It is difficult or perhaps impossible to find an industry sector that has not yet increased focus and public promotion of its corporate targets related to environmental, social, and governance (ESG) programs. A remarkable shift is occurring towards a much higher consideration of the impact of business operations on the resources and people of the planet. Focusing on materials, specifically the polymer-based sealing elements that are used across the valve spectrum in the industry, several challenges exist in creating more sustainable solutions in the families of polymers that dominate this application space.
By Dr. Tim Bremner, Materials Technology Director Advanced Sealing Technologies – A Michelin Group Company
The Move Towards Sustainability
Shareholders of publicly traded companies are now looking at more than share prices and monetary rewards. They have begun to scrutinize the plans and policies of companies they choose to invest in, with regard to sustainability goals, environmental stewardship, and employee treatment. While ESG results reporting is voluntary in most companies, corporations have taken the proactive step of making this information available to the public within their annual reports. In 2021, 96% of companies listed in the S&P 500 stock index were found to be publishing sustainability reports.1
A survey of 133 international companies conducted in late 2021 by Sphera2, a leading global consultancy firm, found that 87% of the respondents have committed to integrating sustainability targets into their company strategy, and a further 71% have committed to sustainability targets in their product development arenas. Accompanying this shift in corporate objectives is a move towards more transparency to the public at large, with over 70% of the surveyed companies indicating that their sustainability goals are shared publicly alongside traditional revenue and growth targets. This is highly encouraging as the world comes to grips with negative factors such as global warming, plastics pollution, air pollution, and water insecurity.
When one thinks of sustainability within a manufacturing environment, where goods are produced for either industrial or consumer use, there are several different but connected contributors to improved sustainability, including the raw materials. Figure 1, represents some of the more common elements of sustainability that are typically considered in a manufacturing process.
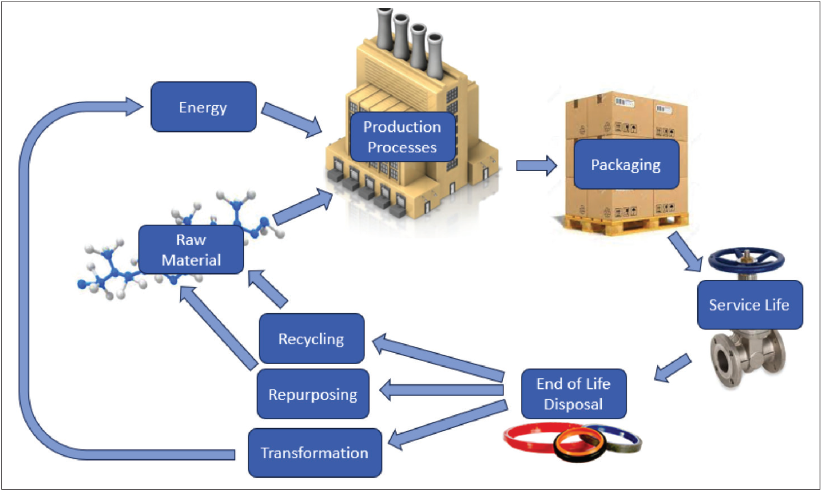
Challenges for Industrial Valve Sealing Elements
Focusing on materials, specifically the polymer-based sealing elements that are used across the valve spectrum in the industry, several challenges exist in creating more sustainable solutions in the families of polymers that dominate this application space. While the commercial availability of bio-based or sustainably sourced polymers is not new, the specific polymer types that are produced through these more environmentally friendly production pathways, unfortunately, do not have the required property balance to be utilized in most of the sealing situations that are encountered in the industrial markets.
