In recent years, the hydrogen industry has gained significant attention due to the growing interest in clean energy sources. As the demand for hydrogen continues to rise, it is important to also address potential safety considerations associated with industrial valves used in hydrogen service. In this rapidly evolving industry, safety requires key considerations such as material selection, design validation testing, and fugitive emissions testing.
By Tom King, Director – Quality, Vendors & Auditing – MRC Global
Hydrogen, the smallest of all molecules, holds immense potential as an energy source. Hydrogen valves play a pivotal role in controlling the flow of this highly flammable gas to maintain the protection of personnel, equipment, and the environment.
Valve Selection
Selecting appropriate valve types is crucial for safety and reliability in hydrogen service applications. Commonly used valve types for hydrogen service include ball valves, globe valves, and check valves. Ball valves are ideal for on/off service and provide excellent shut-off capabilities, making them well-suited for hydrogen isolation applications.
With their precise flow control and throttling capabilities, globe valves are often used in hydrogen systems where flow regulation is necessary. Check valves play a vital role in maintaining the integrity of hydrogen systems by preventing backflow and safeguarding system safety. Adherence to industry standards such as API 600, API 602, and ASME B16.34 is essential when selecting valve types for hydrogen service for compatibility and performance.
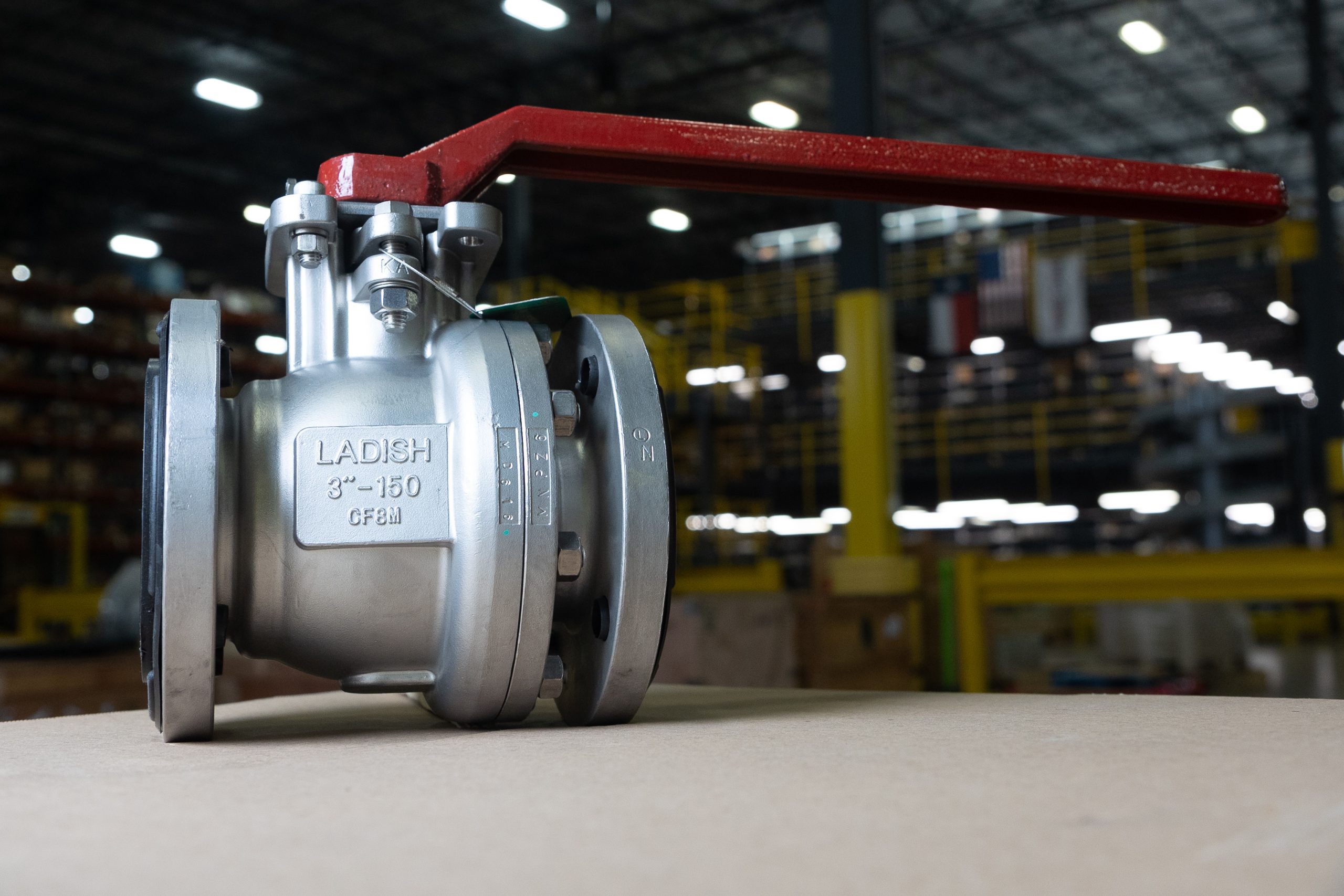
Base Materials
Choosing the right materials for valves in hydrogen service is crucial for safety and reliability. Commonly recommended materials for hydrogen service include stainless steel (ASTM A351 CF8M), nickel- based alloys (ASTM B564, N10276), and titanium (ASTM B348). These materials exhibit high resistance to hydrogen embrittlement and are well-suited to withstand the unique challenges posed by hydrogen service conditions. Industry standards from organizations such as ASTM International, American Petroleum Institute (API), and American Society of Mechanical Engineers (ASME) provide valuable guidelines for material selection and compatibility in hydrogen service.
