As valve end users strive to reduce emissions within its facilities, they frequently look to fugitive-emissions (FE) qualified valves as a solution. However, the emissions performance of these valves does not last forever, and will eventually need repairs. When it comes time to repair them, how can repair facilities and end users ensure they are returned to their original emissions-certified performance level?
By Matthew Doherty, Technical Support Manager, and Christian Meade, Product Champion – Schlumberger
Sealing Is Paramount
To start, it is important to be aware of the factors that can impact external sealing performance. In the case of fugitive emissions, stem sealing performance is the primary area of focus. Because of their dynamic nature, stem seals can experience a higher frequency of leaks when compared with other seals within the valve. While stem seals receive significant attention, static external sealing mechanisms can also contribute to fugitive emissions, particularly when exposed to variations in pressure and temperature. For any of these seals to work properly, several factors—including the installed compression of the seal, surface finishes, and relative positioning of components—must be considered. When an FE qualified valve is repaired, particular attention must be placed on ensuring these factors remain consistent with the originally qualified design. To clarify, it is important to consider how valve FE type testing standards incorporate sealing performance factors into the qualification of valve designs. In each of the primary FE type testing standards, including API 624, API 641, and ISO 15848-1, a test is completed on a single valve from production to qualify a range of valves with a similar configuration. One key element of the configuration that must remain constant across the qualified range is the external sealing mechanism. If a valve’s external sealing mechanism changes from the qualified configuration, then the qualification no longer applies.
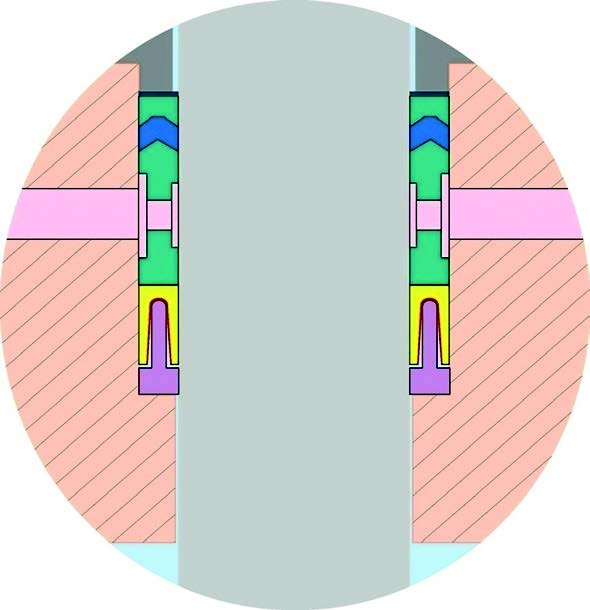
Understanding How FE Type Testing Standards Impact Valve Repairs
Understanding the qualified range concept when valves are being repaired is critical, because the process of repair can alter the external sealing mechanism to the point where the valve would require requalification to the applicable FE type testing standard. It is pertinent to review the primary valve FE type testing standards to see how the qualified range statements can impact the repair process.
API 624 is an FE type testing standard for rising stem valves that use stem packing arrangements previously qualified to API 622 standard. The current revision of API 624 indicates that any change to the stem sealing system design requires requalification of the valve assembly. In this case, a change in the stem sealing system may be anything from a different packing material to a different packing model number. During a repair, this means that to retain the original API 624 qualification, the repair facility must use the same stem packing that was used in qualification testing. The only exception to this is when that valve assembly has been qualified with multiple packing materials or configurations. As a result, repair facilities and end users will need to properly plan for the sourcing of the correct components prior to repair to maintain the valve’s qualification.
API 641 is an FE type testing standard for quarter-turn valves. In some cases, valves qualified to API 641 use packing sets qualified to API 622, but this is not a requirement. In API 641, there are many more extensive limitations on how much the external sealing systems can change and still be covered under the original qualification. As with API 624, the stem sealing design, including materials, sealing stress, and shape, must remain the same. Additionally, the tolerance classes and surface finishes for all components that impact external sealing performance must remain the same. These are key items to consider when repairing a valve qualified to API 641. For instance, in the stem sealing arrangement, the repair facility must ensure that the dimensions and surface finishes of the stem and stuffing box and seal grooves remain in tolerance based on the original qualified design. If this is not done, the sealing configuration may differ from the qualified configuration and the FE certification is no longer valid.
