The quest for emission reduction has reached a fevered pitch. Driven by corporate goals for environmental improvements and backed by a host of recent government standards targeting greenhouse gas emission reductions, plant personnel are faced with a pressing mandate to reduce, and ideally eliminate, releases to the atmosphere. But where to begin?
To start, it is important to consider the variety of ways available to cut emissions and meet corporate and regulatory goals. By describing the various types of emissions, and providing several different solutions to target and reduce those emissions, it becomes evident that the implementation of these technologies can be very successful.
By Marcelo Dultra, Dan Myers, and Emily Thomas – Emerson
A Changing Environment
The global focus on greenhouse gas emission reduction has spurred government agencies around the world to address the issue. Each revision of the Environmental Protection Agency regulations mandates ever tighter limits on a wide variety of targeted chemicals, and many investors and stakeholders are now actively demanding that companies engage in environmental improvements and publicly show their progress. The calls have been so great that the Security and Exchange Commission is creating reporting guidelines so companies can provide consistent and accurate accounts of their environmental, social, and governance programs—alongside their standard financial reports.
Beyond the obvious benefits to the environment and a company’s public image, emission reduction also makes financial sense. Every bit of product and raw material that escapes the plant is money thrown away. Add in the cost of wasted energy used in production, plus the time and effort required for processing, and the losses can be staggering.
Clearly, there is strong incentive for a company to reduce these emissions, but until recently the cost of these projects could be overwhelming. Fortunately, valve vendors have introduced a host of new solutions, each of which offer significant emission reductions at a competitive price.
Understanding Emission Sources
The first step to achieving emission goals is understanding the problem. There are two types of emissions that occur in an operating plant, and each has its own challenges and solutions, see Figure 1. Fugitive emissions are unintentional and undesired leaks that discharge gases or vapors from pressure-containing equipment. There are a wide variety of fugitive emissions, but the more common types are valve packing leaks, relief valve seat leaks, pump seal leaks, and flange leaks.
The other type of emissions is vented emissions. These emissions result from intentional releases of gases or vapor from equipment such as relief valves and pressure vents, and from pneumatic equipment which uses natural gas instead of air as the actuating media, with the latter type of installation common at well sites because instrument air is often not readily available.
Each of these types of emissions can be dramatically reduced by utilizing a variety of solutions, as described below.

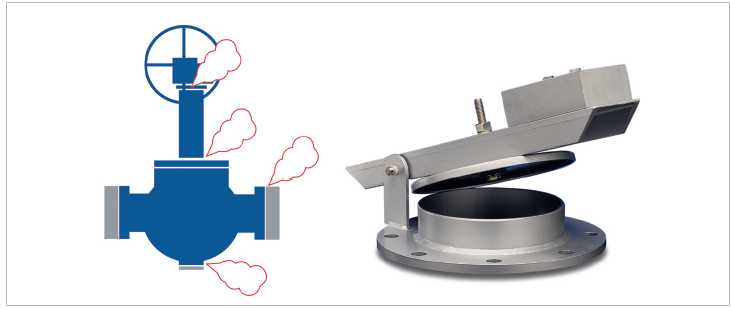
Solutions for Fugitive Emission Reduction
Valve packings have a difficult task to perform. They must contain the process and avoid leaks, while allowing the valve actuator to move freely. This can be quite challenging, particularly with a valve design where the valve stem moves up and down and cycles continuously. The combination of process pressure and temperature swings, along with thousands of valve cycles, presents a difficult design problem.
Recent advances in materials and engineering designs have yielded dramatic improvements in valve packing performance, shown in Figure 2. The latest environmental packing designs utilize spring-loaded washers to continuously compress the packing seals, paired with a combination of different packing ring materials, to achieve extremely low leak rates of less than 100 parts per million (ppm). Despite the low leak rate, they are developed to handle a wide range of process temperatures and pressures. The new packing designs also incorporate valve stems with special coatings and materials to provide long life, along with smooth and unimpeded movement.
Older valve styles do not usually incorporate this type of packing, so the first step for many plants is to evaluate the packing styles on existing valves and quantify their performance. If the existing valve components are well known and leakage data is available, this evaluation is easily implemented. If the valve design data is not readily available, then the plant can perform a walk-down of their facility, targeting valves that handle volatile organic products and other targeted and/or restricted process media. These walkdowns can be performed by plant personnel, or they can be outsourced to a third-party service provider if plant resources are constrained.
