By Karan Sotoodeh – Baker Hughes
Localized Corrosion Types
Corrosion is a costly issue. Crevice, pitting and stress cracking corrosion are forms of localized attacks which can occur with steels used in seawater systems[1]. Pitting corrosion causes the formation of cavities, spots or pits on the metal surface, as the name implies[1],[2].
Crevice corrosion has a very similar mechanism to pitting corrosion, with a less severe effect that can form from crevices[1],[2]. Chloride stress cracking corrosion (CLSCC) is defined as the cracking of the metal due to localized corrosion such as pitting which is combined with applied or residual stress in the presence of a chloride containing environment such sea water[3].
All of these corrosion types can occur internally due to the seawater fluid service in piping systems and/or externally through contact with the marine offshore environment. Figure 1 illustrates crevice and pitting corrosion types on a stainless steel surface which is being tested in a seawater and chloride containing environment. Figure 2 illustrates a mixture of pitting and stress cracking corrosion in a bolt.

Material Selection for Seawater Services
A combination of three parameters: stress, poor material selection and a corrosive environment results in stress cracking corrosion (SCC). A combination of susceptible material and corrosive environment excluding the stress leads to pitting and crevice corrosion types.
Thus, the most common strategy to mitigate the risk of localized corrosion is to select suitable materials. That is the reason the NORSOK[4] standard has specified that “Seawater corrosion resistant materials shall be used for seawater systems, taking into account that most seawater for process use is chlorinated.”
Titanium piping and valves are widely used in the Norwegian offshore industry in corrosive sea water services[4],[5]. Alternative materials such as 25 chromium super duplex maybe used for deaerated seawater piping or in seawater with maximum 20°C operating temperature[4],[5]. Deaerated (oxygen free) seawater and seawater with maximum 20°C operating temperature are not categorized as corrosive. Sea water is used for cooling or fire extinguish purposes.

NAB vs Titanium for Cost Savings
NAB instead of titanium valves were probably used for the first time in the Norwegian offshore industry during the Edvard Grieg project in 2012 to 2014. The Edvard Grieg oil field is located in the North Sea, 35 km south of Grane and Balder fields and at a water depth of 110m[6]. The main reason for replacing the titanium valves with NAB was to save cost.
Titanium is the most expensive alloy used for piping and valves in the Norwegian offshore industry. Nickel Aluminium Bronze (UNS C95800) is a copper alloy containing 4.5% nickel, 9% aluminium, iron, manganese and copper[4]. NAB cost is higher than carbon steel and cast iron and lower than super duplex, nickel alloy and titanium[7].
Chart 1 compares relative cost of materials for piping systems given by a major bulk piping supplier in 2015. NAB and copper nickel are the cheapest materials after carbon steel and low temperature carbon steel. Titanium costs between 14 to 17.5 times as much as NAB. Butterfly valves are very common in seawater systems for both throttling (fluid control) and on-off flow purposes[8],[9]. Thus, the change in materials strategy from NAB to titanium affects valves the most.

Mechanical Strength
NAB has the advantage of a higher mechanical strength compared to titanium. Allowable stress for the body of the valves in forging or casting can be simply defined based on the below criteria given in ASME B31.3, Process Piping Code[10].
Allowable Stress = (2/3 * Yield) or (1/3* Tensile) whichever is lower Titanium Tensile and Yield are 50Ksi and 40Ksi respectively[10], and the allowable stress is calculated as lower of (2/3 * 40 = 26.7) or (1/3 * 50 = 16.67), which is 16.67 Ksi. NAB Tensile and Yield are 85Ksi and 50Ksi respectively, and the allowable stress is calculated as lower of (2/3 *50 = 33.3) or (1/3 * 85 = 28.33), which is 28.33 Ksi.
