By Sarah Bradley
Process plants and facilities rely on hundreds or even thousands of control, on-off, and pressure relief valves for safe, efficient, and reliable operations. Assuming these valves have been correctly specified and installed, optimal operation of each requires expert service, ideally guided by analysis of diagnostic information.
Some plants and facilities choose to perform valve monitoring, run diagnostics, and service their valves inhouse—but many others just run their valves to failure. An alternate approach is partnering with the original equipment manufacturer (OEM) vendor for these services. This will ensure valves are maintained to specification and the highest standard of quality to deliver optimal operating performance.

Common Valve Maintenance Challenges
Repair needs for control, on-off, and pressure relief valves vary greatly because of service conditions and product configuration-requiring broad product knowledge and flexible repair support throughout the valve lifecycle. For example, looking at critical and general service control valves, repair needs fluctuate independently throughout the typical lifecycle of each category (Figure 1).
All valves undergo an initial startup phase, which includes determining spares and parts planning. This effort typically coincides with the plant’s first production and is performed during the warranty phase.
After this first phase, service requirements ebb and flow throughout a valve’s lifecycle, with exact needs depending on type of service, hours in use, operational cycles, process media, and many other factors. Given all these factors, valves should undergo periodic inspection, supplemented by automated monitoring and diagnostics for critical service valves. Without this type of expert service, a valve may run to failure prematurely, with consequent issues such as unplanned repairs and extended downtime.
Increased operational expense can be an issue due to repeated, unplanned failures of aging assets, leading to excessive maintenance costs and expediting charges. These problems are often exacerbated by a diverse installed base of valve types and vendors, with variable valve reliability and inconsistent performance, leading to accumulatively inefficient inventory practices.Â
Costly shutdowns due to unplanned downtime often dwarf any increased operational expenses from valve maintenance and repair, with work scope continuing to grow as issues are uncovered. An inability to predict failures before they impact production means that critical assets actually needing attention are ignored.

Calling in the Experts
Efforts to address these and other issues are often hindered by a lack of in-house expertise to perform diagnostics and interpret collected data due to underutilization of installed or existing technologies. When repair is required, any lack of proficiency within the inhouse maintenance team can present a risk, often the case because valves are complex pieces of equipment. Multiple valve vendors add difficulties due to differences among components and recommended services procedures, and the remote geographic location of many industrial plants and facilities may present few cost-effective options for utilizing OEM valve expertise.Â
There can be a temptation to rely on local mechanical shops, but it is very difficult for these types of facilities to repair a valve so it can perform as originally designed. This is true even for the most capable non-OEM facilities because access to information regarding initial methods of valve fabrication and testing will not be available, increasing the risk of not using OEM parts. Premature valve failures can be expected if repairs are not performed correctly, with often catastrophic results.
Fortunately, all of these issues can be resolved by partnering with an OEM-accredited service provider.
Service Provider Solutions
Depending on a plant’s needs, most OEM service providers can assist with any or all areas of valve service. End users should look for a single-source vendor capable of providing technical engineering expertise, a broad offering of valve technologies, project management and execution expertise, and local and global service support.
Local support, regardless of facility location, should be available during all phases of a valve’s lifecycle, either provided directly by the OEM or through accredited service providers. The following is a description of the four typical phases throughout a production plant’s lifecycle, during each of which OEM or OEM-accredited service is paramount (Figure 2).

