Several governments, operators, and suppliers are betting on hydrogen as a major tool to meet greenhouse gas goals. Regarding valves, they are classified in one of two markets: discrete or process. The discrete market includes small valves used with fuel cells in mostly mobile applications. Process includes the production and transport of hydrogen.
By Bob McIlvaine, President & Founder – The McIlvaine Company
Discrete vs. Process
The discrete classification is defined as a valve associated with a piece of equipment. For example, check valves can be furnished for vehicle fuel cells. These are small valves and are sold to vehicle or fuel cell manufacturers. Many automotive companies are moving forward with hydrogen fueled vehicles.
Process is the classification of valves used in the production and transport of hydrogen. This can also include their use in processes such as: steam generation, compression, creation of chemical products, or heat generation using combustion with hydrogen as the primary or secondary fuel.
Since the discrete market involves small valves and a unique set of customers, the suppliers are not the same companies furnishing the larger process valves.
Effects on the Market
While the process market preceded the discrete market, much of the industry activity is currently in the discrete segment. Over the next 15 years, it is expected that the process expansion will outstrip discrete. By 2040, however, the discrete market will advance while the process market slows down.
Based on the analysis, much of the near-term valve potential is in gray and blue hydrogen. Gray hydrogen uses valves for partial combustion as well as for purification processes, such as pressure swing adsorption. For example, in molecular sieve switching processes, metal seated ball valves compete with triple offset butterfly valves.

The potential for yellow hydrogen is also substantial. Environmentalists have recognized the need for carbon negative processes, and biomass combustion with carbon capture and sequestration (BECCS) is the only cost-effective carbon negative option.
The conversion from gray to blue hydro- gen similarly entails carbon capture and sequestration. As many valves are utilized in the absorption and separation as well as liquefaction and transport, this valve market will likely grow as well.
Analysis
Multiple analyses of the valve companies and the products which they are supplying for hydrogen applications shows that acquisitions are positioning some valve companies to improve their market share. For example, ITT has purchased Habonim, and Atlas Coco and Ingersoll Rand have combined valves with compressors and other complementary products to pursue markets such as hydrogen.

Contributing Factors
The hydrogen process valve market is highly dependent on the mix of fuels for the power industry.
Hydrogen Use
An electric car plugged into an electrical outlet can be using fossil fuel. Using the fuel cell eliminates this route. The extent to which hydrogen currently replaces coal or gas for combustion has not led to an increase in valve revenues. Valve expenditures per kWh can be compared.
If solar or wind is used to make hydrogen which then is used in fuel cells, the valve purchases could range from 20% to 70% of a coal fired plant, when both production and use are considered, see Figure 4.


Hydrogen Production
Creating yellow hydrogen using biomass will have niche uses, and as BECCS is just as yellow (carbon negative), this option will require the most valves. Therefore, the extent to which BECCS is adopted will affect the increase in the valve market.
There will be robust growth under the BECCS based strategy outlined here. If countries do not continue to strive for GHG emissions, to meet the Paris Agreement (no regulations), there will be modest growth in line with GDP. With a mix of technologies such as those envisioned by IEA to meet net zero there will be low growth. If the environmentalists were to dictate a mix heavily dependent on solar and wind (environmental), there would be significant revenue reduction over the next 10 years.


Today, electrolyzers, the devices used in production, typically utilize one of two technologies: low-pressure electrolysis or high-temperature electrolysis. Technological developments have already seen the progression up to large-scale 20 MW electrolyzers, and 100 MW units are not too far in the future. Several valve manufacturers are confident that they have the valves to fulfill the requirements of electrolysis applications for the PEM, AWE or SOEC electrolyzers of both today and tomorrow.
Ultimately, much of the process valve market will be generated through fossil fuels using Small Modular Reactors (SMR) and other technologies.
At lower temperatures and pressures, torque-seated gate valves, often equipped with either solid Stellite® or Stellite®- welded overlay trims, may suffice for applications that do not require tight shutoff. Torque-seated valve designs involve the application of substantial forces to the valve components to adequately seal against line pressure.
Over time, these forces wear down the critical sealing components of the valve, resulting in shortened product longevity versus those of position-seated valve designs.
As temperatures and pressures rise, gate valves are often replaced by Y-pattern globe valves, similarly equipped with either solid Stellite® or Stellite®-welded overlay trims, to achieve improved shutoff performance at initial installation. Unfortunately, the improved shutoff performance of globe valve is offset by the following disadvantages:
- Substantial pressure drop across the valve,
- Short product longevity.


To address the underperformance of globe valves in severe-service applications, companies engineer and manufacture quarter-turn, metal-seated floating ball valves (‘MSBVs’) that can achieve a ‘bubble-tight’ seal per ANSI FCI 70.2 Class VI shutoff – or better. The quarter-turn mechanics of a MSBV not only eliminates packing leaks, but also enables the usage of low emissions packing that complies with prevailing fugitive emissions certifications, such as API STD 641.
Final Thoughts
Forecasting the valve revenues in the short term is challenging. Forecasts to 2050 include so many variables that constant adjustments will be required.
References:
- Hydrogen Valves, published by the McIlvaine Company
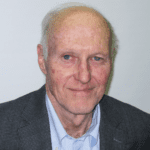