The taps at one’s favorite brewery or beer bar might look like a magic wall that beer flows from when the bartender pulls the tap handle, but there is no magic show. The tap wall is a pretty display of decorative tap handles and shiny stainless steel or brass faucets, but behind that wall is where you will find a series of kegs, hoses, couplers, valves, applied gas, and of course, beer. This is the side that the customer never sees, but it is responsible for making sure beer hits the glass when the tap handle is pulled.
By Chad Pilbeam – Contributor
The same thing happens at home. No one sees the treatment plant or the pipes underground, but when the faucet gets turned on in the kitchen, water comes out. Flush the toilet and the waste disappears. If there is an interruption in the flow on either of these, panic and hopelessness set in, which can only be matched by the desperation of opening the fridge and realizing you are out of beer. Continuing the “Everything I ever needed to know about Industrial Valves, I learned from beer” series, this installment examines flow control and the impact it has on brewing and other industrial applications.
Flow Control Regulation
Most flow control in brewing, and in the beer industry, is mechanical and can easily be regulated with a series of valves. The consequence of improper flow on a draft beer system means an improper pour, and this makes everyone unhappy. Customers want a perfect pint, beertenders want to serve the customer, and the owners do not want the waste from improper pours. Flat beer, over-carbonated beer, a glass full of foam, or no ‘magic’ beer appearing from the ‘magic beer wall’ when the tap handle is pulled, are all consequences from improper flow control. The most serious of all flow control concerns in a brewhouse is the release of CO2 from a fermenter. One can think of a fermenter like a pressure cooker; yeast consumes sugars and converts them to alcohol with a by-product of CO2. If CO2 is not vented out of the fermenter (one direction flow of gas), the result is ‘explosive’. It has happened before.

One of the oldest and most notorious incidents in history was The London Beer Flood of 1814. Yes, this was a real event, and yes, people died as a result, along with a lot of wasted beer and property damage. One of the brewery’s fermentation vessels was compromised and the flow of gas from the fermenter was not sufficient to relieve pressure. As pressure built, the fermenter was stressed, and the result was an explosion that sent over 320,000 gallons of beer flowing through the streets of London. A 15 foot ‘tidal wave’ of beer went through the narrow streets of the neighborhood destroying buildings and ultimately killing eight people (and one dog). For obvious reasons, safety must be a priority.
Valve Safety is a Priority
Through experience, knowledge transfer, proper maintenance of equipment, and the correct valves for the specific application, flow control can ensure unnecessary wear and stress is not placed on system components. By making safety a priority, maintenance and inspection is also prioritized, resulting in optimized performance, lower overall costs, and reduced downtime. It is not all that different than a brewer who wants to maximize their efficiency from the ingredients and pour every drop of beer from keg to glass so to maximize profit.
Going back to the ‘magic wall where beer comes from’, there is not an actual flow valve in the tap or faucet, but the brewer must create a ‘balanced draft system’. Using a series of calculations, there is a specific psi that gets applied to a keg of beer based on the volumes of CO2 in the beer, the dimension and length of the beer line, and the temperature of the beer. This is not all that different from other industrial applications. Flow control valves account for the size of the orifice, the pressure difference between the inlet and outlet of the flow control, and the temperature of the fluid being transferred.
In that way both brewers and pipeline operators have something in common; they both seek lower costs and better efficiency through a ‘balanced’ system. Flow control valves help provide that balance.

