Maintenance protocols for wellhead components have conventionally been relying on routine visual inspection and preventive techniques to evaluate their health and maintain their reliability. These techniques require routine site visits and have several safety and cost pitfalls leading to higher safety incidents and lost time. Digitalization, automation, and implementation of smart analytics to critical wellhead process control components does not only reduce safety incidents, but also improves maintenance plans and reduces operating cost.
By Hossam Gharib, Ph.D., P.Eng., Senior Product Engineer, Surface Safety Systems – Stream-Flo Industries Ltd.
Background
A study conducted in 2017 by the National Institute for Occupational Safety and Health (NIOSH), center for disease control and prevention (CDC), estimates that 32% of casualties in the oil & gas industry are due to roadway incidents. A similar, but more recent 2021 safety performance analysis by the International Association of Oil and Gas Producers (IOGP) estimates 60% of fatalities in the industry are due to roadway and maintenance incidents combined. Another recent study by Energy Safety Canada in 2022 covering Western Canada (Alberta and Saskatchewan) estimates that 40% of the industry’s fatalities are due to transportation accidents and 72% of that is due to highway incidents. These studies indicate the need to limit inspection and maintenance trips to the wellhead to reduce safety incidents.
To address this occurrence, digitalization, automation, and implementation of smart analytics to critical wellhead process control components should be considered. Remote condition monitoring is time saving and when coupled with autonomation methodologies can identify potential failures and prompt corrective actions, which consequently leads to asset life and availability improvement. In addition, remote monitoring and process control limits the number of field trips for inspection and manual operation, thus leading to a reduction in operating cost and increase in efficiency.
Challenges
Achieving an autonomous wellhead operation is considered part of developing a normally unattended facility (NUF). According to the IOGP, an NUF is “a facility or installation where all process control and operations (including start-up and shutdown) are either completely automatic and/or managed remotely, such that human personnel are not normally present for determined periods of time and meets reliability, availability, and production efficiency targets similar to a manned facility.”
Limiting the presence of personnel in an NUF is challenging since several operation and maintenance tasks are still required, whether routine or unplanned tasks. Some of the routine tasks include starting/stopping equipment, turning manual valves, cleaning of process equipment, and visual inspection. Unplanned tasks include remotely resetting a valve after process/emergency shutdown (ESD) interventions, detection of leaks and fires, and ability to isolate and disconnect equipment.
Smart Emergency Shutdown System (ESD-EHX) Architecture
A vital component of the wellhead is the surface safety valve (SSV), which is designed to close upon loss of power supply, or process upset, in the event of an emergency. Common actuation of the SSV is conducted through an ESD system utilizing fluid power, commonly hydraulic or pneumatic. At Stream-Flo Group of Companies, the journey towards wellhead autonomation and achieving an NUF commenced with the development of a Smart ESD that integrates a self-contained electro-hydraulic power unit with control elements, sensors, edge computer/controller, and local and remote connectivity to control and monitor an SSV. Figure 1 presents the high-level architecture of the Smart ESD system, designated as ESD-EHX. A low power electric motor is used to generate the hydraulic pressure, which allows the system to be solar powered.
The edge computer/controller runs the system diagnostics and analytics and only sends evaluated data through a cloud storage system. Edge processing leads to an improved system responsiveness, efficiency, security, and reliability, while cloud communication provides remote control, data storage, ease of accessibility, and multi-site management.