ISO 15848-1 is an FE type testing standard that can be broadly applied to industrial valves, including both isolation and control valves. In this standard there are no restrictions on the type of stem sealing system used. The broad scope of possible external sealing systems leads to qualification extension limitations that are similar to those in API 641. Specifically, any changes to the stem sealing design, as well as tolerance classes and surface finishes of components that impact sealing performance, result in the need for a new qualification test. Additionally, ISO 15848-1 specifies that the loading arrangement applies similar stress to the external sealing elements. This requirement highlights the importance of proper reassembly during the repair process, in addition to the considerations on dimension, tolerance, and finish discussed previously. For example, during the reassembly process, the bonnet bolting torque should be in-line with the original assembly procedure, particularly with gasket type bonnet seals, to achieve the same sealing stress level.
At this point, one may be wondering how current valve repair standards, such as API Recommended Practice (RP) 621 and Annex A of the 25th Edition of API 6D, which is replacing API RP 6DR, align with the points presented in this article. To begin, API RP 621 provides guidance on the repair of heavy wall gate, globe, and check valves, such as gate valves designed to API 600. This RP provides prescriptive guidance on the inspection and acceptance of major valve components, including the stem, stuffing box, and gasket surfaces, all of which can impact external sealing performance. However, there is no assurance that the recommendations provided in API RP 621 will return the valve to the original FE qualified condition. For instance, API RP 621 allows for some pitting to remain in the stuffing box provided that it does not span more than half the height of any single compressed packing ring. While this may be acceptable for general repairs, it is clearly a deviation from the FE qualified stem sealing system and could result in reduced emissions performance.
Annex A of API 6D 25th Edition provides guidance on the repair of valves manufactured to API 6D. This document also provides guidance on the inspection and acceptance of major valve components but is much less prescriptive than API RP 621. Annex A of API 6D indicates that inspection and evaluation shall be completed based on documented procedures and goes on to provide some basic guidance on what could be considered acceptable. For instance, the “stem sealing preparations or stuffing boxes shall be verified to meet the dimensional, material, and surface finish requirements that were validated for the seal design” (API 6D 25th Edition, Section A.5.2). This statement is better aligned to the concept of assuring that the valve retains the same FE qualified stem sealing configuration. However, it does not have similar requirements for static sealing elements.
