Bray’s fully integrated and innovative product portfolio not only meets, but exceeds the expectations of their customers in all regions around the world, with products such as standard and severe service ball valves, specialty slurry valves, knife gate valves, check valves, resilient seated butterfly valves, high performance and triple offset, pneumatic & electric actuators and related accessories.
By Sarah Bradley
By Sarah Bradley
Bray continues to expand its market presence with an innovative approach to providing a wide range of solutions with a growing product portfolio. Bray’s leadership in metal-printing, low emissions and extended reliability has been hugely impressive. Bray continues as a technology leader in valve automation & controls. In this article we highlight innovative solutions Bray provides in critical services using its S98 Pneumatic Actuator, Smart Positioner and IIoT offerings.
World of Valve Performance
Bray understands that valve performance plays a crucial role in its customers’ ability to maintain their assets. The company has developed cost-effective valve testing solutions that can be adapted to many different applications without the challenges of nuisance false alarms. This article will focus on two critical applications: Safety Instrumented System (SIS) Valves and Automated Emergency Block Valves (EBV).
Safety Instrumented System valves (SIS) and Automated Emergency Block Valves (EBV) are used to isolate or vent a process when unsafe conditions occur. The common life cycle of these valves is to remain in one position and only move during an emergency scenario. Due to the critical nature of these valves and the fact that they do not regularly move, safety practices are implemented to ensure function. One such practice is the partial stroke test (PST) where a valve is cycled a few degrees to test movement without interrupting the process. Like everything in the process control industry, a PST can be implemented in many ways.

Operation and Customization – Manually Operated Mechanical PST
S98 Partial Stroke Module
The Bray PST module is a mechanical device that can be added to the S98 Scotch Yoke Actuator. This patented design can serve as a dual function of extended travel stop and partial stroke test. With the hand lever set in free mode the actuator push-rod is free to move through the device allowing 90 degrees of travel. When the hand lever is activated the push-rod travel is limited, as seen in Figure 1. This travel limit can be adjusted for the range of movement required for the PST.
In practice a PST is initiated by activating the travel limit lever and cycling the solenoid valve. This test will validate the function of the valve travel and the associated control systems. Travel limits and time will need to be measured by the technician.
Thanks to its all-mechanical configuration, the implementation of this system is cost effective and simple to use. The main drawback to this system is, of course, its susceptibility to human error since it relies on a technician to run the test at the appropriate times and visually verify that movement is occurring.
Digitally Automated PST
Electronic Approaches
Partial Stroke Testing can also be done digitally with the use of a smart positioner such as the Bray 6A positioner. By using a digital approach, parameters such as stiction, speed, dwell time and friction can be measured. These parameters improve the quality of a partial stroke test and can be used reliably to predict valve faults earlier than mechanical solutions. This is done by comparing tested values against user/manufacturer defined thresholds or limits. A second advantage is the data logging ability during testing. By documenting tests over time, the Bray 6A smart positioner provides plant managers a record of all testing being performed and can be utilized for a wide range of benefits from compliance reporting to predictive algorithms.
Full Controllability
Unlike the mechanical offline approach, the digital approach gives users the ability to control multiple variables of the PST and program logic responses. Test quality can be improved by adjusting variables such as stroke distance, rate of position changes and tolerance for required movement. The test program can further be improved with automated response to a failed test. For example, if a PST fails by a certain degree a “fail” condition such as an alarm or position state can be initiated.
Initiating a test can be done multiple ways.
1. Local or remote initiation with binary input activation:
a. The 6A smart positioner is equipped with one binary input slot as standard. This input can be used to activate the partial stroke test either remotely with PLC/DCS or by ESD push button.
