As concerns about Per- and Polyfluoroalkyl Substances (PFAS) contamination continue to grow, the Fluid Sealing Association (FSA) has been actively involved in research and policy development to address the environmental and health risks associated with these persistent chemicals. With pending regulations set to shape the future of PFAS management, Valve World Americas had the opportunity to sit down with Phil Mahoney, the Chairman of Governmental Affairs at FSA to gain insights into the association’s approach, the challenges faced, and the potential impact of these regulations on fluid sealing technologies and industry practices.
By Foster Voelker II, Director of Engineering – Williams Valve
What is a sealing device and where are they used?
In any industrial system, there will be a myriad of equipment used: pumps, agitators, mixers, electric motors, valves, flanges, and piping (not to mention control systems, sensors, etc.). All these devices must be fitted with sealing devices to ensure that what is inside the system does not escape to the air, soil, or water where that system is installed.
A basic definition of a sealing device is: a component or assembly of components that are used to contain a fluid, solid, or gas within a system. They can be used in static, which are two components that do not move relative to each other e.g. two flanges, or in dynamic applications where one component moves relative to another, e.g. a valve or pump.
Figure 1 shows a simplified example of a typical system found in an industrial plant. Every component in the picture contains a sealing device. There are gaskets used to seal statically between two bolted flanges that connect the pipe. The pump will have a mechanical seal to contain the fluid inside the pump as moves fluid through the piping system. The electric motor has seals to prevent ingress of water, dust, and other contaminants. There are expansion joints that allow the piping system to expand and contract with changes in temperature and pressure. Valves typically have compression packing in them to allow the valve to open and close while ensuring the fluid in the system does not escape to the environment.
Sealing devices are often exposed to a wide range of service conditions- full vacuum to extreme pressures (10,000+ psi), extreme temperatures from cryogenic to well over 1,000°F, and aggressive chemicals that can be toxic, explosive, or harmful to the environment.
From the dishwasher or furnace in a home and the hydraulic systems in every commercial airplane, to the electric power generation stations that power homes and businesses, and chemical production facilities, sealing devices are literally found in every possible corner of society.
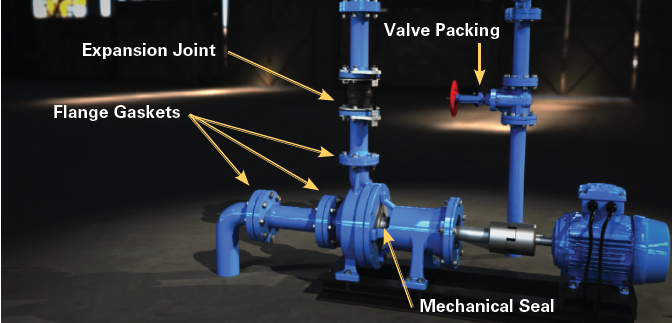
What are the challenges with current legislation & regulatory activities related to PFAS?
The term PFAS is an abbreviation for Per- and Polyfluoroalkyl Substances which are a huge group of over 4,700 chemicals that contain carbon-fluorine bonds. Some of the chemicals under this group have been found to be possibly harmful to human health, and studies are ongoing to better understand levels of exposure and health outcomes.
PFAS chemicals are further classified into two categories: Non-Polymers and Polymers, see Figure 2. Two non-polymer PFAS chemicals, PFOA (perfluorooctanoic acid) and PFOS (perfluorooctanoic sulfonate) have been identified as being a primary concern and studied extensively. These materials have been found to be bio-persistent and have been found in water supplies, soil, and in living organisms. These two materials have driven much of the legislative efforts to regulate PFAS as a group.
One of the most common PFAS materials in the polymer category is PTFE (Polytetrafluoroethylene) as well as several fluoro-elastomers. These materials are regarded as polymers of low concern (PLC’s). They are considered non-hazardous as their properties are distinctly different from non-polymers, and they have a number of chemical properties that make them unique and extremely valuable in a huge range of applications where other materials are not effective.
The concerns with these materials and mitigating their effects on the environment has driven several legislative efforts to regulate PFAS in Europe and at the federal and state level in the U.S. While it certainly makes sense to regulate materials deemed harmful to human health through proper scientific analysis, the challenge with much of the legislation being proposed is that it treats all PFAS the same and assumes all are hazardous.
A more logical, scientific approach needs to be utilized in regulating these materials to ensure those that are safe and non-hazardous are not banned for being lumped under the simple definition of a PFAS. Given the sheer number of PFAS chemicals, it would make sense to group PFAS chemicals that are similar to each other to ascertain the risk of each group. Simply clarifying the definition of a PFAS in the various proposed rules to remove polymers from the definition would be a logical approach.
What are the implications of these regulations for the sealing device industry?
While sealing device manufacturing is not considered a specific ‘industry’ by many typical classifications like aero-space or mining, it is a multi-billion dollar business annually. Every single industry utilizes sealing devices: power generation, water & wastewater treatment, oil & gas production, mining and ore processing, pulp and paper, pharmaceutical, aerospace, and semiconductor production. The list goes on and on.
Fluoropolymers and fluoro-elastomers have unique characteristics that make them critical to the proper performance of sealing devices. Fluoropolymers are unique among all man-made materials in that they are unmatched in oxidation resistance and attack from almost all chemicals. They have excellent durability and stability and do not degrade over time. They have one of the lowest coefficients of friction of any material available today.