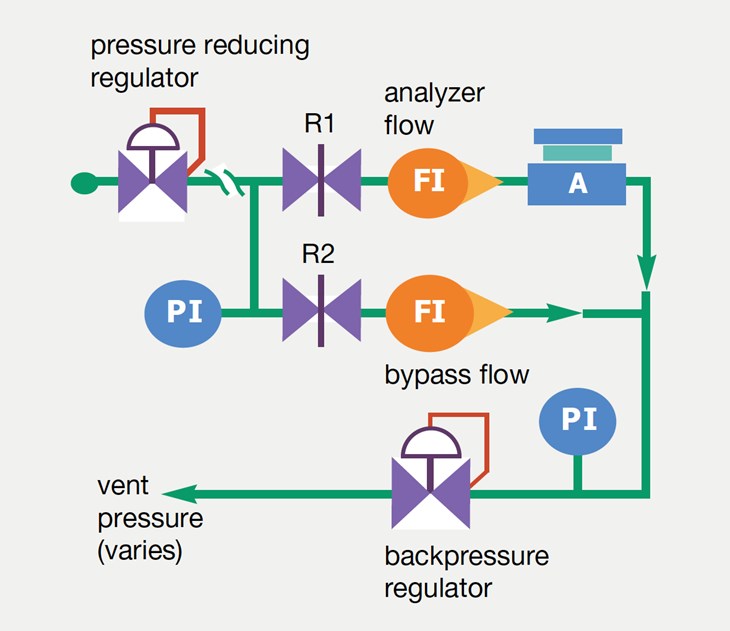
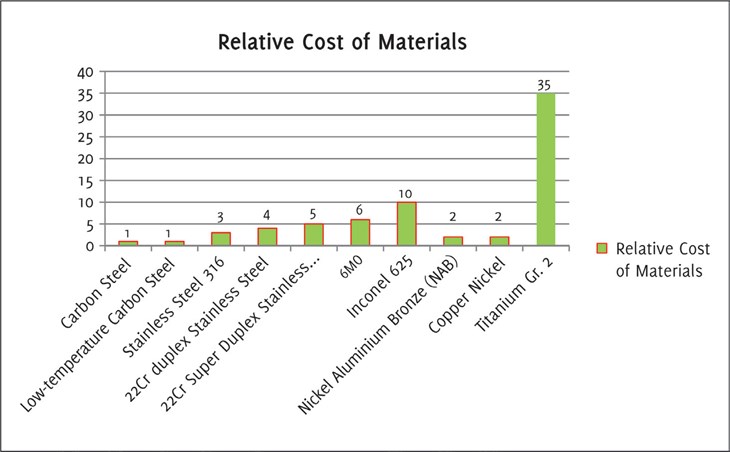
Pressure-Temperature Rating
Seawater services are mostly used in low pressure classes such as CL150 equal to pressure nominal of 20Barg[11]. ASME B16.34[11] provides Equation #1 for calculation of pressure rating of materials as follows:
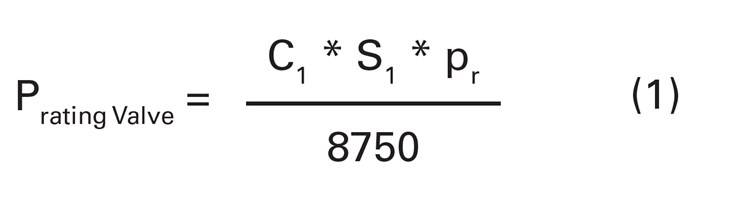
C1 = 1, For Class 150 Pr = 115, S1 = Selected Stress of lower between 60%* Yield & 1.25*25%* Tensile
For NAB, Tensile Strength = 85000 psi & Yield Strength = 35000 psi
S1, Selected stress is the lower of:
1: 60% × Yield = 60% × 35000 = 21,000 psi
2: 1.25 × 25% × tensile = 1.25 × 25% × 85000 psi = 26,560 psi
Thus, S1 = 21,000 Psi
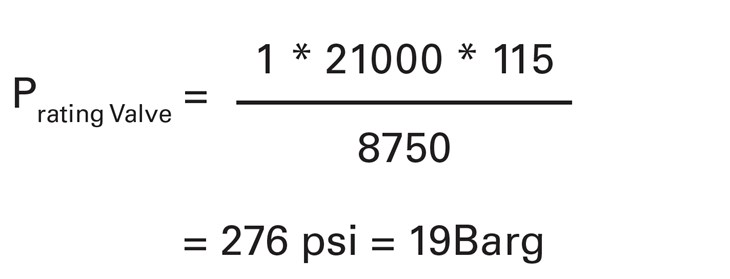
For titanium, Tensile Strength = 50000 psi & Yield Strength = 40000 psi
S1, Selected stress is the lower of:
1: 60% × Yield = 60% × 40000 = 24,000 psi
2: 1.25 × 25% × tensile = 1.25 x 25% × 50000 psi = 15,625 psi
Thus, S1 = 15,625 Psi

The results of the calculations show that NAB in pressure class 150 can withstand higher pressure compared to titanium.
Any pressure value above 14.16Barg and lower than 19Barg requires CL300 titanium piping, valves and flanges which increases the weight and cost of the valve.