The demands on polymers used in a consumer environment are substantially different, and usually lower than those used in an industrial engineering application. As a result, any uninformed suggestion that bio-based polymers are readily available and viable is not valid when it comes to engineered valves and valve-sealing elements. In 2020, the total bio-based structural polymer production capacity was very low, on the order of 0.8% of the total global polymer output for all polymer types. This is not too surprising, given that the dominant polymer families utilized for valve seal production represent a very low proportion of global polymer output that is dominated by generally less robust and more consumer-focused polymers like polyethylene, polypropylene, polyvinyl chloride, polystyrene, and polyethylene terephthalate. An indication of the polymer types that dominate the bio-based polymer portfolio is provided in Figure 2.
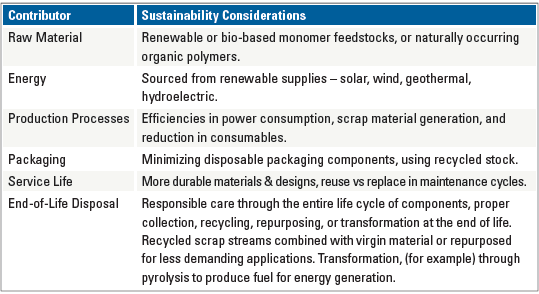
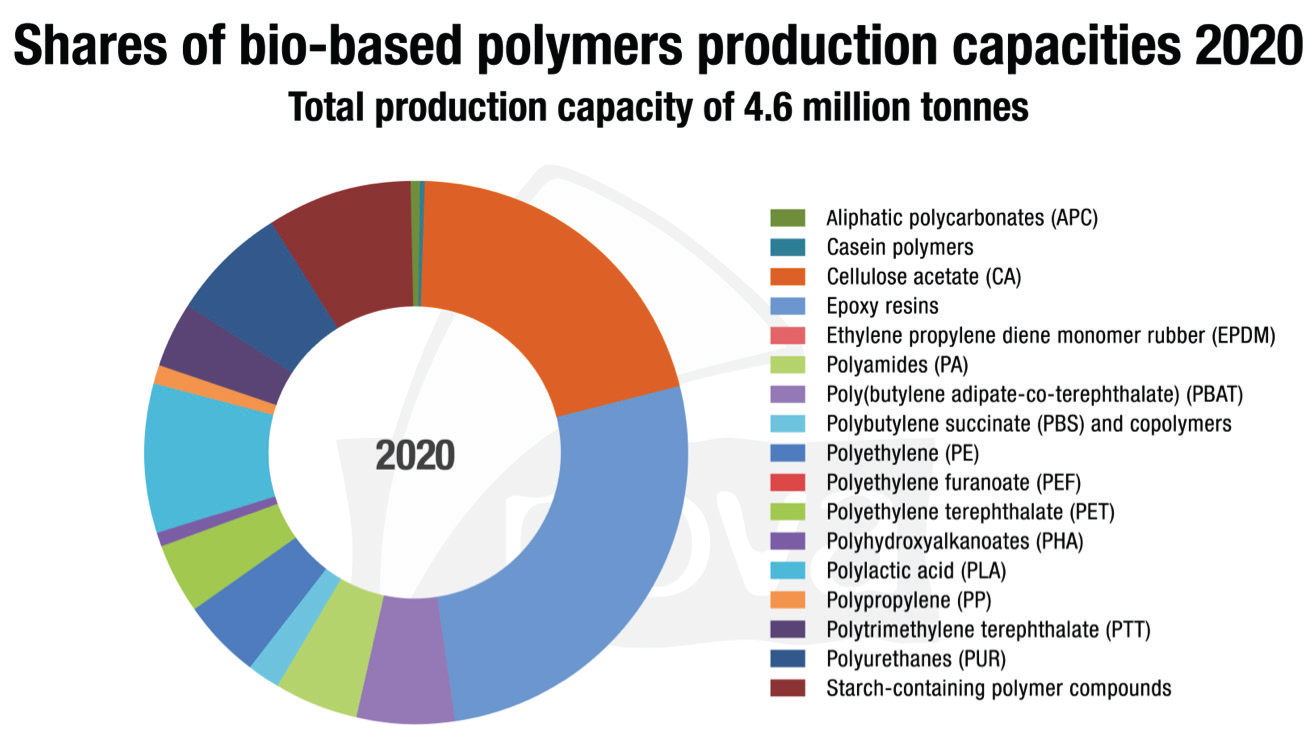
Primary Challenges in Sustainability Sourced Engineering Polymers
There are several challenges to consider when given the task of identifying sustainable replacements for the incumbent non-sustainable polymers that are used today. Intentionally trying to avoid turning this discussion into a chemistry class, three of several challenges are discussed below, with the recognition that there are more.