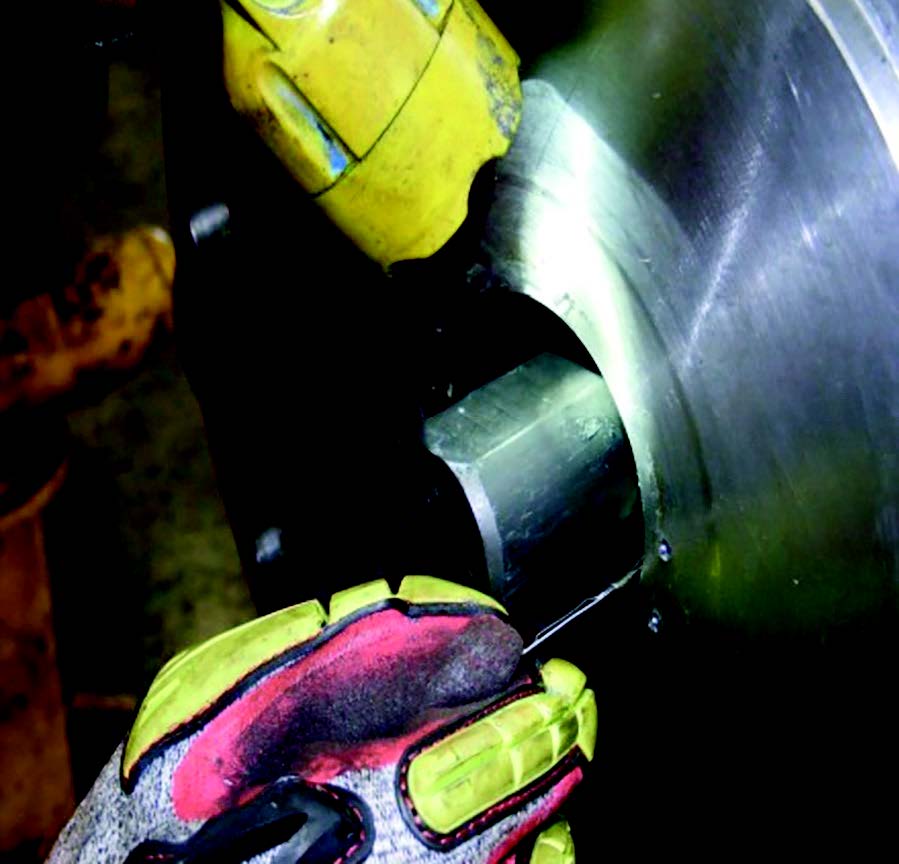
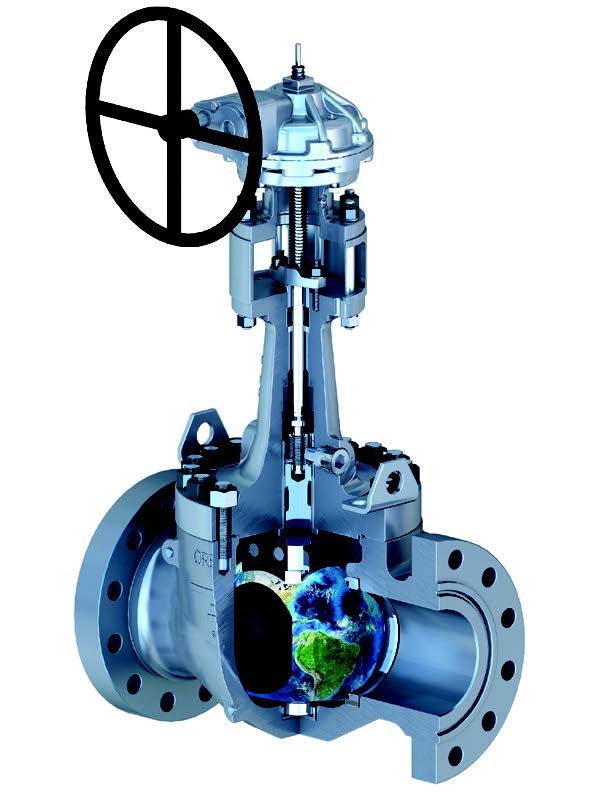
Supplemental Guidelines
As seen previously, * ensuring that repaired valves are returned to their FE qualified condition requires special attention that is not explicitly covered by valve repair standards today. That said, using the information previously discussed as a guide, repair facilities and end users can begin to identify key supplemental guidelines to follow during repairs to ensure continued FE certification. To start, parts used in the repair process should be based on the original bill of materials for the valve and should be identical to the original components. The best way to ensure this is to source parts from the original equipment manufacturer. This will guarantee that the proper sealing materials are used and that the dimensions and surface finishes of metallic components are within the original design tolerances. Next, when metallic parts involved in external sealing are to be reused, the parts should be properly inspected to ensure dimensions and surface finishes remain in tolerance based on the original qualified design. When surface damage requires addressing on external sealing surfaces, the process should not result in the relevant component dimensions falling outside the qualified design tolerance. Incorporating these elements into the repair process helps ensure the ongoing performance of FE qualified valves.
The guidelines presented above will require some time for planning and proper sourcing of materials, so what can be done if sufficient time is not available? Limited time is something that comes up a lot in the valve repair business, so it is good to have a backup plan. However, it should be clear that if the guidelines outlined here cannot be followed, the original FE qualification may not be considered valid. That said, the only recourse available in such a time crunch is to rely on supplemental testing to provide some level of certainty that the repaired valve will provide sufficient emissions performance. The best industry standard guide currently is ISO 15848-2, which covers production testing of FE qualified valves. However, this is specific to valves previously qualified to ISO 15848-1, and requires testing with helium, a commodity that is becoming more expensive and difficult to source. This highlights an opportunity for end users and industry standards work groups to consider more broadly relevant production testing standards to apply to repaired FE qualified valves.
Final Thoughts
It is imperative that end users continue this journey to reducing fugitive emissions, and FE qualified valves are one way to do that. However, it is equally as important that these valves are repaired properly to ensure ongoing emissions performance. It is our hope that the information presented here helps lead toward consistent performance of all FE valves, regardless of where they are in their asset life cycle.