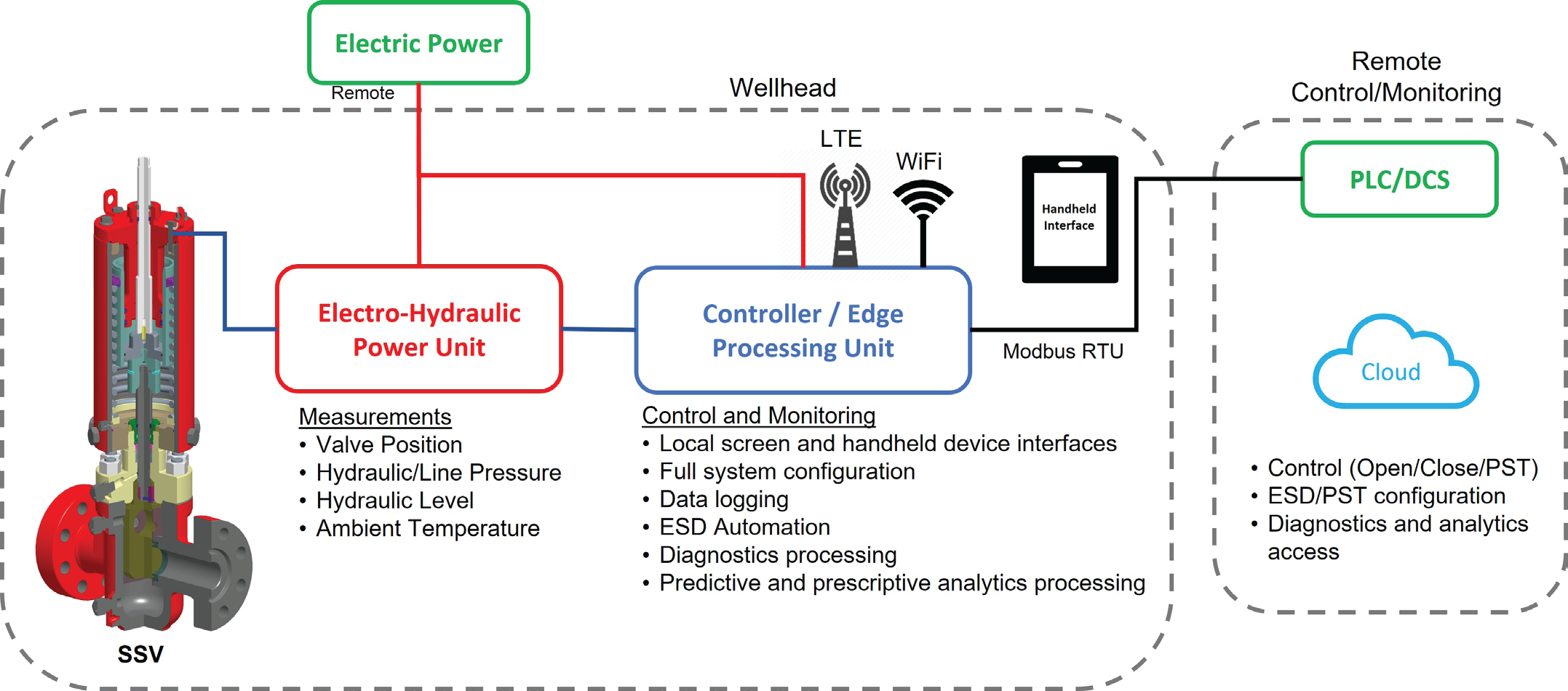
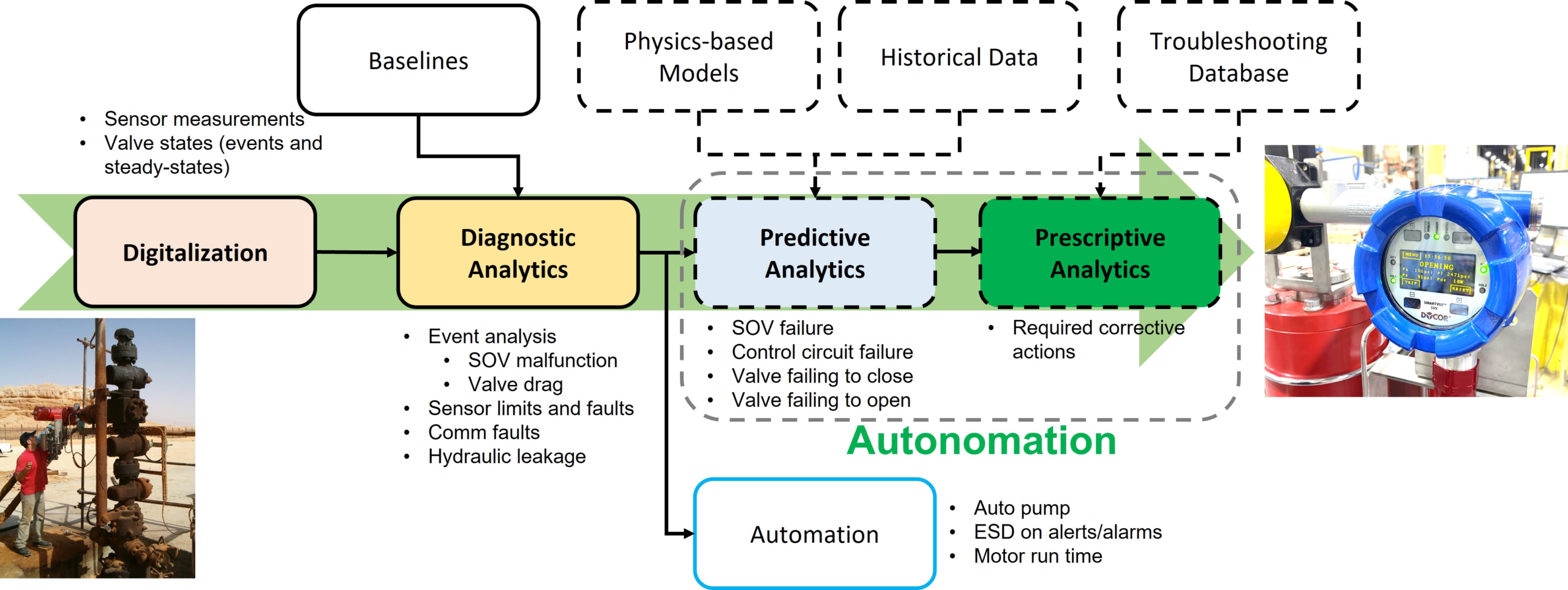
Maturity Levels and Analytics
The system development, shown in Figure 2, spans four maturity levels through digitalization, diagnostics analytics, predictive analytics, and finally prescriptive analytics. This transitions the SSV operation and maintenance from manual and visual processes to autonomous control and health evaluation. The transition involves automation and autonomation of the ESD system. To understand the difference, below are two examples applicable to an SSV.
In the case of automation, usually a simple control loop is used to sense, analyze, and act. For example, cycling the hydraulic pump is based on sensing a low-pressure level signal, which the controller analyzes through comparison to a set limit and acts to energize the pump’s electric motor.
On the other hand, an autonomation system involves a higher level of logic to perceive, understand, and solve. It involves real-time and historical data processing coupled with physics-based models to reach a final solution. For example, to predict failure to trip an SSV, the system will perceive a high drag from the coupled real-time data and models, which is then compared to historical data to predict through extrapolation when the SSV system will fail.
In addition, autonomation of the Smart ESD involves identifying corrective actions through prescriptive analytics. In its simplest form, this can be performed through selecting the corrective action(s) from a user input troubleshooting database. An advanced approach involves machine learning based on historical failures and their corrective actions to determine the best course of action given specific constraints, such as repair cost and lost time.
