Solving problems for his customers is what sets Jody Millsap apart from the pack.
“I love to investigate a problem and find a solution,” the 50-year-old president and owner of Water Solutions Engineering said. “This is what I really enjoy. This is one reason why I like to do consulting in addition to our regular work. The customer I started consulting with in 2012 had a 15-year-old problem. It was water related and we were able to solve it. This is what I really love to do—go in and help a customer solve an issue—to show what the problem was and show how we solved it. The gratification of doing that means the world to me.”
Background
Millsap became interested in engineering at an early age. “My dad had a huge impact on my life,” he said. “Growing up I was good in science and math. He worked at Eastman Chemical Company in Kingsport, Tennessee. When I was 10 or 12 we had an issue with a camper that exploded. Over 60% of his body was burned, and I had third-degree burns on my hands and other places. We were in the middle of lawsuit, and my dad recommended that I should think about being an attorney, but that required too much school for me. So I focused on my science and math skills and went to the University of Tennessee in Knoxville (UT) to study chemical engineering.”
Millsap worked a couple summers at Eastman, but he didn’t enjoy the large corporation atmosphere. “It was just too big,” he said. “But I learned a lot from the operators. They really know the process. My advice is always to get to know the operators, and you will learn the most. I went into engineering mainly because my father recognized the skills I had. I now can admit that perhaps fathers and mothers know more than their kids know.”
Millsap earned his Bachelor of Science degree in Chemical Engineering from UT then worked the next two years in management for a textile chemical company and then worked at a coating company. Then he landed a project process engineering position with a fiberglass extrusion company, which is where he got more involved with valves, automation, and large mixing projects. He worked there for about 5 years and then became interested in chemical water treatment.
For the past 10 years, he has been running Water Solutions Engineering, which treats industrial water for corrosion, scale, microbiological issues, cooling towers, boilers, chill water systems, and everything industrial, but nothing potable. He cofounded the company with another gentleman in 2008, but became sole owner in 2014.
Chemical water treatment typically consists of adding numerous types and sometimes excessive amounts of chemicals necessary to overcome poor water quality in the attempt to achieve acceptable performance from water systems. “The key to our chemical water treatment programs is to first provide and maintain the best possible water quality through physical water treatment, followed by chemical treatment to enhance the performance of water; rather than combat poor water quality with an abundance of chemical,” Millsap explained.
Water Solutions Engineering™ is headquartered in Kingsport, TN, (90 miles north east of Knoxville). Reducing overall water and energy consumption is a priority. Water Solutions Engineering™ relies on its experience and expertise to design total water solutions for its customers utilizing the latest technologically, advanced industrial wastewater treatment equipment and a wide variety of environmentally-friendly chemical water treatments.
“We have about 100 customers, and perform chemical water treatment on a much smaller scale for small and mid-size industries and commercial accounts,” he said. “Employees handle the day-to-day operations of seeing customers, ordering chemicals, ensuring the chemical levels are correct and that the equipment is functioning the way it should. In 2012, I began doing some consulting to help customers as a chemical water treatment supplier and to help them with overall water re-use, water savings, and overall industrial water usage and chemical programs.
For example, recently Millsap installed about 9 or 10 water meters and re-wired some controllers for a manufacturing company in California.
Problem Solving Expertise
Millsap described one kind of problem that he might be asked to tackle.
“One customer had a staining issue with their product,” he said. “Their product is white, but had steam and cooling water that would regularly touch the product so they would randomly have small stains—a yellow staining area. It was very small and difficult to see at times, but it was ongoing for about 15 years. Through a combined effort and after several visits, we discovered that the staining was a result of an incompatibility between some chemical water treatment from the previous vendor. We made some changes and found that the stain got worse. This helped us to isolate the problem. Prior to 2012 it was completely random. They could not increase or decrease the amount of staining, nor could they affect it adversely or positively. We were able to adversely affect it, which helped us identify the incompatibility issue with some of the chemicals they were adding to their water. We removed the chemical and now the stain has not resurfaced for the past 4-plus years.”
Millsap’s process for problem solving is simple, but precise.