2. Data management software communicating through HART protocol:
Units that are equipped with HART or Profibus will have the capability of activating a PST or FST (full stroke test) through an asset management software. With this tool all Bray 6A positioners in a plant are given a unique ID name chosen by the user. Through this system, plant managers will have the ability to view all positioners and run PST/FST as needed with real-time data being presented in the control room. PST/FST settings can be adjusted for individual positioners or by valve type/size/features/application. Variables such as test frequency, stroke distance and time can be adjusted to improve performance on the fly.
3. Adjustable Cyclic Test Interval at agreed threshold safe start point:
The Bray 6A positioner can be programmed to automatically run a PST at designated time intervals. Activation of this mode can be done both local to the unit or remotely through the PDM (process device manager) software. Time intervals are done in days allowing for users to meet their minimum availability requirements.
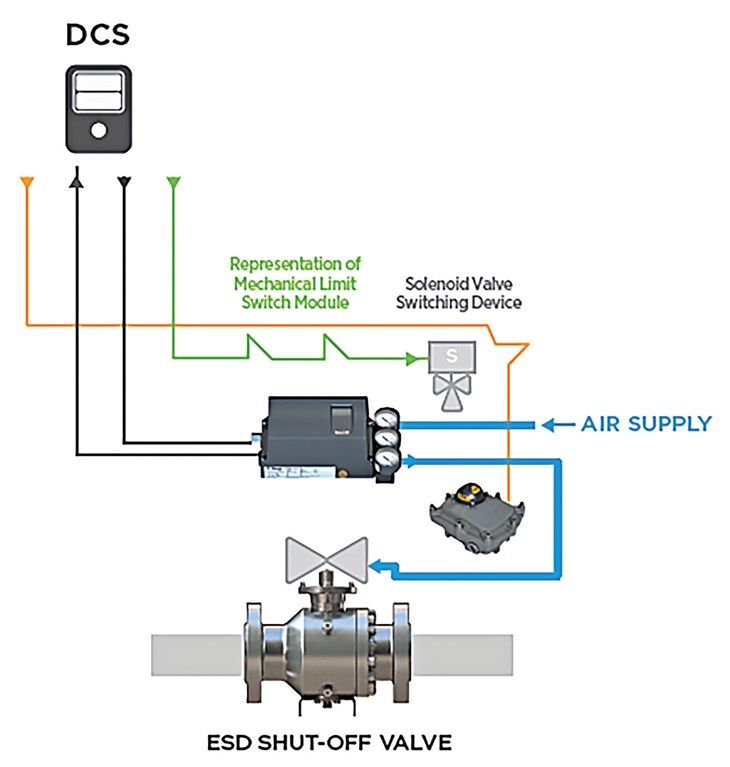
Example 1: Bray 6A Circuit – PST with Solenoid
Safety shut down valves that use a solenoid to override the positioner in an emergency add another device to validate. In order to accomplish this, the limit switch card is used in conjunction with a solenoid relay. In practice the inputs on the limit switch card are used to override the solenoid circuit causing the valve to move. Travel is limited by having the second limit switch activate at the desired degrees of motion to disengage the coil. This allows for a PST that includes testing of the emergency valve and the solenoid.

Example 2: Bray 6A Circuit – PST without Solenoid
The Bray 6A positioner is certified in accordance with IEC 61511 to SIL2 for reliably depressurizing. It can therefore replace the solenoid valve with a supply voltage of 24 V. Since it is equipped with diagnostic functions, it can also perform a partial stroke test at regular intervals. An additional device does not have to be mounted on the actuator, because Bray 6A functions both as a solenoid valve and PST execution device.