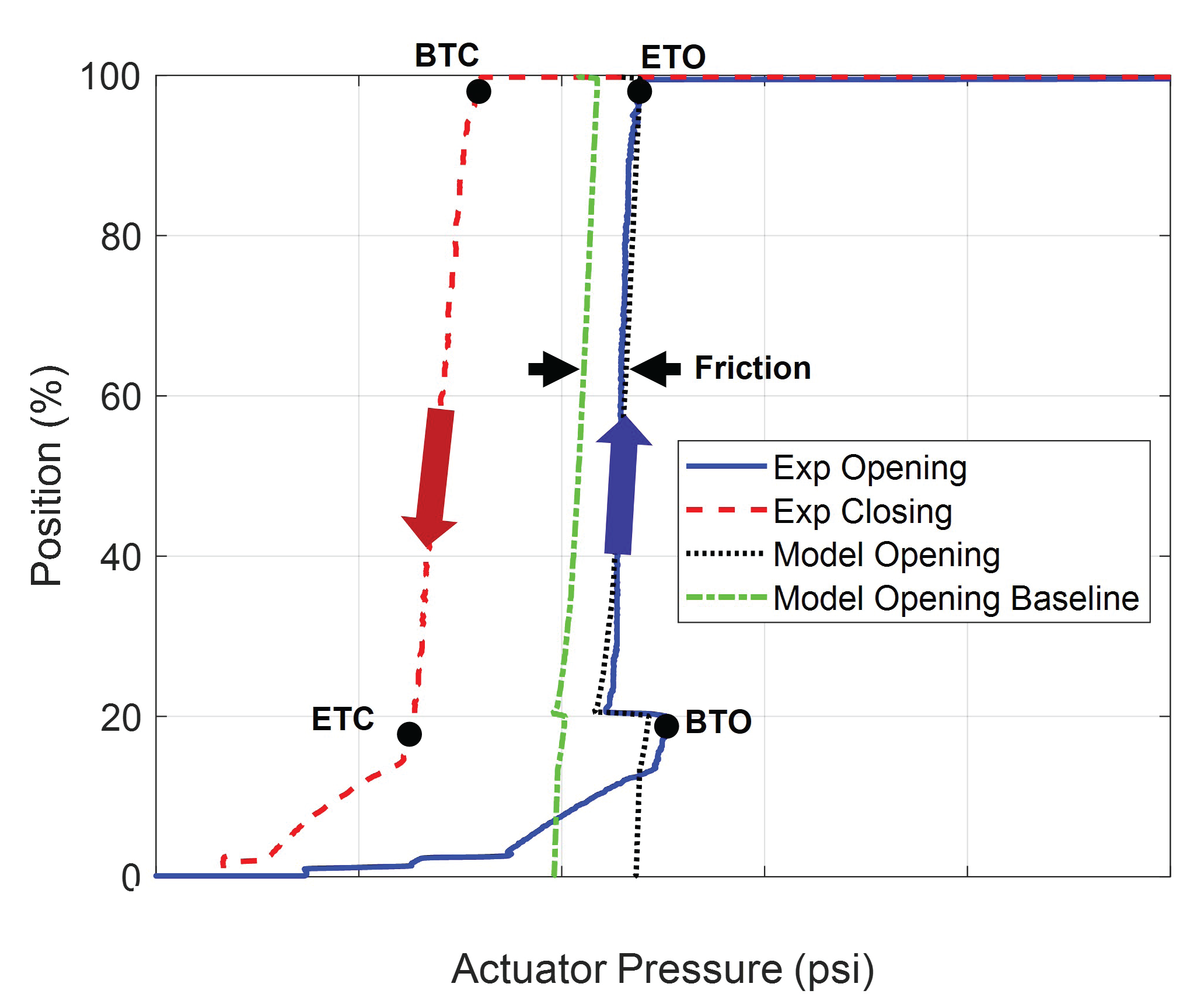
System Validation
Validation of the smart ESD system hardware and analytics logic has been conducted using a purpose-built unit tested at a Stream-Flo test facility. The unit emulates an actual field setup and includes control elements to operate the electro-hydraulic power unit and sensors to measure system hydraulic and process line pressure, ambient temperature, and hydraulic reservoir level. The effect of process pressure and ambient temperature on the gate valve, actuator, and control circuit was tested through connecting a compact valve pressurization system and placing the test unit outdoors. The edge controller was used for data logging, processing the system analytics, and sending data through an integrated radio to a personal computer.
