Reducing fugitive emissions from industrial equipment is essential for sustainability and environmental protection. Valves, notorious for their propensity to leak, are a focal point in emission mitigation strategies. By implementing low-emission packing solutions, industries can significantly reduce emissions and ensure compliance with stringent environmental regulations.
These advanced sealing solutions not only minimize emissions but also reduce the frequency of maintenance and replacements, extending the lifespan of pipeline components and ensuring smoother, more reliable operations. This enhanced reliability and durability directly translates into cost savings, making industrial sealing solutions a vital investment for industrial infrastructure.
By Angelica Pajkovic, Client Specialist, and Josmar Cristello, Applications Engineer – Teadit
Compliance with Industry Standards
Fugitive emissions, the unintended releases of gases or vapors from pressurized equipment, significantly contribute to global greenhouse gas emissions, pose health risks, and result in notable economic losses. According to the Environmental Protection Agency (EPA), 60% of these emissions originate from valves; control valves are often identified as a primary source.
To effectively mitigate these emissions, standards such as API 641 and ISO 15848-1 impose rigorous requirements on valve performance. These standards outline criteria for acceptable leakage rates and the durability of valve packing under various operational conditions. Adherence to these standards not only ensures environmental compliance but also optimizes operational efficiency and reduces the total cost of ownership.
Key Standards:
- API 641: This standard specifies the type of testing requirements for quarter-turn valves to evaluate their fugitive emissions performance. The testing involves mechanically cycling the valve 610 times and thermally cycling it three times, reaching temperatures up to 260°C. Methane is used as the test medium, and the maximum allowable leakage rate is set at 100 PPMv.
- ISO 15848-1: This standard applies to both isolating and control valves. For control valves, it provides various testing procedures, including up to four thermal cycles and 100,000 mechanical cycles. The standard allows for using either methane or helium as the test medium.
In addition to these standards, the EPA mandates refineries under consent decrees (CD) to use packing styles warranted or guaranteed by the manufacturer to remain leak-free for five years. These styles must be tested in accordance with generally accepted engineering practices and standards.
Advanced packing solutions such as Teadit 2848 not only address these environmental and operational challenges but also contribute to substantial cost savings through improved efficiency and reduced maintenance requirements.
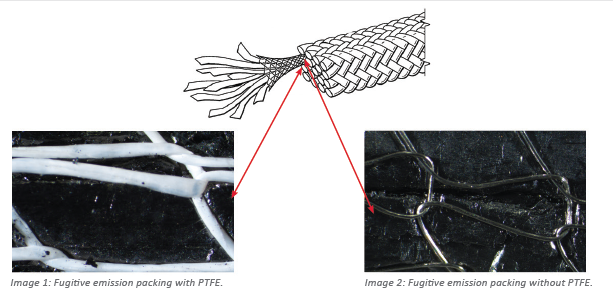
Advancement in Low Emission Packing
The traditional Certified Low Leak Technology (CLLT) packing products typically have flexible graphite, some degree of metal reinforcement, and PTFE. They are typically recognized for easily meeting the low emission (LE) requirements mandated in the API 622, and being approved with valves tested on API 624, ISO 15848-1, and TA Luft standards.
Teadit 2848 packing has been specifically engineered to meet the challenges of fugitive emissions. Utilizing oxidation-inhibited flexible graphite yarn reinforced with a high-strength PTFE thread structure, this innovative packing offers unique ad- vantages for control valves compared to traditional materials such as Inconel wire. Its braiding and materials provide a higher extrusion resistance and significantly lower friction, resulting in extended service life and reduced maintenance costs.
Technical Advantages of Teadit 2848:
- Lower Friction: Replacing the traditional metallic reinforcement with PTFE significantly reduces friction, minimizing wear and tear on valve components and extending their operational lifespan.
- Prevents Shaft Damage: As there is no metal reinforcement, the risk of scoring (damaging) the valve stem is eliminated, which is especially important for control valves due to their frequent operation.
- High Breaking Load: The advanced construction offers more than twice the breaking load of traditional materials, enhancing durability and reliability.