Corrosion Comparison
Table 1 compares corrosion performance of titanium and NAB based on 3 types of corrosion: general, pitting and crevice[7]. The corrosion values are from number 1 as the lowest corrosion resistance to 10 as the highest. Titanium has an excellent performance in a corrosive environment such as seawater services. NAB is not as good as titanium but has very good resistance to general corrosion as well as pitting and crevice corrosion.
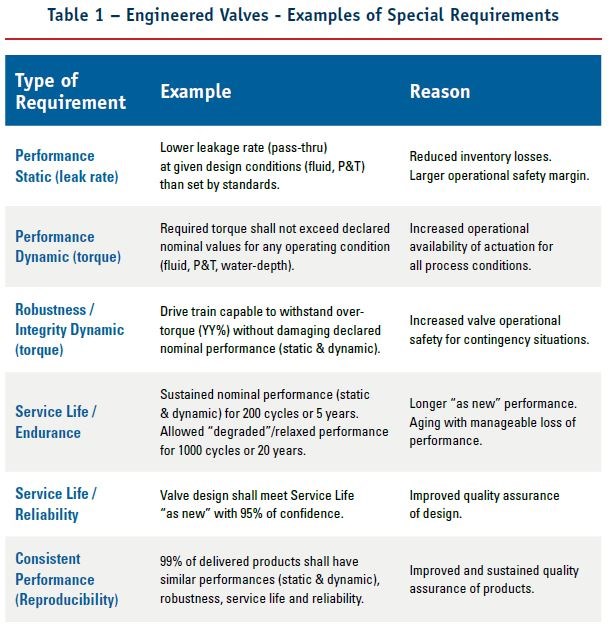
Conclusion & Recommendation
NAB and titanium are two material alternatives for valves in seawater fluid service. Titanium has excellent corrosion resistance to seawater but it is the most expensive material for piping systems in the offshore industry. The price of titanium is almost 17 times of NAB and 35 times of the carbon steel. On the other hand, NAB has very good corrosion resistance to seawater with advantages such as high mechanical strength (allowable stress) as well as higher pressure-temperature rating compared to titanium. This paper proposes using NAB instead of titanium regarding the mentioned advantages.
However, two points should be considered for usage of NAB valves. The first one is that NAB valves are used with GRP (Glass Reinforced Plastic) piping. Fabrication, stress analysis and supporting challenges related to GRP piping should be taken into account. The other parameter is the weakness of NAB in polluted sea water and possibility of H2S (hydrogen sulphide) formation due to microbial activities inside the sea water.
REFERENCES
1. GREEN D. W. & PERRY R. H. (2008). Perry’s Chemical Engineers’ Handbook (8th ed). New York, NY: McGraw- Hill Education.
2. Aluminium Plant and Vessel Company (2008). APV Corrosion Handbook. New York, NY: SPX Corporation.
3. National Association of Corrosion Engineers (NACE) MR0175-ISO 15156 (2001). Petroleum and Natural Gas Industries – Materials for use in H2S – Containing Environments in oil and gas productions (1st ed). Geneva, Switzerland.
4. NORSOK M-001, (2014). Material Selection. 5th edition, Lysaker, Norway.
5. NORSOK L-001, (2017). Piping and Valves. 4th revision, Oslo, Norway.
6. Norwegian Ministry of Petroleum and Energy (2018). Edvard Grieg. [online] Available at: https://www.norskpetroleum.no/en/facts/field/edvard-grieg/
7. STRANG J.R.C. (2009). Nickel-Aluminium Bronze for Seawater: Flattered by Comparison. [online] Available at: http://www.valve-world.net/pdf/vw1009_materials_shipham.pdf
8. SOTOODEH K. (2018). Why are Butterfly Valves a Good Alternative to ball valves for Utility Services in the Offshore Industry? American Journal of Industrial Engineering. Vol.5, No.1, pp 36-40
9. SOTOODEH K. (2018). Selecting a Butterfly Valve Instead of a Globe Valve for Fluid Control in a Utility Service in the Offshore Industry (Based on an Industrial Experience). American Journal of Mechanical Engineering. Vol.6, No.1, pp 27-31.
10. American Society Of Mechanical Engineers (ASME B31.3). (2012). Process Piping. New York, NY.
11. American Society Of Mechanical Engineers (ASME B16.34). (2004). Valves- Flanged, Threaded, and Welding End. New York, NY.
About the Author:
Karan Sotoodeh works as Senior/Lead Engineer-Valves and Actuators for Baker Hughes in Høvik, Norway. He has 14 years of experience in piping engineering in Iran and Norway and working with European valve manufacturers in EPC projects. Karan has a Master’s Degree in Oil and Gas Engineering and a Master of Research Degree in Mechanical Engineering from Robert Gordon University of Aberdeen.