Analytics
Sensor data along with baseline data and physics-based models are used to solve key performance indicators (KPIs) of component and system health. Three primary sets of KPIs were evaluated: valve health, control circuit response, and hydraulic circuit leakage. Evaluation of these KPIs is conducted by processing the time-based data for pressure, position, and temperature.
Valve health analytics rely on the actuator pressure versus valve position dataset coupled with physics-based (analytical) model of the valve thrust. This evaluation can be conducted during either full or partial valve stroke cycles to determine the following vital key points during opening and closing: break-to-open (BTO), end- to-open (ETO), break-to-close (BTC), and end-to-close (ETC), as shown in Figure 3 for a full stroke cycle. The evaluation of these four points is critical to determine the available safety margin during opening and closing and predict potential failure to reset or trip the SSV. Also in Figure 3, analytical models show good correlation with the measured data at different operating process pressures, which helps to evaluate valve opening friction.
Evaluation of the control circuit health is based on the incremental response time for each component and/or event during valve opening and closing. During valve closing, this diagnostic is important as it evaluates the system’s ability to ESD upon demand. For example, if the incremental response time of the pressure reducing valve (PRV) exceeds a certain baseline, it can be an indication of a jammed or malfunctioned internal PRV component. This will alert the operator to conduct further investigation while identifying the potential source of the problem.
Leakage in the hydraulic circuit is determined through the analysis of pressure signatures, which is found to distinguish between leakage in the low- or high- pressure control circuits. Figure 4 shows two plots for the leakage indication function distinguishing between (a) leakage in the hydraulic actuator circuit