Fasteners – screws, nuts, bolts, or studs – are used in many industries for structural and pressure-containing applications. Regarding the latter, bolted connections failures in oil & gas facilities are responsible for many serious incidents, such as spills, fires, and loss of life and limb. A common recommendation in many of the incident investigations was to improve the quality system for fasteners. More specifically, to apply to fasteners the same traceability requirements used for other pressure containing parts, such as body castings. Several organizations have already issued standards with more stringent rules regarding traceability for fasteners, such as API and the IOGP. Read on to find what are these requirements and how they affect fasteners used in the valve industry.
By Davi Sampaio Correia, Technical Consultant
Fastener Integrity
Fasteners for valve applications are used both in structural (or load-bearing) and pressure-containing applications. For example, fixing a gearbox to a valve and connecting a body to bonnet, respectively. Reports about fasteners failures in the oil and gas industry, such as references 2 and 3, have shown that failures in pressure-containing applications often have more serious consequences than structural ones. The following is a breakdown of areas where the integrity of a bolted connection might be compromised (for the rest of this article, ‘bolting’ will be used interchangeably with ‘fasteners’):
- Design – wrong load assumptions, lack of provision for cyclic loading, etc.
- Materials selection – Misjudgment of environmental conditions, not acknowledging the dangers of cathodic protection, etc.
- Manufacturing – wrong composition used by mistake, lack (or mishandle) of heat treatment, etc.
- Installation – Failure in torqueing procedures (overload, lack of lubrication, etc.).
- Operation – Lack of inspection and maintenance practices regarding loss of pretension (e.g. loose bolts/nuts) and degradation (e.g. corroded bolts/nuts).
As seen from the list of potential integrity compromises, integrity management of a bolted connection must be upheld for the entire lifecycle of the application. Starting with design, all applicable standards and specifications concerning a particular application need to be reviewed, including loads and environmental factors. Once bolts and related coatings are selected, design integrity relies on a single assumption: that the selected materials will display the mechanical and chemical properties stated in their specifications.
The alloys used in fasteners “can be processed by a variety of methods, and the resultant quality levels depend on the initial chemistry and the processing route. Oftentimes, there is no requirement to track each processing step for a particular fastener. Thus, the pedigree of the material depends on the integrity of the adherence throughout the entire supply chain to qualified manufacturing processes as verified by specified quality assurance methods. Thus, recreating the exact processing steps for fasteners that fail in the field is challenging because there normally is scant traceability of specific processing steps for a specific fastener.”4
