Valves, as critical components of fluid control systems across various sectors, have witnessed significant advancements over the years. Innovations in materials and design have led to more efficient, durable, and cost-effective valve solutions.
By Foster Voelker II, Director of Engineering – Williams Valves
A notable example in the refining sector is the implementation of Certified Low Leak Technology, initially driven by environmental regulations and eventually adopted by industry standards, which has drastically improved fugitive emission performance. This trend continues with recent developments in valve technology, including the integration of smart materials like Shape Memory Alloys and Magnetorheological Elastomers, as well as advanced manufacturing techniques like additive manufacturing, which are driving the industry toward even greater efficiency and innovation.
Traditional Challenges in the Valve Industry
The valve industry has traditionally faced several challenges, including high operational costs due to expensive materials and complex mechanisms, frequent maintenance needs, material limitations, and difficulties in achieving precise control. Valves, reliant on mechanical parts, are prone to wear and tear, leading to costly maintenance and downtime. Material constraints often restrict valve performance in high-temperature and corrosive environments. Increasing regulatory scrutiny due to environmental concerns adds to the complexity. Safety issues, complex installation processes, and slow response times further complicate valve operations. Innovations in smart materials and additive manufacturing are ad[1]dressing these issues, offering more efficient, durable, and cost-effective solutions. The integration of Shape Memory Alloys (SMAs) and Magnetorheological Elastomers (MREs) is revolutionizing the valve industry.
