Across the globe, oil and gas production companies face ongoing challenges as they work to minimize greenhouse gas emissions from their production wells, refineries, chemical plants, and pipeline operations.
By Jill Burdette, Global Business Development Process Energy and Transformation, Discrete Automation – Emerson
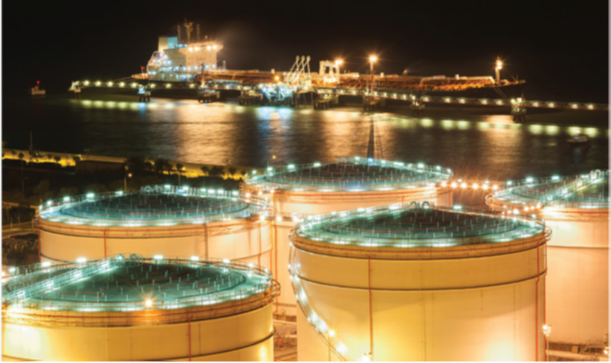
In recent years, there has been a major focus on the fugitive methane emissions released from both oil and natural gas wells and the pipelines that move these products from the wellhead to production facilities. Fugitive emissions are unintentional and undesirable emissions, leakages, or discharge of gases or vapors from pressure-containing equipment or facilities.
It is estimated that control valves account for 60% of fugitive emissions in the industry and offer an opportunity to improve emissions reduction initiatives. Oil and gas producers and refiners are announcing ambitious plans to measure, reduce, and report these emissions over the medium- and long-term.
Oil and Gas Company Applies Automation to Methane Emissions Reduction
A leading oil and gas company is deploying methane detection and control technology across the globe to help reduce its carbon footprint.
The company’s expanded use of methane detection and direct measurement technology can help it better observe and measure methane and provide real-time tracking to predict, prevent, and mitigate fugitive emissions. Through these efforts, the company expects to reduce methane intensity by more than 50% within six years.
Production areas for many companies consist of widely dispersed wells and distribution equipment. These large geographic areas, often with remote locations, create a major maintenance and service challenge for controlling and reducing methane emissions.

Until recently, when excess methane emissions were detected at a site, field crews would be deployed to address the issue. Often, the sites are remote and spread many miles apart, forcing crews to spend unproductive time driving with minimal knowledge of the issue or what service tasks are needed prior to arrival at the site.
Along with other pilot projects in the region, the company developed a solution to help prevent unscheduled flaring, venting, and well shutdowns. The automation solution performs several key functions:
- Continuous monitoring of methane emissions levels at locations where it is installed.
- Reporting those results to central control rooms for analysis and efficient planning of maintenance and service response.
- Throttling back well production when it detects emissions or other conditions that exceed established thresholds
- Restore production once conditions allow
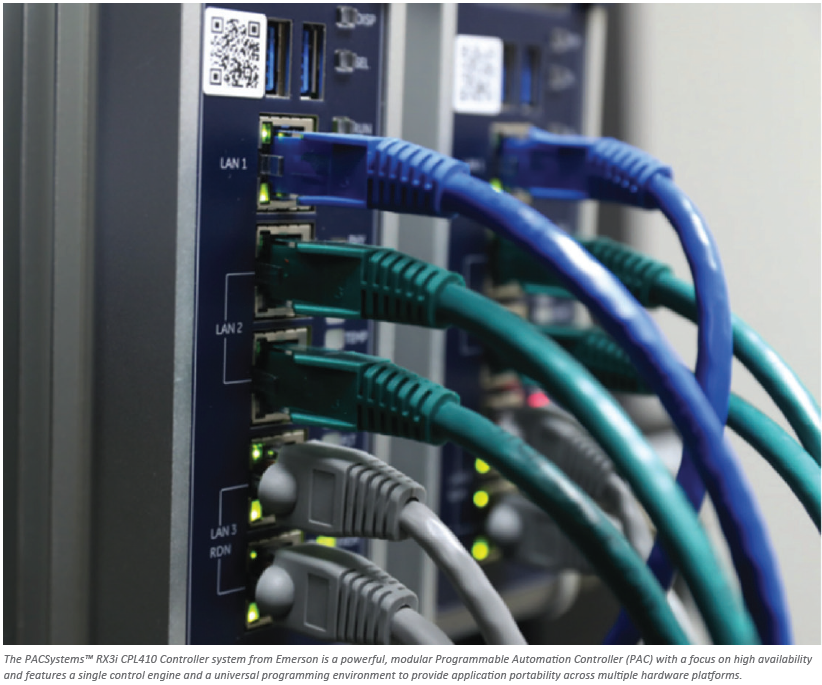
The company used PACSystems™ RX3i CPL410 Controller system from Emerson to build the automation solution. The system is a powerful, modular Programmable Automation Controller (PAC) with a focus on high availability and features a single control engine and a universal programming environment to provide application portability across multiple hardware platforms.
The CPL410 Controller features PACEdge™ software platform, designed to help users to securely collect, analyze, store, and serve up machine data near the source or across enterprise systems. End users can easily build and deploy applications for a wide range of uses.
It also features built-in security protocols and a broad suite of cyber security technology and tools to help protect against attacks, prevent unauthorized code and application updates, and protect against man-in-the-middle and denial of service attacks.
The company deployed the automation solution using the Linux/PACEdge capabilities of the controller. The company had been working for some time to develop an automation capability, and the CPL410 provides several advantages:
- The flexibility of the control solution allowed for programming in multiple languages outside the control environment.
- The controller’s hypervisor secure connection between the Linux side of the controller and the control engine provided a higher level of security.
- The controller’s open connectivity enabled the solution to communicate easily with third-party devices, providing a very flexible solution that made it possible to use the automation solution in both brown field and green field applications.
Automation Pilot Project Yields Positive Results
Product management worked closely with the company to provide technical support as it developed the solution and launched the pilot project across select unconventional production sites.
According to a company report, the first year of the pilot using the automation technology showed an 80% decrease in flaring and venting upset volumes at sites and a 40% reduction in well shutdowns. As a result of these improvements, the company is working to scale the use of the automation solution across location sites. In addition, the automation solution provides a practical way to help improve safety for company personnel working at the location by helping take people off the roads who would otherwise be exposed to safety risks.
Automation technologies like this one, which leverage the advanced edge computing platform of the RX3i CPL410 Controller, are giving major industrial operations new automation capabilities that can transform people’s productivity, while helping to reduce the carbon footprint.