1. Viable synthetic chemistry pathways to produce identical monomers.
With specific regards to the engineering polymers that are used in valve sealing elements today, the ideal situation for sustainable solutions would be to produce a chemically identical polymer from sustainably sourced monomers, with the goal of achieving a drop-in solution that has identical performance characteristics as the incumbent. If this were possible, the transition would be much simpler and less costly to manage from an Engineering Change Management perspective, and the risks associated with such a transition would be more palatable.
Unfortunately, the chemistries associated with many of the more modern and popular polymers used today in the valve industry are complex or do not have known reaction pathways that would allow the production of chemically identical monomers from bio-based or renewable resources. If the derivatization of natural feedstocks into the same chemical structures as those derived from (for example) petroleum-based feedstocks requires multiple reaction steps with several reagents, the overall sustainability potential may be erased due to overwhelming energy costs.
Consider for example the case of fluoropolymers, whether thermoplastic like PTFE or elastomeric like FKM, in which the primary raw material for the perfluorinated polymers is a mineral called fluorspar (also known as fluorite or calcium fluoride) that is mined from the ground. This material and its derivatization into hydrofluoric acid is by far the dominant source of fluorine for all fluorine-containing chemicals. There is no identified alternate source for fluorine from naturally occurring bio-based materials today, so attempting to obtain a sustainably sourced fluoropolymer today is simply not viable.
One family of polymers that has had some success is polyamides, known generically to many as nylons, which are used in a variety of valve sealing elements that demand high modulus and good abrasion performance. Today, the most common nylons used in seals are nylon-6, nylon-6,6, and nylon-4,6 in part due to the attractive performance features like high modulus and thermal stability and a good performance-to-cost ratio. Several other varieties of nylon with significantly different properties are commercially produced from bio-based sources, including nylon-11 (which has been available since 2012), nylon-6,10, nylon-10,10, and nylon-10,12, but these lack the high modulus and rigidity that is so desirable in rigid functional seals. Therefore, while similar they would by no means be considered drop-in replacements for the nylon-6,6 and nylon-4,6 variants.
2. Determination of equivalence
Some of the materials that are used in valve sealing elements today have been in use for years or decades, and high confidence exists in the reliability of these materials due to this long history of good performance. Consider that PTFE-based seals have been used since 1948, and operators have therefore had a long time to become familiar with the inherent properties of this material and learned where it will and will not work; the specification for PTFE seal compounds is never very elaborate and usually lists just some very basic bulk properties.
Polymer materials are complex, consisting of molecules of varying lengths and morphology that may be anisotropic, as is the case with semi-crystalline thermoplastics comprised of crystalline and amorphous domains. Included with these differences in molecular architecture, the ultimate finished part morphology and rheology can be strongly influenced strongly by thermal and mechanical processing conditions in manufacturing steps. Given these characteristics and influences, it is commonly stated that polymers are almost always under-specified, meaning that they will often have bulk properties that match a laboratory-measured specification target, but may fail miserably in the application.