Design Validation & Testing
Safety is paramount, particularly in the context of hydrogen valves designed to withstand the unique challenges associated with handling this volatile gas. These valves must exhibit the ability to handle high pressures, prevent leaks, and maintain efficient flow control to mitigate the risks associated with hydrogen, safeguarding both human lives and valuable assets.
Confirmation of their functionality through design validation testing for industrial valves in hydrogen service is crucial to make certain that they are reliable under demanding operating conditions. Recommended types of tests for validation include engineering design calculations and simulations, pressure testing to assess structural integrity and leak tightness at high pressures, and cycling of the valves in simulation-type testing scenarios. Automation is recommended during cycling to reduce safety concerns for personnel.
“Confirmation of their functionality through design validation testing for industrial valves in hydrogen service is crucial to make certain that they are reliable under demanding operating conditions.”
There is a growing trend in pneumatic testing over hydrostatic testing for valves in hydrogen service due primarily to the potential for water to impede very small, microscopic defects at lower pressure testing or due to water contamination within certain valve designs. Using an inert gas substitute may provide a higher level of sensitivity in testing. Functional testing under similar operational conditions using media such as clean dry air, nitrogen, helium, argon, or even hydrogen itself should be performed by professionals well-versed in associated hazards.
Bunkers should be considered for higher pressure pneumatic testing. Cryogenic testing is essential for validating the functionality of valves at low temperatures, particularly for hydrogen service. Compliance with industry standards such as API 598 and ASME B16.34 for valve design and testing is crucial, but additional testing times and methods beyond standard limits are commonly seen to provide extra assurance, depending on service conditions.
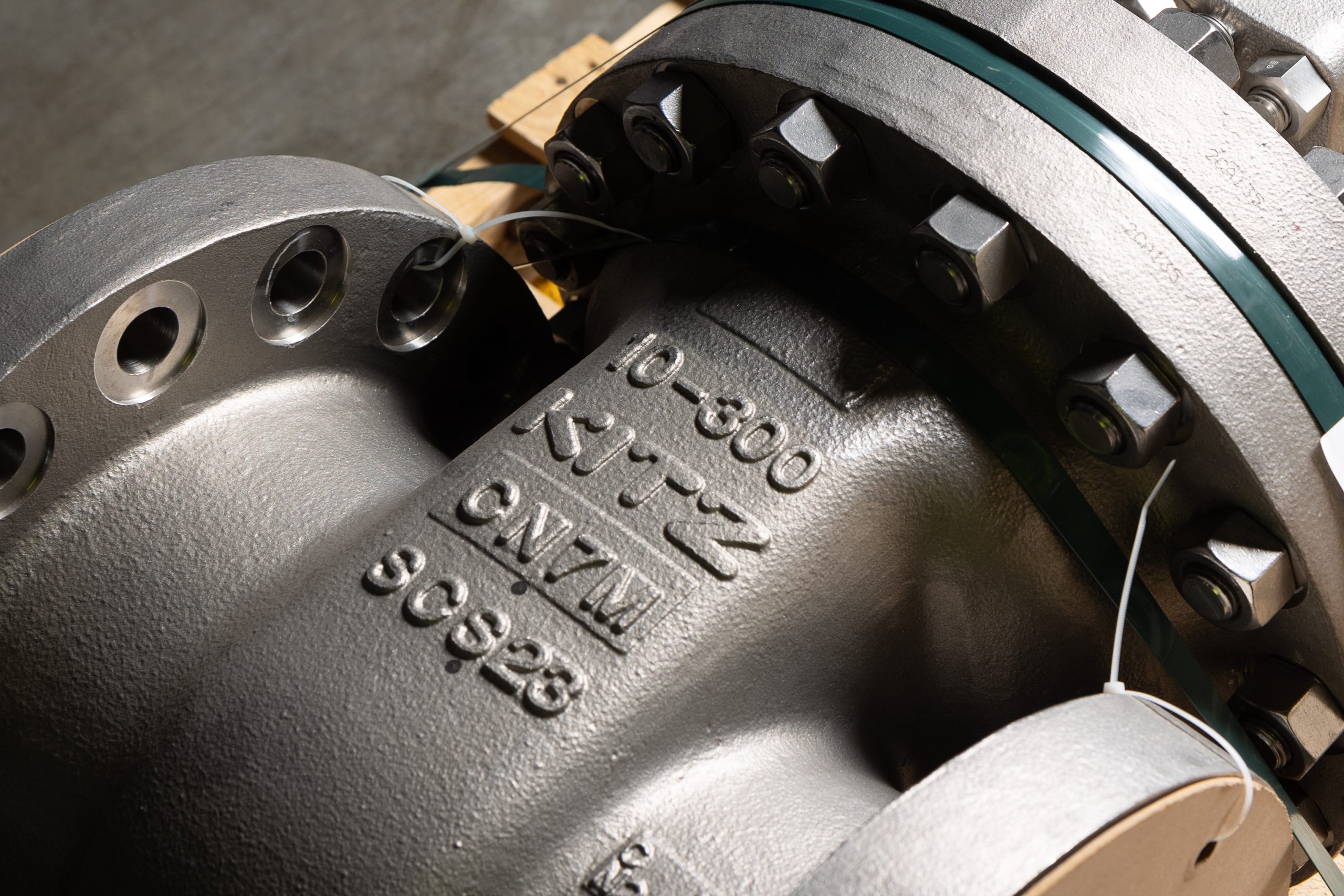