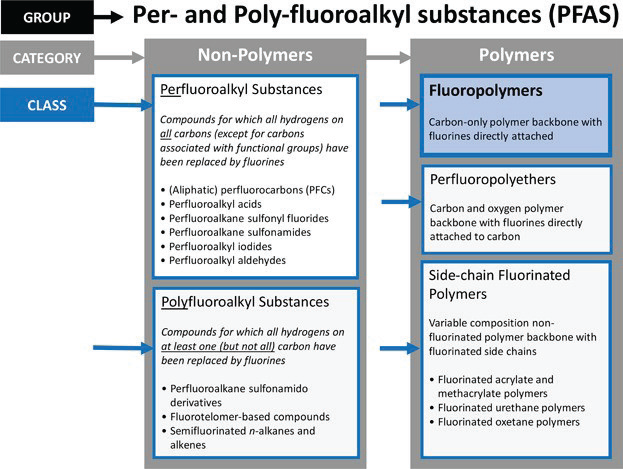
The characteristics of these materials make them an integral part of a wide range of sealing devices. Here are some examples:
- Valves found in refineries must meet very stringent leakage requirements to ensure they do not leak greenhouse gases into the environment. Note that globally, there are millions of valves in service in this sector alone. The current seals used in these valves all use fluoropolymers as a key ingredient to meet these very low leakage requirements; these seals have been rigorously tested to U.S. and international standards. These sealing devices are considered the best available technology in this industry.
- Almost all mechanical seals use o-rings made from various elastomer types to allow the seal to adjust to varying operating conditions and prevent fluid from leaking around the primary sealing elements. While there are many different types of elastomer o-rings available, fluoroelastomers can handle much higher service temperatures and a wider range of chemicals than any other type. Mechanical seals can be installed in very aggressive media at high temperatures- these can be very dangerous and difficult to seal. Without fluoroelastomers as a secondary seal, much of the equipment that uses mechanical seals would not have a viable option to operate safely in these applications.
- Piping systems in all industries are typically fitted with flanges to facilitate easy removal and replacement of different components in the system. Most flanges are fitted with gaskets that are compressed between the flanges to maintain a tight seal thus preventing leakage of media from these connections. These gaskets must be made with materials that resist degradation in aggressive chemicals and a wide range of pressures and temperatures.
- Fluoropolymers are the only materials that can effectively seal in certain applications such as those where strong oxidizers are present. They are also used in applications where very low leakage rates are required or the flanges are made of a unique material that cannot sustain high loads that may be required for other sealing materials (glass-lined pipe for chemical service).
- Expansion joints are sealing devices that allow for the expansion and contraction in mechanical systems as temperatures and pressures fluctuate, thus protecting the surrounding equipment from being overstressed and possibly damaged. Many of these incorporate fluoropolymers and fluoroelastomers to handle the aggressive media that no other material can handle. In metallic expansion joints, fluoropolymers can also be used to line the inside of the device which is exposed to the media, allowing the manufacturer to use commonly available materials to produce the assembly. Without fluoropolymers, the manufacturers would have to use more exotic, harder-to-source metallurgies, and even those options may not be suitable for the application.
What alternative material options are there for sealing devices?
Manufacturers are constantly looking for new, better-performing materials for their product lines. In most of the examples provided above, there are limited or no options currently available to replace fluoropolymers or fluoroelastomers. There may be some discreet alternate technologies for some sealing device applications, but they are not a panacea.
Consider the low emissions requirements for a typical refinery valve. Based on the extensive testing and emissions monitoring programs, the existing sealing solutions that utilize fluoropolymers in some form provide the best sealing performance in valves. Alternate technologies such as bellows could be used on a valve in place of a standard valve sealing device. However as these bellows designs are much more expensive and are much larger, they may not fit into the existing piping systems without heavy modifications. This gets more implausible when you consider the fact that a single refiner may have over 10,000 valves that must meet low emissions performance standards.
The challenge to replace fluoroelastomers in mechanical seals is even more challenging. The companies that produce new elastomer technologies are certainly working on alternative technologies, but at this point in time, there are no known alternatives available to replace them. Just as with valves, bellows technologies are available, but the same challenges with the size of the mechanical seal fitted with bellows and their suitability for the same range of applications as a standard design remains.
How are these challenges being addressed by the users of PFAS?
From the sealing device perspective, the first goal is to educate legislators and regulators on what sealing devices are and the importance of fluoropolymers and fluoroelastomers to the industry. Most of the manufacturers of sealing devices in the Americas are members of the Fluid Sealing Association, which is a trade association founded in 1933. One of the main goals of the FSA is to provide training and education to anyone (end users, material suppliers etc.) on sealing devices of all types (www.fluidsealing.com). In the case of PFAS, the main goal is to highlight the critical nature of the polymers that fall under the definition of a PFAS. Certainly, our members understand and agree with efforts to address the issues specific to well-studied PFAS that have been identified as potentially harmful. At the same time, end users of PFAS polymers are mindful and concerned about the impact of proposals to ban all PFAS materials, including the safe-to-use polymeric materials that are so ubiquitous and essential to industrial applications across all industries.

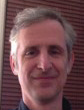