To combat climate change and create a clean energy future, fundamental changes in the refining industry are necessary to reduce Green House Gases (GHGs) and methane emissions. Many governments worldwide are currently trying to achieve net zero by 2030. Some of the clean energy plans will eliminate coal as a fuel source for electricity, boost renewable energy, such as wind and solar energies, and ideally reduce carbon emissions by 90-95%.
By following specific initiatives, organizations will implement practises that could result in the realization of net zero methane emissions. These changes are inputted with the intention of reducing environmental methane emissions.
By Gobind Khiani – Consulting Fellow-Piping/Pipelines
Paving the Path Towards Sustainability
Organizations are diligently working towards creating sustainable practices without impacting the production or supply chain. There are therefore several methods currently set in place to help reduce GHG and methane emissions by 70 to 80%.
• The first, and most obvious, method is taking the appropriate steps to maintain refining facilities and their applications. Replacing aging piping and other equipment in a refinery, such as, cast iron main lines and older service lines.
• The second practice is to rehabilitate outdated infrastructure and retire well rehabilitation.
• While it is important to reevaluate existing structures and mandates, adapting to new technologies and operational practices is another method that often aids with emission reduction. It is beneficial to increase damage prevention practices, implement leak reduction methods, and retire older assets. This creates a pathway for practical and sustainable performances.
• Implementing best practices such as compressor engine rod packing, station emergency testing as well as distribution system leak surveys, and maintenance alignment. These are achievable and practical measures that can be taken to reduce emissions.
Although this may seem like a non-exhaustive list, the industry faces several obstacles when it comes to emission reduction.
Hydrogen and Steel Applications
The introduction of negative GHG and methane, also know as renewable natural gas, can further mitigate the occurrence of GHGs and emissions. New strategies and technologies are being constantly explored to coincide with the net zero emissions goals. The use of renewable gases and hydrogen, as an alternate source of energy, is a topic in the industry that has been steadily gaining momentum. Hydrogen comes in various forms and is often depicted by colour. Each variation of hydrogen is produced in different ways but contains little to no carbon emissions. As the use of hydrogen in pipelines continue to gain the attention of industry professionals, it is important to consider the tribulations that might be present with steel applications and hydrogen.
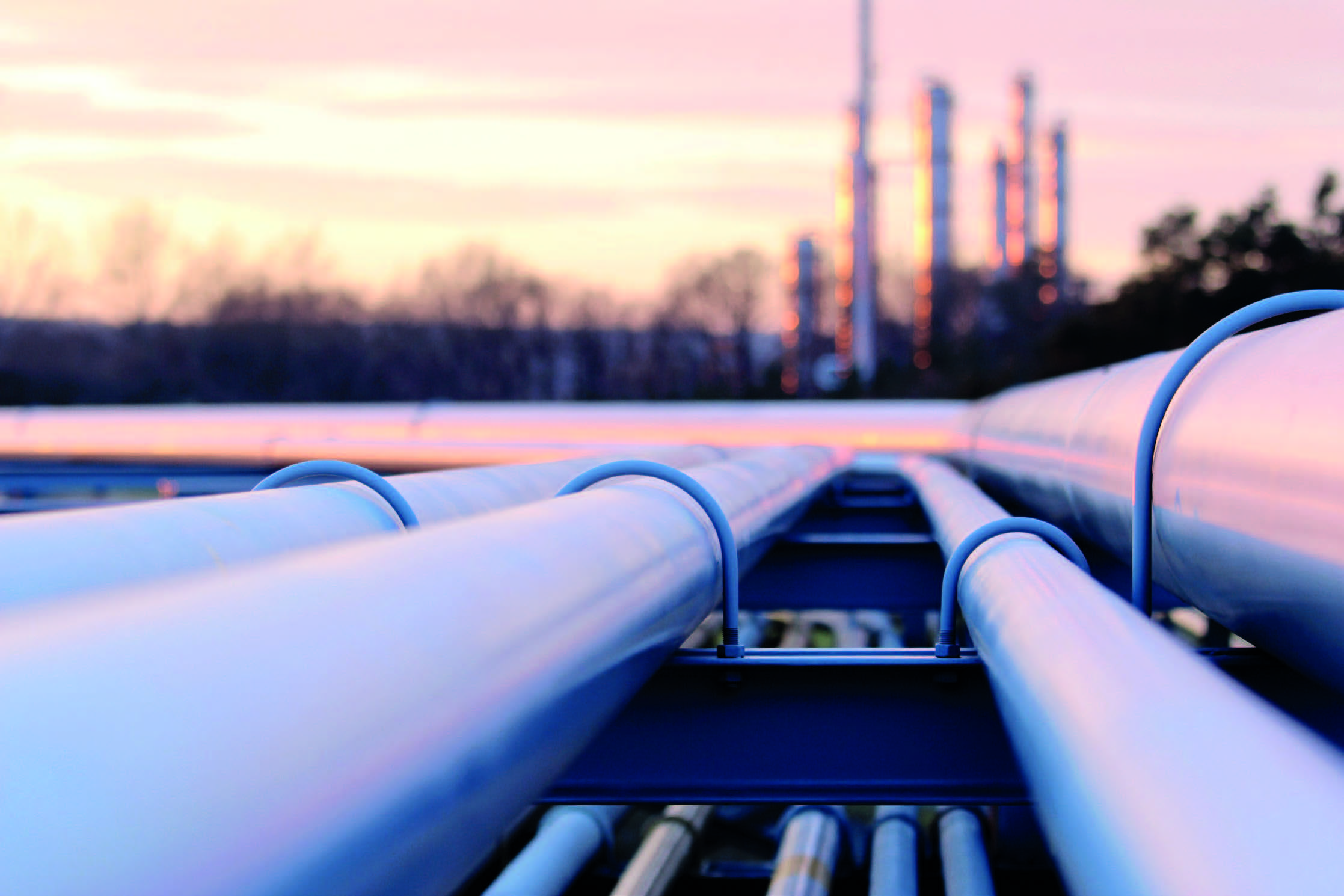