Fugitive Emissions
Functional testing, pneumatic testing, and cryogenic testing are not all the primary considerations when selecting a valve for hydrogen service. To make certain that the valves are capable of meeting worse-case scenarios, they should undergo fugitive emissions and fire testing.
Can a cost saving approach be considered by joining functional testing with emissions testing? A functioning valve under the most extreme conditions can reduce emissions pollution and potentially save lives. In the context of fugitive emissions testing for industrial valves in hydrogen service, specific testing methods should be considered for environmental and operational safety. Helium leak testing, using mass spectrometry or gas detection techniques, is commonly used to assess the leakage rates of valves with exceptional sensitivity.
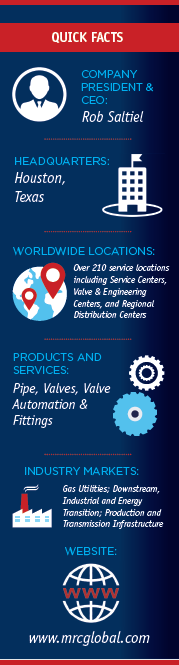
Typically, this testing process is used in procedures based on the methods of ASME V. These methods allow for the detection of very small leaks that may not register on a typical analog gauge, confirming that valves meet stringent emission standards and minimize the risk of fugitive emissions. Furthermore, compliance with standards such as ISO 15848-1 and API 622/624 for fugitive emissions testing is essential to address the environmental impact and safety concerns associated with hydrogen service.
Conclusion
Safety in the hydrogen industrial valve industry demands a meticulous focus on material selection, design validation testing, fugitive emissions testing, proper valve type, and consideration of the challenges posed by hydrogen service based on your risk profile. By prioritizing these and aligning with industry standards and best practices, manufacturers and industry stakeholders can uphold the highest safety standards and promote the reliable and sustainable use of hydrogen as an energy source. As the hydrogen industry continues to expand, the commitment to safety will be pivotal in shaping its success and fostering public confidence in this transformative energy sector.
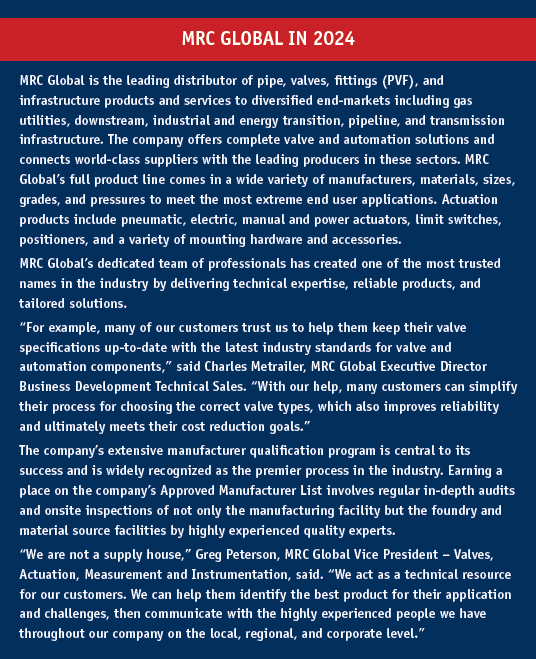
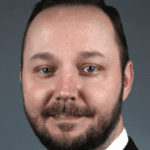