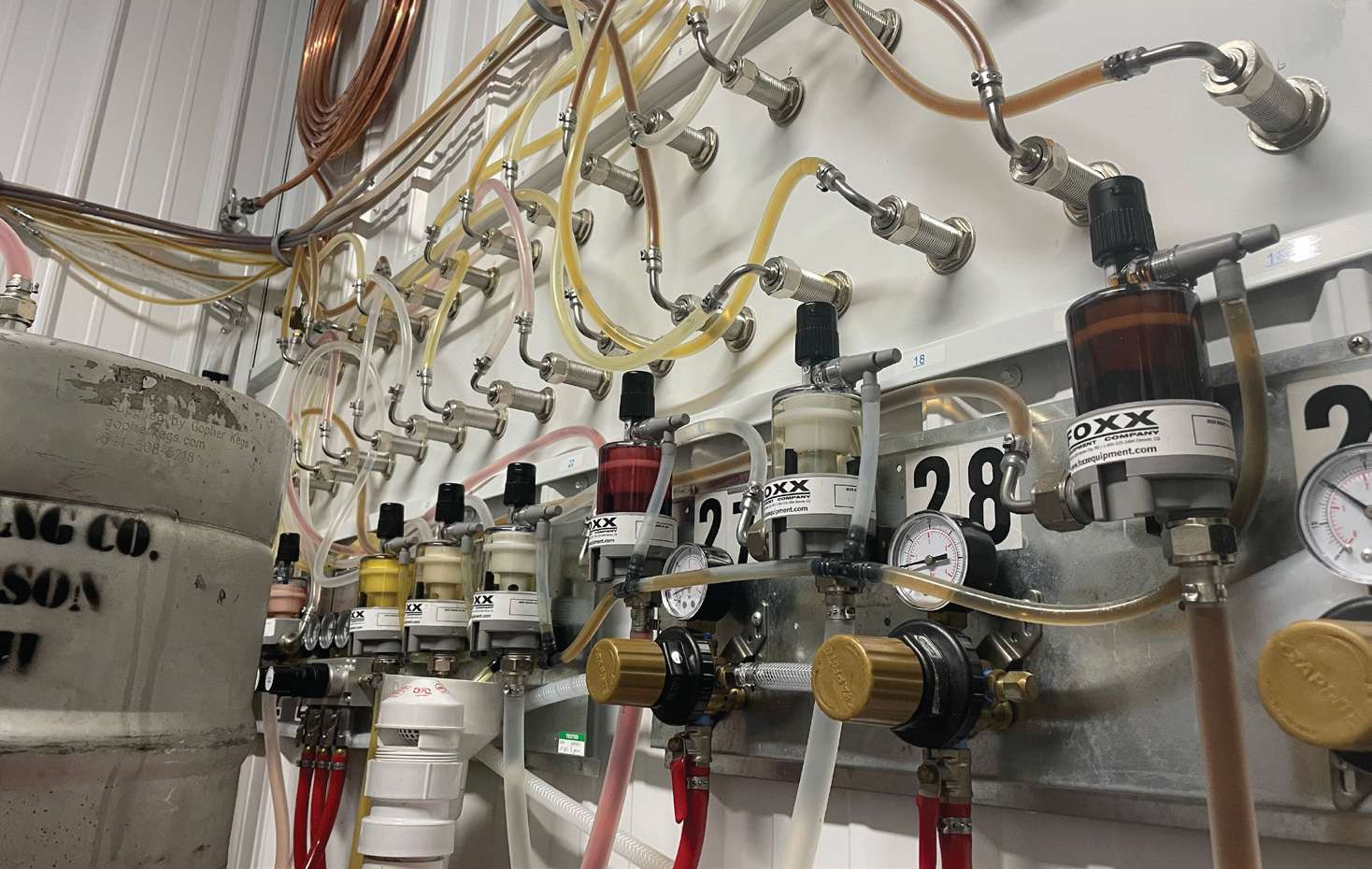
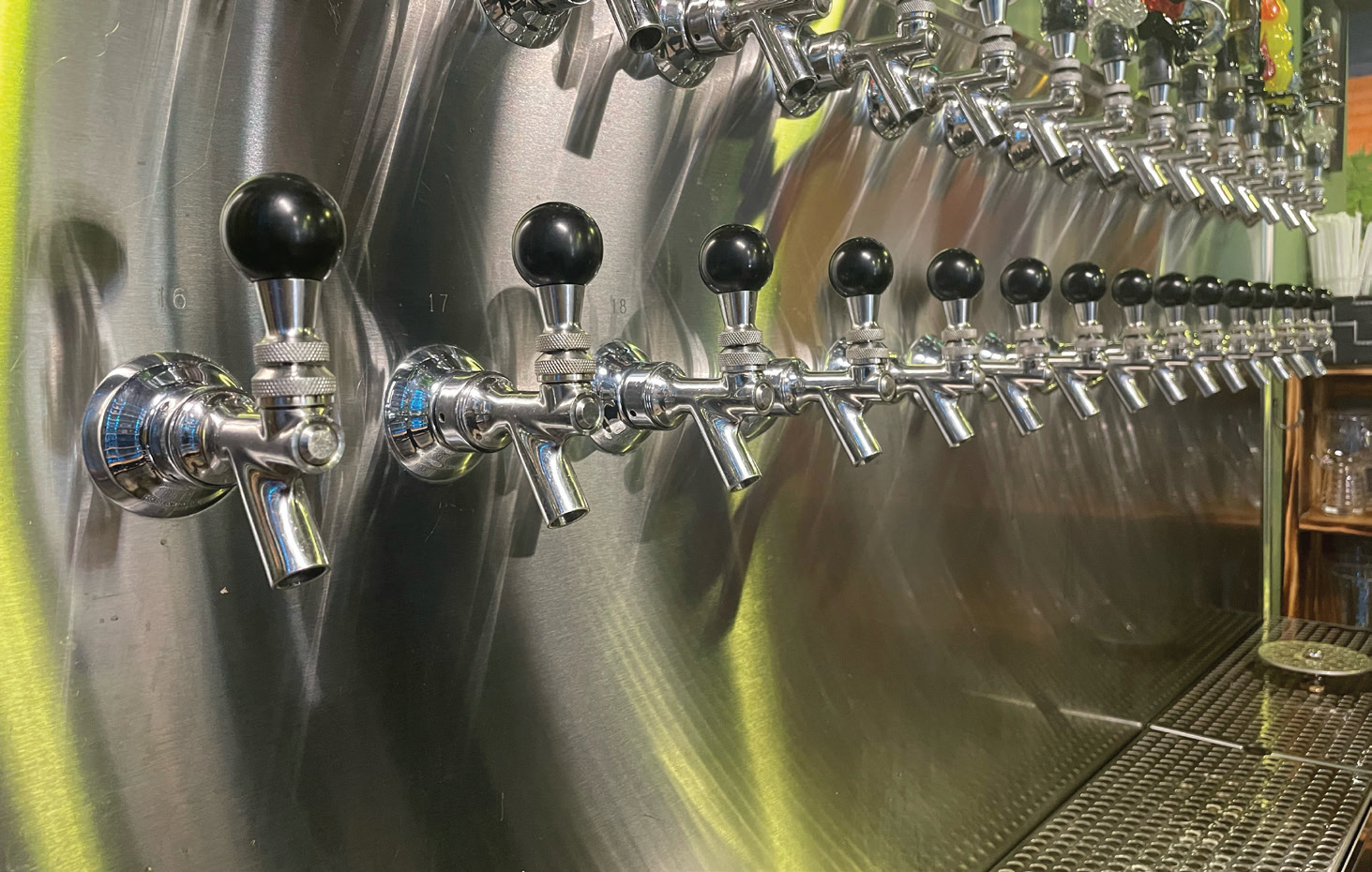
Finding a Balance
There is a right way and a wrong way to pour a beer. Even on a balanced draft system a beertender can pour a beer improperly. The angle of the glass must be considered to ensure it does not fill with foam, and there is another contributing factor. Grab the top of the tap handle and the flow control is slower than if you grab the bottom of the tap handle and pull it open. Slowly opening the faucet restricts the flow of beer from the line to the faucet. Many inexperienced beertenders believe that if a beer is pouring too foamy the solution is to pour more slowly and reduce the foam. Not only does this do nothing to help with foamy pouring beer, but it exacerbates the problem. Restricting the opening through which a carbonated beverage must pass without removing any of the applied pressure will increase the foam dispensed. Flow control at the tap is a product of the beertender, and their ability to control the flow of beer to the glass has a direct impact on pour cost and customer satisfaction; so, pull the handle all the way open and let it flow, let it flow, let it flow. Beer Logic applied!
