Although the danger of neglecting regular maintenance may not be obvious right away, in an emergency shut down situation, neglected actuators could put both the facility, and the workers at risk.
By Ivy Davis
For day-to-day operations, actuators control the flow of products depending on the needs of a facility. In emergency situations actuation allows valves to be turned on and off from a remote location. This ensures that operators are out of harm’s way and allows a critical situation to be addressed quickly. It is therefore essential that the actuators not only be tried and tested before use, but that a maintenance plan with protocols for repair and replacement be in place.
There are 5 key reasons for preventative maintenance of actuators.1
1. Increase the reliability of actuators in-use.
2. Identify problems before damage to the actuator is incurred, or operability is affected.
3. Reduce overall maintenance costs.
4. Opportunity to make small repairs reducing the likelihood of major shutdowns. Schedule large repairs to convenient times.
5. Control and predict costs thus allowing for realistic budgeting.
The risk of critical failure is reduced by simply ensuring that an actuator is, first, able to provide accurate result and work well for the application in question, and second, has a maintenance plan.
Types of Actuators
To fully understand the importance of actuation maintenance, an operator must first know:
1. What service is the actuator in:
a. Liquids or Gas.
2. What is the power supply to move the actuator?
a. Pneumatic, Electric, Hydraulic, Direct Gas, Gas over Oil.
3. What the actuator is doing in terms of movement?
a. Linear, Quarter Turn, Multi Turn.
4. What function is the application serving?
a. On/Off, Modulating, Shut Down, Emergency Shut Down, Emergency Open.
As the answer to these questions varies based on the type of actuator that is being employed, it is best to address these questions by looking at the various types of actuators specifically; they vary according to the type of energy that drives them. Each type has its advantages and understanding the differences can help maintenance engineers reduce downtime and cost.2
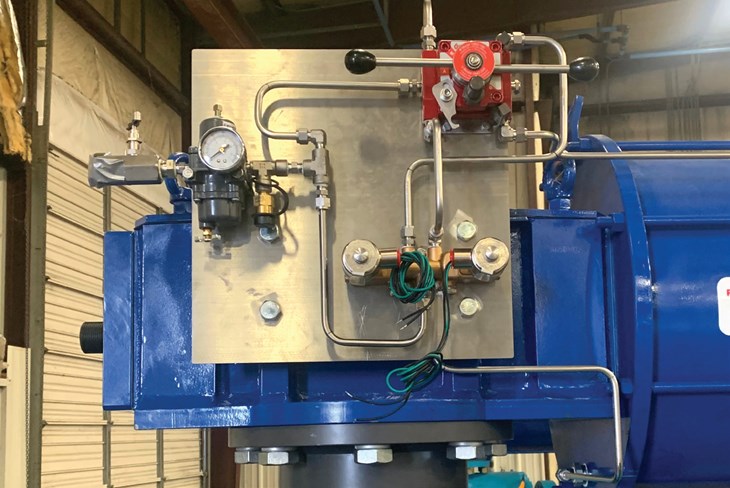
Pneumatic Actuators
For instance, a pneumatic actuator, which is one of the most widely used actuators, is known for its reliability, efficiency, and safe source of motion control; it is often trusted in instances where there is a fire or ignitions risk. Pneumatic actuators are well suited to a wide variety of application types, and service many different industry areas. They are reliant on the presence of some form of pressurized gas or compressed air entering a chamber where pressure moves a piston. They are also extremely durable and can, therefore, reduce the costs required to maintain their performance. Less maintenance means a longer product lifecycle and therefore greater output.3
Electric Actuators
Electric actuators use electrical power to actuate a valve. Compared to their pneumatic and hydraulic counterparts, electric valve actuators provide an energy-efficient, clean, method of valve control. This type of actuation is the first choice for most oil and liquids applications. They are ideal for general process valve automation, non-critical applications, and light duty modulating applications (generally up to 1,200 starts per hour), although some can modulate continuously up to 3,600 starts per hour.4 There are various types of electric actuators.
Multi turn electric actuators use electrical energy to open or close valves through a gear mechanism that allows for a stem nut to be turned multiple times. These actuators usually require the highest degree of maintenance because of the number of cycles and the wear and tear on these actuators. In some applications these actuators can see extreme heat or cold and vibration. Quarter turn electric rotary actuators use electrical energy to open or close valves and dampers through a 90 degree motion (or a quarter turn). Quarter turn valves and dampers are some of the easiest to automate and are used in a number industrial applications.