There are a few standard codes that the industry currently uses when working with equipment made of steel in hydrogen services. These codes are to ensure proper handling and functioning of the equipment while hydrogen is being pumped through the applications. The two most relevant codes are API RP 941 and ASME B31.12. They detail the following:
API RP 941
API RP 941 applies to any equipment in refineries, petrochemical facilities, or hydrogenation plants that operate in environments where hydrogen-containing fluids are processed at elevated temperatures and pressures.
The API RP 941 is a recommended practice developed and published by the American Petroleum Institute (API). The RP is intended to help identify and manage equipment potentially subject to high temperature hydrogen attack by putting into place practical operating limits for carbon and low alloy steels in hydrogen service at elevated temperatures and pressures. This RP also discusses how the resistance of steels to hydrogen damage can be affected by high stress, heat treating, chemical composition, and cladding. A summary of inspection methods to evaluate equipment for the presence of HTHA is also included.
API RP 941 was originally published in 1997, and the most recent 8th Edition was published in February of 2016. API RP 941 only covers equipment that runs at high temperatures and does not cover any equipment that runs at below 400°F (204°C). At those lower temperatures, hydrogen enters the steel with the assistance of an electrochemical mechanism, operating under different principles.
Additionally, this RP only covers HTHA resistance for steels operating within the recommended guidelines. The guidelines in this RP can also be applied to hydrogenation plants such as those that manufacture ammonia, methanol, edible oils, or higher alcohols.
ASME B31.12
ASME B31.12 is a standard on Hydrogen Piping and Pipelines containing requirements for piping in gaseous and liquid hydrogen service. These standards will aid with the transition to implementing the use of hydrogen on a more regular basis.
Valves in the Hydrogen Industry
Valves used in hydrogen industry have several requirements that extend above and beyond general application testing standards. These standards define leak testing requirements for external or internal leaks. Common standards include:
1. API 598, Valve Inspection and Test
2. ASME B16.34, Valves – Flanged, Threaded and Welding End
3. ISO 5208, Industrial Valves, Pressure Testing of Valves
4. ANSI FCI 70-2, Control Valve Seat Leakage
5. MSS SP61, Hydrostatic Testing of Steel Valves
6. ISA-S75, Hydrostatic Testing of Control Valves
The primary test conducted on valve assemblies to be used in hydrogen applications are external test, such as a hydrostatic shell test. The shell test confirms the soundness and strength of the valve body. It also pre-stresses the valve body, which aids in avoiding fatigue with cyclic pressure. It is done with water at 1.5x the valve body pressure rating. The shell test is typically done with valve in the partially open position. As the body of the valve should be externally leak resistance, it is preferred to use fully welded body design for this application.