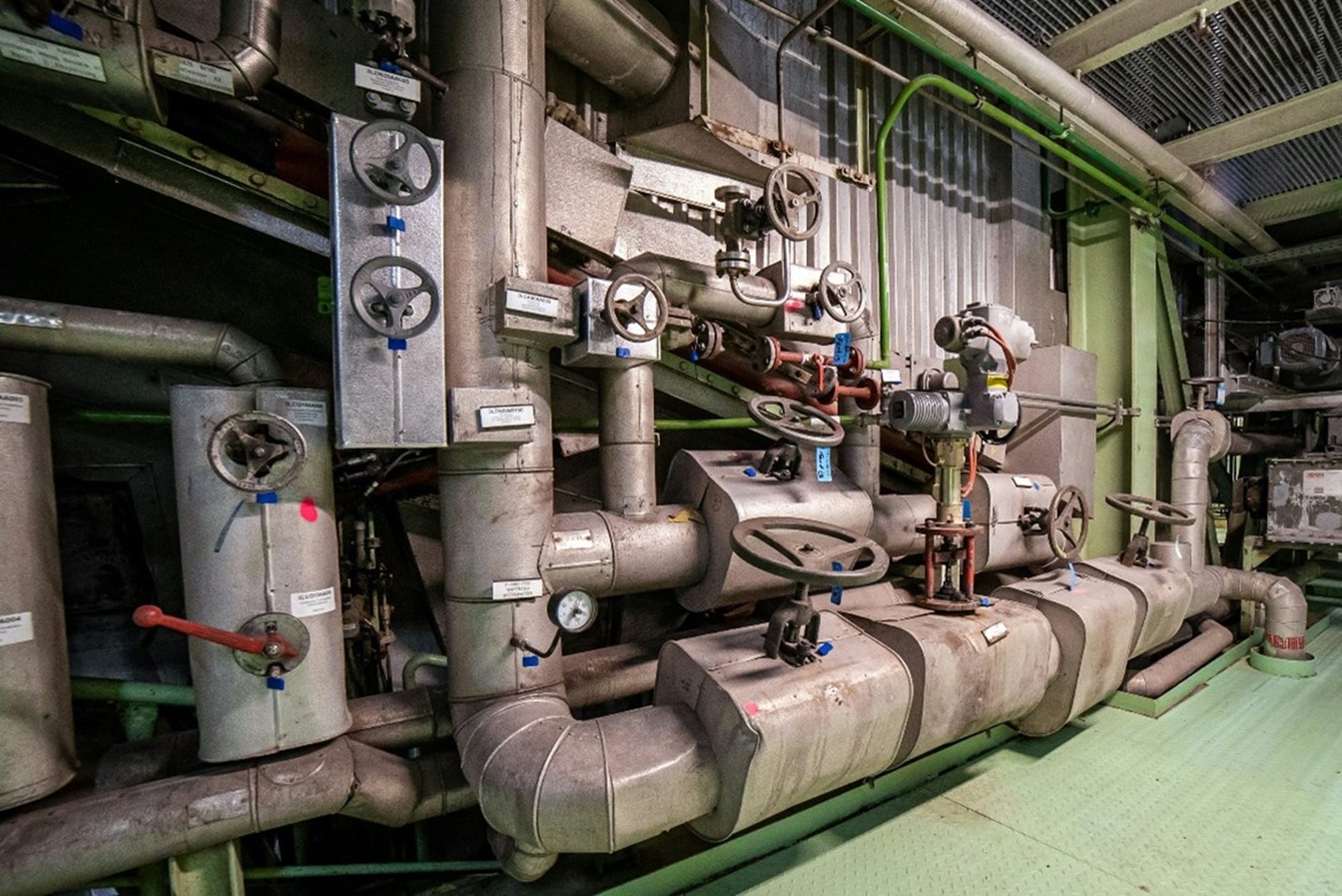
Shape Memory Alloys
SMAs are a class of smart materials known for their ability to return to a predetermined shape when subjected to thermal, electrical, or magnetic stimuli. The most commonly used SMA is Nitinol, an alloy of nickel and titanium. SMAs exhibit two distinct phases: martensite (low-temperature phase) and austenite (high-temperature phase). The transformation between these phases allows SMAs to undergo significant deformation and recover their original shape upon heating. This property enables high actuation force and precision, making them ideal for high-temperature and precision control valves in industries such as aerospace and healthcare. SMAs facilitate compact, lightweight designs by eliminating bulky mechanical components, thus reducing material usage and installation costs.
In a study by Zaman et al. (2023), an SMA spring-actuated valve was developed for high-temperature applications, aiming to replace traditional electro[1]mechanical actuated valve mechanisms with lighter and less expensive actuators. The research demonstrated that an SMA spring-actuated valve could significantly reduce both cost and weight compared to conventional valves. The SMA springs generated a maximum force of 3.2 N and achieved the fastest actuation time of 2.85 seconds with a current of 10 A. The final valve assembly offered a cost reduction of over 30% and a weight reduction of more than 80%.1
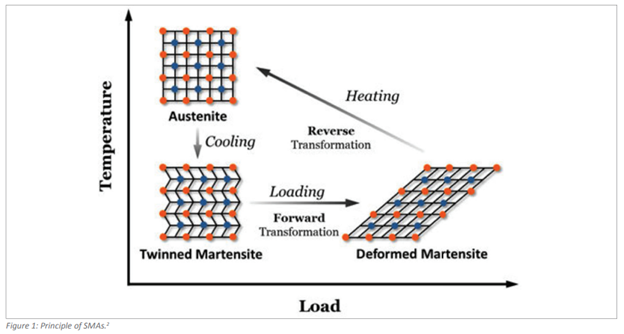
Magnetorheological Elastomers
MREs, composed of magnetic particles in a flexible matrix, offer tunable stiffness and damping properties under an external magnetic fi eld. This adaptability enhances durability and reliability while providing rapid response times, making MREs suitable for proportional control valves and adaptive damping systems in robotics, automotive, and industrial applications.