Electric actuators can include a battery back up in an external enclosure to provide for fail safe operation. The fail-safe battery backup unit is added to supply electricity to the actuator in the event of power failure. In most cases a solar panel or wind turbine is added to keep the batteries charged. These secondary systems add additional maintenance items to check.
Spring return electric actuators can be used in quarter turn, and linear applications. The main operating principle involves using the energized actuator to oppose the motion of a spring, resulting in a buildup of potential energy. Upon de-energization (loss of power), the potential energy in the spring is released, instantly sending the valve to its fail position (fail closed & fail open). These valve actuators are used in small valve critical automation applications where fail-safe functionality is required and space is at a premium.
An electro-hydraulic actuator is an actuator that operates a valve via pressured hydraulic fluid. Its main source of energy, however, is electric power. The supplied electric power is used to energize a motor that runs a hydraulic pump which then supplies the pressurized fluid to operate a hydraulic actuator for the control of the valve. The complete system is self-contained which eliminates the need for a separate hydraulic power unit, simplifying the system construction and improving safety and reliability.5 The electro-hydraulic actuator, it is often used to carry heavier loads in compact spaces. These actuators provide precision and accuracy which is why they are the primary choice in emergency shut down applications.
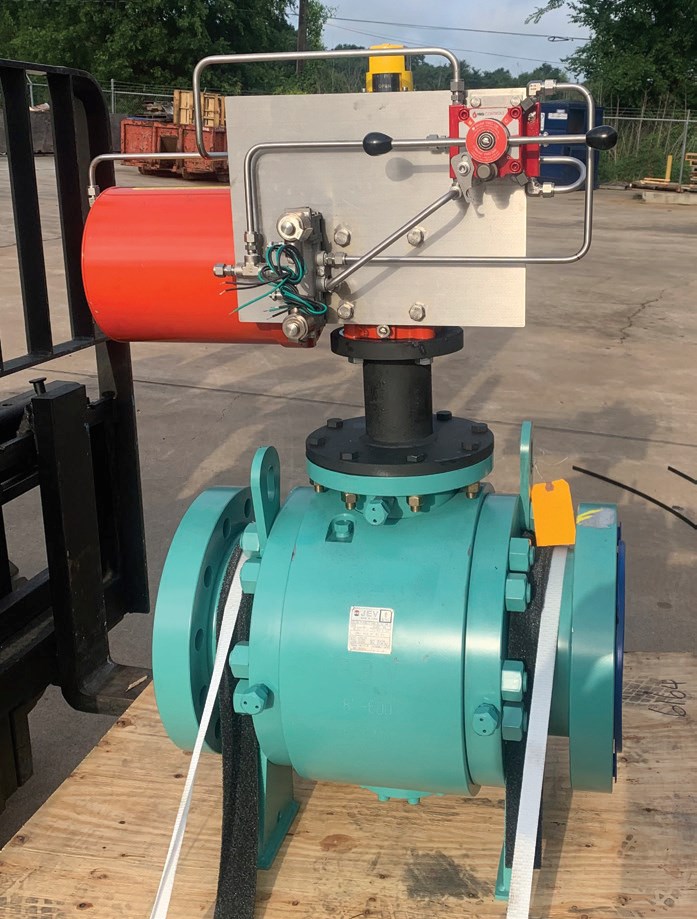
Hydraulic Actuators
Hydraulic Actuators, employ hydraulic pressure to drive an output member and are used where high speed and large forces are required. Offshore installations and upstream applications are the primary users of hydraulic actuators. In these environments, the space and weight-saving benefits of the small cylinders are significant enough to offset the higher costs and risks associated with the use of high-pressure hydraulic fluids. Onshore applications will primarily require hydraulic actuation only when extremely high torques or operating speeds are required by a specific application.
Lack of maintenance of hydraulic systems is the leading cause of component and system failure. The foundation to perform proper maintenance on a hydraulic system has two areas of concern.
The first area is preventive maintenance. The second area is corrective maintenance, which in many cases can cause additional hydraulic component failure when it is not performed to standard.6
Gas-Powered Actuators
Direct gas actuators are built to provide long and efficient service with minimum maintenance. Typically, they are used in remote areas, ideal for pipeline applications where no external sources of motive power are present, and provide a robust heavy-duty design and long service life. This makes them the actuator of choice for installation in remote or unmanned facilities.