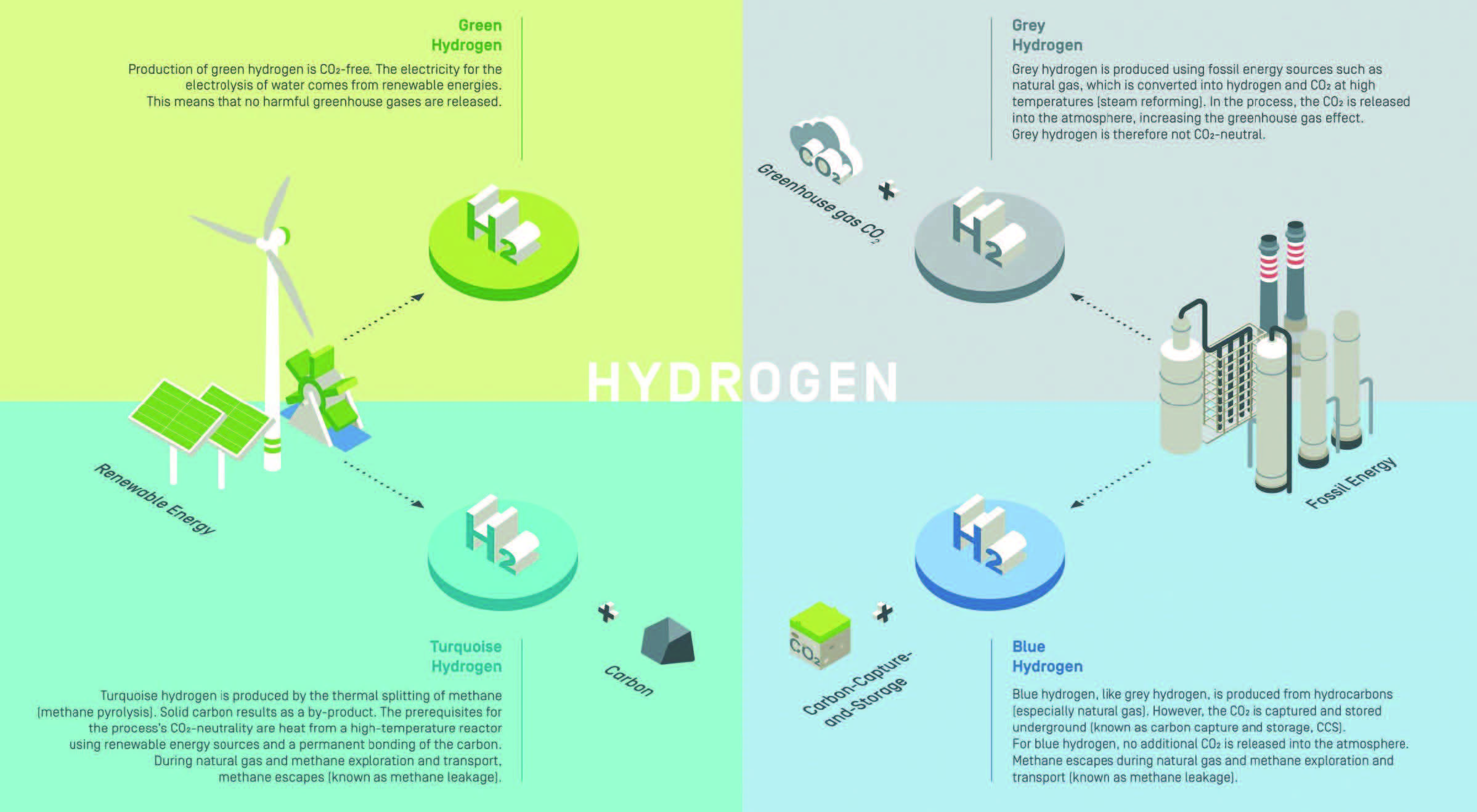
Transporting Hydrogen
The transportation of high-pressure hydrogen in steel structures presents challenges. Hydrogen gas can adsorb and dissociate on the steel surface to produce atomic hydrogen. Dissolution and diffusion of atomic hydrogen into steels can degrade mechanical properties, creating hydrogen embrittlement, thus making the application susceptible to fractures. Hydrogen reduces typical measures of fracture resistance such as tensile strength, ductility, and fracture toughness, accelerates fatigue crack propagation, and introduces additional material failure. Steel structures that do not fail under static loads at ambient temperature are susceptible to time-dependent crack propagation in hydrogen.