“First, we try to understand the whole process, not only the water, but what outside influences are impacting the problem area,” he explained. “Then we determine if there is direct or indirect contact. So the focus begins inward and then expands outward. We try to discover what are the potential sources of impact. One at a time, we try to make changes on the direct contact, and wait to see how it impacts the issue. If you make a change, you have to give it some time to take effect. Sometimes we wait 24 hours, for example. If we don’t get a change or response, we try something else. It’s important to not change more than one thing at a time, because then you can’t identify the problem. The key is isolating the problem.”
Problem Solving Valves
In the water treatment industry, Millsap said he mainly works with blowdown valves—which is a generic term for a needle valve, or a ball valve, or a gate valve. These valves are generally electronically actuated in contrast to a hand valve.
“A blowdown releases water from a cooling tower or a boiler system to let the old concentrated water out and let some other sort of city water or fresh water in,” he said. “We use these often in our industry. Cooling towers have very low pressure and let the water out of the basin or the recirculation line, which usually run around 60 psi. It’s typically a solenoid-actuated ball valve that will open, then the equipment will read the conductivity of the water and tell the valve to close. Some of the problems we run into are debris and other foreign objects getting caught in the ball valve and not allowing it to close all the way properly. Sometimes it’s a diaphragm or piston valve that will have the same issue with debris. We have to troubleshoot to understand why the conductivity is low because generally some water is still getting through. We try to install these so the end of the pipe at the drain is visible.”
Boilers are more complicated, he said, because of the high temperatures and high pressure. There are two types of blowdowns on a boiler.
- 1. An automated valve that blows down surface water (usually a ball valve on the bottom so you can do a boiler-bottom blowdown to get all the sludge that has settled in the bottom. This is typically hand operated for 2-3 seconds, 1-2 times a day.
- 2. Electronic valve.
“The biggest issue is the solenoid mechanism can go bad,” he said. “Over time, the seats or diaphragms get stale (deteriorate) or get corroded. Ball valves typically are pretty robust and the water going through them is already treated, so corrosion is not likely. We specify stainless steel balls with Teflon seats. These are robust and last a long time. Most industrial ball valves use these materials.”
Problem Solving Pumps
The standard pumps that Millsap’s company uses for chemical injection are peristaltic pumps.
“If you want a precise amount of chemicals delivered into a system, a metering pump is perfect,” he said. “But in our industry, most of the time we really need reliability and self priming more than precision. If you are pumping something like bleach, it can air lock and you have to check it often. If you run empty on a tank or empty on a drum, air can get in and you have to bleed that air out. This can cause the diaphragms to fail. In 2005, we started seeing a lot of bleach (sodium hypochloride) and sodium bromide (a halogen product) being used because of off-gassing. In these cases, peristaltic pumps are very reliable—if it runs dry it doesn’t matter or if it gets air in the line it doesn’t matter, that pump will continue to pump. They are not as precise, but we don’t need to be that precise. The standard tubes last a long time, and they are user friendly as far as changing the pump head and tubes.”
For pumping water, Millsap prefers a basic centrifugal pump. “Sometimes we have customers who use diaphragm pumps for chemical injection, so of course we know them and understand them and can provide them. We can replace parts and perform rebuilds, if needed,” he said.
Maintenance Tips
Valves are fairly robust, Millsap said. “For general maintenance, I would suggest to check the operation of the valves monthly for cycling, closing operation, check for leaks at the seal, and make sure everything is working correctly,” he said. “For the pumps we use, general maintenance includes checking the pumps at least once a month. Check for functionality and leakage. Make sure they are mounted properly. If the pump head or tube ever leaks, the chemicals can get into the motor if it is not mounted properly. Mounting is key. These pumps are great for industrial settings, but if you have a lot of dust the pumps may need to be placed in a dust-proof box that provides good air flow. Motors need to be kept cool while running, so it’s a good idea to have good air flow.”
Safety Tips
The first rule of safety, Millsap said, is to always wear the proper PPE (personal protective equipment).