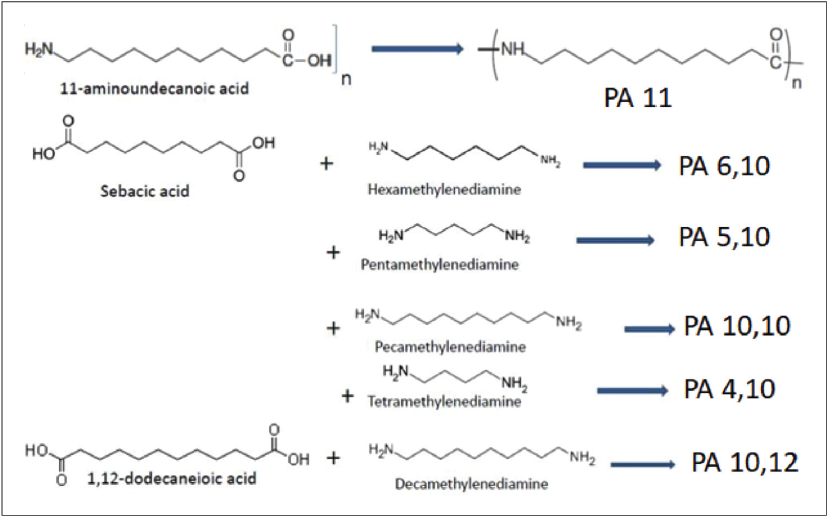
If one was asked to define a suitable sustainable replacement for a tried-and-true seal material, what set of properties would they measure that defines such attributes as ‘conformability’, or ‘seal through contamination’? The industry has come to rely on certain materials knowing they work without a fundamental understanding of why they work, so a sustainability-driven transition to a different material, in most cases, will not simply be a specification match.
A similar situation exists when dealing with in-use dynamic strain properties – what attributes of a polymer material can be measured that indicate the propensity for a material to crack versus flex, after a few thousand cycles? In short, there are material specifications that exist, which in many cases do not sufficiently characterize the attributes of the material necessary for its function. Therefore, determination of equivalence of a sustainably sourced analog will often rely to some degree on proof of service rather than simply matching numbers on the specification.
3. Availability of commercial quantities of sustainably sourced materials.
In the simplest sense, transitioning to a sustainably sourced material from a mature and well-established polymer source will need to be managed carefully from a supply chain continuity perspective. If some company is fortunate enough to have identified a viable process for the production of a desirable polymer material arising from naturally occurring, renewable resources, it will take time and capital investment to build production capacity to meet the anticipated demand. If the primary raw material for this new sustainable polymer is plant-based, then challenges will exist in ensuring that the land and water resources required to produce the biomass can be maintained, perhaps in competition with uses of that same land for food production. Consider for example that leading international chemical companies are today pursuing the production of bio-sourced monomers for use in polyurethanes that are derived from glucose fermentation (sugar cane or sugar beets), castor bean oils, and palm oils. Many of the bio-based polyamides mentioned previously rely on plant-based biomass for monomer precursors, and thus if the popularity of these polymers grows, the arable land used to produce them should grow too.
Conclusion
The transition to sustainably sourced polymer materials for use in engineering applications will take some time and considerable effort, but it can be an exciting opportunity for materials scientists and engineers as their objectives are now more broadly impacting on society as a whole, rather than simply the profitability of a corporation. There is no doubt that new polymers or new ways of enhancing the properties of existing bio-based or naturally sourced polymers will be required to meet the continuously increasing performance requirements of these valuable materials in valve sealing applications as well as the much broader engineering materials space. This will be a somewhat disruptive transition compared to the historical lower concern for the planet and people, but it is certain that objectives related to sustainability and ESG initiatives will persist for decades to come, with obvious benefits to coming generations.
References:
- Governance and Accountability Institute, Inc. Press Release – Sustainability Reporting
- 2021 Snapshot of Sustainability Maturity, report available online: 2021 Snapshot of Sustainability (Sphera Inc.)
- The nova-Institut publication from January 29, 2021 found here: Bio-Based Polymers 8% CAGR
- From Dr. Robert Humphreys contribution to the Polymer Innovation Blog (2013) found here: Bio-Polyamides: Where Do They Come From?
