As operators in the oil & gas industry, it is vitally important to optimize the performance of control valves to maximize efficiency and profitability while maintaining safety and reliability. Usually, during a turnaround or maintenance, control valves need to be replaced or upgraded to maximize efficiency and profitability. In the past century, there have been many technological advancements in medical science, artificial intelligence, autonomous flying vehicles, and more.
By Kyle Daniels, President & CEO, Clarke Valve
Globe Valves in the 21st Century
The pressure from the government to prevent emissions from releasing into the atmosphere in the oil & gas industry is ever-increasing. As the requirements to stay within the regulatory limits for methane emissions become stricter, the demand for a valve that does not leak, requires no adjustments or maintenance on the packing and measures 2 parts-per-million, increases.
Attempting to achieve net zero operations while utilizing globe control valves can cause setbacks to an entire organization’s methane target dates. The conventional globe valve design was patented at a time in which environmental protection efforts were not a top priority, and the core of the original design has seen little change since its inception. Typically, these types of valves record a methane leakage rate of ~500 ppm, and the most common solution to reducing the leakage rate is to have maintenance personnel tighten the stem packing during inspection periods. This method only marginally reduces emissions and does require constant attention and maintenance visits, which is costly and inefficient.
New valves, such as the Dilating Disk™ Valve, are becoming a move viable solution for upgrading relatively inefficient leaky, and high-maintenance globe valves in the field.
Rather than improving on existing designs, engineers have seen the benefits of engineering from the ground up. This clean sheet approach resulted in a long-overdue change in valve design that achieved the first-ever recorded methane leakage rate of 0 ppm in the field. It also provided a centralized flow path that greatly reduces cavitation, precision flow control capabilities, and a more compact and lightweight package than traditional globe valves. One of the critical elements that set new designs apart from traditional globe valve designs is its patented stem seal technology, a redesigned stack of spring-energized seals that prevent methane from escaping the valve and eliminates the need for field adjustments. This was a major factor in earning the valve its ISO 15848-1 and API 641 certifications with A-ratings, which have leakage rate standards of 50ppm or less.
Valve Trend Data
Valve trend data is an important metric for end users and control valve manufacturers. Valve trends are data points, based on electronic signals taken from the valve positioner and the control room, taken at regular time intervals. In this case, the end user is collecting valve position data points once a day. Although the valve cycles many times throughout the day, an end user can verify that the control valve is moving to the correct position through daily measurements. As noted in the data, the valve trends are a near-perfect match between the signal, which is the control room data point, and the valve position (actual), which is the valve positioner data point. This is what end users and valve manufacturers are looking for when reading valve trend data. The better the match between signal and position, the more accurate the valve, and the better the process is being managed by the control valve.
The reason a control valve has to change position so often can vary from process to process. Typically, the main reasons a control valve will change position is to precisely adjust the temperature, pressure, or flow rate of a process. Without the ability to precisely control these variables, it would be impossible to produce high-quality, high-purity chemicals such as gasoline, natural gas, or even drinking water.
By following all applicable industry standards for control valves and adhering to the most rigorous standards for quality, it is not only precision that is important, but also safety, reliability, and as always, zero emissions.