If a valve has a history of leaks, a simple and inexpensive packing upgrade to a more advanced design will typically yield dramatic reductions in emissions. Improved positioner diagnostics also provide a means to continuously monitor packing performance and alarm if problems are detected. Alternately, plant personnel can replace a valve style with a rotary actuator, which tends to leak less over time. In certain lethal-service applications, a zero-emission bellows seal design may be an excellent choice.
Another common source of fugitive emissions comes from relief valve seat leaks. These leaks can be very difficult to detect since each valve lacks any embedded sensors and often vents into a flare header, where a leak is not easily noticed. The preferred solution for this situation employs a WirelessHART® acoustic sound and temperature monitor, which is simply strapped to the discharge of existing relief valves Figure 4.
When a leak event is detected, the plant can immediately respond to eliminate the leak and avoid lost product. These solutions have yielded dramatic reduction in emissions, product loss, and reportable releases.
Solutions for Vented Emission Reduction
Vented emissions often result when a pressure relief device opens to protect the process from an overpressure event. While this does protect the equipment, the resulting environmental release must be documented and reported. The obvious solution to reducing vented emissions is to avoid the overpressure event in the first place, but these issues cannot be addressed until the plant has an easy way to detect and quantify pres-sure relief events. One solution for detecting relief events has already been discussed. A Wire-lessHART® acoustic and temperature transmitter mounted on the discharge of critical relief devices indicate when a release event is occurring, Figure 4. Pairing these devices with downstream flow measurement on the flare header allows plant personnel to immediately detect a relief event, calculate the magnitude of the release, and move quickly to resolve the overpressure condition.
Open thief hatches, gauge hatches, and pressure relief manways are another source of vented emissions. Thief hatch and gauge hatches can be inadvertently left partially or fully open, and tank pressure vents can lift undetected. Solutions for these devices can be as simple as a switch which detects when the hatch or vent is open, position sensors which indicate when a tank vent is operating, or monitoring tank blanketing regulators to indicate developing problems, Figure 5.