Industrial flow control valves include ball valves, check valves, butterfly valves, gate valves, globe valves, and needle valves. The beauty of these valves is that as pressure and temperature change, they can be adjusted (or adjust automatically) to maintain the flow rate. Beyond cost control and efficiency, proper flow rate impacts the safety of the operation and customer satisfaction. Balance for the transfer of water, sewage, chemicals, fuel, or gases, relies on properly sized piping, pumps, ancillary components, and the flow control which is regulated by the flow control valve. These are not approximate calculations, rather they are precise, which is why when there is any change or fluctuation in the system the flow control valve must accommodate these variations. This makes choosing the right flow control valve critical because they account for the fluctuations that can be anticipated, but not always predicted.
There are specific, complex, and scientific explanations that can be given for the benefit and consequence of improper or failed flow control valves, but in short, if flow control is not maintained in an industrial application, performance deteriorates, components are affected, and efficiency declines. To operate without a flow control valve, any fluid or gas travelling through a pipeline that changes direction will have wasted energy. When the direction changes, friction is created and pressure drops. Flow control valves reduce energy loss by increasing flow rates and maintaining pressure. The opposite of this is also a benefit. Restricting flow rates prevents overuse and limits energy use to only what is required. Up, down, more, less; with the emphasis on uptime and cost, precise control is not optional, it is the expectation.
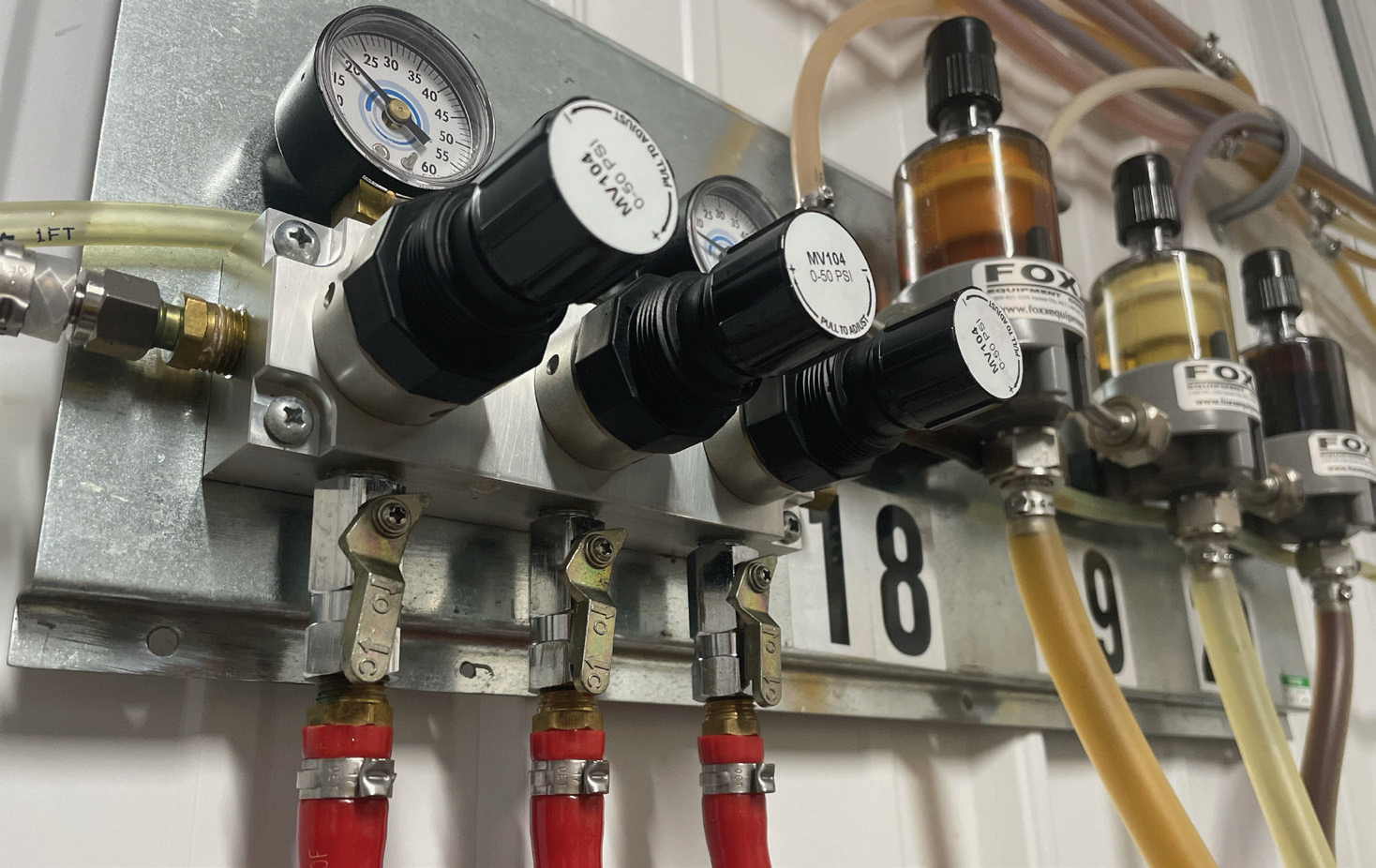
Achieving Efficiency