“We follow the customer’s PPE standards, and we even go one step further,” he said. “For example, they may not require safety shoes, but we still wear safety shoes. We use steel-toed shoes, safety glasses, ear plugs, and gloves. We are typically handling chemicals or equipment that contain chemicals. So the gloves, though not required, are something we use most of the time. Follow the safety guidelines of the facility. Be aware of your surroundings and the location of the exits. Many customers require annual safety training. We are fortunate that in 10 years we’ve had nothing more than minor incidents that required minimum first aid.”
Millsap’s team enters up to 90 different sites on a monthly basis. When people go into the same facility every day, they know all the hazards, he said. “We are going into a plant once a week or once a month, or once a quarter. There are constant changes at these facilities. We train our guys to be sure to walk slowly, look around, don’t be on your phones, and pay attention. Make sure you have the proper protection equipment. Any hazards we find, we bring to the maintenance team’s attention. Our philosophy is to be an extension of the customer’s maintenance team. Make sure the area you are working in is well lit. If you are doing extensive work, make sure someone knows where you are in case of emergency like electrocution, etc., especially when working in remote areas.”
The Water Solutions Engineering team works primarily in Tennessee, Virginia, North Carolina, and South Carolina. But they also service some customers in Maryland, Florida, and California.
Advice for End Users
First and foremost, Millsap advices other end users, especially young engineers just beginning their career to simply be happy and enjoy what you are doing. “If you don’t enjoy it, make a change,” he said. “Don’t make decisions based on money. If you love what you do, the money will come. If you don’t love what you do, you will be miserable. Find what you enjoy and give it 110%. And, be like a sponge. Listen and learn from others. Try to understand what others are doing because that could impact what you are doing. The more you learn, the more you know. This will always add value to what you do.”
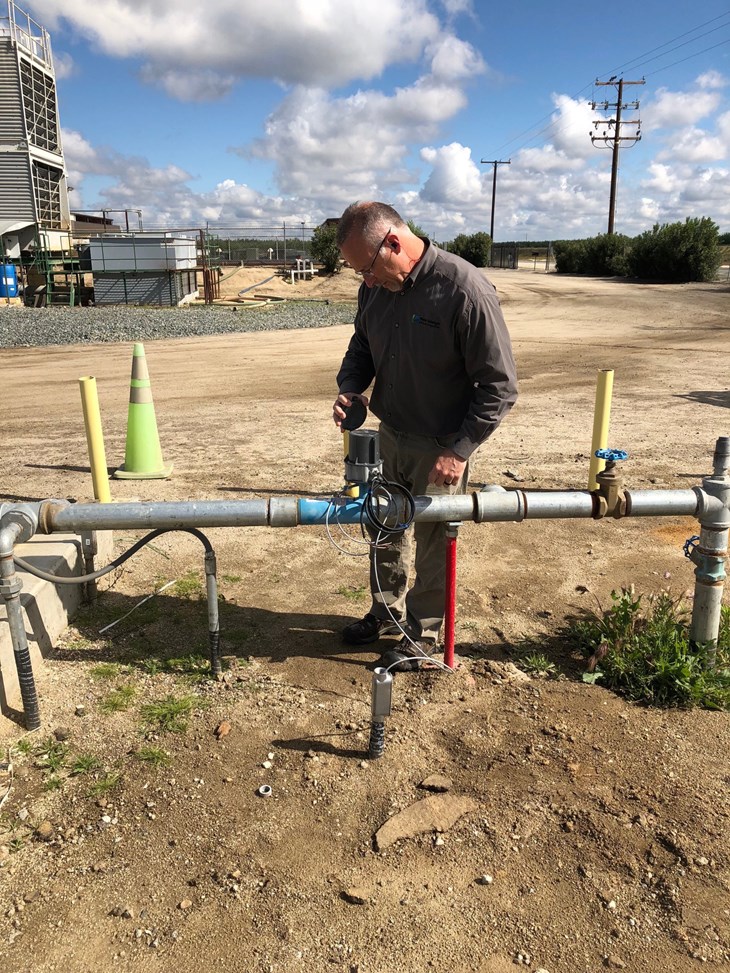