A WirelessHART gateway enables a multitude of devices to be inexpensively installed across the plant. These devices provide a means for plant personnel to immediately detect and react to releases and stop them quickly.
Another significant source of vented emissions occurs at remote oilfield sites where natural gas is used to actuate pneumatic equipment because instrument air is not available. These devices bleed natural gas to the environment constantly, and environmental agencies across the globe have targeted this equipment, mandating low bleed or even zero emissions.
Automation providers have introduced a broad array of very low bleed and zero emission alternatives for these remote sites. The most common solution involves low power, electric valve actuators and electronic transmitters. These devices cut methane vented emissions to zero, while providing information to enable a host of advanced process control strategies, each of which can be implemented from a remote location. This solution yields dramatic emission reductions, while generating significantly increased profit from greater well throughput, tighter control, and reduced maintenance and operating costs.
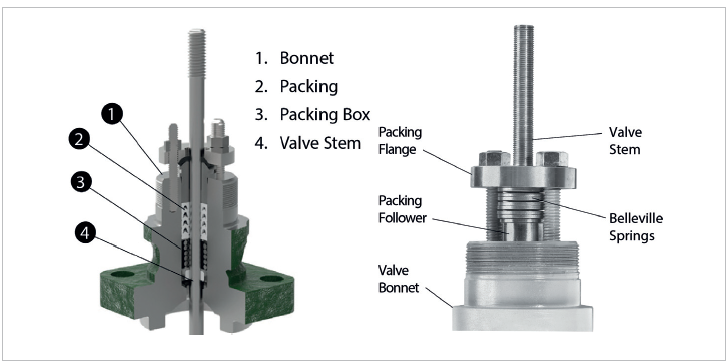
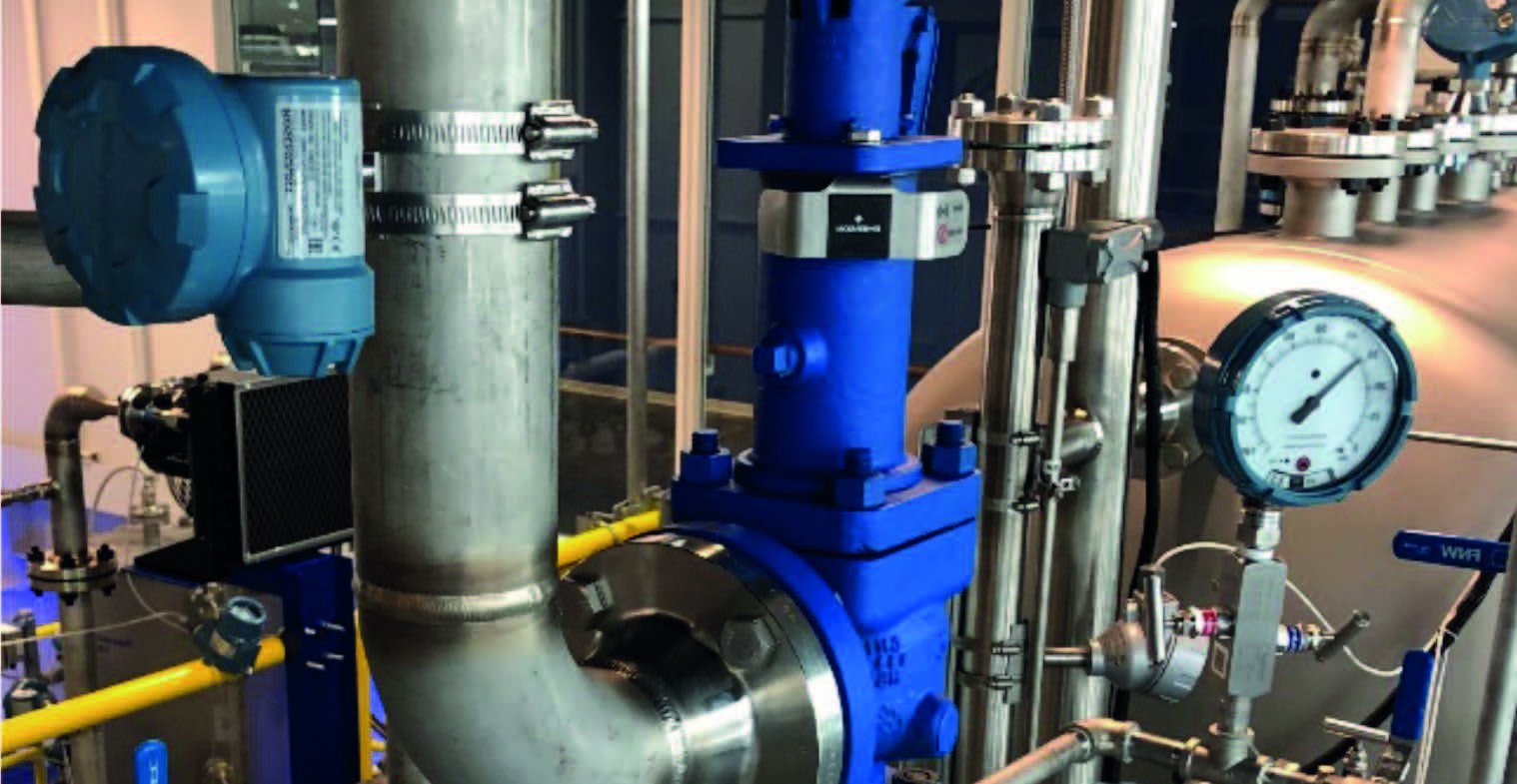
Real World Savings
Several facilities have employed these technologies to not only achieved dramatic emission reductions, but to also experience significant cost reductions that quickly paid for the project.
One refinery installed flow meters and relief valve acoustic detectors on their extensive flare header system. The project paid for itself in five months by providing plant personnel with the information needed to immediately detect and stop relief events, as well as detect leaking relief valves. This allowed the plant to reduce overpressure events, which had been costing between USD $2,500 to USD $50,000 per release.
Several oil companies are actively pursuing wholesale electrification of their well site valves and instrumentation. The expected savings are nearly USD $1 million per well due to increased production, reduced losses, remote control capability, and significantly improved operation.
The array of technology solutions and equipment options are extensive, so end users may find it helpful to consult with their valve vendor to determine the best choices for achieving their emission reduction goals.