and (b) leakage in the hydraulic control circuit. Ambient temperature is monitored during the leakage emulation to exclude the drop in pressure being attributed to diurnal changes in temperature. The ESD system is programmed to cycle the electric pump once there is a pressure drop below a certain limit, which generates the saw tooth profile shown in the plots.
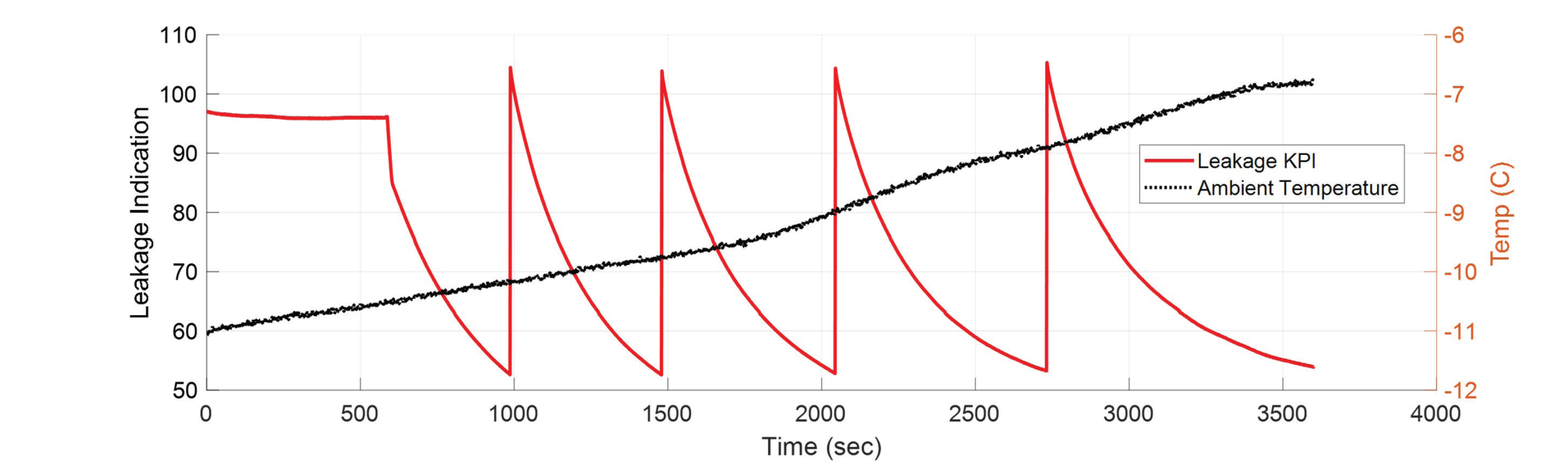
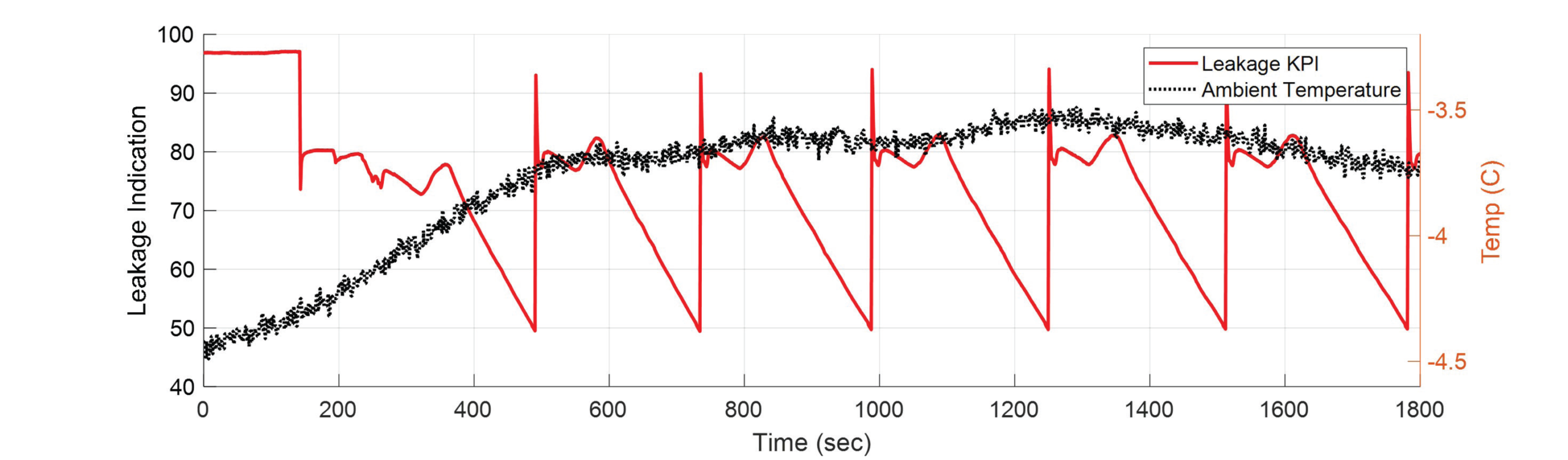
Summary and the Way Ahead
The developed Smart ESD system brings a valuable addition to the current journey towards autonomation of the wellhead. The different elements of the system including the electro-hydraulic actuation, data digitalization, and smart algorithms can reduce the environmental impacts caused by greenhouse gases (GHG), lower operating cost, and improve efficiency. The self-contained hydraulic system with the ability to be solar powered does not interfere with the process fluid and/or generate any GHG emissions compared to conventional gas motors, direct gas, and gas-over-oil systems which rely on process fluids and end up releasing gas pressure after valve operation. In addition, the system can reduce safety incidents by limiting wellsite visits and exposure of personnel to hazardous environments.
The test results for the analytics related to control circuit health, valve health, and hydraulic leakage are promising and pave the way towards achieving a higher maturity autonomous system. The developmental road map for the Smart ESD is applicable to other components on the wellhead and oil & gas facilities that involve process control and health monitoring. Achieving fully autonomous analytics of the wellhead components is a long journey and the ability to establish the highest level of maturity, prescriptive analytics, depends on the availability of physics-based models and historical data. This requires industry collaboration and partnership to generate historical data and validate existing and future models.
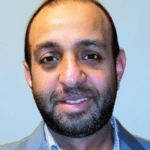