- Extrusion Resistance: Designed to endure installation stresses without requiring anti-extrusion end rings, often necessary for some traditional CLLT solutions.
- Traceability: The Teadit TAGS technology integrated into the product ensures that the packing can be identified, even after use, facilitating efficient maintenance and accountability.
This innovative packing is designed to be self-lubricating and non-hardening, making it suitable for a wide range of applications, including those involving chemical services, and high pressures.
Savings on the Pipeline
Implementing low-emission packing, such as Teadit 2848, has a positive impact on the total cost of ownership (TCO) for industrial pipelines and equipment. By reducing the frequency of leaks, maintenance, and replacements, plants, and refineries can substantially reduce operational expenses.
Reduced Maintenance Costs:
- Longer Service Life: By preventing leaks and reducing friction, the packing helps maintain the integrity of valve stems and other components, prolonging their operational lifespan and reducing the need for replacements.
- Minimized Downtime: Fewer maintenance interventions and replacements mean pipeline operations can continue with minimal interruptions, leading to enhanced productivity.
- Enhanced Reliability: The packing’s performance and reliability reduce the risk of unexpected failures and leaks, ensuring smooth and continuous pipeline operations.
- Improved Operational Efficiency: Lower emissions and friction contribute to the smoother and more efficient operation of valves and other equipment, which can result in energy savings and optimized performance.
Inventory Management:
- Versatility: The packing’s ability to perform effectively in a wide range of applications reduces the need for multiple packing materials, simplifying inventory management and reducing costs.
- Standardization: Using a single, high-quality packing product for various a plications allows for standardization across operations, leading to more efficient procurement and reduced inventory carrying expenses
Proven Performance
Extensive testing of Teadit 2848 packing has confirmed its high-quality performance. Friction tests showed the 2848 packing has 40% lower friction at room temperature than packing styles with no PTFE. This friction reduction is even more pronounced at higher temperatures. Field tests conducted in petrochemical plants have validated these laboratory results, showing dramatic reductions in fugitive emissions over 20 months.
For instance, a valve with a problematic leak was reduced to just 0.2 PPMv after installing Teadit 2848 packing. These significant reductions highlight the environmental benefits and emphasize the economic advantages, including decreased emissions-related fines and lower maintenance expenses.
Adopting innovative sealing solutions that use advanced technologies significantly impacts the TOC for industrial operations. The enhanced reliability and performance of engineered packing contribute to a reduction in overall operational risks, leading to more predictable and manageable costs. This outcome can be seen when considering the impact of improved sealing capabilities on environmental compliance and sustainability goals.
Environmental Compliance:
- Regulatory Adherence: Compliance with API 641, API 622, API 624, ISO 15848-1, and EPA requirements ensures that companies avoid fines and penalties associated with non-compliance.
- Sustainability Goals: Reducing fugitive emissions aligns with corporate sustainability goals, enhancing the company’s reputation and potentially leading to incentives or subsidies for environmentally friendly practices.
Economic Impact:
- Lower Operational Costs: The reduced need for maintenance, replacements, and downtime directly translates to lower operational costs.
- Increased Efficiency: Enhanced efficiency and reliability of pipeline operations lead to improved productivity and profitability.
Final Thoughts
Teadit’s 2848 packing represents a cutting-edge, reliable, and cost-efficient solution for industries aiming to reduce their environmental impact and comply with stringent emissions standards. Its advanced design and high performance ensure a reduced total cost of ownership, making it an optimal choice for control valve applications. By integrating Teadit 2848, companies can achieve substantial savings and operational efficiency, paving the way for a more sustainable and economically viable future.
Key Takeaways
- Teadit 2848 packing significantly lowers stem friction and reduces packing wear.
- The packing meets and exceeds API 641 and ISO 15848-1 standards.
- Field tests confirm substantial reductions in fugitive emissions.
- Adoption of Teadit 2848 can lead to significant environmental and economic benefits.
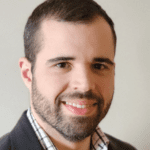