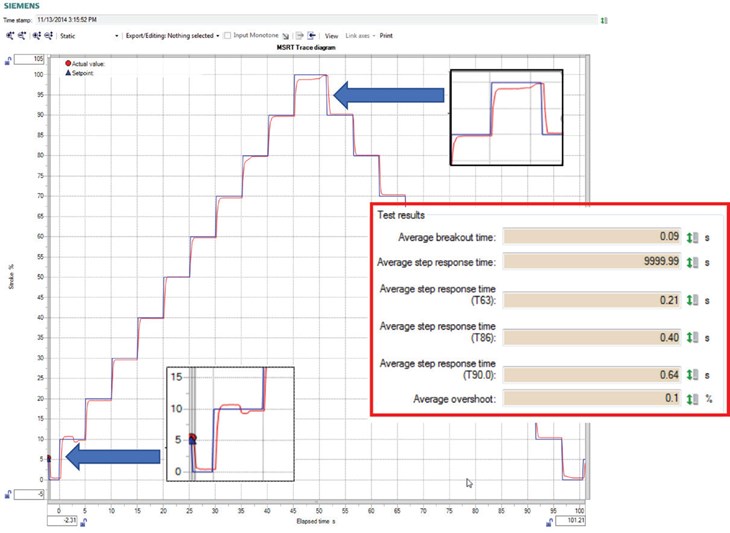
Example 3: Digitally Automated FST
When possible, a full stroke test can be done to validate a full stroke signature to ensure valve isolation or unseating capability. Like a PST, the FST is logged in the Bray 6A memory. An example chart is shown below where a full stroke baseline is compared to real-time test response. This can be recorded and logged for maintenance personnel to review at any time.
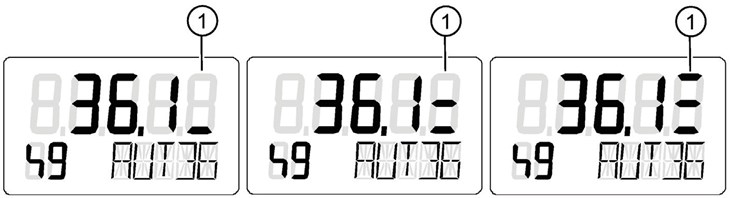
Example 4: Alarm Notification
The 6A positioner has the capability of outputting alarm codes based on real-time measurement values such as valve torque increases over time or valve movement time and hours of operation. A 3-tiered scale is used to indicate maintenance required, maintenance demand and maintenance alarm. The below image outline the visual display of each alarm level found on the Bray 6A screen. For networked units, this alarm can be sent to a PLC or DCS through a protocol network or binary outputs. Further diagnostics can drill down to the specific alarm reason.
As an example, in the context of a PST this tiered system can be applied to time taken to run the stroke of the test. The above table outlines the tired alarm program for a 3 second PST (Table 1).
By giving users the ability to control the sensitivity and relevance of these alarm variables a system that reduces false positives can be created and provide the user full customizable valve reliability testing.
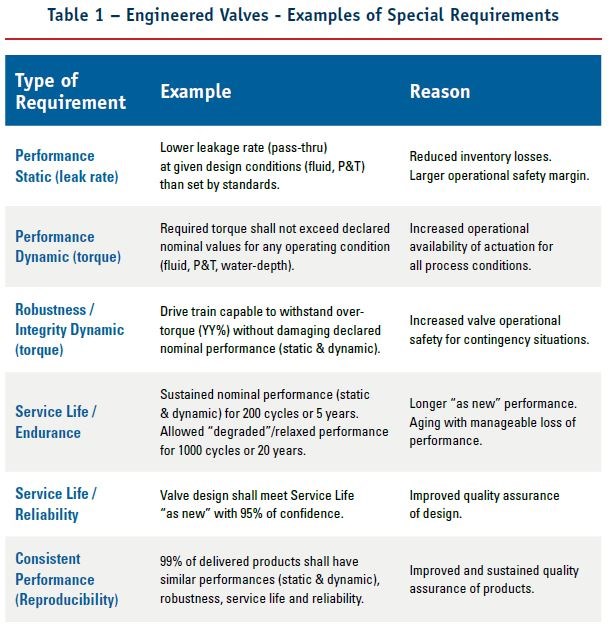
IIoT Solutions Improve Efficiency and Safety of Process Automation
Evolution of Asset Monitoring
Bray is actively supporting the adoption of Industry 4.0 by developing smart connected products and solutions that provide valuable intelligence to integrated systems.