Startup & Commissioning Phase
Ensuring a safe and timely plant startup can be a complex process moving from project construction or after a shutdown, turnaround, or outage (STO). Juggling multiple vendors, a lack of expert resources, disorganized documentation, and improper valve installations can make this phase complicated.
OEM or OEM-accredited service providers employ certified technicians who have application and safety expertise, follow compliance management practices, and utilize asset planning and tracking to help ensure a smooth handover from construction, or STO, to startup. An OEM or OEM-accredited service provider helps to reduce complexity and minimize the chances for valve damage and cost overruns in this phase.
Maintaining the Plant as it Runs
Repeated and unplanned equipment failures lead to lost production and increased cost while running the plant. A shrinking workforce, retiring in-house technical expertise, and tightening budgets make it increasingly difficult to dedicate the resources necessary to identify opportunities for plant improvement.
OEM-accredited service providers are usually located locally, providing quick response to address any unforeseen issues that may arise. They also have OEM service credentials to vet their capabilities, along with industry application knowledge and a long history of safety performance—so end users can trust them as an extension of their onsite team. OEM-accredited service providers can guide the creation of a proper maintenance strategy to help reduce total cost of ownership through digitizing the installed base, optimizing spares, using analytics to conduct proactive repairs, and helping with larger scope maintenance planning. This helps end users prioritize and reduce inefficiencies to reduce overall maintenance costs and improve reliability and uptime.
Shutdowns, Turnarounds, & Outages
Avoiding scope creep, planning with an attention to detail, and meeting schedule, budget and quality goals are typical challenges when heading into a shutdown, turnaround or outage. STOs often make up the largest maintenance spend within a plant’s budget, so these events must be conducted with precision.
STOs are large-scale maintenance projects, often requiring OEMs to utilize local accredited service providers. These service providers follow the same safety and quality programs and planning processes as the OEM. They also use digital efficiency tools, mobile workshops, and OEM-certified parts for repair to help the STO come in on time and within budget.
Asset Performance Optimization
An aging and diverse installed base brings variable reliability and inconsistent performance—which can lead to the inability to predict failures before they impact production. Valve diagnostics, coupled with engineering expertise to analyze data, is necessary for proper planning and timely decisions regarding upgrades.
Many OEM and OEM-accredited service providers analyze asset performance, lifecycle stage, and compliance of aging assets experiencing repeated reliability issues and frequent failures (Figure 3). Coupled with in-depth valve and application knowledge, they can recommend valve or technology replacements, upgrades, or retrofits to improve production performance and reduce variability.
These types of services can produce real-world results when provided by expert personnel, as demonstrated by the following examples.
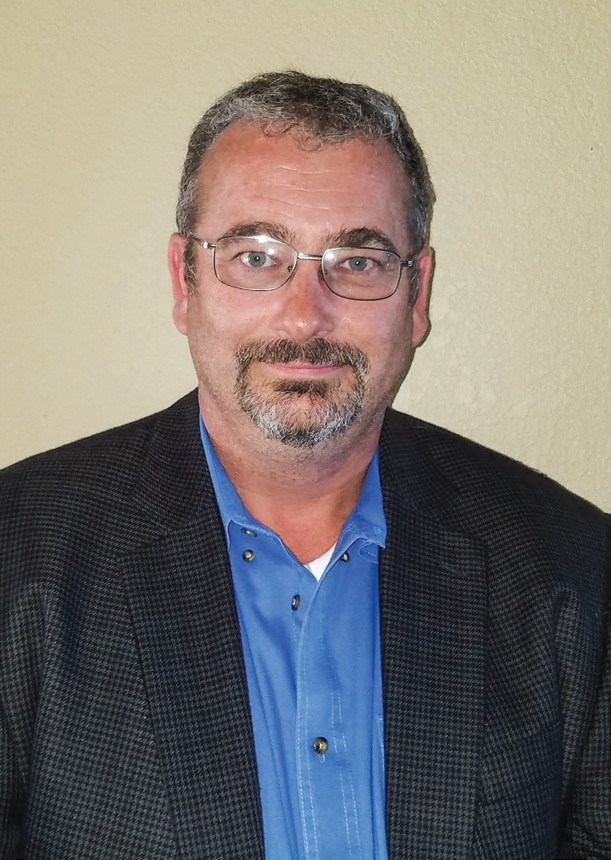
Getting Real-World Results
A refinery in Asia went online in 2016, using high sulfur crude as a feedstock. The plant had over 1,800 valves in service, and Emerson was selected to assist with the first major turnaround.
The engagement began in December of 2018 with turnaround plan discussions. Emerson’s proven STO process and execution capabilities were discussed, followed by a site walkdown conducted in June 2019. ValveLink™ software was installed, and diagnostic data was collected for all Fisher™ valves from July to Oct 2019, including offline diagnostics for 37 valves.
Based on the site walkdown and diagnostic data, Emerson worked with refinery personnel to finalize the scope and spare parts list. Plant personnel selected an Emerson accredited service provider for overhaul and support during the turnaround because they offered local, OEM-certified support.
Service personnel worked with the plant team to determine a strategy for repairing versus replacing each valve, and then performed Emerson’s proven STO process to complete the turnaround on schedule. The accredited service provider won the trust of the plant team through successful work performed onsite and were chosen to provide service for future needs.
A paper producer in China needed to service 330+ valves of varying brands during a turnaround. Emerson’s local accredited service provider was selected to assist, and they used Emerson’s Walkdown App to conduct a complete site walkdown and create an accurate digital installed base repository.
Service personnel held several meetings with site engineers, and with instrumentation and electrical management personnel, to understand and address pain points and goals for the upcoming turnaround.Â
The accredited service provider followed Emerson’s STO planning process and leveraged Emerson’s technical support to complete the work on schedule. Sales personnel continuously reviewed customer requests and visited the site regularly with a service team member, and this close cooperation between the accredited service provider sales and service teams enabled them to provide the required level of service.
Conclusion
Many plants and facilities prefer to engage service providers to deliver the specialized support required for valves through their lifecycles. Emerson supports these end users with a global network of company-owned service centers and accredited service providers to deliver valve engineering and repair expertise, maintenance planning proficiency, and broad service execution capabilities on a local level. This network includes 200+ service center locations with 80+ mobile service centers.
Accredited service providers must meet regular and stringent qualifications every few years, ensuring their services and sales practices are equal to those provided by Emerson, allowing these providers to act as an extension of Emerson worldwide. Emerson accredits two tiers of service providers: 1. Authorized Service Providers provide local OEM service and support. 2. Premier Service Providers offer comprehensive local service and support while serving as an exclusive sales channel. Accredited service provider capabilities include everything from repair execution, maintenance planning, diagnostics gathering, to expert monitoring. These and other services are supported by expertise in factory-supported procedures, OEM training, and close coordination with product engineering personnel. The entire service network is OEM-trained and certified to plan and execute maintenance activities through a valve’s entire lifecycle.Â
Valves are complex pieces of equipment, and maintaining production through the demanding lifecycle of a process plant only adds to the complexity. When selecting a service provider, end users should ensure all their needs will be met not just at a site level but worldwide throughout the entire lifecycle of each valve, regardless of manufacturer. A thorough review of capabilities, OEM expertise, and safety performance should be completed before engaging any provider, including a check of references and interviews with local personnel. Once this due diligence is performed, management can select the right provider to work with plant personnel to deliver the desired level of support.
All figures courtesy of Emerson.