Conveying a substance from one place to another along a tube would be a simple affair if one never needed to control its flow. A single unbroken piece of pipe can be relied upon to do an effective job conveying material without issue, at least until corrosion or human error betrays it. The need to control flow necessitates a valve. This means finding a way to have a valve mechanism move freely across the boundary of the pipe. Suddenly, one is actively introducing rupture where it seemingly does not belong.
By Justin Yule
Sealing and Packing valves is a serious challenge that occupies a position on the front-lines against fugitive emissions and environmental devastation. Ever more stringent environmental regulations, along with demands for high performance and low maintenance, have made the valve packing selection process more critical.
Why Do We Need Sealing and Packing?
Stem-actuated valves use a ‘stem’ to perform its basic function. The stem is a shaft that passes from the interior of the valve, where it does the all-important work of opening or closing the flow of process substance, to the exterior where an operator can actuate the valve, either manually or using an electronic actuator. Whereas other joints in a pipe system can be sealed with a relatively simple gasket, the point of entry of the stem into the valve itself must navigate the cross-purposes of preventing leakage and allowing free movement. As such, much thought has been given to devising mechanism that will solve the conundrum of allowing and disallowing movement of different kinds in the same location.

What is Sealing and Packing?
Control valves generally fall into two main categories which dictate the nature and movement of the valve stem. Sliding stem valves have a stem that moves perpendicular to the flow of the pipe, while rotary stem valves have a stem that rotates around an axis perpendicular to the flow of the pipe. Whether the stem is rotating or moving in and out, its movement is essential to its proper function. Therefore, the valve stem must be held in place with a material flexible enough that it can be compressed against the stem to create a seal, but that also allows for the relatively frictionless movement of the stem. The sealing mechanism, housed within the valve bonnet, generally consists of packing material formed into rings around the stem and packed tightly into the bonnet. A packing flange is then placed against the rings of packing material and tightened with nuts onto the bonnet. This flange places consistent compression force on the packing rings and creates the seal.
For sliding stem valves, a different type of sealing mechanism is possible, one that makes only secondary use of packing materials. A bellows seal is an accordion-like metal tube that encompasses a portion of the valve stem. One end of the bellows seal is attached the stem, and the other is attached to the valve bonnet. The flexible material of the bellows permits the valve stem to move in and out with very little friction while also presenting no point of vulnerability for leakage – it is an uninterrupted piece of metal. A leak detection port placed above the bellows allows for detection of rupture to the seal, and if this occurs, a secondary sealing mechanism of standard packing is present to prevent full leakage.
The Recent History of Sealing and Packing
Before the introduction of legislation to restrict and control dangerous emissions, like the USA Clean Air Act Amendments by the Environmental Protection Agency, valve packing was an under-theorized and under-engineered area of concern. Financial incentives determined that it was generally in the interests of operators to not regularly lose large amounts of process substance out of the valve aperture, but if there were smaller leaks that represented only a negligible percentage of the total, these could be tolerated. Packing ring selection was largely a matter of making sure high-pressures did not blow the packing from the valve and cause major loss. Legislation introduced a new consideration. Even financially negligible amounts of spilled process substance and fugitive emissions can create major environmental and safety concerns, and governments had decided to compel industry to bear this in mind. This intervention initiated new developments in sealing and packing technology that would bring leakage down to a bear minimum while still allowing for the smooth functioning of valves in their basic task of opening and closing. Emissions limits were first brought down to 500 ppm, but have since dropped to 100 ppm, and even 50 ppm in some cases. Innovation was needed.
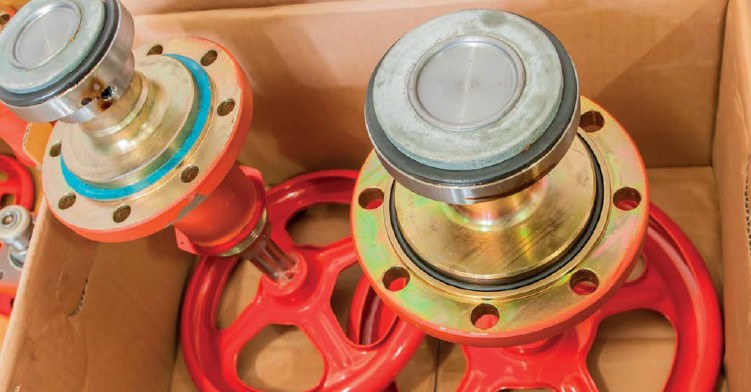
A response to this new challenge has been ‘live loading’. The traditional approach to packing involves packing materials that are compressed by bolts against the valve stem. This is called ‘stationary loading’ or ‘jam packing’. In this set-up, the only elasticity in the system is that of the packing material itself. Normal functioning of the valve wears at and fatigues the material and in turn the packing must be recompressed or replaced. In order to reduce the rate at which the sealing mechanism wears and requires attention, packing is ‘live loaded’. This involves the introduction of springs into the packing assembly that provide sustained compression even as the packing material wears. This can be a simple coil spring or spring-steel washers known as Belleville springs which, when placed in the correct sequence, act as a spring.
What Material Is Used in Packing?
When it comes to the material used in the packing material, Asbestos was considered to be optimal. Asbestos is flexible enough to be woven into rings, suitable for very high process temperatures, and is not conductive of electricity and so not liable to galvanic corrosion. Its classification as a hazardous substance now precludes its use as packing material for modern valves.
The two most common packing materials today are Teflon (Polytetrafluoroethylene, or PTFE) and graphite. Teflon is exceptionally good at creating a tight seal, is highly chemical resistant, and offers an extremely low coefficient of friction. It can be trusted to create a reliable and durable seal. However, it has a limited temperature range, foreclosing some common valve usages, such as at nuclear power plants. The partner to Teflon in packing material dominance is graphite. It has a far greater temperature range than Teflon, and is able to endure harsh nuclear radiation. However, graphite creates more friction against the stem, and permits galvanic corrosion due to its electrical conductivity. As Control Automation adds, ‘sacrificial zinc washers are sometimes added to graphite packing assemblies to help mitigate this corrosion, but this only postpones rather than prevents corrosive damage to the stem.’
Other hybrid packing materials have been developed. Carbon fiber packing combines high strength and high thermal resistance, making it ideal for high-pressure applications. Aramid fiber packing is high-strength and has good abrasion resistance, making it suitable for high-speed rotating equipment.
Key Elements to Consider – Sealing and Packing Solutions
Many factors must be taken into consideration when identifying appropriate sealing mechanisms for valves.
- Identify the pressure and temperature of the process substance;
- Know the valve type, manufacturer, and model;
- Determine the legislated fugitive emissions standard for the process substance.
With these variables in mind, one can seek out the right vendor providing the right packing solution. Manufacturers will provide instruction for installation and maintenance that must be followed in order to achieve optimal performance.
In terms of maintenance, the tightness of the packing nuts on the valve flange is a common point of human error. Care is needed to achieve sufficient packing flange force to create a seal, but not to tighten too far as to over-compress the packing material, leading to excessive friction against the stem and premature packing failure. ‘Valve Packing, the latter scenario [over-tightening] is what one usually finds in industrial settings, where well-intentioned but uninformed personnel over-tighten valve packing in an effort to prevent leaks. The proper remedy for a packing assembly that leaks despite having been properly torqued is the replacement, not further tightening.
REFERENCES
- https://control.com/textbook/control-valves/valvepacking/
- https://www.processingmagazine.com/valves-actuators/article/21248111/simplifying-control-valve-packing-selection
- https://www.arthomson.com/blog/info-1/understandingvalve-packing-13