With over 37 years in the chemical industry, Bill Patrick has witnessed the evolution of piping technology like no other. The drastic changes the industry has faced with the increasing amount of new technology has allowed users to witness the development of innovation on the rise and changes made to day-to-day tasks, in addition to the overarching practices in the chemical industry.
Valve World Americas had the pleasure of speaking with former Chairman of the Valve World Americas Conference & Global Improvement Leader – Piping Technology, at Dow Chemical Company (retired), Bill Patrick, about his experience working in the industry leading up to his retirement, the ways in which technological advancements has impacted his work, as well his take on the future of the industry.
By Charlie Evans and Shopia Ketheeswararajah
After graduating from Western University in London, Ontario, Patrick began a career at the Dow Chemical Company. After completing his Master of Engineering Science Degree, and 14 months of working in the chemical plant, he transferred to the engineering department where he developed his skills as a project, pressure vessel and piping engineer, gaining a Professional Engineer designation in the Province of Ontario. “In 1986, I initially started at a power plant before being transferred into a mechanical engineering group. “From there, I was transferred to Houston and moved into piping technology, eventually becoming the Global Valve and Valve Sealing Technology Leader until 2008,” said Patrick. “Now I work as the Global Improvement Leader – Piping Technology.” This includes valves and valve sealing technology, pressure vessels, heat exchangers, and more.
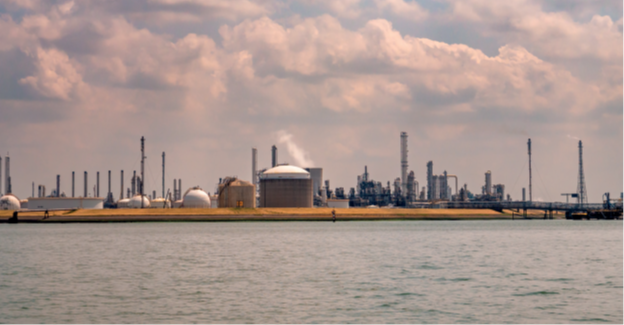
Being in the chemical industry, he explains that the fluids being transferred are often potentially dangerous and require the correct application of material to meet specifications. “It is a little different than the specifications required in the oil industry because they are typically dealing with hydrocarbons. On the other hand, the chemical industry not only deals with hydrocarbon, but with all sorts of different chemicals at the same time,” Patrick states. Dow used to be a chlorine-based company, and at that point, the company was working with very corrosive fluids. With changes to the business, while still dealing with corrosive material, the company narrowed down the types of fluids they had worked with.
Working Alongside Digitalization
A common concern for some is the digitalization that comes along with innovative technologies. “Although some people may be concerned with artificial intelligence eliminating human talent, I believe the industry requires the best of both worlds. Currently, piping components are not digitally tracked in a plant,” he shares. Currently, there are plenty of leak detection technologies available. “There are acoustic detection devices, infrared cameras, and thermal imaging available that can aid in assisting or monitoring leaks within an area,” he said. “From my point of view, this technology will allow engineers to better make decisions, and we will run safer plants, in addition to keeping people out of danger,” he added.
Keeping up with innovative technologies is vital for success in the industry, but in addition to this, being able to communicate with the company on a grand scheme is just as important. It goes without saying that there are more obstacles when it comes to implementing changes or proposing new ideas and initiatives in larger companies, however, from his years of experience, Patrick sheds some light to the importance of being able to work alongside a large group.

“When working for a large company, it can feel hard to affect change in a way that is satisfying, there are many individuals you need to sell an idea to, whereas with a smaller company, things can happen rather quickly. However, working with so many different people does have its advantages,” said Patrick.
“The best part of the role is the opportunity for interaction with people,” relayed Patrick. “Since COVID, our office has not had the same energy it once did, however, people are slowly coming back as more time passes.” When putting together a project, Patrick believes collaboration is key. “Face-to-face meetings where there is a dialogue are essential when conducting projects. Engineering is an inherently creative environment, and you need people working together to accomplish that,” he continued.
Exciting Projects
A few specific projects within his career stand out for Patrick. “Dow has a dictionary of items. Previously, I consolidated the ball valves within that dictionary,” he said about one of his most challenging projects. “I had to find out what Dow wanted from the plants, in the plants, what technology was coming, what was available, and more.” During this, the second-generation PTFEs with improved properties provided similar mechanical performance as the earlier reinforced PTFEs.
“New material was coming out and we standardized on that because it showed good and desirable permeability qualities. Information at the time that identified mechanically energized packing also provided benefits.” continued Patrick. “To address emissions, we standardized our carbon and stainless steel ball valves to require energized packing. Therefore, we were able to optimize our ball valves in the dictionary and remove a bunch of valves from the dictionary. Some manufacturers struggled with the new requirements as Dow was asking for Inconel washers rather than stainless steel due to concerns around stress corrosion cracking due to chlorides. Some valve manufacturers at the time were not willing to go to the Inconel washers and thus were removed from approval list.”
This also calls material selection into question. “You can go to titanium, which is very high cost, or you can go with a plastic lined valves and pipe, which is typically PTFE,” explained Patrick. “However, you may not get ten years out of the lined equipment. You may have to replace it because of the permeation issues that may arise. Based on service fluid and expected performance, a value assessment can be developed comparing the use of higher alloy components vs the lined systems.”
Another exciting project for Patrick involved a new design. “We wanted to shoot a laser into one of our processes and get feedback to determine the status of the reaction in real time. I designed a probe housing for the laser meeting the code requirements which incorporated a glass lens, having to additionally seal the glass against the end of the probe within the reactor. This project was further complicated by the fact that it required registration with the local authority, so the calculations were to be reviewed.”

The Future of the Industry
“Most companies have a technical ladder,” said Patrick when asked about advice for newcomers to the industry. “If you have a passion for a specific technology, find a place that inspires you to develop expertise in that area and climb that ladder. Get involved in committees worldwide to educate yourself as much as possible.”
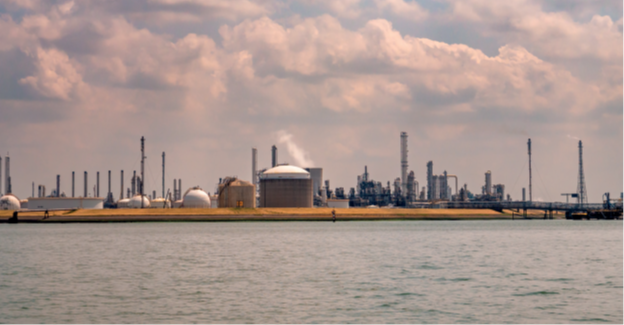
When asked about the industry’s future, Patrick said, “I believe there are three technologies that will change the future completely; namely, point cloud technology, (laser scanning, and photogrammetry), additive manufacturing (3D printing), and artificial intelligence (AI). This is going to change the way we execute projects in the future.
“With additive manufacturing, I think the shapes of much of the stuff that we see in a process plant will change with this technology. Today we are largely governed by shapes of rolled poured materials with technology developed decades ago.”
“There has been a lot of work done with heat exchangers using the same technology used to make circuit boards. This technology I feel easily transfers into a 3D printed heat exchanger,” continued Patrick. “It will be very interesting to see how these changes manifest across all areas of manufacturing.”
“I think technology as a whole is going to change a lot of the way we do things, and AI is going to change the industry entirely. That being said, I do not think society is going to let AI take the place of engineers completely. There will always be the need for human engineers for innovative designs and to take responsibility at the end of the day,” concluded Patrick.