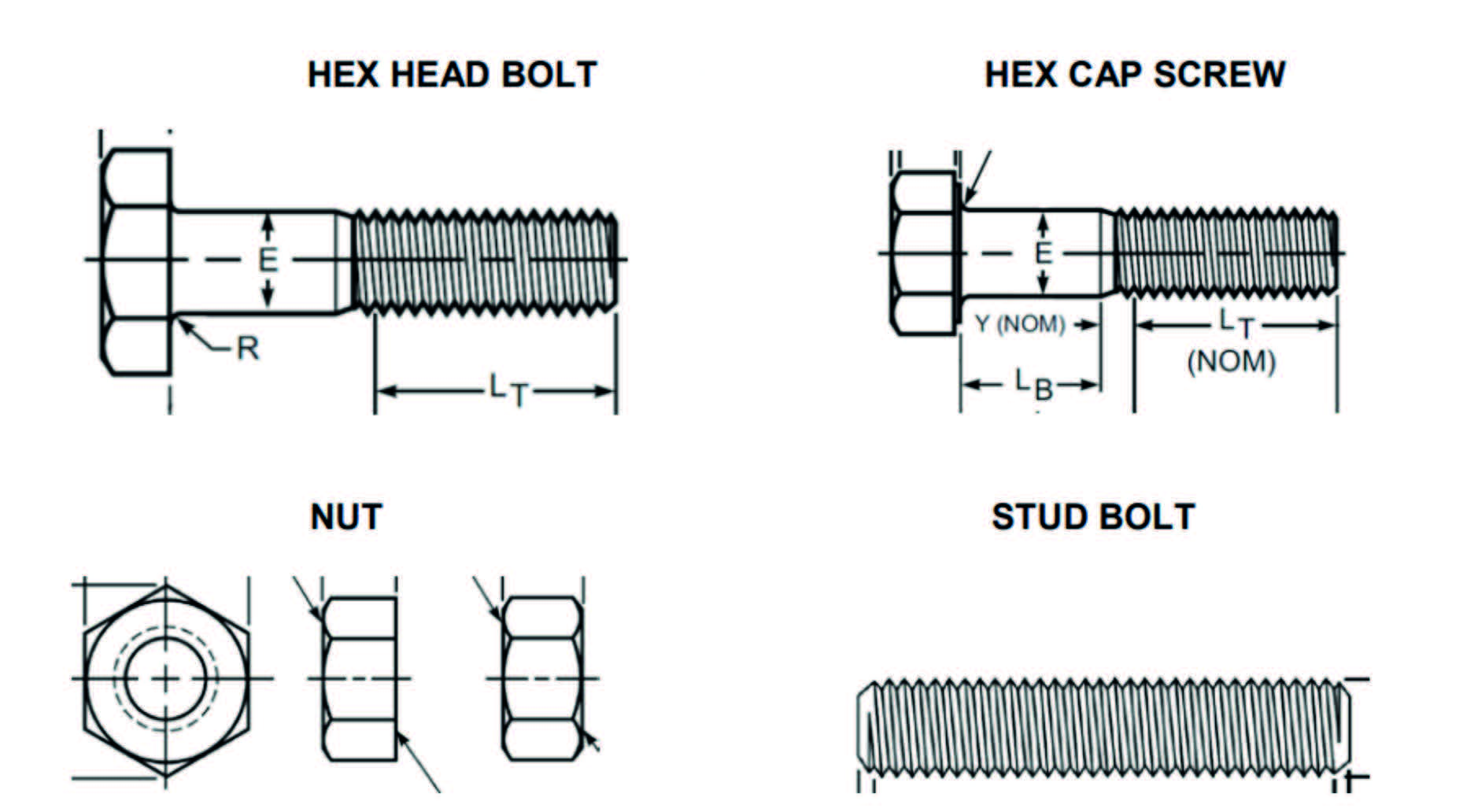
What is Traceability?
For the purposes of this article, traceability refers to the ability to identify and track a product from procurement of raw materials to manufacturing. Traceability requirements are part of a quality system. API, for example, does not formally define traceability in its quality standard, but states that, “the organization shall maintain a documented procedure for identification and traceability while the product is under control of the organization as required by the organization, the customer, and/or the applicable product specifications throughout the product realization process, including applicable delivery and post-delivery activities.”5
Although ISO also does not define traceability in its quality standard,6 the intent becomes clearer. The ISO 9001 standard states that: “The organization shall control the unique identification of the outputs when traceability is a requirement, and shall retain the documented information necessary to enable traceability.”6 So, traceability involves marking parts with unique identification, the ability to match this identification with documentation related to raw materials and manufacturing processes, and keeping those records for a specific period of time.
A third document closely linked to traceability is the EN 10204.7 This document is commonly referred to when inspection plans are being developed. It also defines the different types certificates supplied to a purchaser of metallic products. The EN 10204 defines four levels of documentation, 2.1 and 2.2 (Type 2 documentation) and 3.1 and 3.2 (Type 3 documentation).
When Type 2 documentation (2.1 and 2.2) is chosen, one relies solely on the manufacturer’s quality control capabilities to deliver the properties and composition needed. Type 2.1 provides a statement that requirements were met. Type 2.2 provides the same statement, but with the addition of test results that have not necessarily been taken from the samples collected in the batch/run/heat being purchased. EN 10204 calls this a ‘non-specific’ inspection.
Types 3.1 and 3.2 provide results from a specific inspection, that is, on the products to be supplied or on test units of the products being supplied. For Type 3.1 there is involvement of the manufacturer’s representative, who must be independent of the manufacturing department. For Type 3.2, the manufacturer sends the same representative of Type 3.1, who must liaise with either the purchaser’s representative or an inspector designated by the official regulations.