There are approximately 124 pints in a standard 15.5 gallon keg of beer. It is estimated that as much as 10% of the keg is going to be lost due to overpouring, foam, or flat beer (out of balance systems). This is a real cost that must be absorbed by the publican. Whatever the equivalent of 10% beer loss is in water and wastewater, chemical, or gas applications, the goal is to prevent or limit those losses. It could be energy lost, time lost, increased maintenance cost, or increased wear on components. Downtime and inefficiencies can be anticipated, but not predicted, and the proper use of flow control valves reduces the impact and frequency of these losses.
Think of a flow control valve like a tap handle; it is only one component in the system. Flow control systems work with flow control valves, controllers, flow sensors, and pipelines. When all these components work in synch, accuracy improves, and the process is repeatable. When these components are not in synch (not functioning properly) the inefficient flow contributes to clogging, noise, vibration, oscillation, feedback, and the degradation of system components, as well as increased maintenance cost and downtime. Uptime is the goal, and as a way of appreciating what downtime feels like, think of it as having a keg of beer, but having no way to get it out. Beer Logic applied (again)!
Final Thoughts
Let it flow, let it flow, let it flow. Systems, processes, components, adjustments, maintenance, and calculations all contribute to efficient flow rates. Options in the market give pipeline and other flow control system operators availability to industry and application specific flow control valves. As already mentioned, the precise calculations that control flow result in lower costs, less downtime, and repeatable and accurate performance. Whether these adjustments are manual or automatic, the technology and design of today’s valves offer comprehensive flow rate control while accounting for all variables including changing temperature, pressure, and pipeline size.
There is one ‘consequence’ of an excellent and high performing flow control system; when an individual leaves work and heads to the brewery to have a beer, they and their co-workers will have to find something else to complain about, because your flow control is operating perfectly. Let us just hope the beer they serve is not flat, and you are not served a glass full of foam.
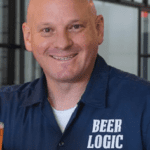