A research study recently published in Advanced Intelligent Systems by Wang et al. (2022) developed an innovative MRE-based proportional valve for soft pneumatic systems, utilizing magnetorheological elastomers that adjust stiffness and damping properties in response to an external magnetic fi eld. In their study, Wang et al. demonstrated that the MRE-based valve could achieve precise control of fluid flow with a significantly improved response time of under 0.1 seconds.3
The MRE valve, made from compliant MRE and silicone materials, offers several key advantages, including real-time adaptive control, enhanced durability, rapid response times, and reduced maintenance needs. With a cost well below USD $5, it is significantly cheaper than its industrial counterparts. Its simple, no-moving-parts structure ensures better mechanical robustness, ease of manufacture, and compatibility with both pneumatic and hydraulic systems. The valve also provides high accuracy in the lower-pressure region (below 40 kPa), making it ideal for soft robotic applications. Additionally, its versatile applications span the automotive industry for adaptive suspension systems, industrial automation for precise fluid regulation, aerospace engineering for efficient control systems, and medical devices for improved fluid management.3
This study showcases the potential of MRE-based valves to address traditional challenges, offering a versatile, efficient, and reliable solution for modern industrial needs.
Additive Manufacturing
Additive manufacturing, commonly known as 3D printing, has revolutionized the manufacturing landscape by allowing the creation of complex geometries that were previously impossible or highly impractical with traditional manufacturing techniques. This technology has significant implications for the valve industry, particularly in prototyping and producing custom valve components.
A case study on the design of an additively manufactured hydraulic directional spool valve presents a compelling example of how 3D printing can be utilized in the valve industry. The study focuses on the development of a hydraulic spool valve using additive manufacturing techniques, specifically selective laser sintering (SLS).4
The primary advantage of using additive manufacturing in valve design is the ability to produce intricate internal structures that enhance the valve’s performance. For instance, the hydraulic spool valve designed in this case study features optimized fluid channels that reduce pressure drop and improve flow characteristics. Additionally, the use of lightweight materials in the 3D printing process contributes to a significant reduction in the overall weight of the valve.
Furthermore, additive manufacturing enables rapid prototyping, allowing for quick iterations and testing of different designs. This flexibility can accelerate the development process and lead to more innovative and effective valve solutions.
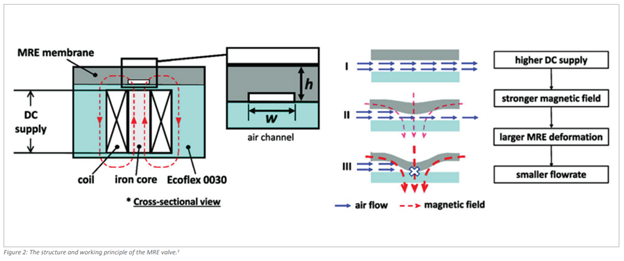
On the Horizon
The future of valve technology lies in the continued exploration and integration of smart materials and advanced manufacturing techniques. Research and development in these areas are likely to yield even more innovative and efficient valve solutions. Ongoing advancements in material science could lead to the discovery of new smart materials with enhanced properties, further expanding their applications in the valve industry.
Additionally, improvements in additive manufacturing technologies, such as multi-material printing and higher resolution, will enable the production of more complex and functional valve components. The synergy between smart materials and additive manufacturing holds the promise of creating valve systems that are not only highly efficient but also adaptable to a wide range of industrial applications.
Conclusion
The valve industry is undergoing a transformation through advancements in materials and manufacturing technologies, addressing traditional challenges such as high costs, maintenance, material limitations, and precision control. Innovations such as SMAs and MREs are revolutionizing valve design by offering high actuation force, precision, tunable stiffness, and enhanced durability. Studies by Zaman et al. (2023) and Wang et al. (2022) highlight significant improvements in cost, weight, and response times using these smart materials. Additive manufacturing further enhances these innovations by enabling complex, optimized designs and rapid prototyping. The future of valve technology lies in the continued integration of smart materials and advanced manufacturing techniques, as well as other innovations, promising highly efficient, reliable, and adaptable solutions for diverse industrial applications.