Carbon and low-alloy steels are therefore common structural materials for high-pressure hydrogen gas vessels and pipelines. The materials used in hydrogen application, such as steel pipelines, have been operated safely with hydrogen gas when specific limits have been placed on properties of the steels. Relatively low strength carbon steels are specified for hydrogen gas pipelines. Examples of steels that have been proven for hydrogen gas service include: ASTM A106 Grade B as well as API 5L Grade X42, and API 5L Grade X52.5,6.
The API 5L steels contain small amounts of niobium, vanadium, and titanium and are referred to as ‘microalloyed’ steels. Microalloyed X52 steel has been used extensively in hydrogen gas pipelines.
Material Selection and The Carbon Equivalent.
Material strength is an important variable that affects hydrogen embrittlement of pipeline steels. One of the principal criteria to consider when selecting steel grades and processing procedures is the limit strength. The maximum tensile strength, recommended for hydrogen gas pipeline steel is 800 MPa. The properties of welds are carefully controlled to preclude hydrogen embrittlement.
As hydrogen pipelines are operated at near constant pressure, cracking due to hydrogen embrittlement must be driven by static mechanical forces. Cyclic loading, which can drive fatigue crack propagation aided by hydrogen embrittlement, has not been a concern for hydrogen gas transmission pipelines. Experience from the petroleum industry, however, has demonstrated that hydrogen assisted fatigue is possible with hydrogen piping. Defects can form on the inner and outer surfaces of steel pipelines from several sources, including welds, corrosion, and third-party damage. Welds are of particular concern since steel pipelines can require two different welds: longitudinal (seam) welds to manufacture sections of pipeline, and girth welds to assemble the pipeline system. These welds are inspected to detect the presence of defects in pipeline walls that intensify stresses locally, creating more severe mechanical conditions for crack extension and concentrating atomic hydrogen in the steel.
Conclusion
Experience with steel vessels and pipelines in the industrial gas and petroleum industries demonstrates that these structures can be operated safely with hydrogen. The use of this gas is however limited to certain ranges of material, the environment, and mechanical variables. Gas pressures in valves, vessels, and pipelines for the hydrogen economy are certain to exceed the limit in current applications.
Data consistently shows that steels are more susceptible to hydrogen embrittlement at higher gas pressures. As operating pressures increase, designs will demand materials with higher strength. Most data indicate that steels are more vulnerable to hydrogen embrittlement when strength increases. The effects of other variables, such as gas impurities, welds, and mechanical loading on hydrogen embrittlement of steel vessels and pipelines in the hydrogen economy are not as certain. Hydrogen embrittlement resistance of steels could be improved through production of low-manganese and low-silicon steels.
Although hydrogen embrittlement is more severe at high gas pressures and in high strength steels, structures can still be designed with steels under these conditions by using fracture mechanics. Provided material data is available for steels in high-pressure hydrogen gas, the limiting crack depth, wall stress, and structure dimensions can be defined using fracture mechanics.
ABOUT THE AUTHOR
Gobind N Khiani, a UCalgary alumnus of Masters in Mechanical Engineering is a seasoned change-maker. He has a proven track record in technical and value engineering and holds a Fellowship in Engineering and an MBA. He is the Chairman of the End User Group at API and Vice Chairman of the Standards Council of Canada. He has done peer review on Emissions Management regulatory documents for ECCA and participated in research and development initiatives.
Further, his experience is in the energy sector in the improvement of standards, technical compliance, strategy, governance, digital innovation, engineering management, technology, sustainable development, and operations. He is also skilled in Asset Integrity and Maintenance Management. As a volunteer, he is involved in technical standards (energy, tech, public safety) and has been a mentor/judge at First Robotics Canada. He is also the past chair of the CBEC of APEGA.