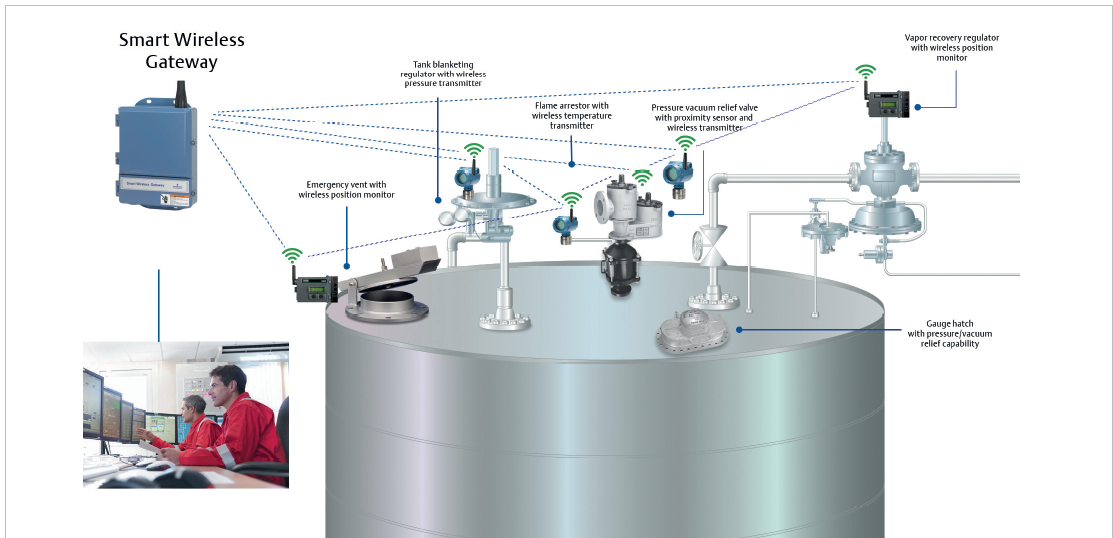
Conclusion
There are many sources of fugitive and vented emissions, included but not limited to valves, thief hatches, flanges, seals, and various types of instruments. Each of these sources can be monitored using a variety of techniques and solutions, such as:
• Live-load packing.
• Bellows seals.
• No-bleed controllers.
• Electric actuators.
Proper selection of devices to limit emissions is the first step, for example correct valve types and sizes. Once the right devices are selected for either new or retrofit applications, the next step is installing monitoring devices as appropriate to detect, and in some case measure, emissions. Vendors offering a comprehensive line of these types of devices, along with corresponding domain knowledge for applying solutions, can assist to ensure proper selection and application.
REFERENCE
All figures courtesy of Emerson.
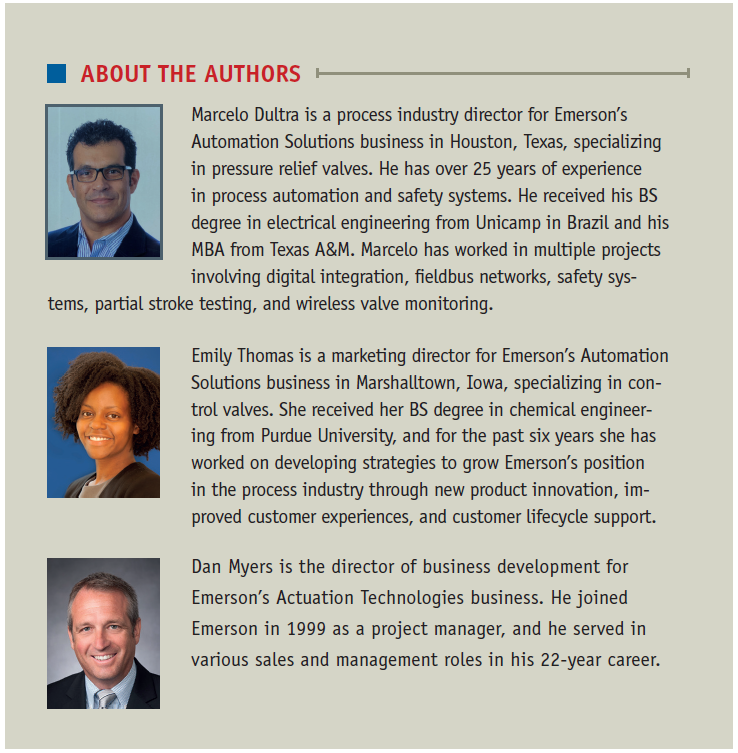