Gas-over-oil actuators utilize pipeline gas which is piped into a tank and used to displace the hydraulic fluid in that tank, which is subsequently piped to the actuator power cylinder.
“The maintenance of an gas/oil actuator depends on the manufacturer. For the most part it is checked to ensure that the proper amount of fluid is in the tanks, all tubing and connections are leak free, filters are replaced, and cylinders seals are tested for leaks or blow by,” explained Mike Vaughn, Director of Sales at DONSOL.
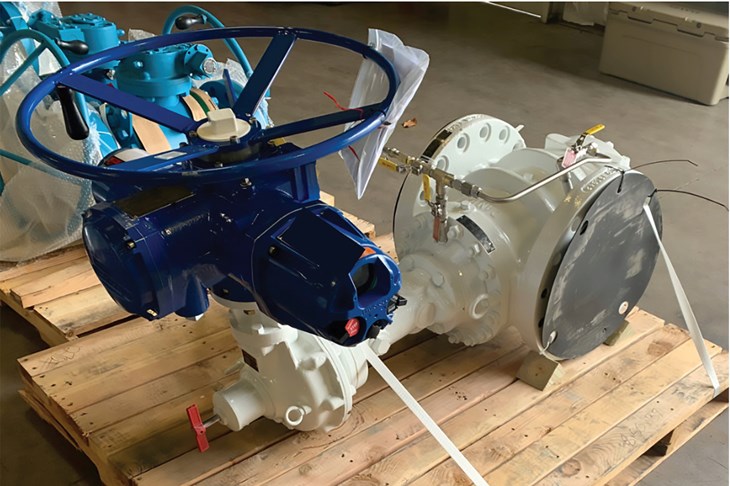
Benefits of Continuous Maintenance
When the correct application has been chosen, and testing and limits are properly set, a well-maintained actuator could last decades. If actuators are not maintained, there is an inherent risk that it could malfunction at any point. In some instances, an actuator can be pulled and repaired once an issue is detected by up-to-date maintenance. In more remote and high-profile locations, such as offshore vessels and platforms, new actuators are installed when an issue is detected.
Some of the essential tips to maintaining an actuator include:
• Maintaining the right amount of grease for motor actuators that use grease for lubrication. Inadequate lubrication is one of the most common culprits to motor actuator malfunction.
• A visual inspection of the external surfaces can reveal minor problems that can be resolved immediately to prevent further damage.
• Establish a benchmark versus optimal torque profiles. Use historical data as your basis.
• Inspect the motor and watch out for connection issues and possible moisture ingress.
• Finally, schedule a regular maintenance of your hydraulic cylinders. Check for corrosion, pitting, or uneven wear.
Regular and continued maintenance on actuators will increase reliability and prevent major shutdowns. If you are able to maintain actuators, then just like the vehicle you drive, it will last decades and be reliable. However, if you choose to ignore maintenance then the risks and cost will come at a high price.
Continuous maintenance could potentially save lives and property in the event of an emergency shut down and at a minimum will reduce costs by controlling the flow of product through valves.
REFERENCES
1. https://www.processindustryforum.com/article/preventativemaintenance-guidelines-actuators
2. https://www.mromagazine.com/features/themaintenanceengineers-guide-to-industrial-actuators/
3. https://www.processindustry forum.com/article/what-is-a-pneumatic-actuator
4. https://www.flowserve.com/sites/default/files/2018-05 (FLSVA-EWP-00005-EN-EX-US-0518-Actuation_Ty_pe Advantages LRI.pdf)
5. https://www.cowandynamics.com/blog/what-is-anelectrohydraulic-actuator/
6. mps://reliabilityweb.com/articles/entry/maintenance of hydraulic systemsOactuators/gas:poweredactuators-ldg
ABOUT THE AUTHOR
Ivy Davis began her career in 2007 with a Bachelors of Business Administration in Marketing from Texas Lutheran University. She was awarded the ‘Outstanding Marketing Award’ for the highest GPA in her graduating class and has since excelled as a marketing professional. Ivy continues to pursue her passion for marketing and regularly consults with organizations to facilitate marketing plans for exponential growth in their industry. She has worked in Houston, Texas for the last decade and focuses predominantly on the oil & gas and technology sectors.