Visual Inspections
Visual Inspections are common practice for many facilities with maintenance programs that are not very mature. They involve manual walk-around routes on a pre-defined schedule, usually every 30 – 90 days. This only provides a snapshot in time of the asset’s health, at the exact moment when the technician is physically performing the inspection. As a result, there are many deficiencies associated with this level of asset monitoring which essentially renders operators and maintenance professionals flying blind between these touch points.
Real-time Condition Monitoring
As organizations become more mature, they implement Real-time Condition Monitoring which includes IIoT connected devices transmitting data directly to control systems over industrial protocols. This provides operators the ability to actively visualize streaming data in a meaningful way and perform analysis to determine an asset’s health. The ability to understand the current performance of the valves in their facility is very valuable information for operators. Real-time condition monitoring is the first step to enabling proactive maintenance planning which drives efficiency and reduces the risk of unsafe operating conditions.
Predictive Maintenance
The next step in proactive maintenance planning is Predictive Maintenance, which involves historical patterns and models being compared against real-time data to predict specific future outcomes. Improvement recommendations are automatically provided to operators and maintenance professionals based on algorithmic outcomes. Predictive Maintenance alarms can also be utilized to automatically trigger a PST/FST to validate that the valve will operate as needed. The actionable insights provided enable the prevention of unplanned downtime by informing decision makers of the specific repairs or replacements that need to occur within a defined time frame (Figure 6).
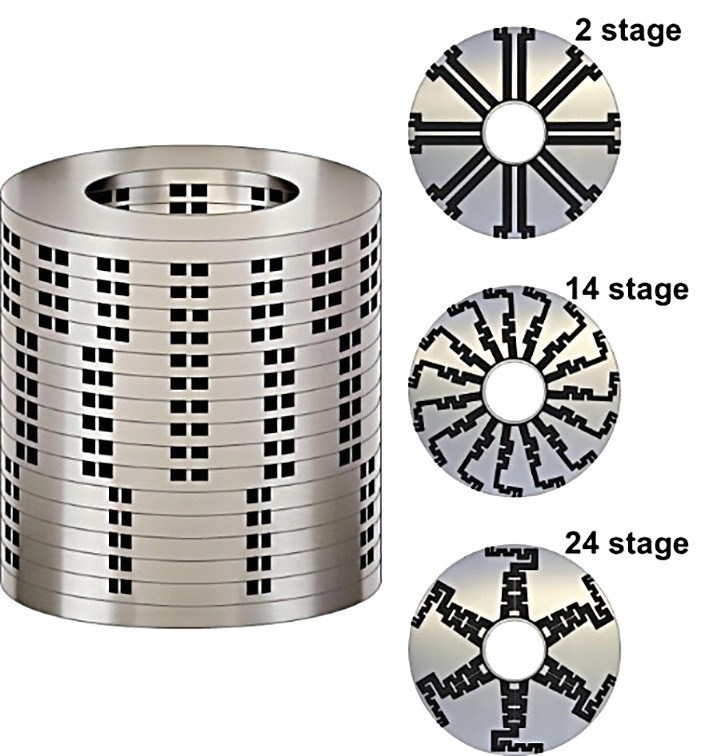
Summary
Bray continues to be a leader and an innovator in the valve industry with a strong focus on automation and controls. A deep product portfolio, a solutions-based approach and strong collaboration makes Bray a partner of choice! Bray continues to extend its automation capability by developing IIoT solutions and is actively supporting the adoption of Industry 4.0 with smart connected products and solutions that provide valuable intelligence to integrated systems.
In summary, Bray offers a wide portfolio of packaged solutions ranging from mechanical to digital that are designed for critical safety applications like SIS and EBV. In today’s uncertain world, Bray’s solutions deliver the actionable insights required for process automation to safely operate facilities.