Types 3.1 and 3.2 certificates are generally much more expensive than Type 2.1 or 2.2, as type 3 certificates interrupt the normal flow of the production line for witnessed tests and inspection. Regarding traceability, the EN 10204 standard includes a note for type 3 certificates that says that the manufacturer must be capable of transferring “relevant test results obtained by specific inspection on primary or incoming products he uses, provided that the manufacturer operates traceability procedures and can provide the corresponding inspection documents required.”7
In conclusion, traceability requires the capacity of correlating between product and raw materials batch, so that test reports for a given batch can be matched with a particular part. However, this does not mean that said part has a unique, permanent identification. See the example of EN 10204; simply asking for a 3.2 does not mean that each part has a permanent marking providing unique identification (as can be seen in Figure 2). If permanent and unique identification of parts are required, end users must state so in the documentation provided during the procurement process. Again, not only the type of inspection documents that are required but also the level of traceability.

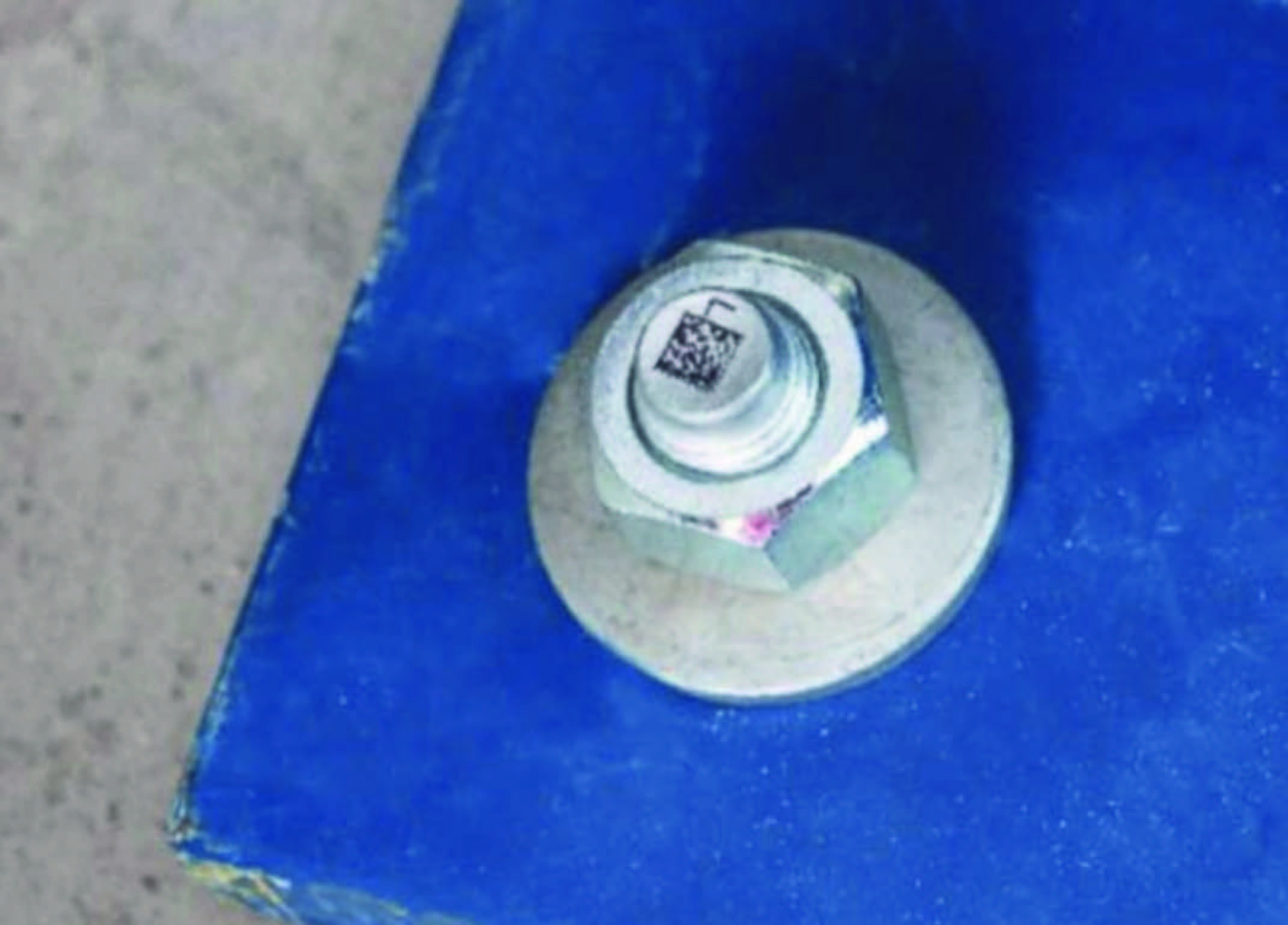
Traceability Requirements for Fasteners Used in Valves
The identification process depicted in Figure 2 is not new to valves; body castings, for example, have been marked with similar codes for a long time. The novelty to note here is the requirement being applied to fasteners for valves in topside applications.
