demands of the liquification process, certain dual plate check valves have been approved for subatmospheric to cryogenic temperatures ranging from -58°F through -321°F.
Another alternative to the conventional swing check valve is the nozzle-style which can be specifically designed for fast-reversing systems, again where back flow is a concern. In critical service applications, a highly engineered check valve can minimize the damaging effects of water hammer in fluid systems, eliminate the chatter associated with conventional valves, protect rotating equipment from damage due to flow reversal, minimize pressure loss in piping systems and provide quick dynamic response to reduce reverse velocity. For critical applications like LNG, the internal geometry of some check valves can be modified to suit the service conditions.
A benefit of both the Dual-Plate and Nozzle style check valve is their lack of a leak path to the atmosphere. Without this path, they emit zero fugitive emissions for the life of the valve with no adjustments ever needed. Check valves typically have higher allowable leakage rates than other valves, but in cases where valuable equipment, pipes and other aspects of the plant’s infrastructure need to be protected, a check valve that restricts leaks can prove valuable to system manufacturers.
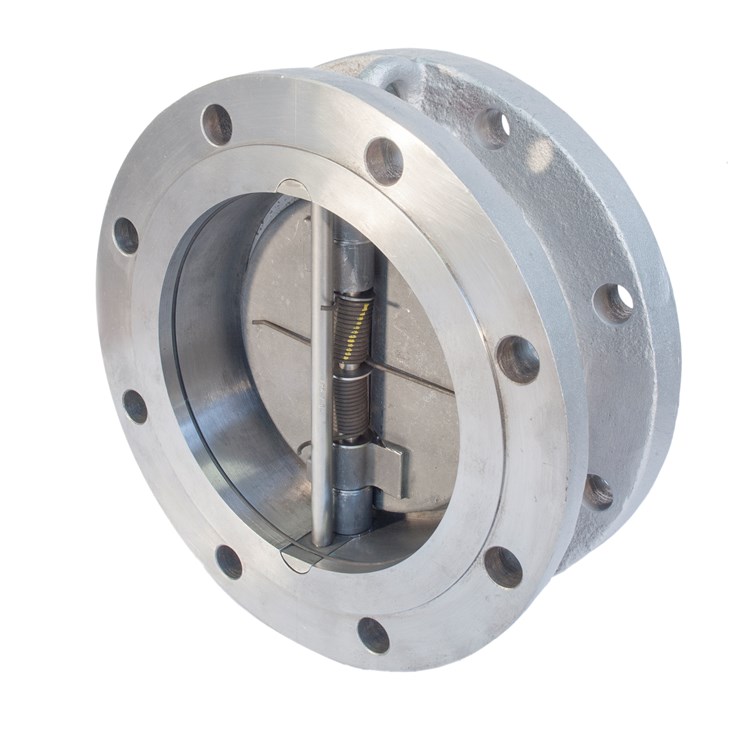
Sizing and Selections
Compared to other valves, check valves are automatic and therefore susceptible to fluctuations in fluid flow. They require no outside stimulation and rely instead completely on the basic forces inside the valve, as well as the external factors present (i.e. fluid type, temperature, etc.) when determining when to close. The actuator for these valve types is actually the fluid system inside the pipe. They close only when the forward flow begins to decrease. Therefore, varying internal system pressures can cause problems during check valve selection and functionality.
To eliminate leaks and back flow, it is very important to ensure the valves in place are also sized appropriately for the application. Generally, valve sizing is done by selecting a valve that matches the pipe size. However, that can be easier said than done, as this process often leaves much to chance and could result in impractical situations in terms of investment and valve performance. What is equally important as pipe or line size is the flow that the valve can provide, which in most cases can be determined by the principles of energy conservation in the flow calculations. For instance, a valve that is too small will not pass the required flow, and a valve that is too large will, for one, be expensive, but also create instability in the system. Additionally, a valve that is too large can wear itself out prematurely, ultimately leading to valve failure.
In determining the proper valve size for a specific application, knowledge of the process conditions is also important. Users must understand the process for which the valve will be used and select a valve that can withstand those conditions, such as energy losses, pressure loss due to friction and turbulence, flow coefficient, and Cv provided by the valve manufacturer. How a valve performs and holds up under these conditions, as well as its listed service life are key factors that must be considered prior to selecting a check valve for LNG applications, and any industry. However, the ultimate consideration has to involve a review of the total process system and its design. Understanding what is needed, for how long, and under what conditions is paramount for safe and trouble-free performance. In short, valve sizing and selection should consider valve material compatibility with the fluid medium, the valve rating (ASME Pressure Class), application flow, design and operating conditions and the installation requirements of a particular facility, as well as line size, end connections, system modifications and leakage regulations.
Conclusion
From cryogenic environments like that of LNG liquefaction to high-temperature applications of LNG gasification, check valves play an important role in the protection of the expensive and critical equipment in place in such manufacturing plants. Their sole purpose of pre- venting reverse flow and the damaging effects it can have on that equipment, as well as the safety threats it can pose to plant personnel make check valves a valuable addition to any operation. As the industry continues to grow, so too will the prevalence and use of check valves, and it’s important that highly engineered solutions are in place. Dual- plate and nozzle-style valves offer added benefits and solutions to the pain points often experienced by traditional swing check valves, and have emerged as essential components within the LNG value chain capable of addressing the needs of natural gas producers worldwide.
About the author
Carlos Davila is a registered professional engineer and a graduate of the University of Houston with a Bachelor of Science in Mechanical Engineering. With over 45 years of experience in the valve industry, Carlos’ background includes design, development, application and production of valves. He has written and published several papers in ASME and Hydrocarbon Engineering, and is an active voting member of the API Manufacturers Subcommittee on Piping and Valves for over 30 years.