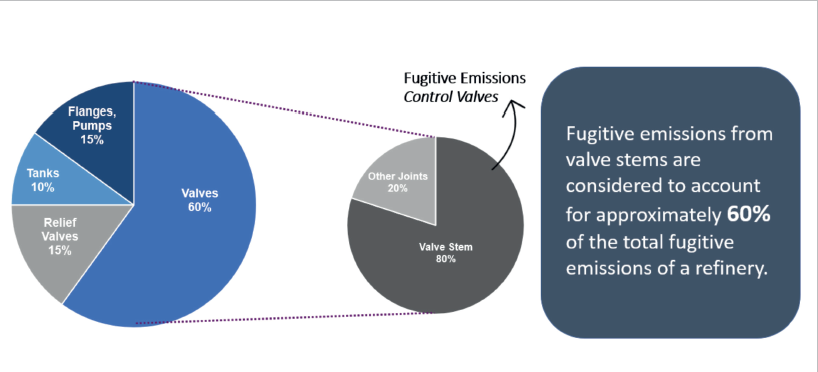
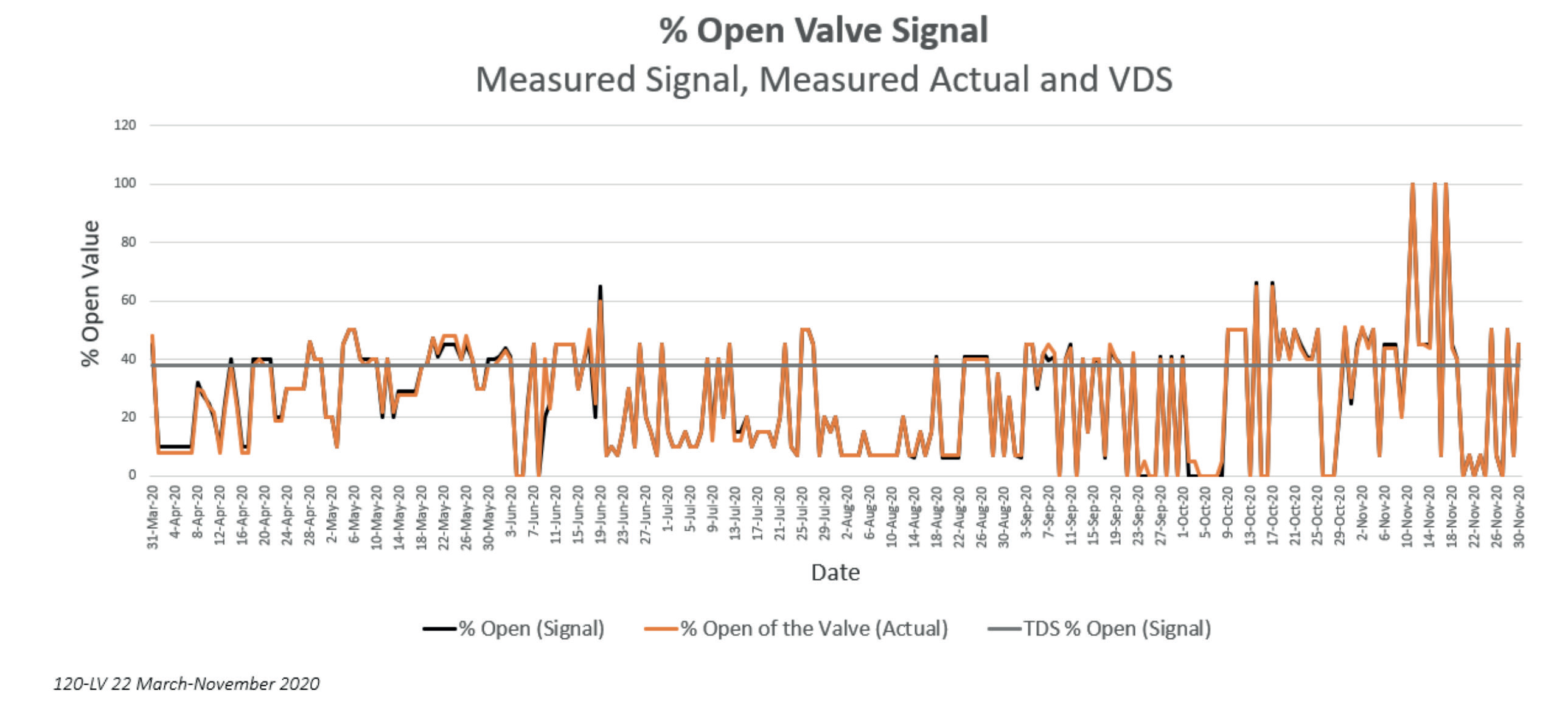

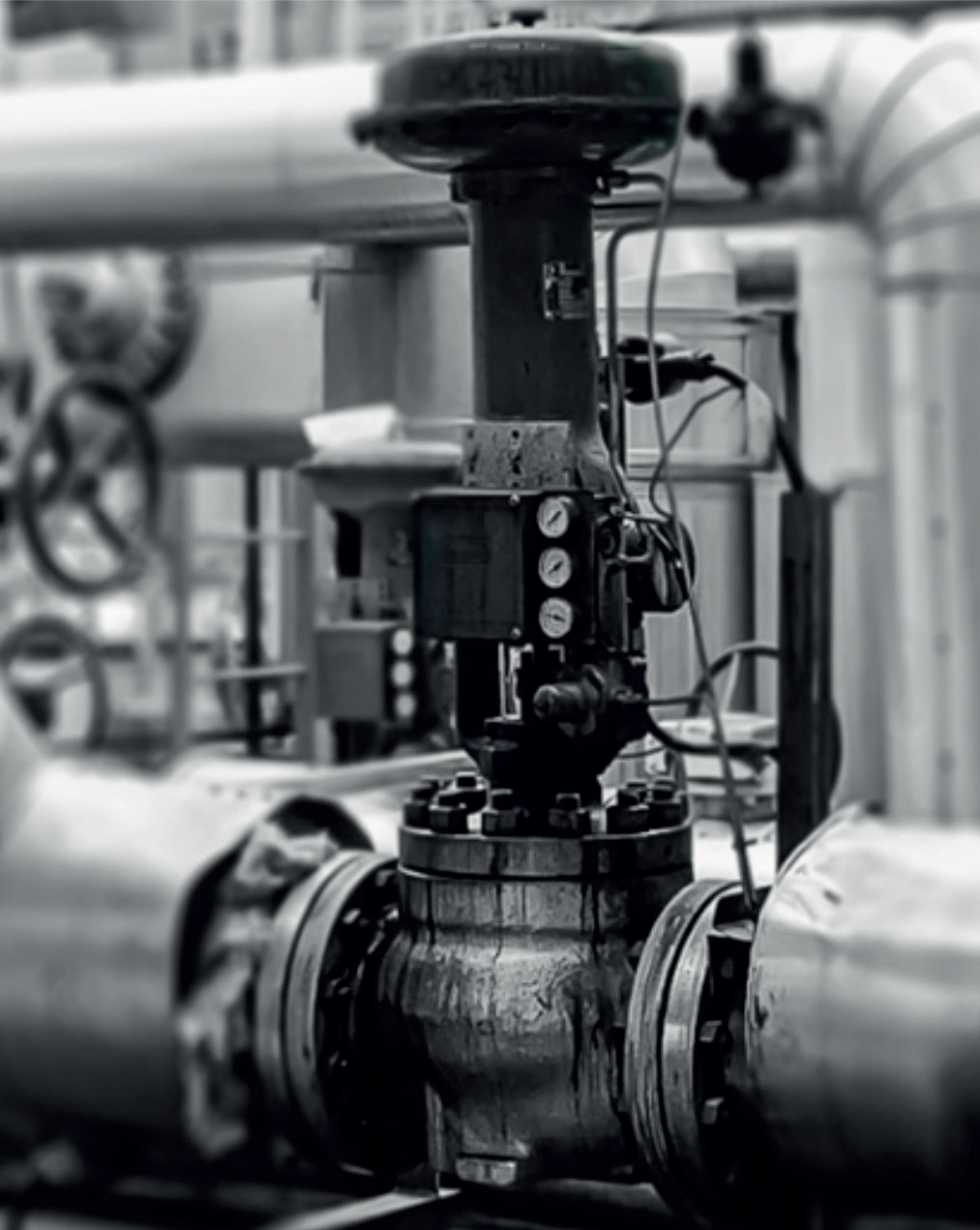

Case Study
The Dilating Disk Valve technology has been field-proven across various downstream oil & gas applications. In February of 2020, five legacy globe control valves were replaced with DDVs in five different applications within the same refinery: raw oil, stabilized oil, water, natural gas, and amine. The goal of this project was to monitor the process control performance of the valves and to measure the fugitive emissions output so that the results could be compared to the valves that were replaced. Over the last two and a half years, all of these valves have measured 0ppm, with zero adjustments and zero maintenance required.
This is why new solutions are becoming more and more desirable; they offer a plug-and-play, field-proven, and reliable replacement option for globe valves. The reimagined design brings operations into the 21st century and allows organizations to take control of methane emissions in the field. By committing to replacing legacy hardware with low emission 21st century technology, the oil & gas industry can make major strides in minimizing the emissions that leak from its facilities.
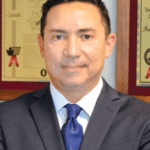
References:
- https://www.linquip.com/blog/control-valves/
- https://www.wermac.org/valves/valves_control-valves_principles-of-operation.html