The S-562 (Supplementary Requirements to API Specification 6D Ball Valves) is a publication from the IOGP with a set of supplementary requirements for trunnion mounted ball valves specified according to API Specification 6D Twenty-Fourth Edition, 2014. Ball valves complying with the S-562 have, among other characteristics, more stringent design rules and more extensive testing than a similar valve following only the API 6D.
The S-562 defines pressure-containing part as “a part whose failure to function as intended results in a release of contained fluid into the environment and as a minimum, includes bodies, end connections, bonnets/covers, bolting, stems, shafts and trunnions that pass through the pressure boundary.”
If bolting is considered a pressure-containing part, then follows that it must comply with the documentation requirements for this category of components. Table J.4 on the S-562 (Documentation Requirements) states that inspection document types must follow EN 10204 type 3.1 or 3.2 (according to valve QSL, Quality Specification Level) and one of three possible levels of traceability:
- Level I: Full Traceability – the material is uniquely identified, and its history tracked from manufacture through stockists (where applicable) to the manufacturer and to actual position on the equipment with specific location defined on a material placement record (the traceability to a specific location only applies to skids / packaged equipment).
- Level II: Type Traceability – the manufacturer maintains a system to identify material throughout the manufacturing process, with traceability to a material certificate.
- Level III: Compliance Traceability – the manufacturer maintains a system of traceability that enables a declaration of compliance to be issued by the manufacturer.
The recently revised API 6D (Specification for Valves, 25th edition, 2021) has also been modified to enforce more stringent traceability for fasteners used in pressure-containing applications. “The new edition also now requires pressure-boundary bolting be purchased from suppliers that can ensure they conform to API 20E (carbon steel bolting) and API 20F (corrosion resistant bolting) requirements. The bolting manufacturers do not need to be licensed to these standards; however, it should be expected that majority of the supply would come from such suppliers. In fact, the introduction of API 20E and API 20F into API 6A and API 6DSS, and now also API 6D, the increased demand should drive the suppliers to get licensed and hence improve bolting availability.”8
Compliance with API 20E and 20F means that any bolt 1” nominal diameter, and larger, must be marked with a unique identification that can be linked to a heat lot identification. Traceability for bolting less than 1” in diameter must be securely containerized for the same purpose. With this new requirements, API 6D has similar traceability requirements as the API Specification 6A (Specification for Wellhead and Christmas Tree Equipment), which is used for subsea equipment.
Some industries are already thinking about the next level of traceability for fasteners. Instead of displaying an identification linked to heat number, some fasteners can now be linked to a unique serial number. Anchor bolts are bolts used in civil engineering to connect structural and non-structural elements to masonry and concrete. As can be seen in Figure 3, a company is promoting capability to ensure that “each fastener comes with a data matrix code (DMC)—a sort of QR-style code laser-printed directly on the fastener. This makes every fastener uniquely identifiable and traceable. The ID contains the item number, batch number, and a serial number.”9
Conclusion
For much of its existence, the oil and gas industry regarded fasteners as commodity items. For many applications, that can be indeed an acceptable strategy. However, when the risk of bolting failure is linked to potential harm to people, environment or facilities, better quality systems need to be in place to ensure bolts do have the required chemical and mechanical properties. To this end, organizations such as API and IOGP have updated valve standards requiring more stringent traceability requirements for fasteners.